A crane can be defined as a mechanical system employing a rope or cable system to lift loads. The significant increase in the utilisation of tower cranes within the construction sector can be attributed, in large part, to the increasing prevalence of prefabricated components in contemporary structures.
Cranes are also indispensable equipment in the construction of highrise buildings, due to the need to lift different kinds of materials and equipment to higher floors. Given the vast array of available crane types, selecting the optimal equipment necessitates a rigorous and systematic approach, informed by economic considerations, technical specifications, site-specific limitations, and anticipated utilisation.
The cranes that are used in the construction industry can be categorised into three broad groups which are:
- Mobile Cranes: Characterized by their inherent mobility and flexibility of deployment.
- Static or Stationary Cranes: Defined by their fixed positioning, offering stability and extended reach.
- Tower Cranes: Distinguished by their vertical mast structure, facilitating efficient operations on high-rise projects.
The focus of this article is on the use of tower cranes in the construction industry.
Tower Cranes
The tower crane has been widely adopted by the construction industry as an equipment for erecting medium- to high-rise structures since its introduction in 1950 by the Department of Scientific and Industrial Research. Tower cranes are available in various configurations, including horizontal jibs with a saddle or trolley, and luffing or derricking jibs with a lifting hook at the end. Horizontal jibs can bring the load closer to the tower, while luffing jibs can be raised to clear obstructions such as adjacent buildings, which is an advantage on confined sites.
Types of Tower Cranes
Tower cranes can be classified into four basic types:
- self-supporting static tower cranes,
- supported static tower cranes,
- travelling tower cranes, and
- climbing tower cranes.
Self-supporting static tower cranes
Self-supporting static tower cranes generally have a greater lifting capacity than other types of cranes. The mast of the self-supporting tower crane must be firmly anchored at ground level to a concrete base with holding-down bolts or alternatively to a special mast base section cast into a foundation.
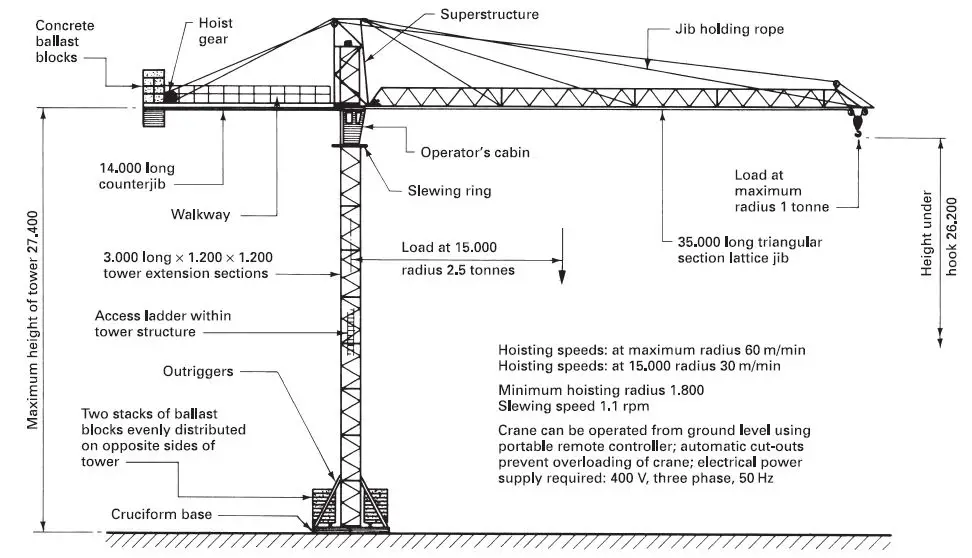
They are particularly suitable for confined sites and should be positioned in front or to one side of the proposed building with a jib of sufficient length to give overall coverage of the new structure. Generally, these cranes have a static tower, but types with a rotating or slewing tower and luffing jib are also available.
Supported static tower cranes
Unlike self-supporting tower cranes, which rely solely on their anchored base for stability, supported static cranes leverage additional anchor points on the rising structure itself. This symbiotic relationship allows them to reach greater heights than their self-supporting tower cranes, often exceeding 300 meters.
