Architectural envelopes often utilize curtain walls, a type of lightweight, non-loadbearing external cladding which are attached to a framed structure to form a complete exterior sheath. They support only their own weight and wind loads, which are transferred via connectors at floor levels to the main structure.
For precision, BS EN 13830 defines curtain walling as “an external vertical building enclosure predominantly comprised of metallic, wooden, or plastic elements.” In essence, most curtain walls consist of vertical mullions (spanning floor to floor) connected by horizontal transoms. Infill panels, either glass or opaque, fill the resulting openings. Typically, such systems are constructed using proprietary systems provided by specialized metal fabricators.
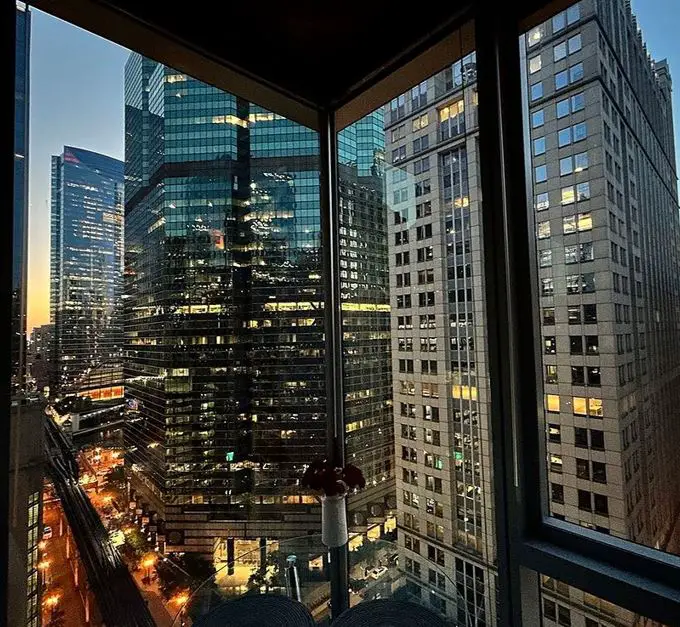
Objectives of Curtain Wall Systems
The primary objectives of using curtain-walling systems are to:
- Enclosure and Environmental Protection: Provide a comprehensive building envelope that protects the structure against external elements like wind, rain, and temperature fluctuations.
- Efficient Construction: Utilize dry construction methods, potentially streamlining the building process and minimizing disruptions at the site.
- Structural Optimization: Minimize the additional load placed on the building’s primary structure by the cladding system, enhancing overall structural efficiency.
- Architectural Expression: Offer a versatile design element to contribute to the building’s overall aesthetic and architectural intent.
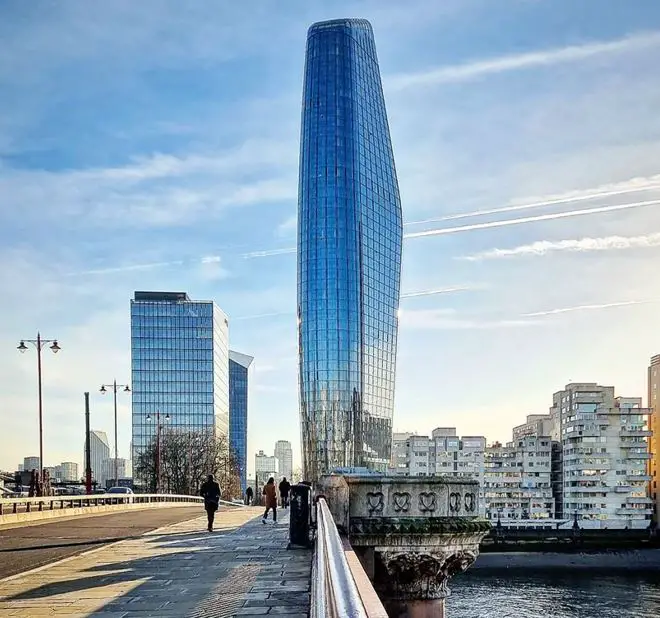
Functional Requirements of Curtain Walls
The following are the functional requirements of curtain walls.
