Bearings are ancillary bridge components that facilitate the transfer of traffic actions, permanent actions, and other environmental actions from the bridge deck down to the substructure, and ultimately, to the ground. To fulfill this function effectively, bearings must be able to accommodate all anticipated service movements (rotations and translations), while also restraining extraordinary movements induced by extreme load cases. The movements allowed by an adjacent expansion joint must be compatible with the displacement restrictions imposed by a bearing. Therefore, bearings and expansion joints must be designed interdependently and in conjunction with the anticipated behavior of the overall structure.
Types of bridge bearing
The type of bearing to be used in a bridge can be determined by a lot of factors. Some prominent issues that can be considered are the strength and the stiffness of the bearing, cost, ease of installation, maintenance cost, etc. The common types of bearings used in contemporary bridges are;
- Reinforced elastomeric bearings
- fabric pad sliding bearings
- steel pin bearings
- rocker bearings,
- roller bearings
- steel pin bearings
- pot bearings
- disc bearings
- spherical bearings, and
- seismic isolation bearings.
Reinforced Elastomeric Bearings
A steel-reinforced elastomeric bearing consists of discrete steel shims vulcanized between adjacent discrete layers of elastomer. This vulcanization process occurs under conditions of high temperature and pressure. The constituent elastomer is either natural rubber or synthetic rubber (neoprene). Reinforced elastomeric bearings are broadly classified into four types:
- plain elastomeric pads
- fiberglass reinforced elastomeric pads
- steel reinforced elastomeric pads, and
- cotton duck reinforced elastomeric pads.
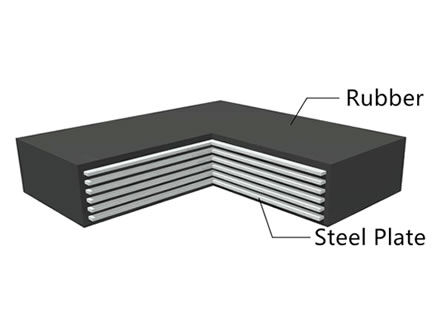
Of these four types, steel reinforced elastomeric pads are used most extensively for bridge construction applications. They are commonly used with prestressed concrete girder bridges and maybe used with other bridge types.
Fabric Pad Bearings
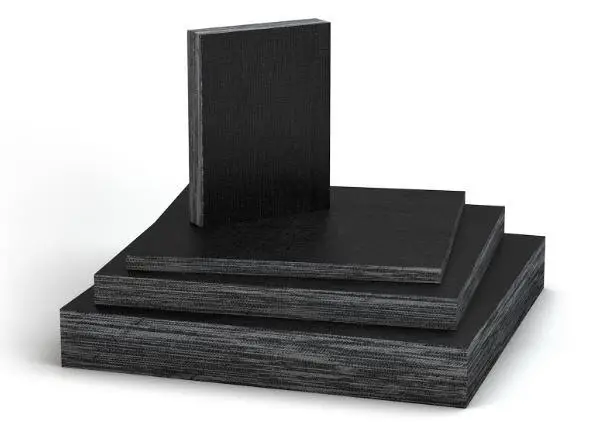
Cotton duck or fabric pads are preformed elastomeric pads reinforced with very closely spaced layers of cotton or polyester fabric. The close spacing of the reinforcing fibers, while allowing fabric pads to support large compressive loads, imposes stringent limits upon their shear displacement and rotational capacities. Unlike a steel reinforced elastomeric bearing having substantial shear flexibility, the fabric pad alone cannot accommodate translational movement. Fabric pads can accommodate very small amounts of rotational movement; substantially less than can be accommodated by more flexible steel reinforced elastomeric bearings.
Read Also …
Design of bridge pier and pier cap
Application of Courbon’s Theory in Analysis of Bridge Decks
Pin Bearings
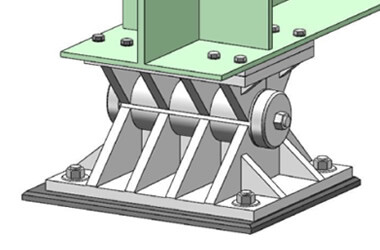
Steel pin bearings are generally used to support high loads with moderate to high levels of rotation about a single predetermined axis. This situation generally occurs with long straight steel plate girder superstructures. Rotational capacity is afforded by rotation of a smoothly machined steel pin against upper and lower smoothly machined steel bearing blocks. Steel keeper rings are typically designed and detailed to provide uplift resistance.
