Damp proof course (DPC) and damp proof membrane (DPM) are two important elements in building construction that play a vital role in preventing moisture ingress (rising damp) through capillary action into a building. Their presence ensures the durability and integrity of buildings by preventing dampness of walls and floors.
It is a building regulation requirement that the elements of a building such as the walls, roof, and floors be designed and constructed in such a way that the building and the people in it shall not be negatively affected by ground moisture, precipitation, condensation, or spillage of water from the plumbing system.
Building elements in direct contact with the ground, such as walls and floors, are particularly susceptible to moisture movement through capillary action. This can lead to a range of detrimental effects, including structural degradation, mould growth, and poor indoor air quality. To mitigate these concerns, damp proofing measures are essential components of a well-designed building envelope.
A DPC is a continuous horizontal barrier integrated within the masonry wall construction. Its primary function is to impede the upward capillary rise of moisture from the ground into the building elements above. This prevents water migration through tiny pores within the wall material. However, a DPM is a sheet material laid horizontally beneath floor slabs or other elements in direct contact with the ground. Its primary function is to prevent moisture transmission from the ground into the building elements above.
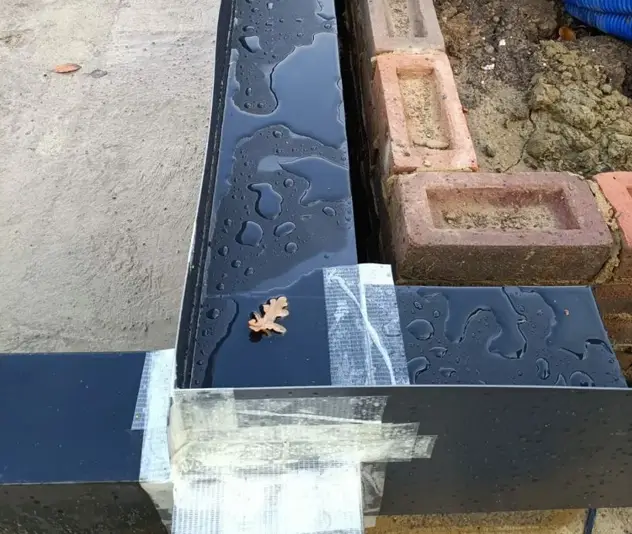
Construction Details of DPC and DPM
Damp proof courses (DPCs) and damp-proof membranes (DPMs) should be clearly detailed and represented in construction drawings due to their importance. However, particular attention must be paid to the junction where walls and solid floors meet. Failure to ensure proper continuity at these critical intersections can compromise the effectiveness of the entire damp-proofing system and create pathways for moisture penetration.
An important consideration involves identifying the optimal material for these intersections. A wide variety of materials possess varying properties in terms of waterproofing capabilities and compatibility with the surrounding building elements. A thorough analysis is required to select the material that best addresses the specific conditions encountered at each junction.
The conventional symbol used to represent damp-proof layers in construction drawings may not always accurately depict the actual thickness of these layers. For particularly thin DPCs and DPMs (less than a few millimetres), representing them to scale on drawings can prove challenging. This can lead to ambiguities in interpretation during construction.
The proposed solution to address the challenge of symbolizing thin damp proofing layers in drawings prioritizes clarity and effectiveness. DPCs and DPMs can be represented with a thickness that exceeds their actual scale. The necessary additional space can be accommodated by reducing the depicted thickness of adjacent building elements on one side of the damp proofing layer.
Importantly, dimensions should always be provided for one face of the damp proofing layer where the adjacent material is shown at full scale. This approach ensures clear communication of the damp proofing system without compromising the overall representation of the construction details.
What is a Damp Proof Course (DPC)?
A damp proof course (DPC) is a horizontal barrier installed in a wall to prevent the upward movement of moisture from the foundation or surrounding soil. It is typically a thin layer of impermeable material, such as concrete, asphalt, bitumen, or plastic, that is embedded in the mortar course of a wall. The primary function of a DPC is to prevent dampness from rising up the wall and entering the building, which can lead to structural damage, decay, and health issues.
