In today’s construction industry, high strength concrete is becoming more popular. Using high-strength concrete has a number of advantages, including reducing the volume of concrete sections required in structural elements, increasing building occupancy rates, and extending the building’s service life (Papadakis, 2000).
When high-strength concrete (HSC) is employed in building construction, there is a greater chance of having smaller concrete sections compared to when normal-strength concrete (NSC) is used. However, will the use of less volume of HSC translate to a reduction in CO2 emission for which the construction industry is famed for? Well, the answer depends.
Due to their inherent performance qualities, high strength concrete (50–100 MPa) and ultra high strength concrete (UHSC) (>100 MPa) are being utilized more frequently in the construction industry. As a result of their significant global usage, these concrete mixes have a higher carbon footprint. It is therefore important to take into account the embodied carbon of the HSC and UHSC.
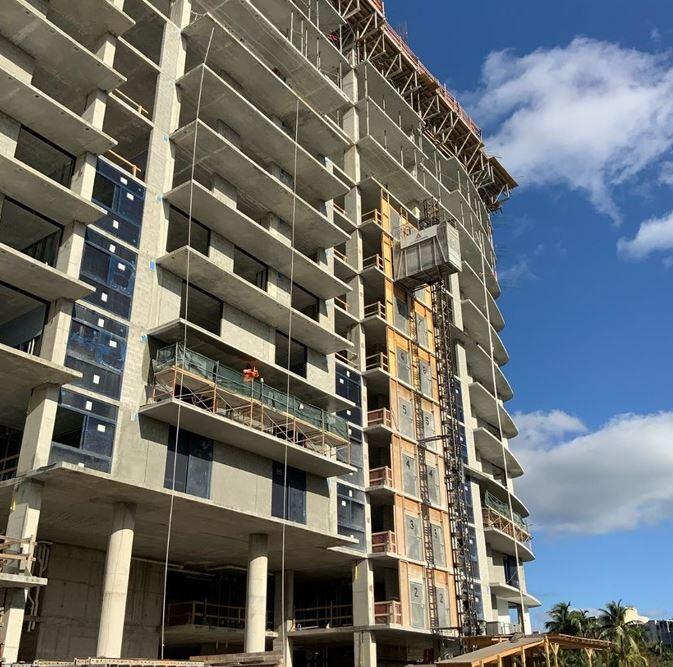
When compared to normal strength concrete, high-strength concrete has a lower water-to-binder ratio. As a result of this, a lot of cement or binder is needed and a lot of CO2 is emitted during the production of high strength concrete.
However, as stated above, the volume of concrete structures can be considerably reduced by adopting concrete systems with high mechanical properties. Because less material is required for the same structural performance, this “performance strategy,” which includes the use of high-performance concrete, reduces carbon dioxide emissions (Fantilli et al, 2019).
Summarily, high concrete strength has a higher carbon footprint, especially during the production stage (Habert and Roussel, 2009), because more binder (and sometimes fibres) is required. As a result, material reduction may not always be sufficient to offset the rise in CO2 emissions caused by higher concrete classes.
Studies on the Environmental Impacts of High Strength Concrete
The Global Warming Potential (GWP) of ultra-high performance concrete and normal-strength concrete was compared quantitatively for bridge structures at the construction stage by various researchers (Bertola et al., 2021; Dong, 2018; Rangelov et al., 2018; Sameer et al., 2019).
According to a comparison made by Aqib and Ma (2022), it was observed that the global warming potential of ultra-high-performance concrete was higher than that of normal-strength concrete by more than 60%. This can be attributed to the increased cement usage in ultra-high-performance concrete and the presence of steel fibres. As the cement content is much lower in conventional concrete, the GWP is also lower.
Reference | GWP of normal-strength concrete (kgCO2eq) | GWP of ultra high-strength concrete (kgCO2eq) | Percentage difference (%) |
Dong, 2018 | 348 | 877 | 60% |
Bertola et. al 2021 | 7217 | 10914 | 66% |
Sameer et al., 2019 | 390 | 1700 | 77% |
Rangelov et al., 2018 | 434 | 1930 | 78% |
However, at the maintenance stage or during the service life of the structure, it was observed that ultra-high-performance concrete had less GWP compared to normal-strength concrete. Due to its superior durability and high strength, the maintenance needs of ultra-high-performance concrete are very low as compared to conventional concrete and hence, the life cycle GWP of ultra-high-performance concrete is very low as compared to normal strength concrete (Aqib and Ma, 2022).
In another study by Larsen et al (2017), a 40m long pedestrian bridge was designed with normal strength concrete (fck = 30 MPa) and ultra high performance concrete (fck = 150 MPa). The bearing structure is divided into two spans of 20 m, and consists of two simply supported T-beams as shown below.
