Fibre-reinforced polymer (FRP), commonly known as fibre-reinforced plastic, is a composite material comprised of a polymer matrix reinforced with fibres. Due to its simplicity of use and unique physical properties, fibre-reinforced polymer (FRP) has emerged as one of the most widely used techniques for repairing and renovating concrete infrastructure.
The fibres in the composite provide the required strength and stiffness and typically carry the majority of applied loads, while the polymer matrix functions to bind and protect the fibres as well as to enable the transfer of shear stresses from fibre to fibre.
Although other fibres like paper, wood, or asbestos have occasionally been utilized, glass, carbon, aramid and synthetic fibres are the most common types of fibre. The polymer is typically epoxy, vinylester, or polyester thermosetting plastic. FRP composites are nonconductive, noncorrosive, and lightweight materials with exceptionally high strength qualities. FRPs are frequently used in the construction, automotive, marine, and aerospace industries.
Composite Materials
Composite materials typically consist of two or more constituent materials that have very different physical or chemical properties yet continue to exist separately and independently inside the final structure. More often than not, the complimentary behaviour/action of the different materials defines the properties of the composite. Composite materials can be engineered or naturally occurring. Most composites have strong, stiff fibres in a softer, less rigid matrix.
Usually, the aim of engineered composite materials is to produce a component that is stiff and strong, and often times, with a low density. Glass or carbon fibres are frequently found in thermosetting polymer matrices used in commercial materials like epoxy or polyester resins. Since they can be moulded after initial production, thermoplastic polymers may occasionally be preferable.
There are further categories of composites where the matrix is made of metal or ceramic. Furthermore, the reasons for adding the fibres (or, in some cases, particles) to these composites are frequently quite complex; for instance, improvement in resistance to creep, wear, thermal stability, fracture toughness etc. may be desired.
Fibre-reinforced Polymers
Fibre-reinforced polymer composite materials are used in almost every type of advanced engineering structure, including aeroplanes, helicopters, spacecraft, boats, ships, and offshore platforms, as well as cars, sporting goods, machinery for processing chemicals, and civil infrastructure like bridges and buildings.
As these materials are employed more often in their present industries and start to dominate relatively new areas like those for biomedical devices and civil structures, their use is expanding at a remarkable pace. The construction industry accounts for about 26% of the FRP market share by application.
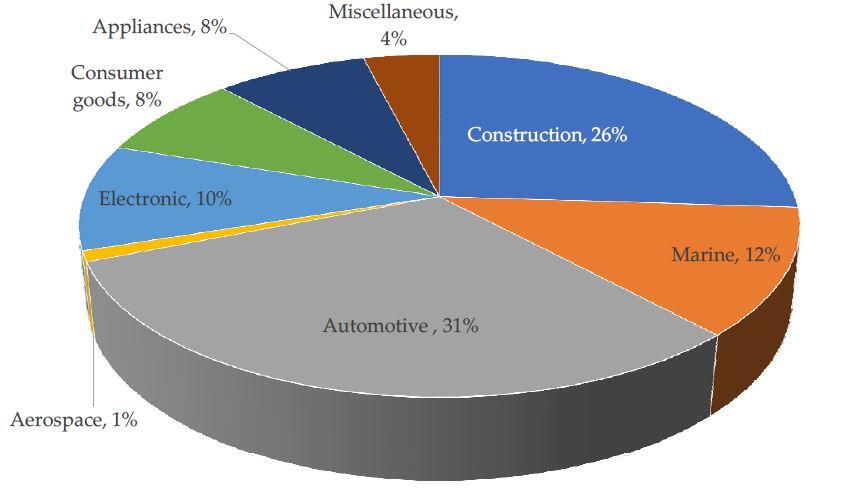
The creation of new cutting-edge forms of fibre-reinforced polymer materials has been a major element in the growth of composite applications in recent years. This includes innovative reinforcing techniques using carbon nanotubes and nanoparticles as well as advancements in high-performance resin systems.
The fibre-reinforced polymer composites (FRPs), which are made of classic civil engineering materials like concrete and steel, are increasingly being evaluated as an improvement to and/or replacement for infrastructure components or systems. In the structural engineering and building construction industry, three FRP types are typically used:
- Fibre-reinforced polymer profiles for new construction
- Fibre-reinforced polymer rebars, and
- Fibre-reinforced polymer strengthening systems
FRP composites are easy to produce, lightweight, non-corrosive, have high specific strength and stiffness, and may be customized to meet performance needs. FRP composites have been used in new construction and structure rehabilitation due to their beneficial properties. They are used as reinforcement in concrete, bridge decks, modular structures, formwork, and external reinforcement for strengthening and seismic upgrades.
FRP Reinforcements
Numerous research studies worldwide by professional associations and laboratories worldwide have actively investigated the use of fibre-reinforced polymer (FRP) reinforcements in concrete structures as an alternative to steel bars or prestressing tendons.
The benefits of FRP reinforcements are their resistance to corrosion, non-magnetic qualities, high tensile strength, lightweight, and simplicity of handling. However, they typically have a weak transverse or shear resistance and a linear elastic response in tension up to failure (referred to as a brittle failure).
