An engineer may face significant challenges while designing the foundations for bridges over water, jetties, and offshore marine facilities. In the case of over-water bridges, the environment (water body) can pose more design challenges than the ground conditions (sea bed) at the bridge location. However, for bridges on land, the ground condition is the major deciding factor for the foundation design.
The loading on the foundation for bridges differs greatly from the loading for building foundations. Imposed loads are more prominent in the design of bridges than they are for buildings. They can be as much as half the dead load on highway bridges and two-thirds of the dead load on railway bridges (Tomlinson, 2001).
Traffic-related imposed loads are moving loads that can cause the bridge deck to experience strong longitudinal traction forces. Transverse forces can be induced by wind loadings, as well as by current drag, wave forces, and ship collisions in the case of river or estuary crossings. Longitudinal forces are also induced by shrinkage and temperature changes in the bridge deck.
Earthquake forces can be transmitted by the ground to bridge supports from any direction, especially when it comes to piers in deep water or high-level constructions where the mass of the displaced water must be added to that of the pier body. When whole spans are erected at ground level and hoisted or rolled onto the piers, for example, there might be a quick application of load to the foundations in addition to working loads from traffic.
Continuous-span bridges are particularly susceptible to the effects of differential foundation settlements. The determined total and differential settlements must also be taken into account in relation to the good rideability of the road surface. The intersection of the bridge and embanked approaches, as well as the joints connecting fixed and link spans, are critical places.
Factors affecting the choice of foundation for bridges over water
The following list of environmental factors explains how to choose an appropriate foundation type and construction approach.
Conditions of exposure and water depths
Bridges on open waterways of a vast estuary or bay crossing are in a hostile environment from winds and wave action, which may limit the operational period of floating construction equipment and potentially damage partially completed structures. This encourages the use of massive prefabricated components that can be quickly sunk onto a prepared bed or piled platform after being towed or transported by barges to the bridge site.
When the water level is sufficient for the unit to float, a box caisson is an appropriate design. However, weather conditions are crucial during the initial stages of towing the caisson to the site and sinking it in position. Weather-related delays should be taken into account while planning the overall construction schedule.
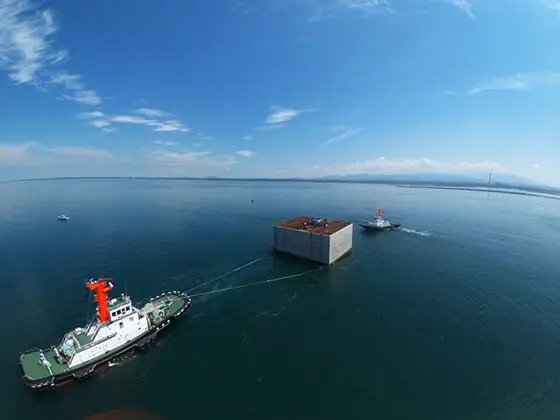
The shallow draft bottom part of open-well caissons is floated to the construction site and buried by removing the soil from the open wells while the walls are sunk gradually. These caissons are employed in shallow water. Compared to box caissons, which can be sunk during a very brief window of favourable weather, open-well sinking construction processes are more weather-dependent.
However, it is possible to sink caissons at exposed sites by sinking the caissons from an artificial island or by deploying a jack-up barge to provide a solid working platform. The advent of heavy-lifting cranes capable of lifting a bridge pier caisson as a single item in various regions of the world has significantly reduced delays and dangers caused by weather conditions in recent years.
The use of simple and single-skin cofferdams is only appropriate for sheltered waterways. However, more efficient forms of cofferdams can be employed in conditions of moderate exposure.
Water Currents and Tides
River currents and tidal streams create scour holes when the soil at bed level is vulnerable to erosion, thereby inducing drag forces on the piers or piles. In the vicinity of cofferdams, where eddies are caused by transient factors like partially driven sheet piles, scour can be a very crucial design factor. As a caisson is lowered through the final few meters of water, mattressing can be necessary on an erodible bed to stop erosion under restricted flow circumstances.