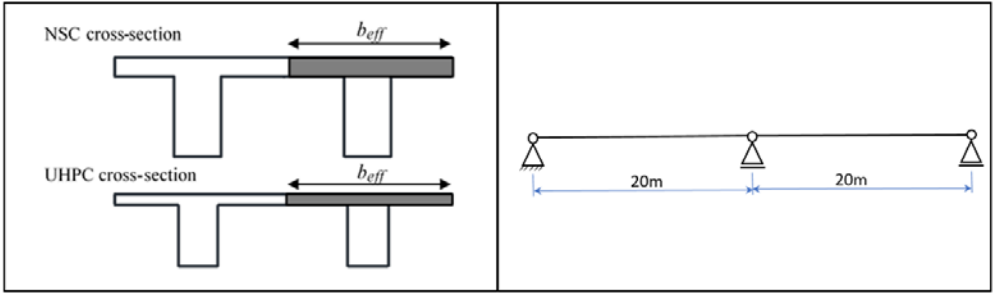
Using life cycle analysis (LCA), the authors determined the environmental impact of each alternative. It is important to note that due to the fact that ultra high strength concrete contains about two to three times the cement content of normal strength concrete, it was important to reduce the volume of the section made with UHSC. After the design, the total amount of concrete used in the UHPC alternative was reduced by 36.7% compared to the NSC alternative.
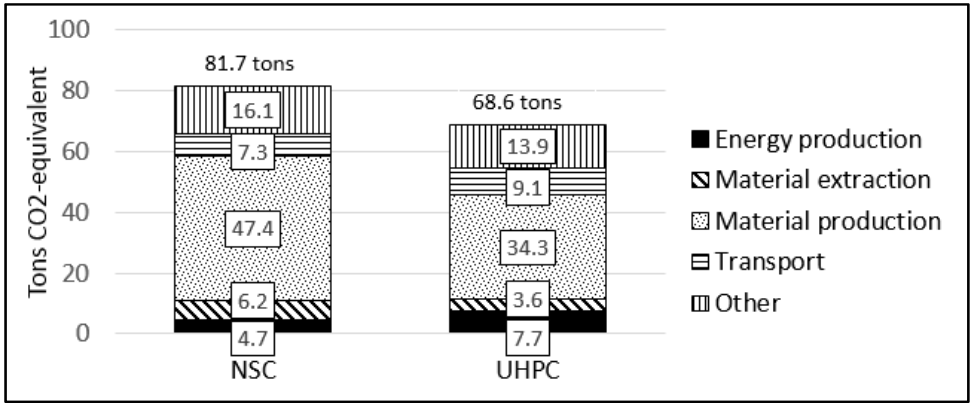
The contribution of the major life cycle phases to the total GWP in tons CO2 equivalent across the lifetime of each alternative is shown in Figure 3. The NSC alternative has lifetime CO2 equivalent emissions of 81.7 tons, compared to 68.6 tons for the UHPC option.
Material manufacturing is the major source of CO2 equivalent emissions for both alternatives at 58% of the overall emissions for the NSC alternative and 50% of the total emissions for the UHPC alternative.
The major findings of the study suggest that using UHPC in pedestrian bridges may have some environmental and design viability. Over a 200-year period, the UHPC alternative had overall lower consequences than the NSC alternative, which were much less. This suggests that the UHPC alternative is better in terms of the environment.
However, the results of this study need to be critically analyzed in light of methodological decisions made regarding the selection of functional units and life cycle phases, the uncertainty surrounding future emissions from material production, and the restrictions of the common T-beam bridge design in a comparative analysis.
In another study, Fantilli et al, (2019) evaluated three RC buildings with 14, 30, and 60 floors, respectively, whose structures are developed using finite element software for four different concrete classes (C25, C40, C60 and C80). The entire amount of concrete and reinforcement required to meet static and dynamic requirements was determined in this manner. When these quantities are multiplied by the materials’ unit carbon dioxide emissions, the global warming impact is calculated.
