Geosynthetics are planar products manufactured from a polymeric material (polypropylene, polyester, polyethene, polyamide, PVC, etc) or natural materials and are used with soil, rock, earth, or other geomaterials as an integral part of a civil engineering project, structure, or system.
Geonaturals are products made from natural fibres (such as jute, coir, cotton, wool, etc.) that are utilized mostly in temporary civil engineering applications. Due to the fact that these materials biodegrade quickly when utilized with earth materials, they don’t have as many field applications as geosynthetics do.
During the production of geosynthetics, planar textile structures are created by combining elements such as fibres or yarns. Depending on their characteristics and purposes, many of such products fall under the general term ”geosynthetics”.
For instance, a permeable geosynthetic made of textiles is called a geotextile. Geogrids are a regular network of tensile elements with holes large enough to interlock with surrounding fill material and are generally utilized for soil reinforcement.
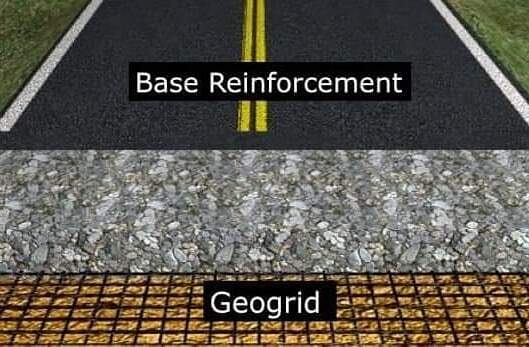
Low permeability geosynthetics called geomembranes are employed as fluid barriers in engineering constructions such as sanitary landfills. To benefit from the properties of each component, geotextiles and related products like nets and grids can be mixed with geomembranes and other synthetic materials.
Geotextile-geonet composites, geotextile-geomembrane composites, geotextile-geomembrane-grid composites, geotextile-polymeric core composites, and even three-dimensional polymeric cell structures can be combined to create these products, which are known as geocomposites.
The process utilized to assemble the filaments or tapes into the planar textile structure determines the type of geotextile. Geotextiles fall into one of two categories: woven or nonwoven. Polyolefin sheets are extruded and oriented to create rigid geogrids with integral joints. Flexible geogrids are constructed from polyester strands that have been knit or weaved together at their crossover points and then coated with a polymer.
The use of geosynthetics to replace customary construction methods has a wide range of applications. Subgrade stabilization, ground improvement, slope stabilization, reinforced earth, a system for lining and cover of landfills, retaining walls, and erosion and scour protection measures for river banks are some of the potential applications. The materials have been around for thirty years, but they haven’t been extensively utilised in all the possible areas of civil engineering construction.
The article discusses the current state of geosynthetics application in various civil engineering projects as well as its potential in the future. It also discusses the challenges of using this material, along with suggestions for how to get over them.
Applications and Functions of Geosynthetics
Geosynthetics have the following primary functions in civil engineering construction works:
- Separation
- Filtration
- Drainage
- Reinforcement
- Barrier
- Protection
Separation
A geosynthetic material is referred to as performing a “separation function” if it must prevent the mixing of adjacent dissimilar soils and/or fill materials during construction and over the anticipated service life of the application under consideration. Synthetic geotextiles are utilized for this. Depending on the manufacturing process, the following categories of geotextiles are currently available:
- Woven Geotextile
- Nonwoven Geotextile
- Knitted Geotextile
- Stitched Geotextile
Monofilament, multifilament, or fibrillated yarns, as well as slit films and tapes, are used to create woven geotextiles. Although nonwoven textile production is a recent industrial development, the weaving method has been around for quite some time. Continuously extruded synthetic polymer fibres or filaments are spun, blown, or otherwise placed onto a moving belt.
The mass of filaments or fibres is then either heat bonded, in which the fibres are welded together by heat and/or pressure at their sites of contact in the nonwoven mass, or needle punched, in which the filaments are mechanically entangled by a succession of small needles.
