Over the past few years, the subject of digital fabrication with concrete has advanced significantly, with numerous alternative techniques having been created and numerous large-scale models having been built.
A recent assessment indicates that 3D concrete printing, the most extensively researched and commercially available of these technologies, is at a technology readiness level (TRL) of 6-7, comparable to polymer fused deposition modelling technology, putting it on the verge of becoming widely used. However, according to Flatt and Wangler (2022), the viability of such processes is still under discussion, which frequently results in divisive and pointless conversations.
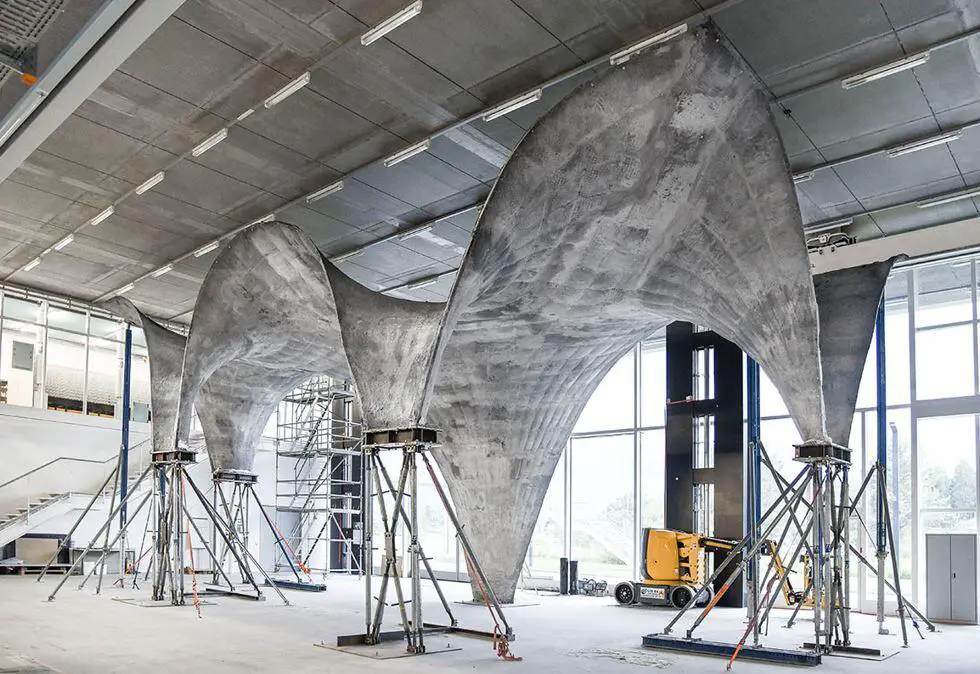
Pioneers created these procedures with the goal of resolving productivity challenges in the building industry. However, in recent years, the need to expand architects’ creative areas and make it more cost-effective to build increasingly complex buildings made feasible by computer-aided design has been a major driving force behind digital fabrication in construction. With this capability, digital fabrication is being pushed more and more as a way to increase efficiency while also lowering the environmental impact of the building industry.
The fact that digitally fabricated structures would only use material where it was necessary, allowing for significant material savings, is a major defense of this claim. This reasoning encounters difficulties with concrete, too, because digitally created concrete frequently has a substantially larger environmental footprint per unit volume than regular concrete.
Additionally, the printing process itself may have some additional negative effects on the environment due to the manufacturing of the printing cell or the energy used to run it. It has been demonstrated that printing factors like printhead velocity and resolution have a significant impact on these process-related effects.
These well-known and currently investigated issues, as well as the fact that previous digital fabrication demonstrations have frequently focused more on “production prowess” than material savings, might result in dry and fruitless discussions of the technology’s sustainability.