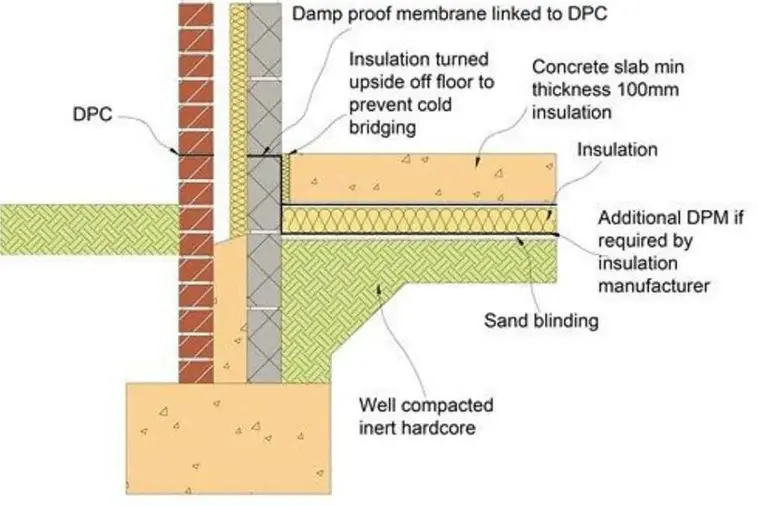
In order to effectively impede rising damp, the damp-proof course (DPC) must adhere to the following stipulations:
- Continuity: The DPC shall be continuous and seamlessly integrated with any damp-proof membrane (DPM) present within the floor structure.
- External Wall Height: For DPCs situated within external walls, their elevation must be a minimum of 150 mm above the adjoining ground level.
- External Cavity Walls: In instances where the DPC is located within an external cavity wall, the cavity itself must extend downward at least 225 mm below the DPC. Alternatively, a cavity tray equipped with weep holes spaced at regular intervals of 900 mm can be employed. These weep holes serve the critical function of enabling the drainage of water accumulating within the cavity, thereby preventing its transmission to the inner wall leaf.
Properties of a DPC Material
An effective material for a damp proof course (DPC) in buildings should possess the following key properties:
- Imperviousness: The primary function of a DPC is to impede moisture ingress. Therefore, the chosen material must be highly resistant to water penetration, acting as a reliable barrier against rising damp.
- Strength and Durability: The DPC is positioned within the building envelope, where it is subjected to various loads, both static (dead) and dynamic (live). Consequently, the material needs to be demonstrably strong and durable to withstand these stresses without sustaining damage or compromising its effectiveness.
- Dimensional Stability: Over time, fluctuations in temperature and humidity can cause certain materials to expand or contract. To ensure the DPC’s continued functionality, it’s crucial to select a material with good dimensional stability, meaning it will maintain its size and shape throughout its service life.
- Chemical Compatibility: The DPC comes into contact with other building materials, such as mortar and concrete. To prevent adverse chemical reactions that could deteriorate the DPC or surrounding elements, the chosen material should exhibit compatibility with these substances.
- Resistance to Salts: Certain salts, like sulfates, chlorides, and nitrates, can be detrimental to the DPC’s performance. Therefore, the material should be resistant to the presence of these salts to safeguard its integrity.
In addition to these core properties, other factors such as cost-effectiveness and ease of installation may also be considered when selecting a suitable DPC material.
Types of DPC
BS 743:1970 provides a list of materials that are deemed suitable for the construction of damp proof courses;
- Lead
- Copper
- Bitumen
- Mastic asphalt
- Polythene
- Slates
- Bricks
- Materials for mortar
Lead or copper sheeting
- A highly durable and effective material for DPCs, but also the most expensive.
- Lead and copper are naturally water-resistant and can last for many years.
- However, lead is a hazardous material and its use is restricted in some countries.
Bitumen
- A common and cost-effective material for DPCs.
- It is a waterproof material that is applied as a hot liquid or sheet membrane.
- However, bitumen can be brittle and can crack over time, especially in cold weather.
Mastic asphalt
- A semi-rigid material made from bitumen, sand, and filler.
- It is more flexible than bitumen and can accommodate some movement in the wall.
- Mastic asphalt is also more resistant to cracking than bitumen.
Slates and cement mortar
- A traditional material for DPCs, consisting of two layers: a layer of slate and a layer of cement mortar.
- Slates are naturally water-resistant and provide a solid base for the DPC.
- Cement mortar helps to bond the slates together and create a waterproof seal.