Weather Resistance
Curtain walls are expected to protect the interior of the building from the weather conditions of the exterior. While the materials of the curtain wall themselves typically offer excellent impermeability, joints within curtain walls present potential vulnerabilities. Careful design and implementation are crucial to ensure weather resistance. Therefore, achieving weather resistance relies on meticulous design and construction. Two approaches exist:
1) Impervious joints: utilizing sealants and gaskets to entirely prevent water entry, mimicking the material’s impermeability.
2) Drained joints: acknowledging potential water ingress but strategically channelling it away through dedicated drainage systems. Both methods require consideration of thermal expansion, structural shifts, and moisture movement, with appropriate materials and skilled installation being crucial for long-term success.
Internal Temperature Control
While large glass areas in curtain walls offer stunning aesthetics, they pose challenges in temperature control. The low heat resistance allows heat transfer and solar radiation to warm internal surfaces, creating uncomfortable heat build-up. Fixed louvres within the system offer limited heat gain reduction, primarily addressing glare. External louvres provide marginal improvement by absorbing and re-radiating heat outwards.
Effective solutions include:
- Deep recessed windows: Coupled with external vertical fins, these create shading pockets to reduce solar heat gain.
- Balanced HVAC systems: These actively manage internal temperature through heating and ventilation for year-round comfort.
- Special solar control glass: Reflective glass with metallic or dielectric coatings deflects solar radiation, reducing heat gain. Tilting the glass further enhances its effectiveness.
Sufficient Structural Strength
While non-loadbearing, curtain walls require sufficient strength to withstand their own weight and varying wind pressures. Wind load intensity depends on three key factors: building height, exposure level, and location.
Curtain wall strength hinges on the rigidity of its vertical mullions and their secure anchorage to the building frame. Glazing beads and compressible materials further enhance resilience against wind damage by allowing panels to move independently within the system, minimizing stress on the overall frame.
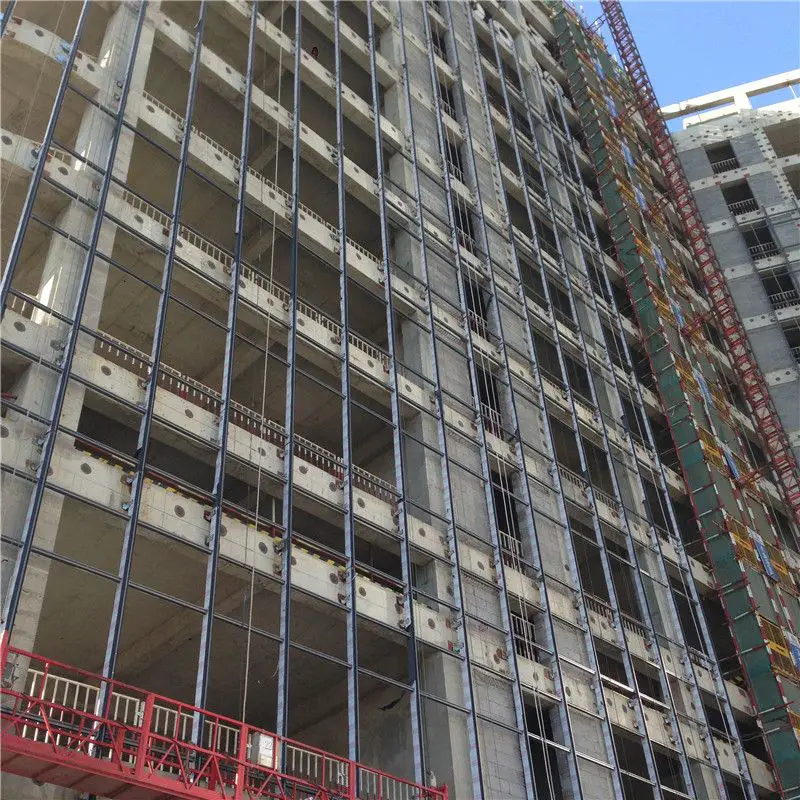
Fire Resistance
The high percentage of unprotected areas in curtain walling systems, as defined in Building Regulations (Approved Document B4: Section 12.7), poses a significant fire resistance challenge. To achieve compliance and ensure occupant safety, architects and engineers must carefully select cladding materials or material combinations for opaque infill panels.
These materials should possess inherent fire resistance properties or be treated with fire-retardant coatings to qualify as protected areas as defined in the regulations. For further guidance on external fire spread considerations, refer to Part 7 of the same document.
