Reinforced concrete (RC) slabs are a fundamental component of reinforced concrete structures, providing a versatile platform for floors, building occupancy, and various structural elements. They are material-intensive structural elements that take a lot of human and material resources to construct. Accurately calculating the quantity of materials for a reinforced concrete slab is very important for cost estimation, material procurement, and efficient construction planning.
It is very pertinent to point out that the quantity of materials required for the construction of reinforced concrete slabs is dependent on the architectural and structural design requirements of the building. Large-spanning floors will require more materials to construct compared to shorter floor spans. Furthermore, special structural features such as cantilever slabs will demand more construction materials compared to simply supported or continuous floors.
The basic materials required for the construction of suspended floor slabs in a building are;
(1) Concrete (cement, sand, stones, and water)
(2) Reinforcement (floor mats and beam reinforcements)
(3) Formwork (temporary wooden support platform consisting of joists, plywoods/planks, and props).
This article discusses the key steps involved in the calculation of the quantity of these materials required for the successful execution of any building construction project. We will use the floor slab layout in Figure 1 as a case study. All the supporting beams are 230 x 400 mm beams.
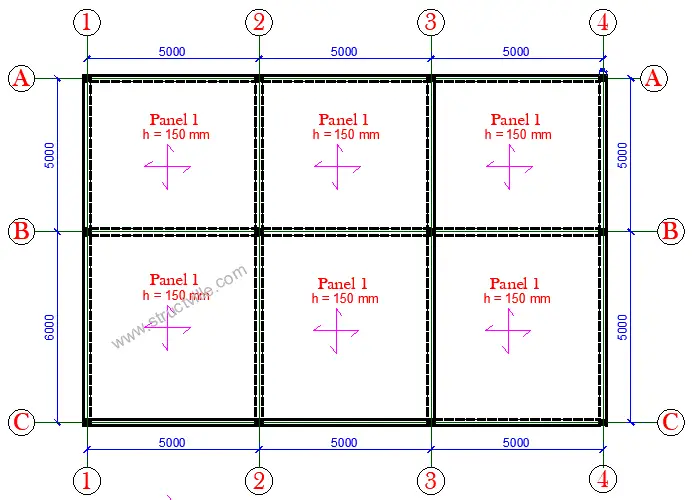
Step 1: Determine Slab Geometry
The first step involves defining the slab’s geometric parameters. These include:
- Length (L): The horizontal dimension of the slab measured in meters (m) or feet (ft).
- Width (W): The perpendicular horizontal dimension of the slab measured in meters (m) or feet (ft).
- Thickness (T): The vertical dimension of the slab measured in meters (m) or inches (in).
For the slab layout above,
Length (L) = 5000 + 5000 + 5000 + 230 = 15230 mm = 15.23 m
Width (W) = 6000 + 5000 + 230 = 11230 mm = 11.23 m
Thickness = 150 mm = 0.15 m
Step 2: Calculate Slab Volume
Once the geometry is defined, the volume (V) of the concrete required can be calculated using the formula:
V = L x W x T
V = 15.23 m × 11.23 m × 0.15 m = 25.654 m3
This volume represents the total amount of concrete needed to cast the slab.
Note: It’s important to ensure all units are consistent (e.g., all in meters or all in feet) to obtain accurate results.
Step 3: Account for Formwork
Formwork is the temporary structure that shapes and supports the concrete during the curing process. While not directly a concrete material, formwork influences the overall material quantity.
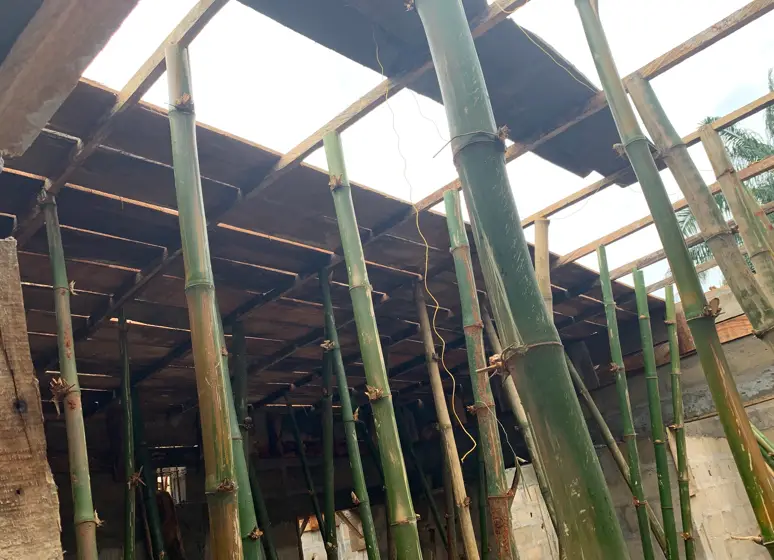
Two approaches can be considered:
- Direct Measurement: If the formwork design details are available, the volume of formwork materials (plywood, lumber, etc.) can be directly calculated using their dimensions and quantities.