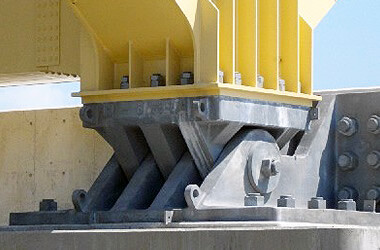
Rocker/Roller Bearings
Steel rocker bearings have been used extensively in the past to allow both rotation and longitudinal movement while supporting moderately high loads. Because of their seismic vulnerability and the more extensive use of steel reinforced elastomeric bearings, rocker bearings are now rarely specified for new bridges.
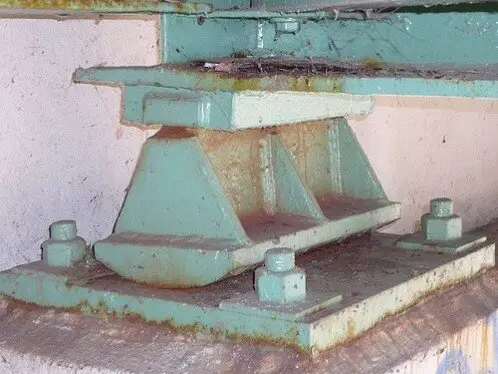
Steel roller bearings have also been used extensively in the past. Roller bearings permit both rotational and longitudinal movement. Pintles are often used to effect transverse force transfer by connecting the roller bearing to the superstructure above and to the bearing plate below.
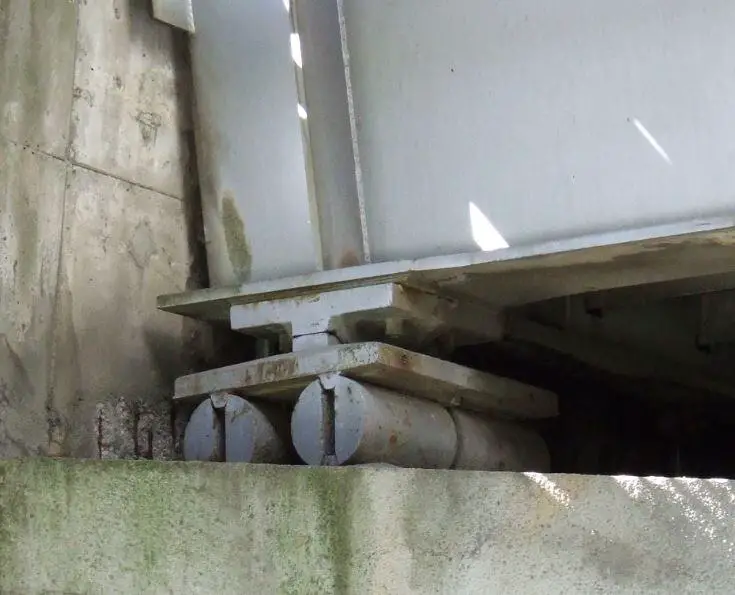
Pot Bearings
A pot bearing is composed of a plain elastomeric disc that is confined in a vertically oriented steel cylinder, or pot.
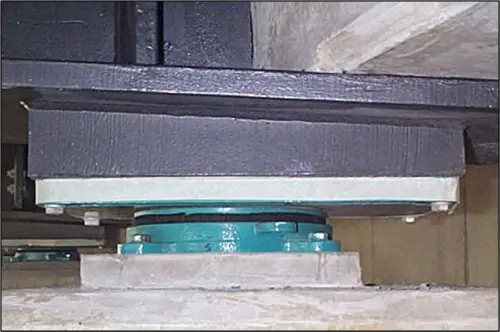
Vertical loads are transmitted through a steel piston that sits atop the elastomeric disc within the pot. The pot walls confine the elastomeric disc, enabling it to sustain much higher compressive loads than could be sustained by more conventional unconfined elastomeric material. Rotational demands are accommodated by the ability of the elastomeric disc to deform under compressive load and induced rotation. The rotational capacity of pot bearings is generally limited by the clearances between elements of the pot, piston, sliding surface, guides, and restraints.