Additionally, they have poor resistance when exposed to fire and extreme temperatures and are susceptible to the effects of stress-rupture and lose a significant amount of strength when bent. Furthermore, their price is expensive compared to traditional steel reinforcing bars or prestressing tendons, whether measured in terms of weight per unit or load-carrying ability.
The lack of plastic behaviour and the extremely low transverse shear strength of FRP reinforcements pose the most critical structural engineering issues. These properties, especially where coupled effects are present, like at shear-cracking planes in reinforced concrete beams where dowel action exists, may cause premature tendon rupture.
The dowel action lessens the tendon’s residual tensile and shear resistance. Solutions and usage restrictions have been provided, and future advancements are anticipated to continue. With rising market share and demand, it is anticipated that the unit cost of FRP reinforcements will drop dramatically. FRP reinforcements are still appropriate and cost-effective in several applications today.
FRP in Strengthening Applications
Existing structures deteriorate due to environmental factors, poor design, lack of maintenance, or unintentional occurrences. By strengthening these structures with FRP systems, they are not only restored but also strengthened. FRP is offered as strips, sheets, and textiles for strengthening.
Research, design, and practice have evolved significantly in the application of FRP as a strengthening material. Existing structures can be strengthened and repaired with FRP. Reinforcements that are externally bonded can be used to strengthen masonry, steel, concrete, and timber structures. Both Europe (CEB-FIP fib bulletin 14) and America (ACI 440.2R-17) have design guidelines for concrete structures strengthened using externally bonded FRP systems.
FRP strengthening can be prefabricated in a factory or applied on-site utilizing hand layup. Epoxy resin is applied by hand or in a wet layup process to woven fabric or flexible fibre sheets to create FRP sheets that are attached to concrete members.
These instances include the repair and strengthening of concrete structures using bonded FRP sheets or plates as well as the usage of FRP meshes, textiles, or fabrics in thin cement products. In relative terms, the cost of repairing and renovating a structure is invariably far more than the cost of the original structure.
Repair typically demands a considerable labour commitment but only a little amount of repair materials. Furthermore, the cost of labour is so high in developed nations that it overshadows the cost of materials. Therefore, the more cost-effective the repair, the higher the performance and durability of the repair material. This suggests that material cost is not actually a problem in repair and that the high cost of FRP repair materials is not an impediment.
FRP in New Building Construction
Pultruded fibre-reinforced forms are mostly used in all-FRP new-build constructions. Automatic pultrusion is a method for mass-producing constant section profiles. Although the FRP shapes behave like timber, they resemble structural steel components. As shown in Figure 2, the conventional profiles are created as I, H, C, leg-angle, and tubular sections.
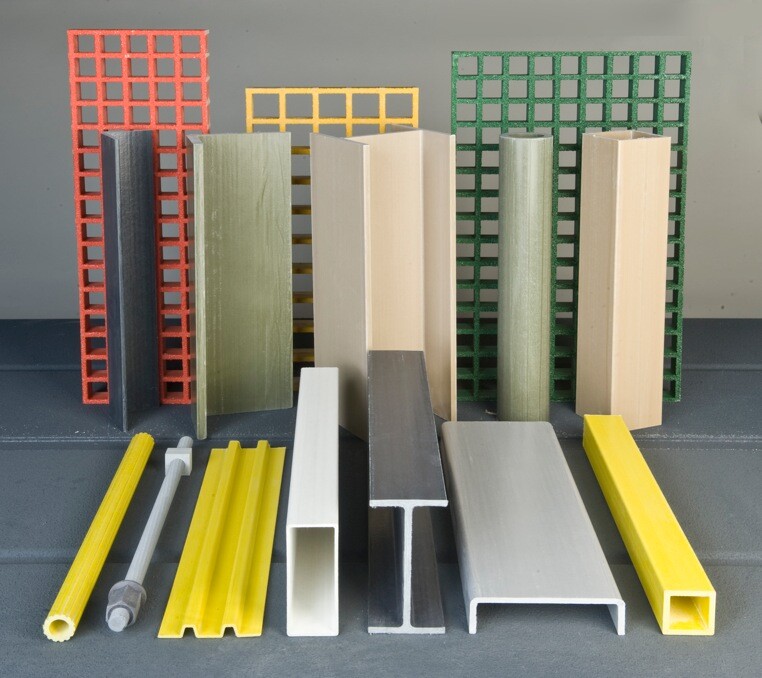
Furthermore, building systems, bridges, cooling towers, chemical and food processing factories, railroad platforms, and maritime structures have all incorporated FRP components. At the 1999 Swiss Building Fair, the first movable five-story FRP building, called Eyecatcher (Figure 3), was displayed. It was afterwards moved to another Basel location, where it is now used as an office building. Three parallel wooden frames with adhesive bonds made up the structure. The only places where bolted joints were employed were for disassembly.