- Percentage Addition: A common practice involves adding a percentage buffer to the concrete volume to account for formwork material absorption and potential overestimation errors. This percentage typically ranges from 5% to 10% depending on the formwork complexity and project tolerances.
For the project layout under consideration, the floor slab will supported by 250 mm x 3500 mm boards (planks) typically called 1″ x 12″ boards in Nigeria. Ideally, the width of the board is supposed to be 300 mm, but experience has shown that the boards available in local markets rarely meet the dimensional requirements. These boards will be supported by 2″ x 3″ softwood joists/stringers spaced at 600 mm c/c, which will be supported on bamboo props spaced at 600 mm c/c.
Wooden plank (sheathing) requirement
Area of floor slab = L x W = 15.23 m × 11.23 m = 171 m2
Area of wooden plank = b x h = 0.25 × 3.5 = 0.875 m2
Number of 1″ x 12″ planks required = 171/0.875 = 196 pcs
Making a 10% allowance for waste, damages, and offcuts = 1.1 × 196 = 216 pcs
(Note: This quantity does not account for the beam formwork requirements which should be calculated using the beam dimensions). If 1.2m x 2.4m marine boards are to be used, the quantity required will be approximately 60 pcs without accounting for waste and offcuts.
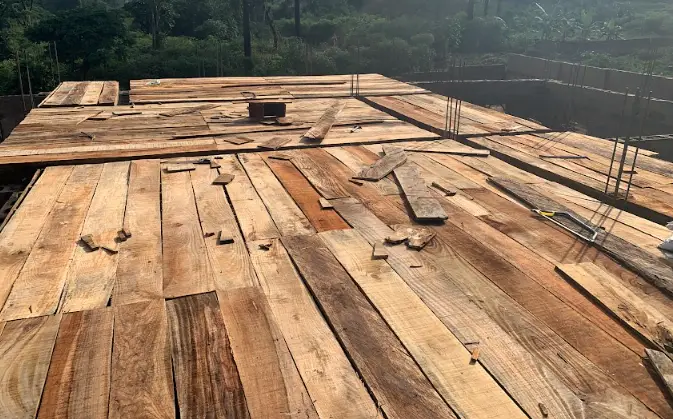
Side edge formwork
The thickness of the slab = 150 mm (therefore 1″ x 6″ board will be adequate for the edge formwork)
Perimeter of slab = 2(15230) + 2(11230) = 52920 mm
Number of 1″ x 6″ edge formwork required = 52920/3500 = 16 pcs
Timber Joist Requirement
To calculate the quantity of timber joists required, the recommended spacing of the joists is required. Using the length and width of the slab floor plan, you can calculate the total length of the timber joist required if the spacing is known. The number of wood materials required can then be obtained by dividing the total length of the timber joist by the supply length.
The supply length of most softwood timber beams in Nigeria is 12 ft (3.6m), but for quantification purposes, it is wise to use a shorter length, say 3.5 m. It is important to also ensure that good quality wood with the appropriate dimensions is supplied.