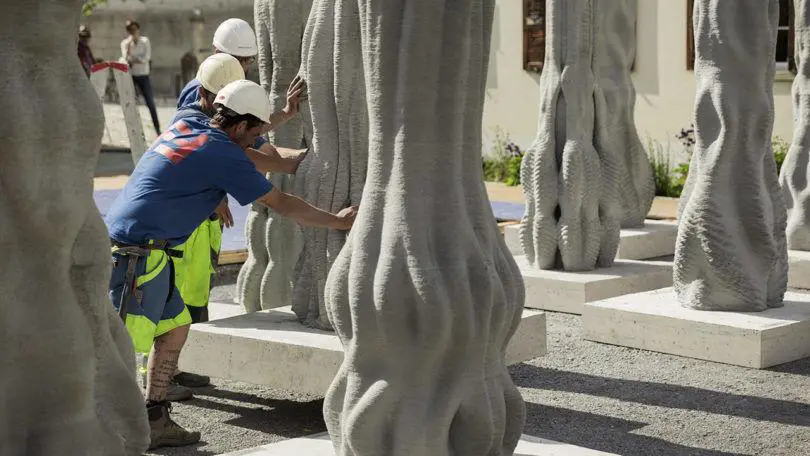
Flatt and Wangler (2022) of the Institute for Building Materials, ETH Zurich, Zurich, Switzerland, recently published a paper in the journal, Cement and Concrete Research to highlight the real opportunities and challenges with regard to sustainability in digital fabrication with concrete, hopefully sparking fruitful discussions on the topic as the technology becomes more widely used.
Their article outlined a straightforward equation that incorporates the primary issues with regard to a structure’s environmental footprint. Three things come into play: Shape efficiency (or material utilized), Material footprint, and Service life (durability). The material itself was then further discussed in the context of concrete extrusion (3D printing), the technology that is most commonly used in many industries like cars, home improvement, computers, and PCB manufacturing. It was emphasized that in many cases, printed concrete is overdesigned and that well-chosen accelerators can address that issue quite effectively.
Main Factors of Concern
According to Flatt and Wangler (2022), three factors primarily determine a concrete structure’s environmental impact:
- The total amount of materials used
- The material’s embodied carbon dioxide, and
- The durability.
According to the equation, it would be the product of the volume of material used and the environmental impact of that substance per unit volume, divided by the service life. It was highlighted that this first-order estimation does not account for variations in this and is only appropriate for comparing structures with equivalent load-bearing capacity. Additionally, the environmental effects of related changes in concrete production, such as formwork use or the aforementioned operating energy, are not expressly taken into account in this relationship.
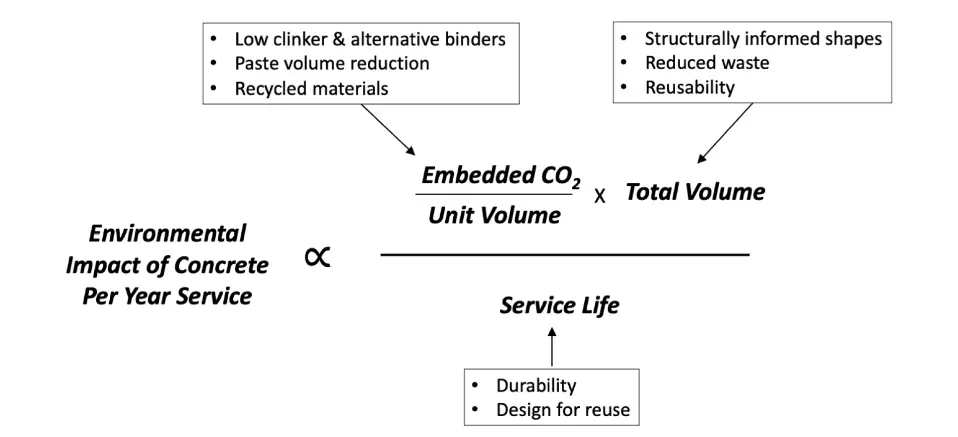
The primary benefit of digital fabrication is that it can require less material. Although the effect on durability is still being researched, this typically accompanies an increase in the material’s environmental imprint and a potential reduction in service life.
Such conflicts mean that the results of environmental balancing will typically not be trivial and will undoubtedly depend on the circumstances. According to Flatt and Wangler (2022), this necessitates a more thorough consideration of the issue, taking into account the true potential for material savings while keeping in mind the limitations of material composition and durability.
Shape Efficiency
The cost of constructing buildings that use less material to provide a certain load-bearing capacity is one of the key defenses for digital fabrication. Thus, it could facilitate structural design methods that are very successful but are all too frequently overlooked. In this context, it is worthwhile to reflect on Pier Luigi Nervi’s ribbed floor designs.
Although labour was inexpensive at the time these constructions were made, concrete was expensive. Today, the situation is the opposite, making it less expensive to create consistent floor slabs by utilizing a lot more concrete than is actually necessary. This is a particularly instructive example because it is simple to visualize the savings since floors are a significant consumer of concrete in structures.