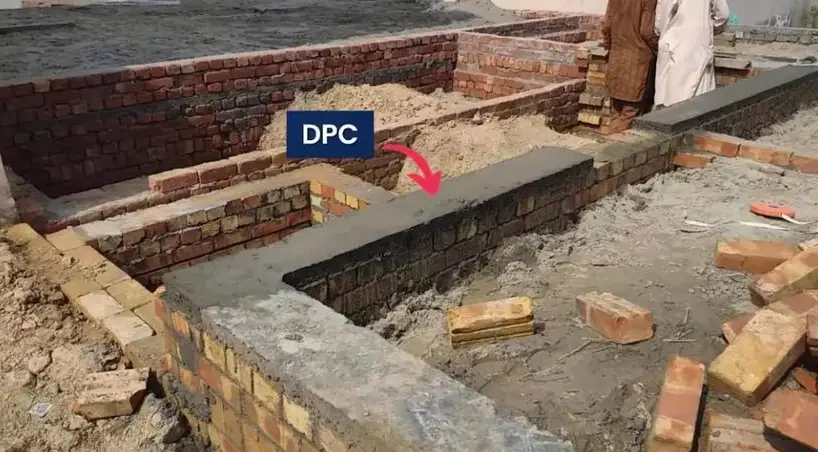
Engineering bricks
- A type of brick that is made to be highly water-resistant.
- Engineering bricks can be a good alternative to bitumen or plastic sheet membranes.
- They are also more resistant to damage from building movement than other DPC materials.
Chemical DPC
- A relatively new type of DPC that is injected into the wall.
- Chemical DPCs create a water-repellent barrier within the wall itself.
- They are a good option for walls that are already built, as they can be installed without disturbing the existing structure.
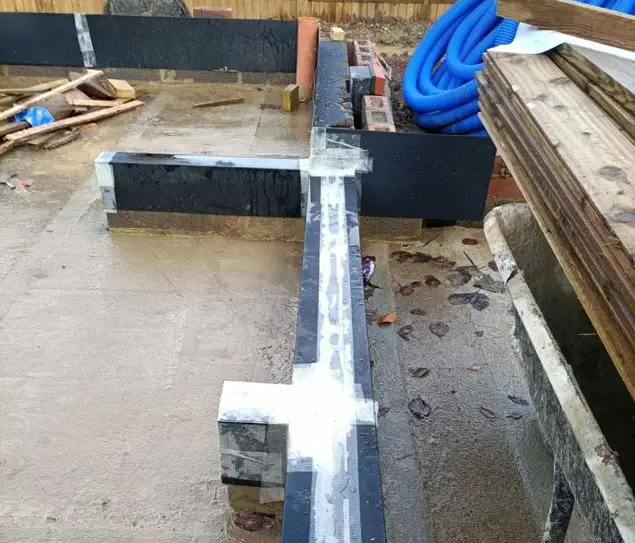
Concrete as a DPC Material
Concrete can be a viable DPC option, particularly for low-moisture environments and standard wall thicknesses. However, its limitations in impermeability and salt resistance should be considered. However, concrete is a commonly used material for DPCs due to its several advantages such as wide availability, strength, durability, and ease of construction.
While concrete offers some resistance to moisture, it’s not entirely impermeable. Over time, tiny cracks can develop, allowing moisture ingress. This is because concrete is brittle and can crack under excessive movement or stress, potentially compromising its effectiveness. Concrete can also be susceptible to degradation from salts like sulfates and chlorides commonly found in soil.
The following approach can be adopted to enhance the performance of concrete as a DPC material:
- Mix Design: Using a richer concrete mix (lower water-cement ratio) can improve its impermeability.
- Waterproofing Additives: Adding waterproofing admixtures to the concrete mix can further enhance its moisture resistance.
- Bitumen Coating: Applying a hot bitumen layer on top of the concrete DPC can provide additional waterproofing.
What is Damp Proof Membrane (DPM)?
A damp proof membrane (DPM) is a thin, impermeable layer that is applied to the surface of a wall or floor to prevent moisture ingress. Unlike a DPC, which is embedded in the mortar course, a DPM is a separate layer that is typically applied to the surface of the substrate. A minimum thickness of at least 1200 gauge (300 micrometres) is recommended for DPMs. This ensures sufficient strength and puncture resistance.
DPMs are commonly used in flooring applications, such as under concrete slabs or screeds, to prevent moisture from rising up from the ground.
