Water retaining structures, from dams to swimming pools and water tanks, demand concrete that adheres to strict performance criteria. Beyond structural integrity, the concrete must exhibit exceptional durability in an aqueous environment, resisting water penetration (leakage), chemical attack, and freeze-thaw cycles. Specifying appropriate concrete for these applications requires balancing multiple factors, ensuring both long-term functionality and cost-effectiveness.
In the year 2018, we made a successful publication on the Analysis and Design of Swimming Pools and Underground Water Tanks. In this article, we will briefly review some construction aspects of water retaining structures with emphasis on the specification of concrete to be used for the construction of water retaining structures. To download the textbook on the design of swimming pools, with Staad Pro video tutorials and an Excel spreadsheet for the calculation of crack widths, click HERE.
After carrying out the structural analysis and design of a water retaining structure, the next step is to ensure that the construction is properly executed such that the water tightness and strength of the element will not be compromised. A good design and a bad construction are as good as a failed project. The recommendations given in the following sections can be followed to ensure good results in the construction of water retaining structures.
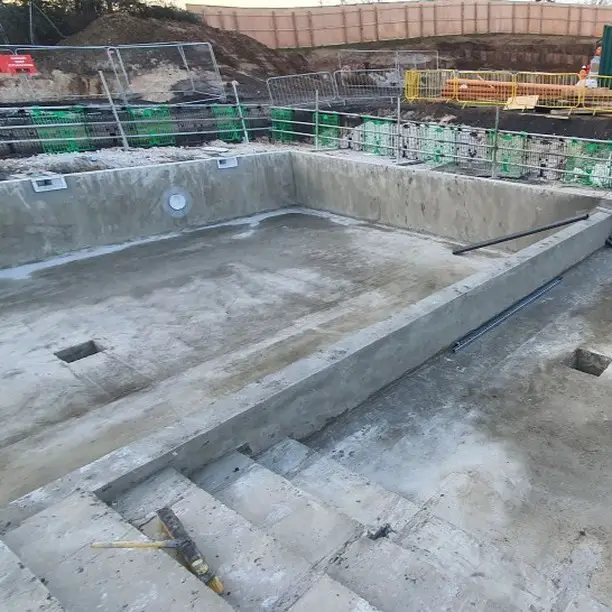
Key Considerations in Concrete for Water Retaining Structures
Strength and Durability
Strength class: Minimum compressive strength is typically in the range of 30-50 MPa, depending on structure type and design loads. Consider future expansions or hydrostatic pressure when selecting a strength class. However, the characteristic compressive strength of concrete for water-retaining structures should not be less than 30 MPa (C30/37) after 28 days of curing.
Permeability: Low permeability minimizes water ingress, reducing the potential for leaching and reinforcement corrosion. Specify a maximum water-to-cement ratio (typically 0.50) and use dense, well-graded aggregates.
Air content: Adequate air content (4-7%) improves freeze-thaw resistance and reduces internal stresses.
Cracking: Minimize by proper joint design, reinforcement detailing, and shrinkage-reducing admixtures.
Material Selection
For the construction of water retaining/excluding structures, class N (normal hardening) cement is recommended and should be used ahead of Class R (rapid hardening) due to shrinkage issues. In general, the concrete should be specified according to BS EN 206 and BS 8500 Parts 1 and 2. For water tanks, all materials in contact with potable water will need to comply with specific regulations and should be non-toxic. This is why all admixtures that will be used must be approved.
- Cement: Portland cement types N (normal) or NA (normal air-entrained) are common choices. For severe environments, consider sulfate-resistant cement or supplementary cementitious materials (SCMs) like fly ash or slag.
- Aggregates: Dense, well-graded, and clean aggregates minimize voids and permeability. Specify maximum size based on wall thickness and reinforcement spacing.
- Admixtures: Utilize admixtures judiciously. Air-entraining admixtures enhance freeze-thaw resistance, while water reducers improve workability without compromising strength. Ensure compatibility with other ingredients and potable water regulations if applicable.
Construction Practices
- Mixing and placing: Employ proper mixing procedures and equipment to achieve uniform consistency. Place concrete promptly and avoid segregation.
- Curing: Implement effective curing practices, such as water spraying or curing compounds, to ensure proper hydration and minimize shrinkage cracking.
- Joints: Design and construct joints to accommodate movement and prevent water leakage. Utilize waterstops (water bars) where necessary.