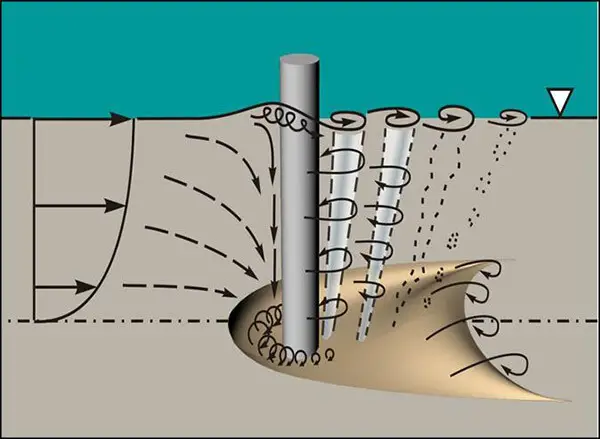
When pitching bearing piles or sheet piles, the current drag forces can cause problems. Before the piles are held in place at the head by the pile cap or temporary girts, damaging oscillations of the piles may occur at some flow rates.
Rivers in flood pose a major threat to bridges Both from the perspective of lateral pressures on the abutments, piers, and superstructures as well as the potential undermining of the foundations due to the scouring impact of the water. The lateral hydrodynamic forces are calculated in a similar manner to those due to wind. Thus from;
q = ρvc2/2
(where vc is the velocity of flow in m/s), if the density of water is taken as 1000 N/m3 then the water pressure:
q = 500vc2/103 [kN/m2]
and
P = qACD [kN]
Values of CD for various shaped piers in the USA are given in AASHTO LRFD (3rd edition) and in the UK are found in BA 59 (Highways Agency, 1994). The degree of scour depends upon many factors such as the geometry of the pier, the speed of flow and the type of soil.
Ship Collision
The cost of the foundations may increase significantly if measures are taken to reduce the possibility of bridge piers collapsing due to ship collisions. Not just the designated navigation channel is at risk. Collisions are equally likely to happen if a ship drifts outside of the designated channel. In certain large estuaries, the deep-water channel can quickly move from one side of the river to the other. Nearly every pier of a multi-span bridge may be in danger if there is a significant variation in tides.
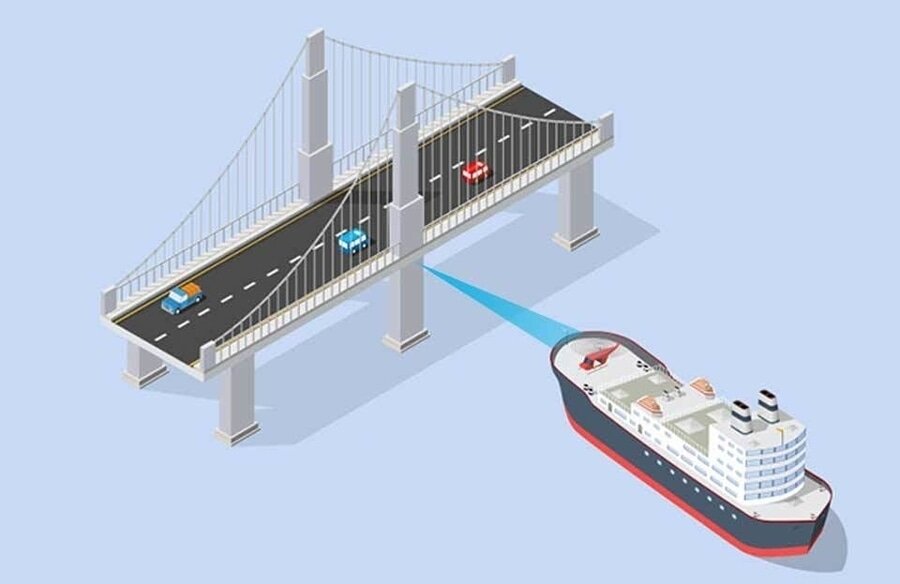
A ring of skirt piles surrounding a group of large diameter piles to prevent ships from getting wedged between individual units, an independent ring fender, or enclosing the pier by a man-made island can all be used as forms of protection for piers. Impact at any angle to the axis of the pier must be considered. The pier body can experience torsional shear from vessel collision.