The supporting structure typically employs single or double steel stays, strategically connected to the building at specific intervals. These stays transfer the crane’s loads and wind forces into the building, requiring careful analysis and robust structural design to handle the induced stresses.

Their masts rely on single or double steel stays anchored to the structure for enhanced stability, necessitating a robust supporting structure to handle the induced stresses. Supported tower cranes usually have horizontal jibs, because the rotation of a luffing jib mast renders it unsuitable for this application.
Advantages
- Unmatched Height: As mentioned earlier, supported static cranes reign supreme in conquering ambitious heights, making them ideal for skyscrapers and other tall structures.
- Reduced Site Footprint: Compared to self-supporting cranes, which require a large base area, supported cranes can be positioned closer to the building, maximizing valuable site space.
- Cost-Effectiveness: In certain scenarios, utilizing a supported static crane can be more economical than opting for multiple self-supporting cranes for a multi-phased project.
- Flexibility: Supported static cranes can come equipped with horizontal or luffing jibs, catering to diverse lifting requirements and site constraints.
Considerations for Careful Deployment
- Structural Analysis: The building must be designed to accommodate the additional loads and stresses induced by the crane’s stays.
- Installation Expertise: Rigging and anchoring the stays require specialized knowledge and meticulous execution to ensure safety and stability.
- Maintenance: Regular inspections and adjustments of the stays and crane components are crucial for maintaining optimal performance and preventing potential hazards.
- Site Coordination: Close collaboration between crane operators, construction workers, and structural engineers is essential throughout the project to ensure seamless integration and safety.
Travelling Tower Cranes
Unlike their static tower cranes that are tied to a single location, travelling tower cranes move along horizontal tracks. These tracks provide a stable platform for the crane’s heavy-duty bogies. This unique setup grants travelling cranes the freedom to roam, easily covering expansive areas in a construction site.
Travelling tower cranes move on heavy-wheeled bogies mounted on a wide-gauge (4.200 m) rail track with gradients not exceeding 1 in 200 and curves not less than 11.000 m radius depending on mast height. The base for the railway track sleepers must be accurately prepared, well-drained, regularly inspected, and maintained to ensure the stability of the crane.
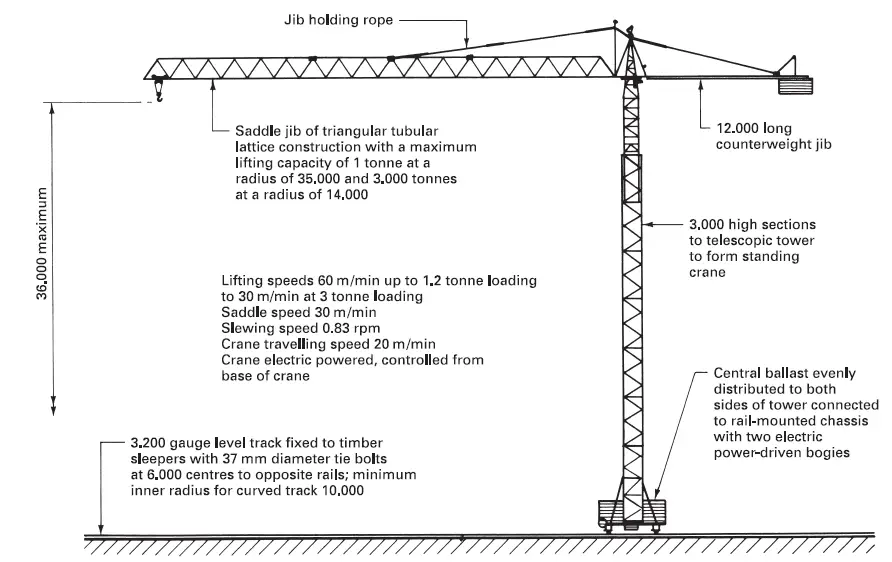
The motive power is from electricity, the supply of which should be attached to a spring-loaded drum, which will draw in the cable as the crane reverses to reduce the risk of the cable becoming cut or trapped by the wheeled bogies. Travelling cranes can be supplied with similar lifting capacities and jib arrangements as given for static cranes.