Types of DPM
Damp proof membranes are typically made of high-density polyethylene (HDPE) or polyvinyl chloride (PVC). Other materials like asphalt sheet membranes might be used in specific situations. Generally, there are several types of DPM materials available, including:
- Polyethylene DPM: A popular choice due to its durability and water resistance.
- Polypropylene DPM: A flexible and versatile option that can be used in a variety of applications.
- PVC DPM: A cost-effective option that provides good water resistance.
- Bitumen-based DPM: A durable and water-resistant option that is suitable for a range of applications.
However, the chosen DPM material should be compatible with other building materials it comes in contact with, like concrete or screed. Certain chemicals in incompatible materials might degrade the DPM over time.
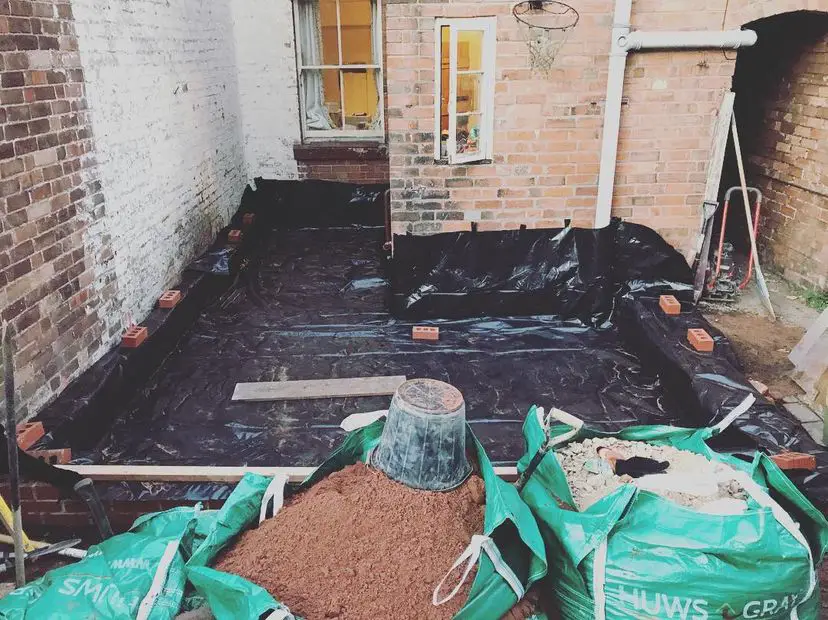
Properties of DPM
These materials offer several key properties that make them suitable for damp-proofing applications:
- Impermeability: HDPE and PVC possess excellent water resistance, effectively preventing moisture transmission through the membrane.
- Durability: DPMs are designed to withstand harsh environmental conditions and maintain their performance over time. They are resistant to degradation from UV exposure, chemicals commonly found in soil, and biological attack.
- Flexibility: Compared to rigid materials like concrete, DPMs offer a degree of flexibility, allowing them to accommodate slight movements in the building structure without compromising their effectiveness.
- Puncture Resistance: While flexible, DPMs are also reasonably puncture resistant, especially when appropriate installation methods are followed.
- Cost-Effectiveness: Compared to some alternative DPC materials like lead or copper sheeting, DPMs offer a cost-effective solution for damp-proofing.
Installation Considerations
Proper installation is critical for the optimal performance of DPMs. Here are some key factors to consider:
- Surface Preparation: The substrate where the DPM will be laid needs to be clean, level, and free from sharp objects that could puncture the membrane. DPMs are typically laid on a layer of sand or blinding to provide a smooth and level surface for the membrane. Sometimes, a DPM might be installed above the concrete floor slab.
- Overlaps and Joints: Overlaps of at least 150mm (preferably 300mm) at the edges of the membrane are essential to create a continuous barrier. Joints can be sealed with high-quality self-adhesive tape or heat welding for a watertight connection.
- Wall Termination: The DPM should be turned up the wall at a minimum height (typically to the level of the DPC) and integrated with the wall DPC material to create a continuous moisture barrier.
- Flashings and Penetrations: Any penetrations through the DPM, such as for pipes or cables, require proper flashing details to maintain water-tightness.
- Protection: DPMs are susceptible to damage during construction. Protecting the membrane from puncturing using a sand-blinding layer or dedicated DPM protection boards is essential.
I WANT TO BECOME A PROMINENT BUILDER