Launched single-cell box girders are employed in situations where the bridge alignment is straight or on a constant radius curve, either vertically or horizontally. It is particularly useful for overcoming access issues or avoiding obstructions at ground level.
Typically, this method is used for bridge spans up to 60 meters, but in some cases, it has been utilized for longer spans up to 100 meters by using temporary piers to reduce the effective span length during launching. The depth of the deck must remain constant during the launching process, with a typical ratio to the launched span of 1:16 or less.
The process involves casting segments behind the abutment and pushing or pulling the deck over the piers. A designated casting area is prepared behind the abutment, where the reinforcement is assembled, concrete is poured, and launching takes place. The segments used for the bridge are usually standardized and have lengths of 20-30 meters.
Procedure for Incremental Launching of Box-girder Bridges
The launching process begins with the casting of the first segment, which is then moved forward on temporary bearings. The second segment is cast against the first, and both are incrementally moved forward. This process continues with subsequent segments being cast and the deck being moved until it reaches the opposite abutments and reaches its final position.
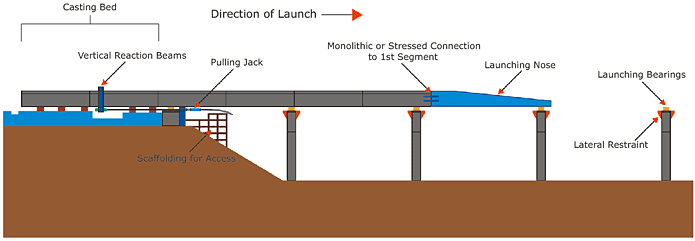
The area behind the casting bay is used for steel fixing and placing prestressing ducts, which can progress simultaneously with other operations. When the deck is launched, the steel cage is attached to the concrete and pulled into position for concreting. The formwork system is designed to be lowered, leaving the deck on temporary supports ready for launching.
Temporary bearings, consisting of steel plates with stainless steel surfaces and laminated rubber pads, are used on each pier and in the casting area to facilitate the deck launching process. A low-friction sliding surface is created by inserting a Teflon pad between the bearing and concrete deck.
Launching devices, typically fixed to the abutments, are employed to provide the necessary thrust resistance. These devices jack up the deck slightly to grip the structure, push or pull it forward, and then drop down to release the structure and move back for another stroke.
During the launching process, the pushing force needs to increase to overcome the frictional force on the temporary bearings, which can range from 2% to 6% of the vertical load. Greater pushing forces are required when launching a deck up a slope, while a braking device is needed when launching it down a slope. The abutment is primarily responsible for resisting the launching force and must be designed to prevent sliding or overturning.
You can watch the video for the incremental launching of box girder bridges below.
Additional resistance can be achieved by providing the casting area with a ground slab as a working platform and connecting it with the abutment. Guides are fixed to the piers to ensure the deck remains properly aligned during the launching operation. Once the launching is complete, the deck is raised, and the temporary bearings are replaced by permanent bearings.
To reduce cantilever moments occurring as the deck is launched over a pier, a temporary lightweight steel launching nose can be attached to the front of the box. The length and stiffness of the launching nose are critical factors in its effectiveness, and a balance must be struck between its cost and the cost of accommodating additional moments in the deck. Typically, the launching nose length is about 60% of the span length, and its stiffness (EI) is approximately 10-15% of the concrete deck.
Alternatively, a temporary tower and stay-cables can be utilized over the front portion of the deck instead of a launching nose to reduce bending moments. The tension in the stays is adjusted as the deck passes over a pier to control the moments and forces imposed on the structure. As the deck moves over the piers, each section experiences changes in moment and shear, and the prestress design needs to account for the full range of these forces.
During the launching process, the deck needs to be strong enough to resist shear forces and the temporary bearing load under the webs as it passes over the piers. The webs are typically kept at a constant thickness, and the corners where the web meets the bottom slab are reinforced to distribute the local loads from the temporary bearings. Design considerations must also account for unevenness in the concrete surface and differential settlement of the piers and temporary supports, which generate additional moments and shears in the deck during launching.
Launching the deck creates friction in the temporary bearings, resulting in a load being applied to the top of the piers. The temporary bearings are aligned parallel to the deck, inducing a horizontal load on the piers in addition to the vertical loads. Therefore, the piers must be designed to withstand these combined horizontal and vertical loads. Providing stays or guys to the top of the piers can help reduce the effects of these horizontal loads.