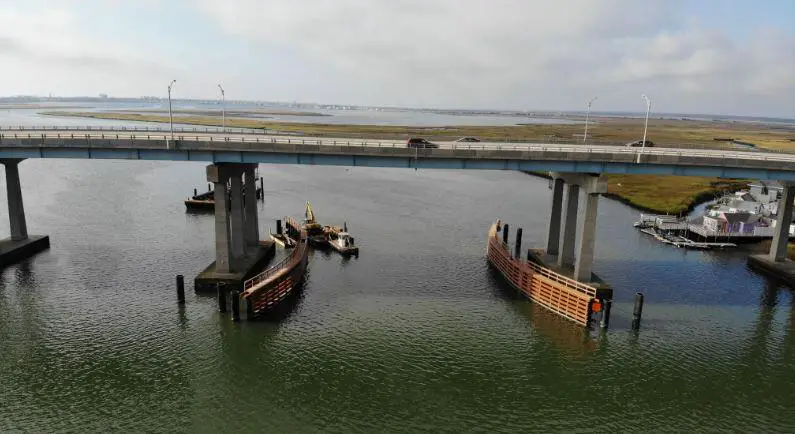
Artificial islands should only be used in shallow water because the area around the pier needs to be big enough to allow the moving ship to ride up the slope and come to rest before the overhanging bow may hit the pier. The amount of fill material, boulder stone for wave protection, and mattressing for scour protection become unreasonably big in deep water, and the islands may block the navigation channel.
Earthquakes
Because the forces acting at a high level on the bridge superstructure combine with the forces acting on the pier body to produce strong overturning moments at the base level, earthquakes pose serious design challenges for deep-water piles. The mass of the pier itself must be multiplied by the volume of water it displaces.
In deep water, the eccentric loading on the pier base can be very high, favouring once more a long, narrow pier. Because earthquake forces can be oriented in any direction, including vertically, a circular structure may be necessary.
The liquefaction of loose to medium-dense granular soils is a result of ground shaking. With information on the soil deposit’s in-situ density and particle-size distribution, the liquefaction depth can be determined. To support the pier, piled foundations or ground treatment to densify a loose soil deposit may be necessary.
Bridge Pier Construction in Cofferdams
Shallow-water locations with sheltered or moderately exposed conditions are appropriate for the construction of bridge piers within cofferdams. Simple earth bank cofferdams can be used to build the piers in sites with very shallow water or at half-tide.
Although an overall depth of 32 m from high water to the base of the excavation was practical for the Thames Bamer foundations, sheet pile cofferdams can be built in water as deep as 15 m without too much difficulty, but the challenges increase as the depth of the water increases.
Wave action can cause damage to single-skin sheet pile cofferdams, and repeated wave impact can lead to fatigue failure of welded connections. Interconnected cells can be used to create strong cofferdams. To prevent ship collisions, the ring of cells can be left in place.
The locations where sheet piling is most advantageously used are those where there is an impermeable stratum at or below excavation level that serves as a cut-off for groundwater ingress, allowing the excavation to be pumped out and the pier foundation to be built in dry conditions. The excavation and construction of the concrete base are done underwater when a cut-off is not an option.
Bridge Pier Construction with Box Caissons
Box caissons are closed-bottomed hollow constructions that are buoyant when being towed to a bridge site and then buried onto a prepared bed by flooding valves. The top can be left open in sheltered conditions while sinking and ballasting are being done, or a closed top can be provided for towing in turbulent waters. Box caissons should not be used for foundations on weak soils or in locations where erosion might compromise the base.
They are particularly well suited for foundations on compact granular soils resistant to scour erosion or on a rock surface that has been dredged to remove loose material, levelled, and covered in a layer of crushed rock. A cement-sand grout is injected to fill the area between the bottom of the box and the blanket, and skirts are provided to allow the caisson to bed into the blanket. Due to weather conditions at an exposed site, bed preparation of a rock surface in deep water may be prone to lengthy delays.