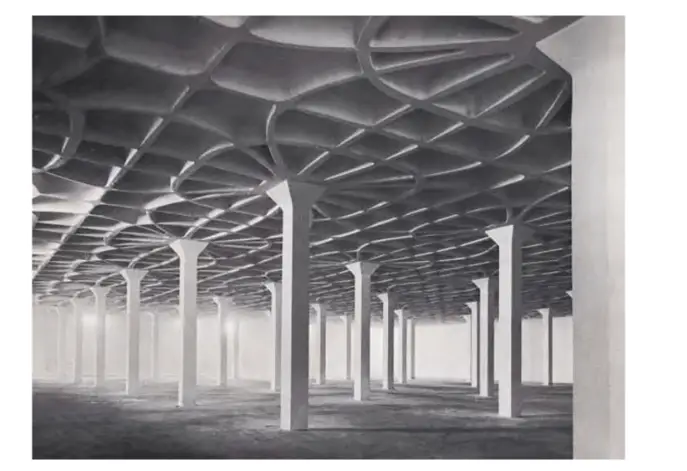
Material Footprint
Despite the potential for material savings, digital concrete frequently has a larger environmental impact than regular concrete, at least for the most popular kind of concrete extrusion. This can be reduced by using recycled components in place of new ones, looking into using different, lower-CO2 binders, or cutting the amount of paste in the cement (increasing aggregate content).
However, none of these approaches are specifically applicable to digital concrete and are instead investigated for concrete in general. The greater level of processing, particularly pumping, which normally increases paste volume, is principally responsible for digital concrete’s higher environmental impact.
In fact, given that mix designs often do not include coarse (>4 mm) aggregate, digital “concrete” is more appropriately referred to as digital “mortar” even though coarse aggregates are beginning to emerge in both academic and industrial settings. Whatever the case, the lower maximum aggregate size restricts the maximum packing fraction of aggregates, increasing the paste volume and, consequently, cement contents and carbon footprints that are larger.
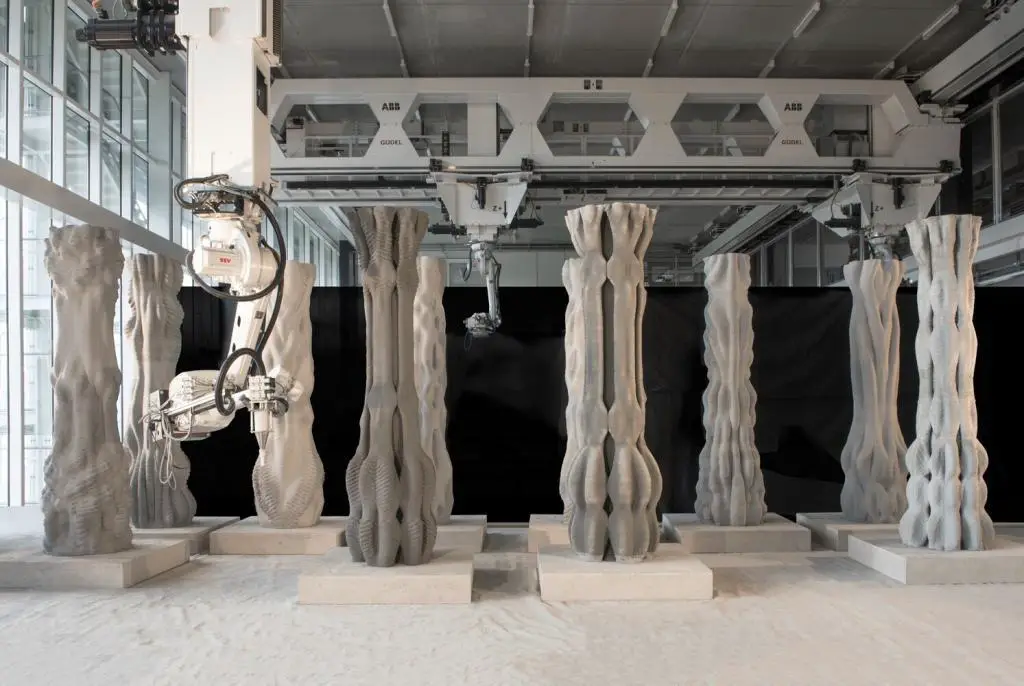
Also keep in mind that while digital concretes have water-to-binder ratios that are more in line with infrastructure and high-performance concrete, their primary use has been in non-load bearing capacities, such as replacing concrete masonry or serving as a lost formwork for cast reinforced concrete. As a result, given their current utilization, digital concrete mixes frequently have twice as much cement content than is really required.