Additional Considerations
- Chemical exposure: For structures exposed to aggressive chemicals, specify cement and additives with appropriate resistance.
- Water quality: If the structure holds potable water, ensure all materials comply with relevant regulations for safety and non-toxicity.
- Sustainability: Explore options like SCMs or recycled materials to reduce environmental impact while maintaining performance.
Standards and Codes
Refer to relevant national or international standards like ACI 318 (Building Code Requirements for Structural Concrete) or BS EN 206 (Concrete – Specification, performance, production and conformity) for detailed guidance and specific requirements.
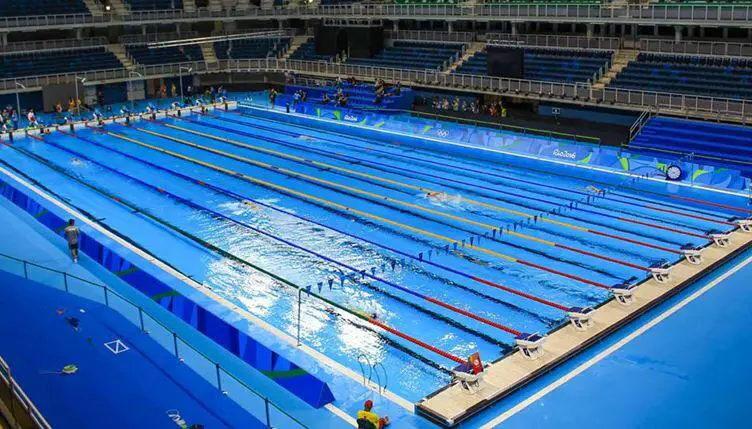
Permeability Considerations
Concrete for water-retaining structures must have low permeability. Water tightness refers to the ability of concrete to hold back or retain water without visible leakage (Kosmatka et al., 2003). It is common knowledge that the permeability of concrete is related to the water/cement ratio because the mix design factor is directly related to the permeability of the hardened cement paste. After the hydration reaction is completed, the remaining water leaves the concrete slowly, thereby leaving pores which reduce the strength of the concrete and the durability.
It is widely believed that a water/cement ratio of 0.2 (about 10 litres of water to 50 kg bag of cement) is needed to complete the hydration reaction, while the rest is to improve the workability of the concrete. However according to Mather et al. (2006), for a given volume of cement to hydrate completely, the quantity of original mixing water required is 1.2 times the solid volume of the cement.
The reason for this is that water should be available to fill up the 30% pore space that must be present after the hydration reaction. Ultimately, the authors opined that not all the cement will hydrate if the water/cement ratio is less than 0.4, even though only half of the water will go into a chemical combination. Research carried out by Kim et al. (2014) showed that porosity in concrete increased by 150% when the water/cement ratio was increased from 0.45 to 0.6.
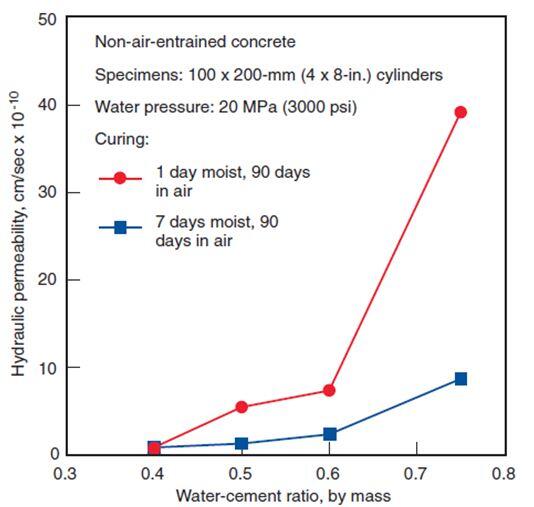
According to Powers et al., (1954) cited by Kosmatka et al. (2003), the permeability of mature hardened cement paste kept continuously moist ranges from 0.1 x 10-12 to 120 x 10-12 cm/sec for water-cement ratios ranging from 0.3 to 0.7 (see Figure 2). Also, in a leakage test conducted by Portland Cement Association on cement mortar disks of 25 mm thickness subjected to a water pressure of 140 kN/m2; the disks made with a water/cement ratio of 0.5 or less showed no sign of leakage after being moist cured for seven days.
However, the disks made with a water/cement ratio of 0.8 showed leakage after being cured for the same period of time. Research has also shown that concrete cured in water is less permeable than concrete that hardened in air, therefore it is recommended that immediately after removing the formwork of tank walls, the tank should be flooded with water. This also helps in autogenous healing of cracks.