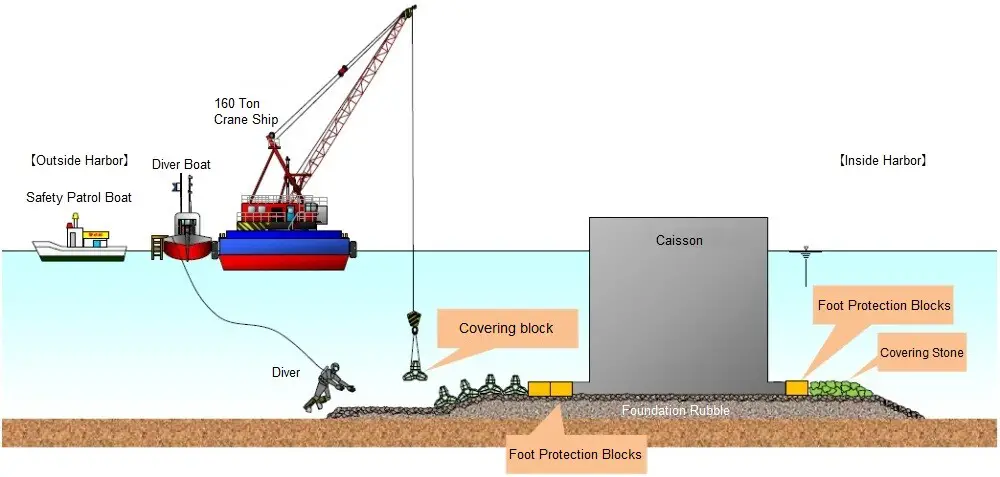
A stacked raft can be constructed to support the caisson in situations when the depth of the mud or loose material is too great for dredging. When lowering a huge box caisson, the final few meters are crucial. The structure’s foundation displaces a huge amount of water, and if the caisson is dropped too quickly, it may slide from its desired position. Slack water is preferred during tidal circumstances to reduce the flow velocity producing erosion in the constricting area between the caisson bottom and the bed.
Sinking can be conveniently accomplished by temporarily fastening the caisson to a moored barge and lowering the unit onto the rock blanket during a single tide. After ballasting, grout can be injected through pipes inserted in the exterior and interior walls between the caisson’s base and the blanket. A 300mm deep peripheral skirt can prevent grout from escaping the blanket’s region.
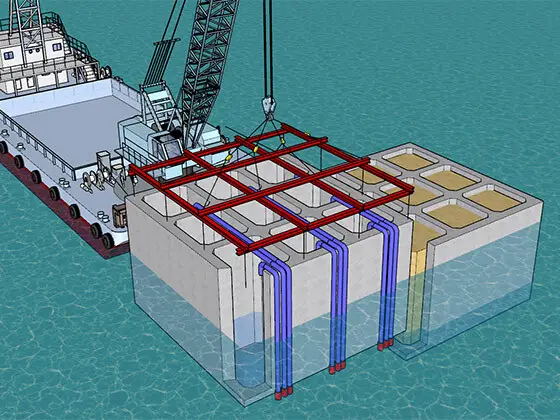
With the exception of the row of cells next to the shallow-water sides of the piers, where the impact from large ships was not feasible, mass concrete can be utilized to fill the cells up to the level of the capping slab. Sand could be used to fill these cells. The pier can then be constructed from the capping slab.
Bridge Pier Construction with Open-well Caissons
Open caissons (including monoliths) are suitable for foundations in rivers and waterways since soft clays, silts, sands, or gravels are easily excavated by grabbing from open wells and do not present a significant skin friction resistance to the sinking of the caissons. Since men are unable to work under compressed air at pressures higher than 350 kN/m2, open caissons are necessary when the required sinking depth exceeds the pressure of that magnitude.