Durability
The durability of digital concrete is a crucial final aspect to take into account when talking about its sustainability. Concerningly, the prevalent technology of extrusion printing in this context can result in cold joints between the layers. However, in general, it depends on the material qualities, state of the extruded material and the previously deposited layer.
The formation of cold joints in 3D-printed concrete is still an active area of research. Therefore, it is influenced by the time interval (contour length and printing speed), and it also seems to be significantly influenced by the substrate’s surface drying throughout the layer time interval. If created, cold joints can weaken the bond between layers, but more significantly for durability, they open up channels for faster ingression of water and/or CO2.
Investigations are now being done to determine how digital concrete reacts to freezing and thawing cycles, although early results show that it performs poorly when compared to conventional concretes. Digital concrete faces the added challenge of curing in full exposure, thus losing the formwork as a “skin,” which increases the likelihood of shrinkage cracking and opens channels for aggressive chemicals.
Only recently have shrinkage issues specific to digital concrete been studied, but future research on these issues will undoubtedly need to be expanded. Noting that lowering the paste content is an easy technique to reduce shrinkage, raising the maximum aggregate size is beneficial for lowering the material footprint as well as boosting durability.
Similar to regular concrete, durability describes a material’s performance under particular exposure conditions and for a particular use. In this situation, it is important to distinguish between structural applications—where reinforcement is required—and other situations because the majority of—but not all—concerns regarding the influx of aggressive species are caused by the presence of reinforcement.
Another noteworthy achievement is the Pantheon, a non-reinforced concrete building whose performance is dependent on sound structural planning. Digital manufacturing can therefore help with important design-related issues of durability.
Determining the appropriate applications for digital manufacturing technologies and whether steel reinforcing is necessary is then crucial. One choice is to largely abandon structural concrete in favour of competing with masonry, or to simply use printed concrete as a substitute for lost formwork.
This eliminates the challenging task of strengthening digital concrete. The problem of reinforcing, on the other hand, must be addressed if structural applications are the focus, and this involves a significant amount of continuing research. Despite this, significant advancements are still required before the majority of reinforcement schemes can be widely accepted and approved in practice.
Conclusions
The fundamental argument made in the study by Flatt and Wangler (2022) is that, in addition to being situation-specific, the subject of the environmental impact of digital fabrication is complex and has a difficult answer. Examples that highlight potential significant material savings were given, however they are now more expensive to build than bulkier pieces with simpler designs.
In fact, the potential for material efficiency is what sets digital concrete construction apart from conventional construction in terms of sustainability, a distinction that should not be lost on those who aim to promote the technology to this end.
This is especially important because adoption of the technology based solely on cost-related factors would entail accepting a higher carbon footprint in exchange for lower labour costs. The current incentives for the implementation of digital concrete processes appear to be primarily cost-driven, related to formwork and masonry labour. These technologies may still have other social advantages (or problems), but those are outside the focus of this research, which is just looking at the environmental aspect of these technologies.
For a variety of reasons, the footprint of digital concrete is bigger than that of traditional concrete. One has to do with using a stronger paste volume, and is a problem that can be solved by increasing the maximum aggregate size through material advancements, which may also have additional advantages like reduced shrinking and greater incentive to use local materials.
The use of high clinker cements and overly strong final designs appear to be another factor contributing to the high carbon footprint. Both are the outcome of ineffectively attempting to meet the needs for gaining strength. Instead, utilizing accelerators based on aluminum can increase strength when it is needed, preventing overdesign of final strength and allowing the use of carbon-lean cements. Therefore, such compounds could be taken into account for quick vertical building rates of thin (and more shape-efficient) structures as well as a way to perhaps reduce the environmental impact of digital concrete.
However, extra caution must be used while employing such compounds because doing so could result in the formation of cold joints, which could reduce durability. In fact, the effect of digital fabrication techniques on the durability of concrete must be further examined in light of durability’s relationship to environmental impact.
References:
Flatt R. J., Wangler T. (2022): On sustainability and digital fabrication with concrete. Cement and Concrete Research, Volume 158, 2022, 106837 https://doi.org/10.1016/j.cemconres.2022.106837
The contents of the cited original article published by Cement and Concrete Research (Elsevier) is open access, under the CC BY license (http://creativecommons.org/licenses/by/4.0/) which allows you to share and adapt (remix) the article provided the appropriate credit is given, and the link to this license provided.