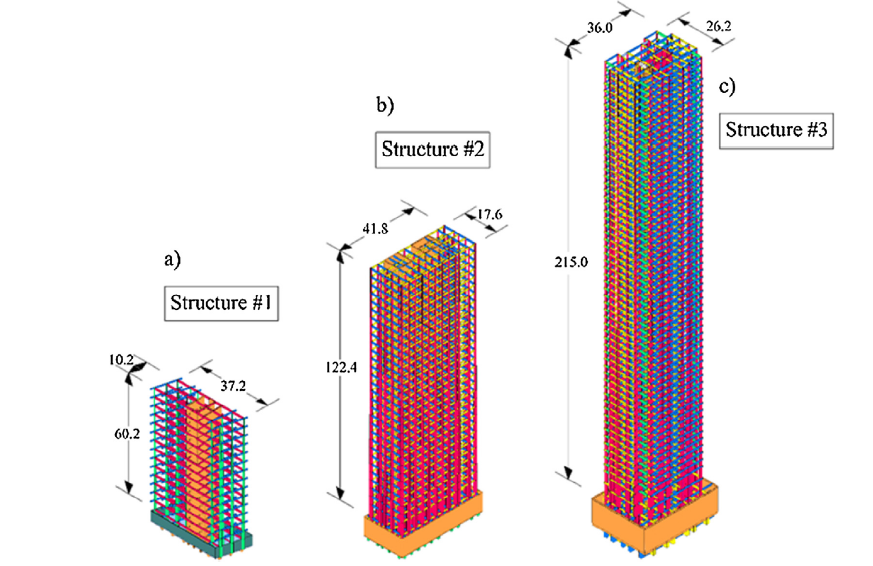
The parametric CO2 content per cubic metre of the concrete classes are provided in the Table below;
Material | Parametric CO2 amount (kg/m3) |
C25 | 215 |
C40 | 272 |
C60 | 350 |
C80 | 394 |
Indicators that link the carbon footprint of concrete to both the cement volume per unit and the compressive strength can be found in the literature. To estimate the unit CO2 emissions as a function of the cylindrical compressive strength of concrete, Habert and Roussel (2009) presented the following empirical relationship:
kg of CO2 per cubic meter of concrete = δ√Strength of concrete
Where δ = 46.5 kgCO2
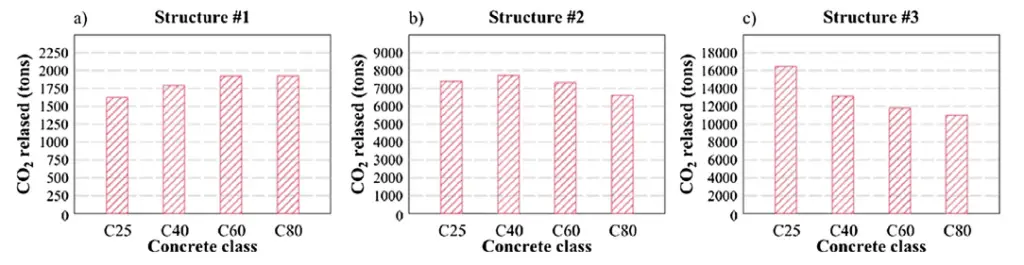
From the study, it was observed that Building #1, which has the lowest number of storeys, exhibited a gradual increase in CO2 with concrete class (Fig. 5a). In contrast, the carbon footprint in the 60-story skyscraper (i.e., Structure #3 – Fig. 5c) reduces as concrete strength increases. At Structure #2, which has 30 stories (see Fig. 5b), emissions increase from classes C25 to C40 but fall for higher classes (especially from C60 to C80). As would be expected, each structure uses less structural material as concrete strength rises.
From the study, the lowest effect of CO2 emission may be ensured for low-rise buildings (14 storeys) by employing normal strength concrete (e.g., C25). In rare circumstances, even when low-strength concrete is present, the theoretical cross-sectional area can be less than the minimum. As a result, the use of high strength concrete in these elements does not rule out the possibility of using less concrete and steel rebar. In comparison to normal strength concrete, it causes an increase in CO2 emissions, particularly in low-rise structures.
The use of high-strength concrete, on the other hand, reduces the environmental impact of high-rise buildings (60 floors). As a result, in tall buildings, the use of the performance strategy to reduce the environmental impact of concrete structures becomes particularly successful, because the volume of structural elements can be significantly reduced.
References
Aqib S. M. and Ma Z. J. (2022): A Review on Carbon Emissions of Ultra-High-Performance Fiber Reinforced Concrete as a Building Construction Material. International High Performance Buildings Conference. Paper 426. https://docs.lib.purdue.edu/ihpbc/426
Bertola, N., Küpfer, C., Kälin, E., & Brühwiler, E. (2021). Assessment of the environmental impacts of bridge designs involving UHPFRC. Sustainability (Switzerland), 13(22), 1–19. https://doi.org/10.3390/su132212399
Dong, Y. (2018). Performance assessment and design of ultra-high performance concrete (UHPC) structures incorporating life-cycle cost and environmental impacts. Construction and Building Materials, 167, 414–425. https://doi.org/10.1016/j.conbuildmat.2018.02.037
Fantilli A. P., Mancinelli O. And Chiaia B. (2019): The carbon footprint of normal and high-strength concrete used in low-rise and high-rise buildings, Case Studies in Construction Materials, 2019(11)e00296, https://doi.org/10.1016/j.cscm.2019.e00296.
Habert G. and N. Roussel (2009): Study of two concrete mix-design strategies to reach carbon mitigation objectives, Cem. Concr. Compos. 31 (6) (2009) 397–402.
IngLarsen I. L., Aasbakken I. G., O’Born, Vertes K. and Thorstensen R. T. (2017): Determining the Environmental Benefits of Ultra High
Performance Concrete as a Bridge Construction Material. IOP Conf. Series: Materials Science and Engineering 245 (2017) 052096 doi:10.1088/1757-899X/245/5/052096
Papadakis V. G. (2000): Effect of supplementary cementing materials on concrete resistance against carbonation and chloride ingress, Cement and Concrete Research, 30(2):291–299
Rangelov, M., Spragg, R. P., Haber, Z. B., & H, D. (2018). Life-cycle assessment of ultra-high performance concrete bridge deck overlays (1st Edition).
Sameer, H., Weber, V., Mostert, C., Bringezu, S., Fehling, E., & Wetzel, A. (2019). Environmental assessment of ultra-high-performance concrete using carbon, material, and water footprint. Materials, 16(6). https://doi.org/10.3390/ma12060851