Want to revolutionize your building inspection process?
The conventional method of inspecting buildings requires a significant investment in time while presenting safety hazards and high costs. Accessing hard-to-reach locations demands inspectors to use ladders and scaffolding while creating safety risks through potential falls and injuries.
What if we discovered a more effective approach?
Building inspections are evolving through the integration of drone technology. Drones provide faster and more precise inspections and additionally help businesses save substantial money while improving safety.
Through this article, you’ll learn about the transformation drones are bringing to building inspections, along with reasons why your business should adopt this technology.
Inside This Guide:
- Why Drones Are Revolutionizing Building Inspections
- Key Benefits of Using Drones for Inspections
- Types of Inspections Drones Excel At
- What to Look for in an Inspection Drone
- How to Start Implementing Drone Inspections
Why Drones Are Revolutionizing Building Inspections
Building inspections through conventional methods demand substantial risk exposure as well as high expenses while consuming a lot of time. Inspectors often need to:
- Set up expensive scaffolding
- Use cherry pickers or boom lifts
- Deploy rope access teams
- Risk their safety on ladders
Traditional building inspection methods present substantial time investment and financial cost along with safety risks.
Enter drone technology. Using American-made drones equipped with high-resolution cameras and specialized sensors, inspectors can now examine buildings thoroughly without leaving the ground. Multiple industries, including construction and real estate together with insurance and facility management, are implementing this groundbreaking approach.
Recent market analysis predicts the global drone tower inspection market will expand at a 16.7% CAGR from 2023 to 2033 to reach USD 1,397.6 million by 2033. The explosive market expansion reveals that industries are moving towards adopting this safer and more efficient inspection technique.
What factors contribute to the rising popularity of drones for building inspections? Let’s look at the key benefits.
Key Benefits of Using Drones for Inspections
Your building inspections will gain significant advantages by adopting drone technology, which traditional methods cannot offer.
Enhanced Safety
The foremost reason to adopt drone inspections is their ability to improve safety standards. Safety for workers is improved because inspectors remain on the ground when using drones for inspections.
- Fall risks from heights
- Dangers of climbing on unstable structures
- Exposure to hazardous materials or conditions
- Need to access confined spaces
Your team maintains safety by using drones to perform challenging access tasks while collecting necessary visual data.
Significant Cost Savings
The use of drones for inspections creates significant financial savings for companies.
- You can avoid the high costs associated with scaffolding rentals and lift equipment expenses.
- Reduced labor costs and man-hours
- Lower insurance premiums due to reduced risk
- Fewer workdays lost to weather delays
During inspections of large structures, savings can accumulate to thousands of dollars and may reach tens of thousands of dollars.
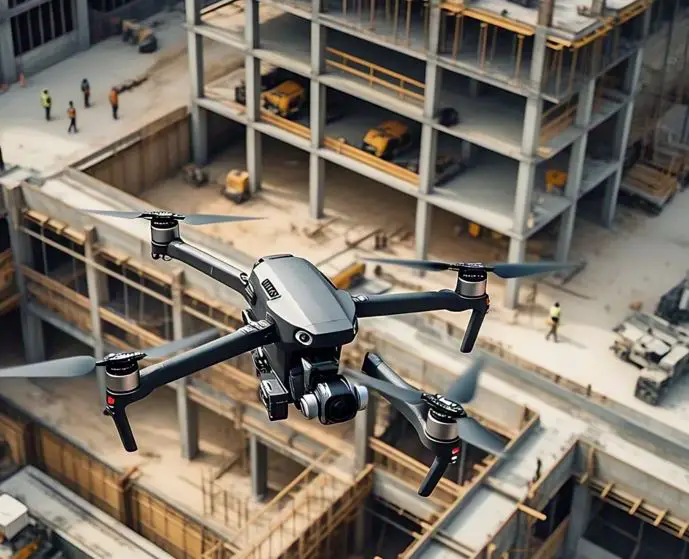
Faster Inspections
Since time directly translates to money within businesses, drone inspections produce substantial time savings.
- Complete inspections in hours instead of days
- Examine large structures quickly without repositioning equipment
- Instantly share digital data with team members
- Reduce building downtime during inspections
The drone roof inspection market will grow at a 14.2% CAGR between 2023 and 2033 and reach approximately USD 645.3 million by 2033. The projected market expansion demonstrates how drones deliver both time savings and operational efficiency.
Improved Data Quality
Modern inspection drones capture incredibly detailed data:
- 4K or higher resolution video footage
- High-resolution photographs from multiple angles
- Thermal imaging technology enables construction professionals to identify areas of heat loss and moisture penetration during inspections.
- 3D mapping capabilities for complete structural analysis
The abundant detailed information enables inspectors to conduct more comprehensive evaluations while facilitating superior decision-making concerning maintenance and repairs.
Types of Inspections Drones Excel At
Specific building inspections benefit greatly from drone technology applications.
Roof Inspections
Accessing rooftops proves dangerous while remaining difficult to reach. Drones help roof inspections become safer and more comprehensive by:
- High-resolution cameras mounted on drones capture complete images of the roof surface
- Identifying damaged shingles, tiles, or membrane materials
- Spotting potential water pooling areas
- Detecting signs of structural issues
The best part? Most drone roof inspections finish within one hour.