Instead of using a weaving loom, a knitting machine can be used to interloop one or more yarns (or other components) to create a knitted geotextile. Geotextiles that have been stitched together or sewn together using fibres, yarns, or both. Figure 2 illustrates how the geotextile layer keeps the structural integrity and functionality of both materials intact by preventing the mixing of soft soil and granular fill.
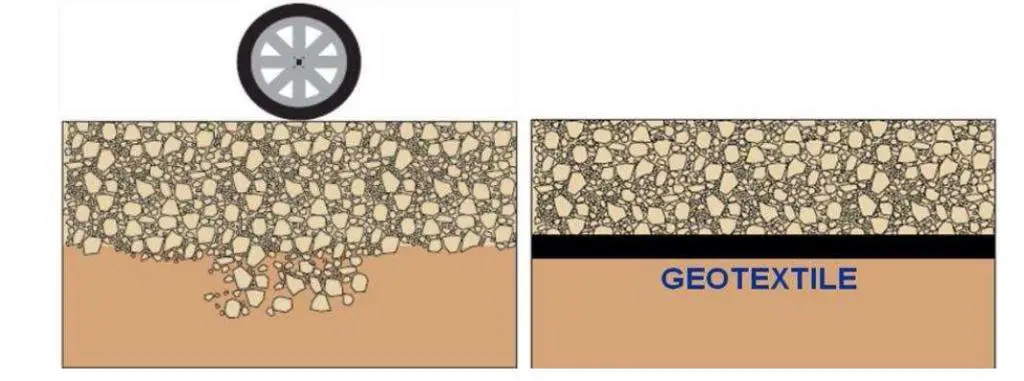
A geosynthetic layer is typically placed at the interface between soft foundation soil and the overlaying granular layer in many geosynthetic applications, particularly in roadways, rail tracks, shallow foundations, and embankments. In this case, it becomes challenging to pinpoint if the primary role of the geosynthetic is reinforcement and/or separation.
When the ratio of the applied stress (s) on the subgrade soil to the shear strength (cu) of the subgrade soil has a low value (less than 8), separation can be a dominant function over reinforcing, and it is largely independent of the settling of the reinforced soil system.
Filtration
A geosynthetic may serve as a filter that allows for enough fluid flow with minimal soil particle migration across its plane during the course of the application’s anticipated service life. Figure 3 demonstrates how a geosynthetic allows water to escape from a soil mass while limiting uncontrolled soil particle mobility. When a geosynthetic filter is positioned next to base soil (the soil to be filtered), a gap forms between the geosynthetic’s structure and the original soil structure.
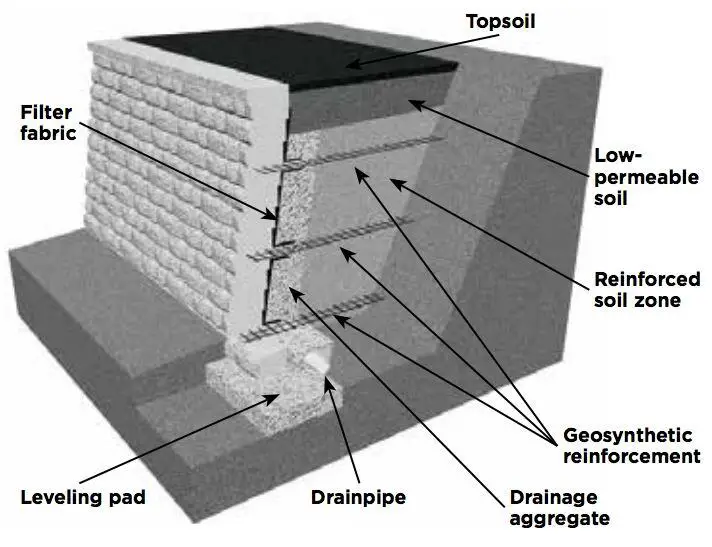
Certain soil particles, especially those nearest to the geosynthetic filter and with diameters smaller than the filter opening size, can go through the geosynthetic under the influence of seepage flow thanks to this discontinuity. The retention of the base material and permeability are the two parameters on which the design of the geotextile filter is based.