Advantages
- Enhanced Site Coverage: With their ability to traverse the length and breadth of the site, travelling cranes eliminate the need for multiple static cranes, streamlining operations and optimizing resource allocation.
- Flexible Positioning: Precise control over the crane’s location allows for targeted material placement and efficient lifting operations tailored to specific construction phases.
- Reduced Footprint: Travelling cranes require a smaller base area compared to static cranes, freeing up valuable space for other site activities and equipment.
- Cost-Effectiveness: In situations where site coverage demands are significant, a single travelling crane can often be a more cost-effective solution than deploying multiple static cranes.
Considerations for Optimal Deployment
- Track Design and Maintenance: The track system must be carefully designed and meticulously maintained to ensure smooth crane movement and prevent derailment.
- Power Supply: Reliable and uninterrupted power supply is crucial for crane operation and safety.
- Site Layout and Obstacles: Careful planning is required to navigate any obstructions on the site and ensure sufficient clearance for the crane’s movement.
- Wind Load and Stability: Understanding wind loads and implementing appropriate safety measures is paramount for maintaining stability, especially with mobile cranes.
Climbing Tower Cranes
As buildings go higher, so too do climbing tower cranes. Unlike their static or mobile counterparts, these cranes reside within the very structures they help erect, offering unique advantages and considerations for ambitious high-rise projects.
Tower cranes that are designed for tall buildings are located within and supported by the structure under construction. The mast, which extends down through several storeys, requires only a small opening of 1.500 to 2.000 m square in each floor. Support is provided at floor levels by special steel collars, frames, and wedges.
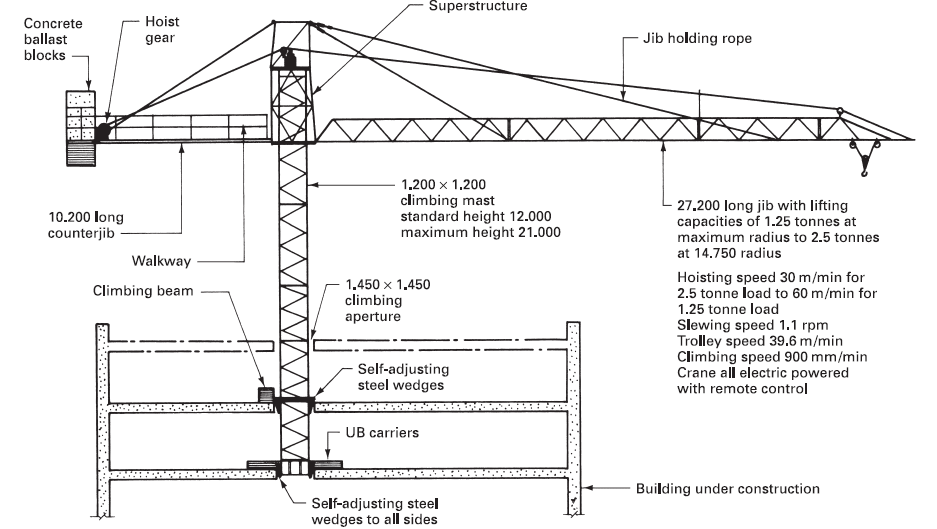
The raising of the static mast is carried out using a winch that is an integral part of the system. Generally, this form of crane requires a smaller horizontal or luffing jib to cover the construction area than a static or similar tower crane. The jib is made from small, easy-to-handle sections, which are lowered down the face of the building when the crane is no longer required, by means of a special winch attached to one section of the crane. The winch is finally lowered to ground level by hand when the crane has been dismantled.
Advantages
- Unmatched Vertical Reach: Climbing cranes effortlessly scale alongside the structure, eliminating the need for multiple relocations and significantly extending project horizons.
- Reduced Site Footprint: By residing within the building itself, climbing cranes free up valuable ground space for other equipment and materials.