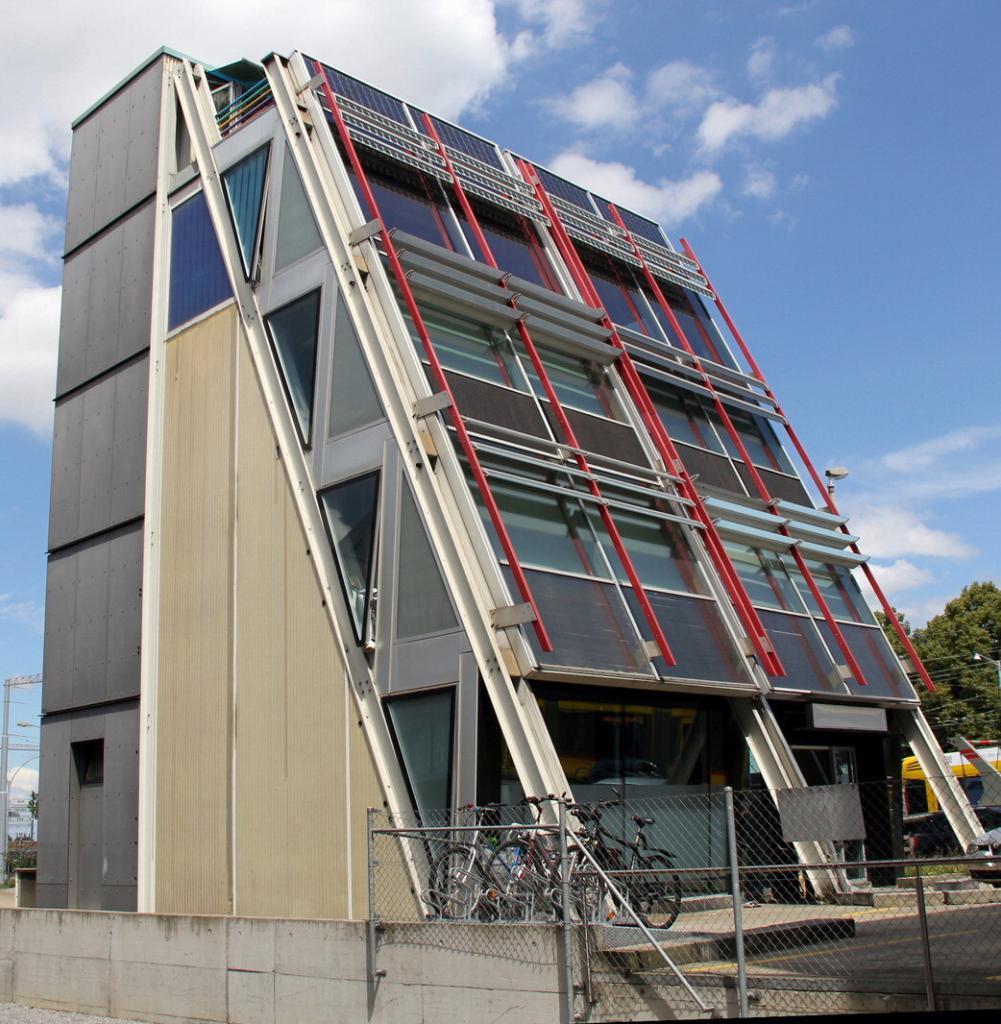
Sustainability of FRP in Construction
When it comes to FRP composites, environmental issues seem to be a hurdle to its viability as a sustainable material, particularly when taking into account the use of fossil fuels, air pollution, smog, and acidification during its manufacture. Additionally, it is difficult to recycle FRP composites, and unlike steel and wood, structural elements cannot be used again to serve the same purpose in another structure. However, a life cycle study of FRP composites used in infrastructure applications may reveal direct and indirect advantages that are more cost-effective than those of conventional materials.
On the surface, it would seem that the case for FRP composites in a sustainable built environment is questionable when merely looking at energy and material resources. However, this conclusion needs to be weighed against the potential benefits of using FRP composites, including those linked to factors like:
- Higher strength
- Lighter weight
- Higher performance
- Longer lasting
- Defence systems
- Space systems
- Ocean environments
- Seismic upgrades
- Existing structure rehabilitation and life extension.
Conclusion
Since their debut, composite materials have seen significant development. However, a number of requirements still need to be met before composite materials may be used as an alternative to conventional materials as part of a sustainable environment.
- The accessibility of standardized data on the durability characterization of FRP composite materials.
- Using FRP composites to anticipate the service life of structural members by integrating durability data and techniques.
- Creation of methodologies and methods for material selection based on analyses of the life cycles of structural parts and systems.
Composites must ultimately be structurally and economically practical in order to be taken seriously as an alternative. There are much research into the structural viability of composite materials in the literature. Since only recent data is available or only economic expenses are taken into account in the comparison, there are few studies on the viability of these materials from an economic and environmental standpoint from the perspective of a life cycle approach. Determining the long-term effects of employing composite materials is also necessary.
To determine if composite materials can be a component of a sustainable environment, the production byproducts, the sustainability of the constituent materials, and the potential for recycling composite materials must be evaluated.