Soil Retention Criterion
O95 < αDw
O95 = Apparent opening size of geotextile
α = 0.5 to 5.0 (a constant)
Dw = Representative soil particle size
= D90 for unidirectional flow
= D15 for cyclic flow Permeability Criterion
Permeability criterion
• Less critical applications and less severe conditions Kgt > Ksoil
• Critical applications and severe conditions Kgt > 10Ksoil
Traditional granular filters can be replaced by geosynthetic filters since they are less prone to clog up regularly over the course of a structure’s service life. Table 1 provides a comparison of granular and geotextile filters. The geotextile filters finds application in earth dams, embankments, engineered landfill etc.
Granular Filter | Geotextile Filter |
Quality control can be difficult | Quality control can be easily assured |
Installation is more complex | Installation is easy |
There can be discontinuities in the filter media | The filter media is continuous |
Clogging can be frequent | Clogging takes a very long time |
Intimate contact with surface | Surface preparation is required |
Large volume of granular material | Conserves granular materials |
Drainage
A geosynthetic is said to perform the drainage function if it permits adequate fluid flow with little soil particle movement within its plane from the surrounding soil mass to different outlets. Figure 4 demonstrates how water from the pavement surface is captured and carried to the embankment drainage built by the geosynthetic layer placed in the pavement.
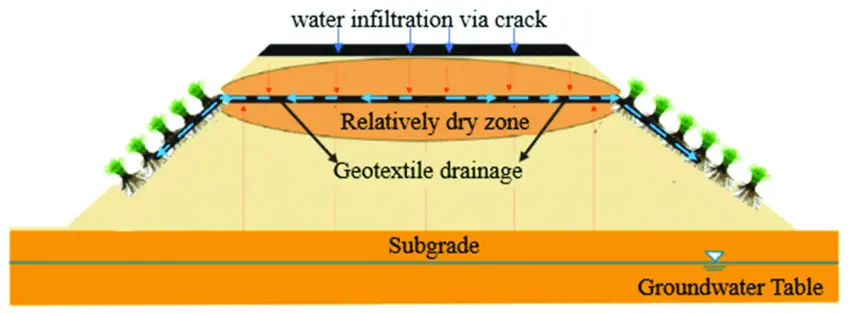
It should be mentioned that a geosynthetic dissipates the surplus pore water pressure while carrying out the filtering and drainage tasks by allowing water to flow in plane and across its plane. This can be accomplished by combining the geocomposite with geotextile (for filtering action) and geonet (for drainage function). It also considers load distribution.
Reinforcement
A geosynthetic serves as reinforcement by increasing the mechanical characteristics a soil mass as a result of its incorporation. A composite material known as “reinforced soil” is created when soil and geosynthetic reinforcement are mixed. This material has strong compressive and tensile strengths and is conceptually comparable to reinforced concrete.
In actuality, the primary function of any geosynthetic used as reinforcement in geotechnical structures is to withstand applied stresses or prevent unacceptable deformations. By acting as a tensioned part in this process and being joined to the soil/fill material via friction, adhesion, interlocking, or confinement, the geosynthetic preserves and enhances the stability of the soil mass.
The soil is reinforced using geogrid. It is a planar polymeric product made of crossing tensile-resistant ribs that are integrally joined at the joints to form a mesh-like or net-like regular open network. Extruded geogrid, bonded geogrid, and woven geogrid are the three different terms for the geogrid that results from joining the ribs together.
A regularly punctured polymer sheet is stretched longitudinally to create an extruded geogrid, which has a substantially higher tensile strength in the longitudinal direction than the transverse direction. a geogrid created by stretching a polymer sheet that has been punctured regularly in both the longitudinal and transverse directions; as a result, it has an identical tensile strength in both directions.