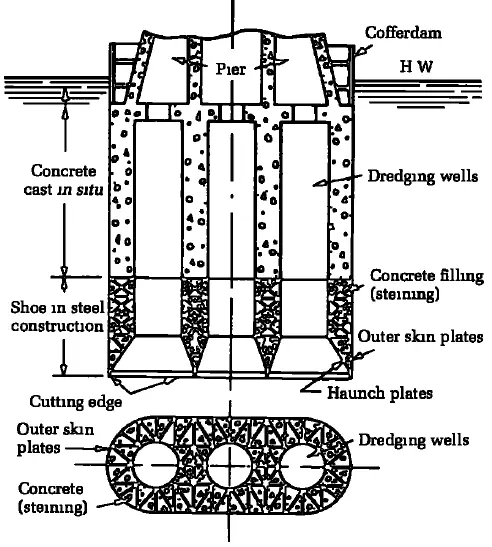
Open caissons are inappropriate for sinking through soils containing huge rocks, tree trunks, and other obstructions. A great difficulty is encountered when it is sunk to an uneven bedrock surface. Furthermore, when they are buried in steeply sloped bedrock, they are likely to move physically out of the vertical. For bridge foundations, open caissons are useful in rivers where there is a significant seasonal level variation.
Beginning in the low-water period, caisson sinking is finished to the design founding level prior to the annual flood. When no work can be done on the bridge superstructure, the caisson can be permitted to be completely or partially covered by flood water without suffering any damage.
Open caissons are sealed after they reach the founding level by pouring a layer of concrete into the bottom of the wells. After pumping the wells empty and adding more concrete, the caissons can be filled with either clean sand or concrete or, in cases where their dead weight must be maintained low, with clean fresh water.
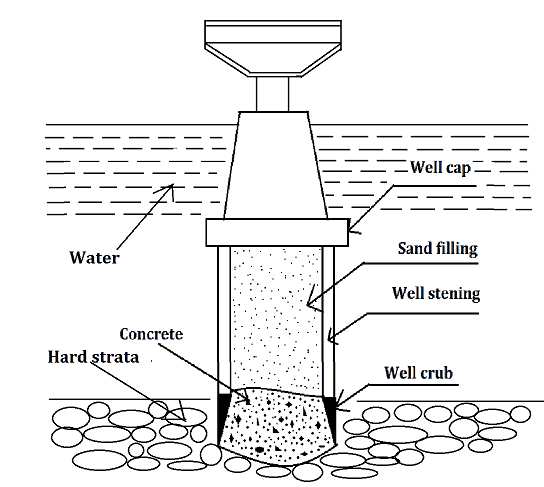
Open caissons have the drawback that the soil or rock at the foundation level cannot typically be inspected before putting the sealing concrete because the sealing is done underwater. The wells can only occasionally be pumped dry to allow for a bottom inspection.
Another drawback is that the act of grasping loose, soft materials beneath the water causes the material to surge and inflow beneath the cutting edge, leading to significant subsidence of the ground around the caisson. Open caissons are therefore inappropriate for usage on sites where nearby structure sinking could result in damage.
Bridge Pier Construction with Pneumatic Caissons
When dredging from open wells would result in loss of ground surrounding the caisson, causing the settlement of nearby structures, pneumatic caissons are utilized instead of open-well caissons. They are also employed for sinking through uneven ground or obstruction-filled ground, where an open caisson would be more likely to tilt or refuse to continue sinking.
The ‘dry’ working chamber of pneumatic caissons has the benefit that excavation can be done by hand, and obstructions like tree trunks or boulders can be removed from under the cutting edge. Additionally, the soil beneath the foundation can be examined, and if necessary, bearing tests can be conducted in-situ. In contrast to open-well caissons, where the final excavation and sealing concrete are nearly usually completed underwater, the foundation concrete is poured in the dry.
Compared to open-well caissons, pneumatic caissons have the drawback of requiring more equipment and labour during the sinking, and the rate of sinking is often slower. Unless another method of ground-water lowering is utilized externally to the caisson, the depth of sinking is limited to 36 m below the water table due to the important restriction that men cannot work in air pressures much greater than 3.5 bar.