Facade and Exterior Wall Inspections
Tall buildings present obvious inspection challenges. Drones easily navigate around buildings to:
- Document the condition of all exterior surfaces
- Identify cracks, spalling concrete, or deteriorating mortar
- Assess window seals and cladding systems
- Spot water infiltration points
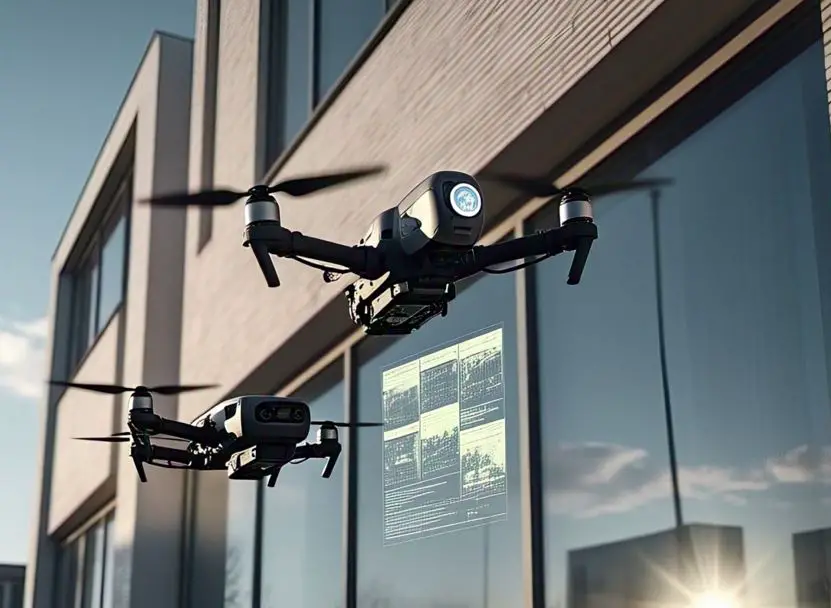
Infrastructure Inspections
Drones prove to be an indispensable tool when examining extensive infrastructure systems.
- Bridges and overpasses
- Water towers and tanks
- Communication towers
- Power plants and substations
The construction drone industry reached a market valuation of USD 3.9 billion in 2023 while analysts project its growth at a rate exceeding 8.5% CAGR throughout the forecast period. Infrastructure inspection applications are the main factor behind the observed growth.
Thermal Inspections
When equipped with thermal cameras, drones can:
- Identify heat loss through building envelopes
- Detect moisture intrusion and potential mold issues
- Find overheating electrical components
- Locate insulation gaps or failures
The features of drones establish them as essential tools for conducting energy audits and implementing preventative maintenance programs.
What to Look for in an Inspection Drone
Drones designed for building inspections vary significantly in their capabilities and performance. Here are the key features to consider:
Camera Quality
An inspection drone relies primarily on its camera system for functionality.
- Look for at least 4K video resolution
- 20+ megapixel still image capability
- Adjustable zoom functions
- Ability to tilt camera up and down
- Optional thermal imaging capabilities
Flight Performance
Reliable performance is crucial for inspection work:
- Wind resistance (at least 20 mph capability)
- Battery life (minimum 25-30 minutes per charge)
- Obstacle avoidance systems
- Precision hovering capabilities
- Return-to-home functionality
Software Integration
Today’s inspection drones need to come with features like live video streaming coupled with flight planning and data management systems. The estimated value of the global drone services market reached USD 6.6 billion in 2023 as many resources were allocated toward software solutions that improve inspection capabilities.
How to Start Implementing Drone Inspections
Ready to modernize your inspection process? Here’s how to get started:
Regulatory Considerations
Before launching your drone inspection program:
- Verify your operation follows FAA rules by obtaining Part 107 certification.
- Check local restrictions and airspace limitations
- Obtain necessary permits and insurance coverage
- Develop clear safety protocols
- Create privacy policies for data collection
Training Requirements
Effective drone inspection requires skilled operators:
- Commercial drone pilot certification
- Specific training on inspection techniques
- Understanding of building systems and common defects
- Data management and analysis skills
- Regular practice and skill development
Integration with Existing Processes
You can achieve maximum benefits by merging drone inspections into your existing operational processes.
- Develop standardized inspection checklists
- Develop systems that enable the storage and retrieval of inspection data.
- Establish clear reporting templates
- Train staff on interpreting drone-collected data
- Develop procedures to address problems that inspections have revealed
The Future of Drone Inspections
The drone inspection industry progresses quickly with new AI advancements in automatic defect identification, enhanced sensor systems, and increased flight independence. If you start using drone technology now you will be ready to take advantage of upcoming advancements.
Wrapping It All Up
Building inspections today benefit from drone technology, which has established new standards of safety and efficiency while delivering more thorough results than before. Market growth data demonstrates that drone technology has moved beyond temporary popularity to become a fundamental industry standard.
By implementing drone inspections, you can:
- Dramatically improve safety for your inspection team
- You can decrease your spending on both equipment rentals and workforce expenses.
- Complete inspections faster with less disruption
- Collect more detailed and actionable data
- Stay ahead of your competition
Companies operating in construction, property management, insurance and facility maintenance will find that drone inspections bring transformative operational benefits.
For your next building inspection you should think about using drones since they could provide your solution through a simple flight.