- Enhanced Safety: Their internal position shields them from wind gusts and other external hazards, improving overall safety on the construction site.
- Cost-Effectiveness: Climbing cranes can offer a more cost-efficient solution for tall buildings compared to employing multiple static or mobile cranes at different stages.
Erection of Tower Cranes
Prior to initiating the erection of a tower crane, careful consideration must be given to its optimal positioning within the construction site. As with all construction equipment, maximizing the utilization of the crane to achieve the project objectives is paramount.
Achieving this objective necessitates a central location within reach of material storage areas, loading zones, and active construction zones. Generally, the expected output of a tower crane ranges from 18 to 20 lifts per hour. Therefore, meticulous planning and coordination of the crane’s operational sequence are crucial to fully capitalizing on its capabilities.
Erection Methods
The specific procedures for erecting mast and tower cranes vary depending on the manufacturer and model. Mast cranes typically arrive at the site in a collapsed and folded configuration, enabling swift unfolding and erection utilizing integrated lifting and assembly mechanisms. Tower cranes, conversely, require on-site assembly.
In some instances, the superstructure supporting the jib and counterjib is assembled atop the base frame. Subsequently, an internal climbing mechanism housed within the superstructure raises the top section of the tower, referred to as the pintle. Additional 3-meter tower segments can be progressively added as the pintle ascends until the desired tower height is achieved. Both the jib and counterjib are attached to the superstructure at ground level, which is then hoisted to the pinnacle of the pintle, facilitating their rotation around the static tower.
An alternative assembly and erection method employed by certain manufacturers involves raising the initial tower section onto a concrete base. The jib and counterjib are then assembled and secured to this section with the assistance of a mobile crane. Leveraging the capabilities of the jib, further tower sections can be fitted within the first segment and elevated hydraulically via a telescopic mechanism. This process is iterated until the desired height is attained.
A similar approach to the latter method involves securing the jib and the topmost tower section to a cantilever bracket arrangement situated offset from the main tower. Additional sections can be incorporated until the target height is reached, whereupon the jib assembly can be transferred to the top of the tower.
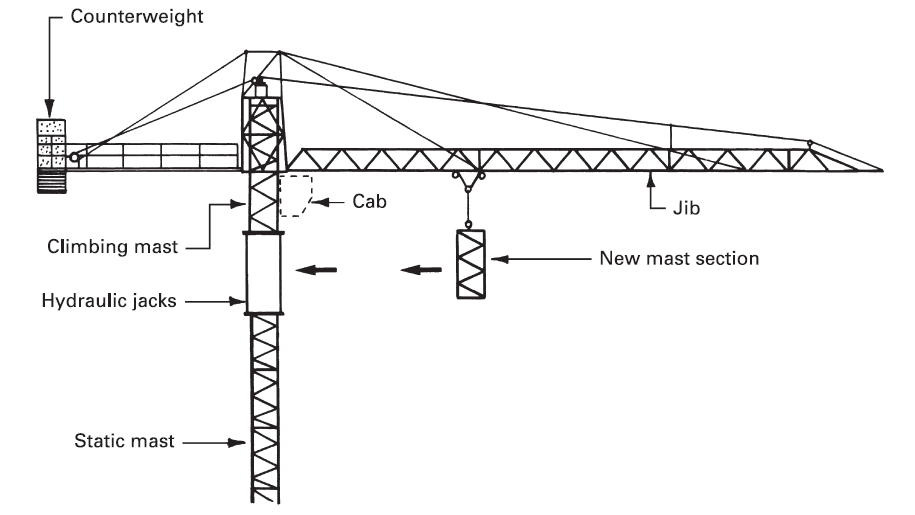
Conclusion
Tower cranes serve a multitude of purposes spanning material lifting, precise placement, and efficient operation within congested urban spaces. These versatile giants come in diverse types, including self-supporting, supported, mobile, and climbing configurations, each catering to specific project requirements and height limitations. Their applications range from hoisting steel beams and prefabricated components for high-rise construction to navigating complex geometries and maximizing site coverage, ultimately revolutionizing the way modern structures are erected with speed, precision, and cost-effectiveness.