Dewatering wells must be situated far enough away from the caisson to be unaffected by ground movement brought on by the caisson sinking if such measures are employed to lower air pressures in the working chamber.
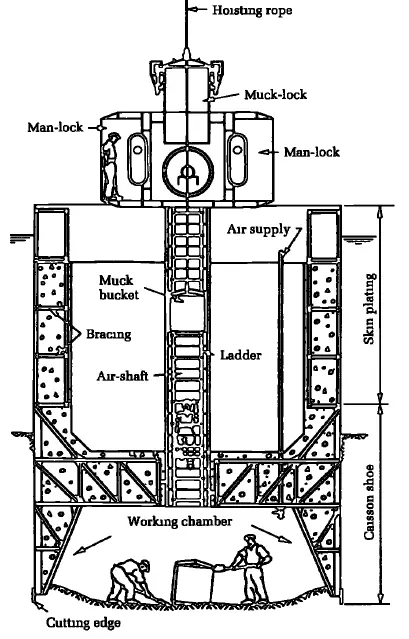
Bridge piers supported by piling
Bridge piers that are situated in water can also be supported by using precast piles that have been driven into the ocean floor. The typical approach is to position the pile heads at or above the level of the high water mark, and then to employ standard pile caps to provide support for the piers.
Typically, barges are used to transport the piles and pile drivers to the desired location in the water. The diameter and embedment length of the piles must be obtained from the geotechnical and structural design using the sea bed soil information and the anticipated loading condition. When the barge floats the piles to the required location, they are placed on the underwater surface and then driven down by the pile driver.
To ensure stability and resistance against water currents, the piles are inclined outward (battered piles), enabling them to support the lateral load of the bridge structure and withstand the forces of the water. The piles are installed in groups, with wider spacing at the bottom and closer spacing at the top, (similar to a triangular shape).
Following the pile installation, the next step involves placing pile caps on the top of the grouped piles. Pile caps serve to create a stable foundation and provide a larger surface area for the distribution of the load onto the piles. Once this is completed, the construction of the bridge pier structure can commence from the pile cap.
An additional possibility is to erect the pile caps inside of a cofferdam. Either the combined mass and bending resistance of the pile group and cap, or a separate fender structure, can provide protection against the possibility of a ship colliding with the structure.
Conclusion
Bridge foundations constructed in water require specialized techniques to ensure stability and structural integrity. These foundations are typically built using one of the following methods: cofferdams, caissons, or drilled shafts/piles.
Cofferdams are temporary structures built in the water to create a dry work area. They are often constructed using sheet piles driven into the riverbed or seabed. Once the cofferdam is in place, the water is pumped out, allowing workers to excavate the foundation and pour concrete. After the foundation is complete, the cofferdam can be removed.
Caissons are large watertight structures that are built on land and then floated into position. They are then sunk to the riverbed or seabed, creating a dry workspace. Caissons are commonly used for building bridge piers or abutments. The caisson is filled with heavy material such as concrete or stone to provide stability. Once the caisson is in place, the foundation is constructed within it.
Precast piles or drilled shafts are another method used for constructing bridge foundations in water. This technique involves drilling deep holes into the riverbed or seabed and then filling them with concrete or reinforcing steel. Alternatively, precast piles can be driven into the seabed and then joined using pile caps.
Regardless of the method used, bridge foundations in water must be designed to withstand the forces exerted by water currents, waves, and changing water levels. They often require additional measures such as scour protection to prevent erosion around the foundation.
Overall, constructing bridge foundations in water is a complex and challenging task that requires careful planning, specialized equipment, and experienced professionals. By employing the appropriate construction techniques and accounting for environmental factors, engineers can ensure the stability and longevity of the bridge structure.
References
Tomlinson M. J. (2001). Foundation Design and Construction (7th Edition). Pearson Education Ltd.
In addition to the fact that these structures should be built of high-quality materials and have a strong support and foundation, remember that after installation, you need to periodically inspect the bridge and monitor its strength.