Assembly and Fixing
The mullion, typically a solid or box section member, forms the backbone of a curtain wall system. It securely connects to the building’s structural frame at floor levels using adjustable anchorages or connectors, ensuring proper load transfer and stability. The infill framing and panels can be delivered as individual components requiring on-site assembly, or as prefabricated units for faster installation. When evaluating different systems, key considerations include:
- Handling ease: Can the individual components or prefabricated units be safely and efficiently manoeuvred on-site, considering their size and weight?
- Site assembly: Is extensive field assembly required, potentially impacting construction time and labour costs?
- Access to fixing points: Can workers readily access and secure the curtain wall to the building structure at all designated anchor points?
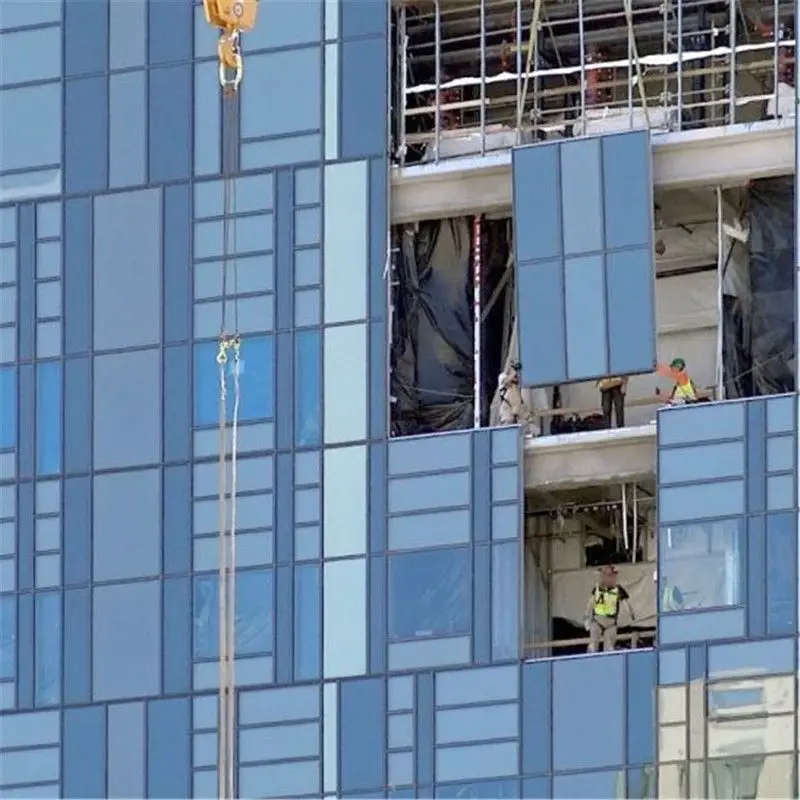
Sound Insulation
Curtain wall systems, due to their inherent lightweight nature, present challenges in terms of sound insulation. Both structure-borne and airborne sound transmission must be addressed to ensure a comfortable and acoustically controlled indoor environment.
- Structure-borne sound: Primarily originating from machinery vibrations, this type of sound can be mitigated by isolating offending equipment with resilient pads or incorporating resilient connectors within the mullion connections. Careful equipment selection and placement can further contribute to reducing vibrations at their source.
- Airborne sound: Lightweight cladding offers minimal inherent sound barrier, making glazed areas particularly vulnerable to sound transmission. Strategies to reduce airborne sound transmission include:
- Minimizing glazing area: Utilizing less glazing or opting for smaller window sections can significantly reduce sound ingress.
- Sealed windows with thicker glass: Implementing sealed windows with thicker glass panels increases the mass barrier, thereby enhancing soundproofing capabilities.
- Double-glazing: Installing double-glazed windows with an air gap of 150-200mm between the panes creates a significant barrier for sound waves, offering superior sound insulation performance.