Recommended timber joist = 2″ x 3″ softwood (supply length is usually 3500 mm)
Spacing = 600 mm
Pick the length of the slab L = 15230 mm
Number of joists required along the length = 15230/3500 = 4.35 pcs
Number of rows of joists required along the width of the slab = (11230/600) + 1 = 20 rows
Therefore the number of 2″ x 3″ wood required = 20 × 4.35 = 87 pieces
Making a 10% allowance for waste, damages, and offcuts = 1.1 × 87 = 96 pcs
Alternatively, number of rows along the length (it can work with either the length or width) = (15230/600) + 1 = 27 rows
Length per row = 11230 mm
Total length of 2″ x 3″ required = 27 × 11230 = 303210 mm
Number of pieces required = 303210/3500 = 87 pieces
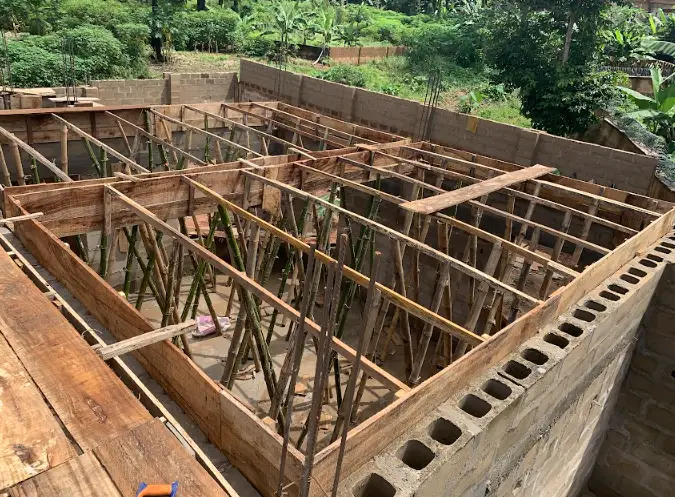
Bamboo prop requirements
To obtain the quantity of bamboo props required, the same steps can be followed as were done for the joists. However, we should know that the bamboo props are individual ‘posts’ standing on their own at a given spacing. Using the recommended spacing of the bamboo, it is possible to calculate the number of bamboo along the length of the floor slab and multiply it by the number of rows along the width of the slab. This should give the total quantity of bamboo required for the slab.
Spacing of bamboo props = 600 mm in all directions
Number of bamboo props along the length = (15230/600) + 1 = 27
Number of rows of bamboo along the width of the building = (11230/600) + 1 = 20 rows
Total number of bamboo props required = 27 × 20 = 540 pcs of bamboo.
If it is assumed that a minimum of 2 pcs of bamboo can be obtained per supply length of natural bamboo, then 270 lengths of fully matured bamboo stem should be ordered. It is also possible to calculate the quantity of bamboo props required ”room by room”.
Step 4: Estimate Material Quantities for Concrete Mix
The next step involves determining the quantities of individual components required to produce the concrete mix for the slab. This is based on the specified concrete mix design, typically denoted as “M XX” (where XX represents the characteristic compressive strength in MPa).
Common mix designs include M20, M25, and M30. For M20 concrete, a concrete mix of 1:2:4 with a maximum water-cement ratio of 0.5 should provide a minimum compressive strength of 20 N/mm2 after 28 days of curing.
Read…
How to achieve grade 25 concrete on-site
Material Quantities per Unit Volume of Concrete:
The specific quantities of cement, sand, and coarse aggregate (gravel) per unit volume of concrete depend on the mix design. However, a general guideline can be used for the initial estimation of a 1:2:4 mix ratio:
- Cement: 6.5 bags of cement (50kg/bag) per 1 m3 of concrete
- Sand: 1000 kg per 1 m3 of concrete
- Coarse Aggregate: 1450 kg per 1 m3 of concrete
For 25.654 m3 of concrete;
- Cement: (6.5 × 25.654 m3) = 167 bags of cement
- Sand: (1000 x 25.654 m3) = 25654 kg of sand (25.6 tonnes of sand)
- Coarse Aggregate: (1450 x 25.654 m3) = 37198 kg of granite (37.2 tonnes of granite)
Note: It is very important to consult the specific mix design for accurate material quantities. This information is typically provided by a structural engineer or obtained from ready-mix concrete suppliers.
Step 5: Quantify Reinforcement Steel
The amount of reinforcement steel required depends on the slab’s structural design. This information is typically provided on the structural drawings or by a structural engineer. The steel quantity is usually expressed in weight per unit area (kg/m²) or total weight for the entire slab (kg). It is therefore important that the accurate quantity of steel required is calculated from the structural drawing.
Common Steel Reinforcement Types:
- Main bars: These primary bars resist the bending moments acting on the slab.
- Distribution bars: These secondary bars distribute loads and prevent cracking.
Let us assume that for the slab above, Y12 @ 150 c/c has been recommended for the sagging and hogging areas, while Y10 @ 250 c/c has been recommended for the distribution bars. For 150 mm c/c spacing, a very rough estimate will show that 12.5 kg of 12mm bars is required per square metre of the slab, while 25% of the quantity of span reinforcement is required in the hogging areas. 15% of the span reinforcement is required as the distribution bar.