Disc Bearings
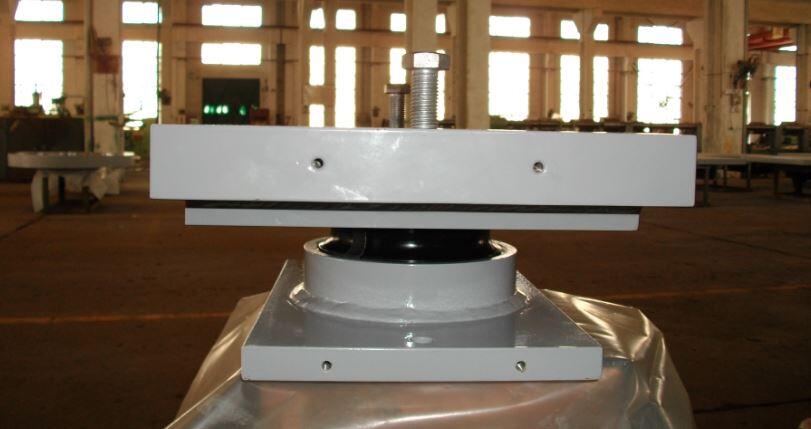
A disc bearing relies upon the compressive flexibility of an annular shaped polyether urethane disc to provide moderate levels of rotational movement capacity while supporting high loads. A steel shear resisting pin in the center provides resistance against lateral force. A flat PTFE-stainless steel sliding interface can be incorporated into a disc bearing to additionally provide translational movement capability, either guided or nonguided.
Spherical Bearings
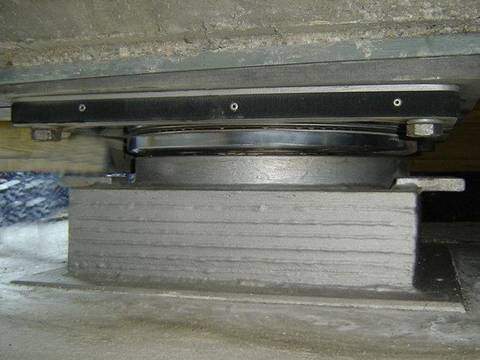
A spherical bearing, sometimes referred to as a curved sliding bearing, relies upon the low-friction characteristics of a curved PTFE-stainless steel sliding interface to provide a high level of rotational flexibility in multiple directions while supporting high loads. Unlike pot bearings and disc bearings, spherical bearing rotational capacities are not limited by strains, dimensions, and clearances of deformable elements. Spherical bearings are capable of sustaining very large rotations provided that adequate clearances are provided to avoid hard contact between steel components.
Spherical bearings are classified into three according to their displacement directions. The three types of spherical bearings are;
Fixed type – Provides only rotation capacity from any direction.
Guided type (Uni-directional sliding) – Provides rotation plus movement in one direction
Free sliding (multi-directional sliding) – Provides rotation plus movement in all directions
Seismic Isolation Bearings
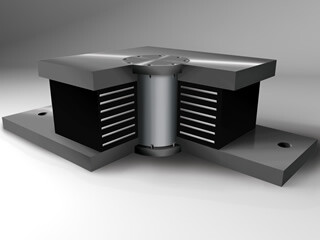
Seismic isolation bearings mitigate the potential for seismic damage by utilizing two related phenomena: dynamic isolation and energy dissipation. Dynamic isolation allows the superstructure to essentially float, to some degree, while substructure elements below move with the ground during an earthquake. The ability of some bearing materials and elements to deform in certain predictable ways allows them to dissipate seismic energy that might otherwise damage critical structural elements.
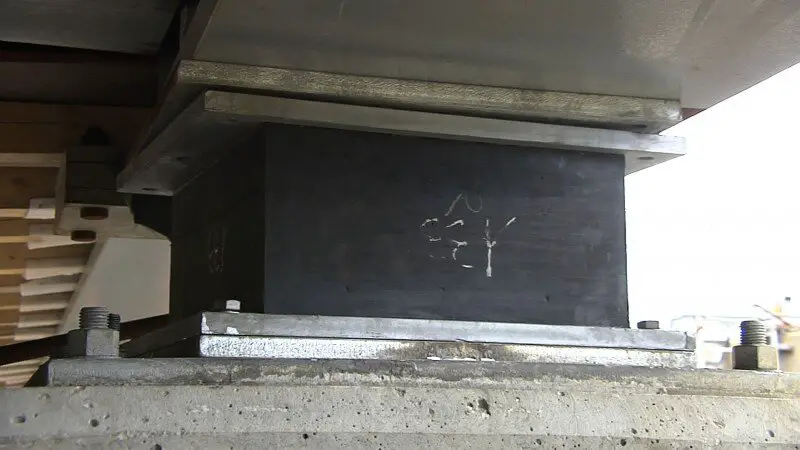
Source:
Chen W. and Duan L. (2014): Bridge Engineering Handbook – Substructure Design (2nd Edition). CRC Press Taylor and Francis Group. International Standard Book Number-13: 978-1-4398-5230-9
Keep Sharing article is good