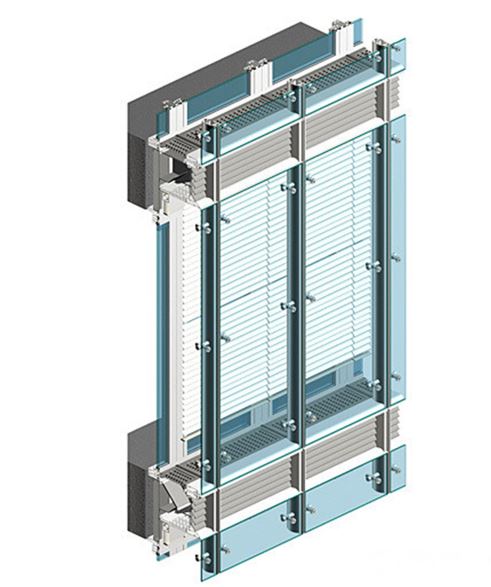
Thermal and Structural Movements
Curtain wall systems, positioned on a building’s exterior, face heightened exposure to temperature fluctuations compared to the internal structure. This translates to significant thermal movement within the curtain wall itself, as well as potential differential settlement between the main frame and attached cladding. To accommodate these independent movements, careful design, fabrication, and fixing are crucial.
Key considerations:
- Slotted bolt connections: These connections offer flexibility at attachment points between the curtain wall and the building frame, allowing for controlled thermal expansion and contraction without compromising structural integrity.
- Spigot connections: Within the curtain wall system, spigot connections join components while permitting controlled movement. This flexibility mitigates stresses caused by thermal expansion and contraction within the system itself.
- Mastic-sealed joints: These flexible sealant joints further accommodate movement by allowing slight shifts between individual curtain wall components while maintaining weather resistance.
Infill Panels for Curtain Wall Systems
Curtain wall infill panels, responsible for opaque areas, require specific characteristics to ensure optimal performance and longevity. These include:
- Lightweight construction: Minimizes overall system weight, reducing structural loads and facilitating handling.
- Rigidity: Ensures dimensional stability and resistance to deflection under wind loads and thermal stresses.
- Impermeability: Prevents water ingress and maintains weathertightness of the building envelope.
- Adequate fire resistance: Complies with relevant building regulations to ensure occupant safety in case of fire.
- Thermal insulation: Minimizes heat transfer and contributes to energy efficiency.
- Low maintenance: Requires minimal upkeep for sustained performance and aesthetic appeal.
Panel Construction and Vapour Control:
No single material possesses all these attributes, necessitating the use of composite or sandwich panels. However, such panels pose a risk of interstitial condensation, which can be mitigated by incorporating a vapour control layer near the inner panel surface. This layer, with a vapour resistance exceeding 200 MN/g, can be formed using various materials:
- Adequately lapped sheeting: Aluminium foil, waterproof building papers, or polyethylene sheet
- Applied materials: Two coats of bitumen or chlorinated rubber paint
Careful placement is crucial to avoid detrimental interactions between adjacent materials, such as alkali attack on aluminium when in contact with concrete or fibre cement.
External Facing Materials:
Direct exposure to the elements necessitates careful selection of external-facing materials. Plastics and plastic-coated options are viable choices if they comply with fire regulations outlined in relevant documents. One popular choice is vitreous enamelled steel or aluminium sheets (0.7-0.8mm thickness).
This process fuses a thin glass coating onto the metal surface at high temperatures, resulting in:
- High hardness and impermeability: Resisting damage from acids, corrosion, and abrasion.
- Crack and craze resistance: Maintaining an attractive finish with lasting strength.
Alternatively, aluminium sheeting with a silicone polyester coating can be employed. By combining these facings with insulating materials like EPS, rockwool, polyurethane, or polyisocyanurate, lightweight infill panels achieving U-values below 0.35 W/m²K can be produced.
Furthermore, both internal and external surfaces must meet fire performance requirements outlined in building regulations, often tested according to specific standards. The insulating core must also exhibit non-combustible properties. Panel dimensions can reach up to 3000mm x 1000mm.