When building embankments with a constrained width and requiring that the face of the wall stay nearly vertical, reinforced earth (RE) techniques are typically used. The use of expensive retaining walls is completely eliminated by the RE wall technique. When ground conditions are unfavorable and adequate backfill materials are locally accessible, savings of between 25 and 50 percent have been documented. Figure 5 shows the various parts of the RE wall.
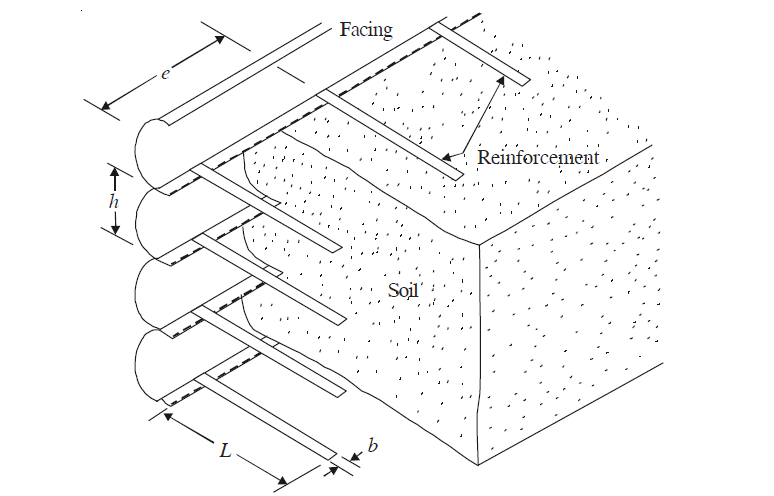
The proper establishment of the friction connection between the soil and the reinforcement, which will depend on the composition, gradation, density, and properties of the fill material and geosynthetics, is essential for the stability of RE structures. RE structures are best suited to cohesionless soil that has been compacted to densities that cause volumetric expansion during shear.
Conversely, cohesive fill material produces short-term structural instability as a result of pore water pressure buildup, creep behavior, and frost actio. Early in the 1970s, because to worries about potential corrosion of metallic reinforcement, geotextiles were first used as reinforcing materials. While steel-reinforced walls have been built to heights exceeding 40 m, geosynthetic reinforced walls have been built to maximum heights of less than 20 m.
Barrier
In the lining and cover of an engineered landfill, geomembrane is employed as an impermeable barrier. It is a planar, comparatively impermeable synthetic sheet used as a barrier or liner in construction projects to restrict fluid flow. The material could be polymeric, asphaltic, or a combination of both. For leachate migration under subsoil conditions, natural or compacted clay liners are insufficient to provide the necessary level of environmental protection or necessitate additional thickness.
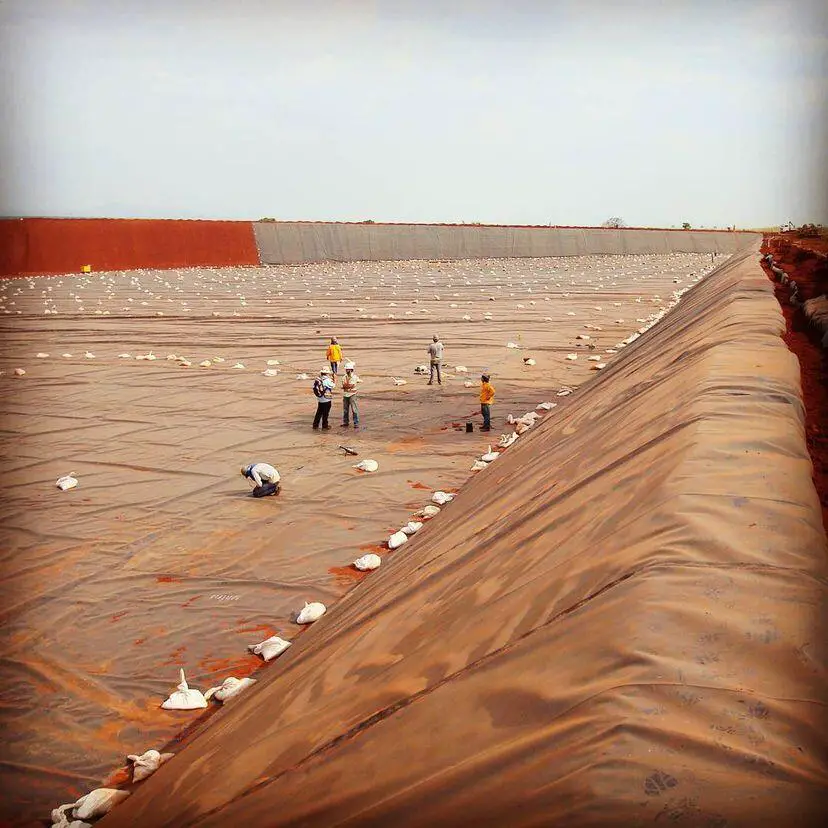