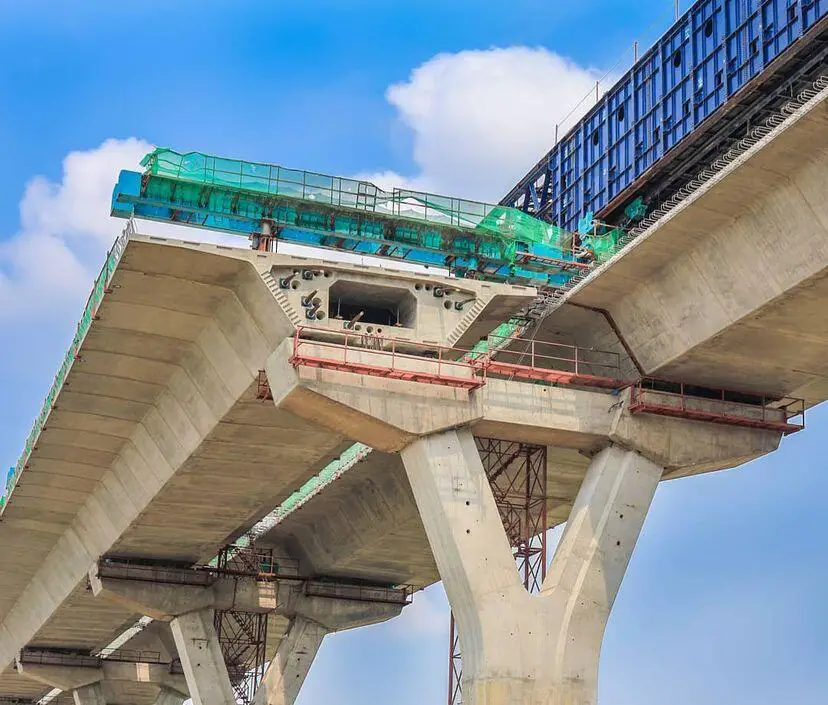
Summary of procedure for incremental launching of box girder bridges
The construction methodology for incrementally launched box girder bridges involves a systematic process that can be summarized in the following steps:
- Design and Planning: The initial stage involves detailed design and planning of the bridge structure, considering factors such as span lengths, segment sizes, construction sequence, and launching forces. Engineering calculations and structural analysis are performed to ensure the feasibility and integrity of the design.
- Fabrication of Segments: The bridge segments, typically box-shaped girders, are prefabricated offsite. This includes the fabrication of individual segments or segments in smaller assemblies, depending on their size and transportation constraints. Quality control measures are implemented to ensure that the segments meet the required specifications and tolerances.
- Construction of Piers and Abutments: The piers and abutments that will support the bridge are constructed first. These elements provide the necessary foundation and stability for the bridge structure. Precise alignment and positioning of the piers and abutments are crucial to ensure the accuracy of the bridge alignment during the launching process.
- Installation of Bearings and Temporary Supports: Bearings and temporary supports are installed on the piers and abutments. Bearings allow for controlled movement and transfer of loads between the bridge and its supports. Temporary supports, such as launching nose beams and sliding bearings, are positioned to facilitate the launching process.
- Incremental Launching: The prefabricated segments are transported to the construction site and assembled in a sequence along the bridge alignment. The launching process involves sliding each segment into its final position using hydraulic jacks, pushing the bridge incrementally forward. The temporary supports facilitate the sliding movement and provide stability during launching.
- Post-Launch Adjustments: Once a segment is launched, adjustments may be made to ensure proper alignment, fit, and connection between segments. These adjustments may involve fine-tuning the position and alignment of the segment, as well as making necessary modifications to the temporary supports or sliding mechanisms.
- Segment Connection and Completion: Once all segments are in place, they are securely connected and integrated to form a continuous bridge structure. This includes welding or bolting connections, as well as completing any required post-tensioning or grouting activities. Additional construction activities, such as deck placement, barrier installation, and finishing touches, are carried out to finalize the bridge construction.
Throughout the construction process, careful monitoring, quality control, and safety measures are implemented to ensure the structural integrity and safety of the bridge. Engineering expertise and coordination among various stakeholders, including designers, fabricators, contractors, and inspectors, are essential to successfully execute the incremental launching method for box girder bridges.
Advantages of incrementally launched box girder bridges
- Access and Obstruction Avoidance: Incrementally launched box girder bridges are beneficial when there are access limitations or obstructions at ground level. By constructing the bridge in segments and launching them over piers, it allows for easier navigation around obstacles or challenging terrain.
- Efficient Construction Process: The incremental launching method allows for continuous construction without the need for temporary support in the middle of the span. This can save time and reduce construction costs compared to other bridge construction methods.
- Reduced Disruption: Incrementally launched box girder bridges minimize disruption to traffic and water flow during construction. The launching process avoids the need for temporary detours or interruptions in the flow of vehicles or water under the bridge.
- Standardized Segments: The use of standardized segments simplifies the construction process, as the same segment lengths can be used for multiple bridge projects. This standardized approach improves efficiency and reduces design and fabrication costs.
Disadvantages of incrementally launched box girder bridges
- Limited Span Length: Incrementally launched box girder bridges are typically suitable for shorter to medium spans, up to approximately 100 meters. For longer spans, additional temporary piers may be required to reduce the effective span length during launching, increasing complexity and cost.
- Structural Integrity during Launching: The launching process can subject the bridge segments to increased bending moments and shear forces. Proper design and engineering are crucial to ensure the structural integrity of the bridge during the launching phase.
- Specialized Equipment and Expertise: Incrementally launched box girder bridges require specialized launching equipment and expertise. The construction process demands careful coordination and precise engineering to ensure safe and successful launches.
- Additional Design Considerations: Incrementally launched bridges require specific design considerations, such as accommodating differential settlement of piers and temporary supports, mitigating frictional forces on temporary bearings, and addressing variations in concrete surface. These factors increase the complexity of the design process.
Conclusion
In summary, the incremental launching of bridges involves casting the deck segments behind the abutment and pushing or pulling the deck over the piers.t This method offers a range of advantages, including reduced traffic disruption, enhanced safety, cost-effectiveness, and improved quality control.
By embracing this innovative construction technique, engineers and contractors can achieve efficient and successful outcomes in the construction of box girder bridges. As technology and construction practices continue to evolve, the incremental launching method will likely play a pivotal role in the development of future infrastructure, enabling the efficient and sustainable growth of transportation networks around the world.