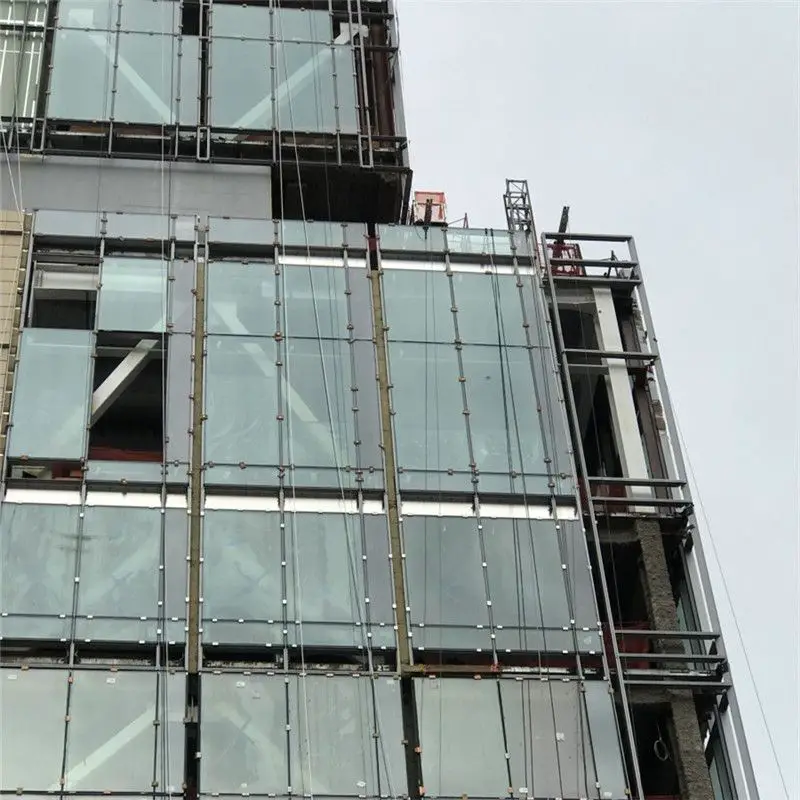
Glazing for Curtain Wall Systems
One critical aspect of curtain walls is glazing—the use of glass in large, uninterrupted areas to create consistent and attractive facades. While protecting the building interior from the elements remains the principal objective of facade materials, the function of glazing transcends mere weather tightness. It plays a pivotal role in orchestrating two key aspects of the built environment:
1. Daylight-Driven Illumination:
Glazing serves as a conduit for natural light, not only fulfilling the basic requirement of illuminating interior spaces but also contributing demonstrably to occupant well-being and energy conservation efforts. However, solely relying on daylight to sufficiently illuminate specific tasks necessitates meticulous consideration of several factors. Window size, placement, and calculated daylight factors all come into play in ensuring adequate and appropriate natural light distribution for dedicated work areas.
2. Fostering Visual Connection with the Exterior:
Beyond illumination, glazing fulfils a psychological need by establishing a visual connection with the surrounding environment. This connection has been demonstrably linked to enhanced occupant well-being, underlining the importance of thoughtful planning when incorporating glazed areas. Size, orientation, and the quality of the view obtained through these areas are crucial aspects to consider during the design phase.
As discussed earlier in this article, other critical considerations pertaining to glazing selection include managing solar heat gain, glare control, thermal insulation performance, and acoustic properties. Therefore, these aspects shall not be revisited here.
Cleaning and Maintenance of Curtain Walls
The use of expansive glazing in high-rise structures, particularly in curtain walling systems, presents a significant challenge: safe and cost-effective access for cleaning and maintenance. While manual cleaning with tools like swabs, chamois leathers, and squeegees remains the standard method, access becomes paramount. Neglected cleaning causes the following problems on curtain wall glazings:
- Aesthetic Integrity: Accumulation of dirt distorts the intended visual appearance.
- Daylight Transmission: Optimal natural light penetration requires clean surfaces.
- Visual Clarity: Unobstructed views are essential for occupants and aesthetics.
- Material Integrity: Glazing materials are susceptible to deterioration from dirt and chemical attack.
For low- to medium-rise structures, access solutions like trestles, stepladders, and straight ladders (up to 11 meters) suffice. However, taller buildings necessitate alternative approaches:
- Tower Scaffolds: While offering access, their assembly and disassembly time and cost make them impractical for frequent cleaning.
- Lightweight Scaffolds: Quick-install systems can be considered for moderate heights (up to 6 meters) due to their efficiency.
High-rise curtain wall cleaning predominantly relies on suspended cradles. These come in two forms:
- Temporary Cradles: These offer flexibility but must be dismantled and reassembled each time.
- Permanent Systems: Integrated into the building structure, they offer readily available access but carry higher upfront costs.
The simplest permanent solution involves installing a universal beam section at roof level, extending 450 mm beyond the facade and encircling the building. A conventional cradle with castors on its lower flange runs along this beam, controlled by ropes lowered to ground level for access.
While challenges exist, a range of options ensures the cleanliness and integrity of high-rise glazed facades, contributing to both aesthetics and occupant well-being.