The use of geomembrane as a suplimentary barrier provides an economical approach to achieve the regulatory standard. Depending on the need, it can be employed in a variety of ways, including GCL (geosynthetic clay liner), HDPE (high density poly ethylene), and LDPE (low density poly ethylene). An engineered landfill offers the chance to use geosynthetics for all of their purposes in various locations. Figure 6 illustrates a typical application of geosynthetics in constructed landfills in all of its forms and purposes.
Protection
When a geosynthetic is applied on a soil surface, it stabilizes the surface by preventing soil particles from moving and dispersing due to wind and rain erosion, frequently while permitting or encouraging the growth of flora. Due to the hydraulic pressure of the soil, the conventional design of cementing the banks is not an inexpensive solution. To prevent erosion of river banks and seashores, geotextile gabions, tubes, and bags are utilized.
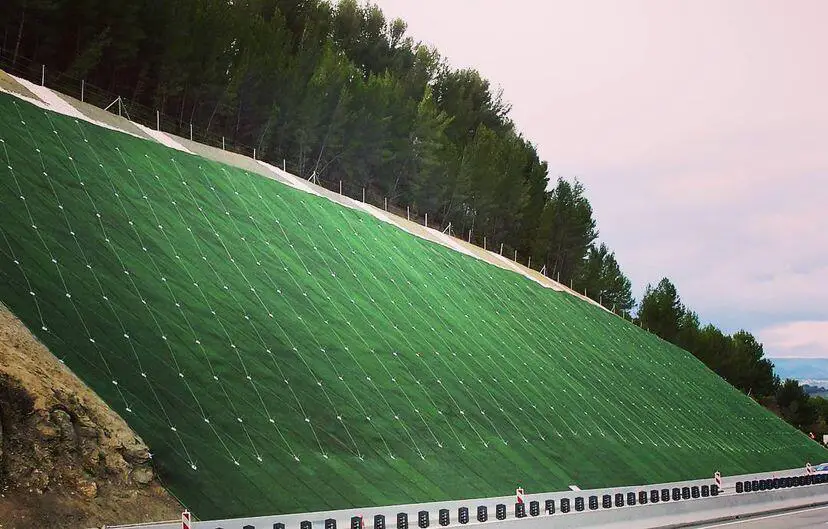
Conclusion
The usage of geosynthetic materials in civil engineering projects has a lot of promise. Although the use of geosynthetic materials in the building of landfills and embankments has gained widespread recognition, additional applications are still lacking. By providing the necessary knowledge at the undergraduate level and scheduling short-term courses for field engineers, certain confidence-building tactics might be implemented. The creation of a uniform code of conduct for use in India is essential, and testing facilities may be improved to make them easily accessible to all users within appropriate travel distances.
Glad to check your page and we are manufacturer of waterproofing materials, includes drainage sheet, drainage board, waterproof membrane, geomembrane, geotextile, drainage cell and HDPE sheet. Our price is good for FOB and CIF.