In reinforced concrete buildings, it is almost impossible to carry out construction without lapping reinforcements at one point or another. This is due to obvious reasons such as ease of transportation and handling. Also at very long lengths, reinforcements will become unstable under their own weight when placed in a vertical position. Lapping (reinforcement splicing) is the traditional way that has been used to join two different reinforcements during construction. However, in recent times, mechanical splices (such as rebar couplers) have been introduced to make two different pieces of reinforcements joined together to behave as ‘one continuous unit’.
The three general methods identified for reinforcement splicing are;
- Lap splices
- Welded splices, and
- Mechanical splices
Read Also…
Detailing of columns to Eurocode 2
It is generally known that when reinforcements are lapped traditionally (lap splices), the two rebars will depend on the bond of the concrete for load transfer. However, with the use of mechanical splices concrete is not needed for load transfer since the two bars tend to behave as ‘continuous unit’. Furthermore, the idea of lapping is inherently wasteful and may lead to heavy congestion of reinforcement in a section of a concrete member. On the other hand, welding of bars is considered a more expensive alternative which may depend on the chemical properties of the reinforcing bar for adequate weldability.
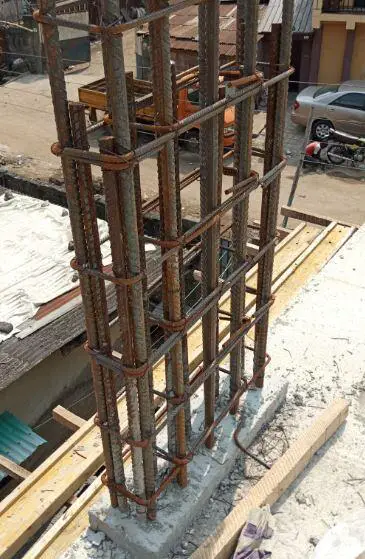
The advantages of using mechanical splices over lap splices in reinforcements are;
(1) Enhanced Structural Performance
The structural integrity of joints connected with the use of mechanical splices is enhanced since the connection does not need to rely entirely on concrete bond for load transfer. In seismic applications, mechanical splices tend to maintain structural integrity when bars are stressed into the inelastic range. On the other hand, lap splices can infringe into the plastic hinge region, which is in violation of code limitations.
(2) Saves design effort
In reinforced concrete design, the engineer is expected to carry out calculation of lap length, which can depend on the size and type of the reinforcement, the grade of the concrete, the bond condition, and concrete cover. But with the use of mechanical splices, such computational effort is eliminated.
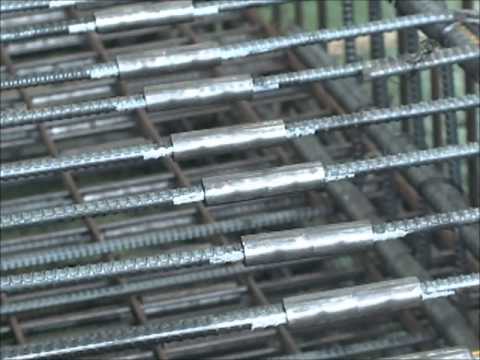
(3) Savings in Materials
With the use of mechanical splices, reinforcement bars do not overlap, thereby leading to savings in materials.
(4) Reduction in bar congestion
Lapping of reinforcement effectively doubles the steel-to-concrete ratio, and the resulting congestion can make the placement and consolidation of concrete difficult. Furthermore, the code limits the area of reinforcement in lap regions of columns to 0.08Ac. Using rebar couplers completely eliminates this challenge.
A peculiar disadvantage of mechanical splices is the extra step of preparation of bars required before couplers are installed. A special care is needed in cutting the threads correctly and to protect the threads from corrosion before installing the couplers as these reasons could lead to improper fixing of couplers.
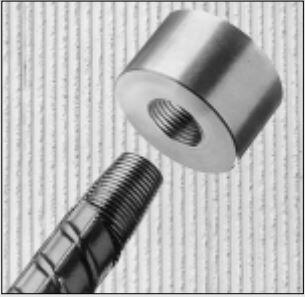
However in a research carried out in Sri Lanka in the year 2018, the additional cost incurred in preparation of bars which includes the cost of two machineries (forging machine and thread cutting machine) and additional workmanship (one electrician and an unskilled labourer), seems to produce attractive cost benefits compared to lap splicing for larger diameter bars such as 32 mm and 40 mm.
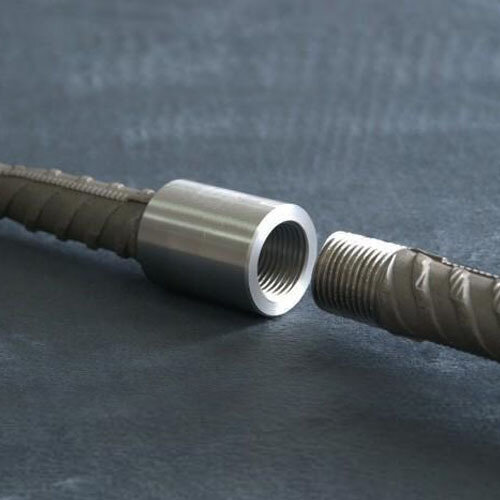
In a study to check the failure pattern of reinforcements joined using couplers, two failure modes were identified which are;
- Failure of the rebar, and
- Failure of connection
However, it was found that the failure stress of the bars which failed due to failure of connection is greater than the yield stress of steel and closer to the fracture point of steel. Due to the fact that the design stress of rebars is taken as the yield stress of steel and also due to the reduced stress in steel when steel are in contact with concrete, the risk of failure due to improper fixing of couplers may not be critical.