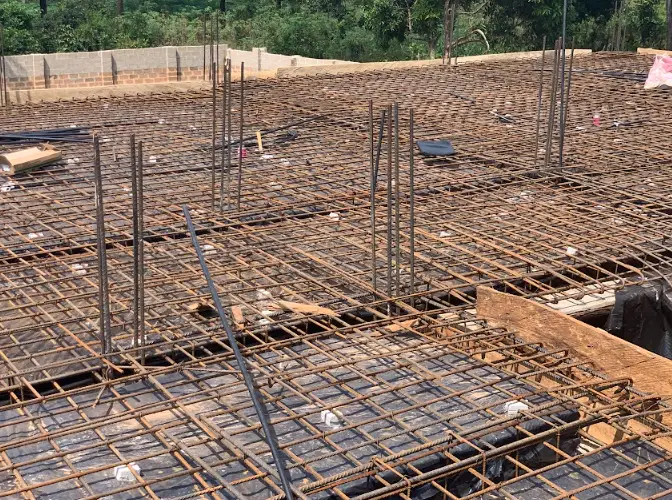
Read…
Quantity estimation guide for construction sites
Therefore, for the slab under consideration:
Bottom reinforcement required = 12.5 × (15.23 × 11.23) = 2137.9 kg of Y12 mm
Hogging reinforcement required = (25/100) × 2137.9 = 534.475 kg of Y12 mm
Distribution bar required = (15/100) × 2137.9 = 320.685 kg of Y10 mm
Alternatively;
Since the bottom reinforcement is placed at 150 mm c/c in both directions, we can calculate the total length of the rebars. We can increase the length and width of the rebars by 2m to account for the return bars. Ideally, this should extend by 0.15L into the span of the slab.
Total length of the slab = 15.23 + 2m = 17.23m
Number of rows required at 150 mm spacing = (11.23/0.15) + 1 = 76 rows
Total length required along the width of the slab = 17.23 × 76 = 1309.48 m
Total width of the slab = 11.23 + 2m = 13.23m
Number of rows required at 150 mm spacing = (15.23/0.15) + 1 = 103 rows
Total length required along the width of the slab = 13.23 × 103 = 1362.69 m
The total length of reinforcement required for the bottom rebars = 1309.48 + 1362.69 = 2672.17m
Rebars are supplied per 12m length, therefore, the total number of rebars required (in pieces)= 2671.17/12 = 223 lengths
Total number of bottom rebars required (in kg) = 2671.17 × 0.888 = 2372 kg of Y12 mm (Note that the unit weight of Y12mm bars is 0.888 kg/m)
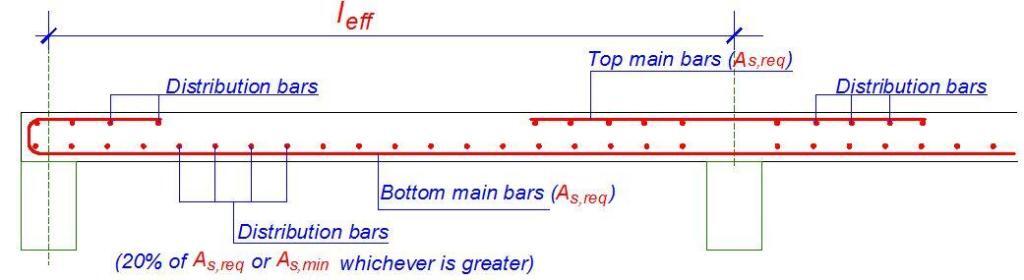
Knowing that the top reinforcements in RC slabs are supposed to extend 0.3L into the span of the slab, the quantity of the top reinforcements can also be accurately determined.
Conclusion
Accurately estimating the material quantities for an RC slab is essential for efficient project planning, cost control, and material procurement. This article has outlined a comprehensive approach to achieve this goal. By systematically considering the slab geometry, formwork influence, concrete mix design, and reinforcement steel requirements, engineers and construction professionals can effectively determine the necessary materials.
It’s important to remember that the initial calculations may require further refinement based on project specifics and the involvement of a structural engineer. However, this process provides a valuable foundation for informed decision-making throughout the reinforced concrete slab construction process.