Furthermore, the permeability and gradation of the aggregates, the quality of the aggregate/cement paste interface, and the ratio between cement paste and aggregates affect the overall permeability of concrete. Workability is usually an issue when we try to keep the water/cement ratio low. The best way out is to use water-reducing admixtures to make the concrete workable.
This is a better option than using waterproofing admixtures and a high water/cement ratio. Waterproofing admixtures reduce absorption and water permeability by acting on the capillary structure of the cement paste. They will not significantly reduce water penetrating through cracks or through poorly compacted concrete which are two of the more common reasons for water leakage in concrete structures.
Summary
Table 1 gives the recommended concrete material requirements for water-retaining structures. A concrete specified and prepared as given in Table 1 should not give problems for water retaining structures provided it is well placed and compacted.
Table 1: Recommendation for concrete to be used water retaining structure
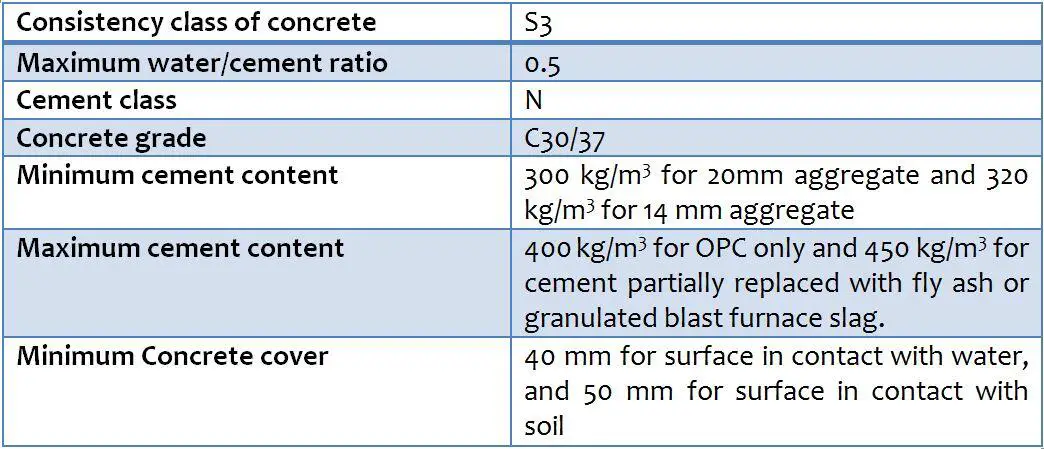
In effect, cracking can only be controlled by structural design based on the structural arrangement adopted: introducing movement joints, or by reinforcing the structure properly to limit the crack widths. Otherwise, Type A water protection should be specified. For water-retaining structures, the recommended minimum thickness for water tightness is 250 mm, unless the hydrostatic pressure in the tank walls is very low.
Specifying concrete for water retaining structures requires a comprehensive understanding of performance demands, material properties, and construction practices. By carefully considering strength, durability, material selection, and construction techniques, engineers can ensure long-lasting, leak-free structures that fulfil their intended purpose for decades to come.
References
Kim Yun-Yong , Kwang-Myung Lee, Jin-Wook Bang, and Seung-Jun Kwon (2014): Effect of W/C Ratio on Durability and Porosity in Cement Mortar with Constant Cement Amount. Advances in Materials Science and Engineering Volume 2014, Article ID 273460, 11 pages http://dx.doi.org/10.1155/2014/273460
Kosmatka, S. H., Kerkhoff B., and Panarese, W. C. (2003): Design and Control of Concrete Mixtures, EB001, 14th edition, Portland Cement Association, Skokie, Illinois, USA
Mather, B. and Hime, W. G. (2002): Amount of Water Required For Complete Hydration of Portland Cement. American Concrete Institute (ACI) Volume: 2 Issue Number: 6 ISSN: 0162-4075 pp 56 -58 http://worldcat.org/oclc/4163061
Powers, T. C.; Copeland, L. E.; Hayes, J. C.; and Mann, H. M (1954): Permeability of Portland Cement Pastes, Research Department Bulletin RX053, Portland Cement Association, http://www.portcement.org/pdf_files/RX053.pdf
Whiting, D. (1989): “Permeability of Selected Concretes,” Permeability of Concrete, SP108, American Concrete Institute, Farmington Hills, Michigan, pp 195 -222.