Reinforced concrete is one of the most popular construction materials in modern building construction, which is known to be responsible for significant amounts of steel and cement consumption. Due to its flexibility, strength, wide availability, and high adaptability, reinforced concrete is widely utilised all over the world. However, the high carbon footprint of concrete from ‘cradle to grave’ remains a big concern for our environment.
The term “sustainable concrete” refers to concrete that has been optimized in terms of material and technology, as well as technical, economic, and environmental factors. Cement is a major contributor to the high environmental impact values of concrete production (Marinkovi et al., 2008), accounting for more than 5% of annual CO2 emissions worldwide (Kurda et al, 2018), as well as other environmental impact categories, such as energy usage (Paris et al., 2016).
According to UNEP (2019), building construction and operations accounted for the largest share of both global final energy use (36%) and energy-related CO2 emissions (39%) in 2018.
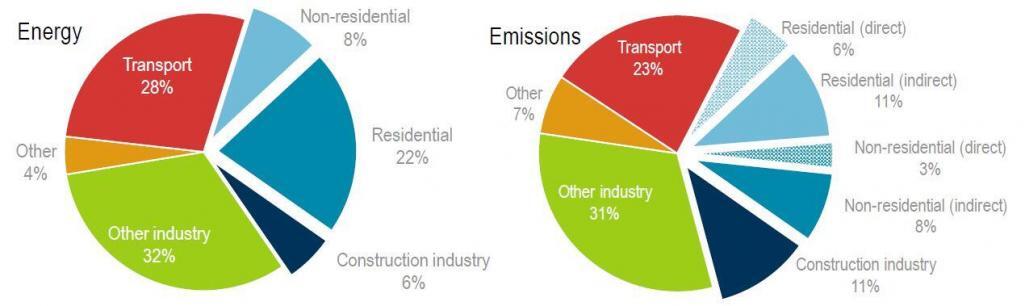
To achieve net-zero CO2 emissions in the construction industry, material efficiency must be improved to minimize the primary demand for these materials. Furthermore, higher-value recycling and reuse of waste materials from the construction industry must be implemented, and the production of concrete/cement must be decarbonized. The most effective strategy to reduce steel and concrete emissions is to utilize them only when they are absolutely necessary for new structures with an emission reduction potential of 25 to 50%.
This necessitates design innovation in the areas of material substitution, extended product and structural lifetimes, ease of deconstruction, component reuse, and high-value recycling at the end of their useful lives. This will necessitate collaboration with national organizations responsible for a variety of issues, including architecture, design, civil engineering, construction, trades, and the development and enforcement of building codes.
The carbon footprint is the cumulative quantity of GHG emissions generated by a person, firm, company, activities, or items, measured in CO2e, and expressed in tons of carbon dioxide emissions per year. CO2 equivalent is a statistical scale that is used for the evaluation and measurement of different GHGs emissions on the basis of their global warming potential (GWP). The CO2e of a particular gas can be obtained by the multiplication of its weight by its related global warming potential as described in the equation below;
“kgCO2e = (weight of the gas in kg) × (GWP of the gas)”
Carbon Footprint of Different Construction Materials
Building structures are influenced by construction practices, regulations, and the accessibility of building materials in the area where they are built. However, the load-bearing and secondary construction elements of a structure are usually created using reinforced concrete, masonry (bricks), wood, steel, concrete, and a combination of these materials.
Due to the wide range of materials available in the construction market, the exact construction materials for any structures may not be known. However, for reinforced concrete, it is common knowledge that concrete (Hoxha et al., 2017) and structural steel (Thiel et al., 2013) are the materials that have the biggest effects on the environment.
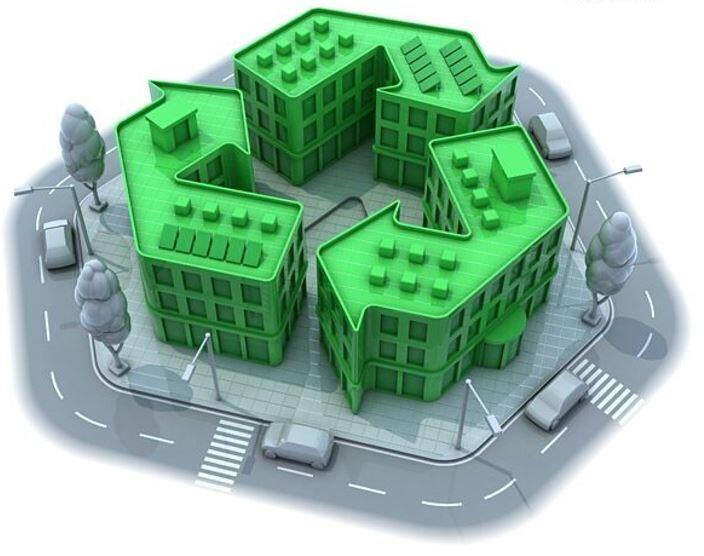
When compared with residential buildings built with other common construction materials, concrete structures have a bigger environmental impact than timber structures (Skullestad et al, 2016), masonry structures have a greater impact than steel (Rossi et al., 2012), and steel has a greater impact than wood (Carre, 2011).
The analysis of various structures (concrete, steel, and timber) for commercial buildings reveal a variation in total life cycle emissions of 9%. It has also been observed by researchers that for commercial/office buildings, concrete has a higher environmental impact than steel (Acree and Arpad, 2005). These two structural materials are the main contributors to the embodied impact of office buildings (Kofoworola and Gheewala, 2008).
The building envelope, in addition to structural elements, makes up a sizeable component of the overall life cycle effect (Hoxha et al., 2017; Stephan et al., 2017), and non-structural materials are the main source of uncertainty in LCA results (Hoxha et al, 2017).
Many studies in the literature have focused on maximizing the life cycle of a building envelope by examining various materials and elements because it encompasses not only the production of materials, as is the case with the load-bearing structure, but also replacement, maintenance, refurbishment, energy use processes, and energy efficiency measures/strategies (Ferdyn-Grygierek and Grygierek, 2017).
The variation and dependence of the envelope composition on a large number of materials, however, necessitates an extensive breakdown and normalisation analysis. This is because “a single building could comprise over 60 basic materials and 2000 separate products” (Haapio and Viitaniemi, 2008).
The embodied energy of various construction materials (cradle to gate) according to the ICE database (2011) are as follows;
Construction Material | Embodied Carbon (kgCO2e/kg) |
Gravel or crushed rock | 0.0052 |
Average CEM I (Portland cement 94% clinker) | 0.74 |
Sand | 0.0051 |
Mortar 1:3 (Cement:Sand mix) | 0.221 |
Mortar 1:4 (Cement:Sand mix) | 0.182 |
Mortar 1:5 (Cement:Sand mix) | 0.156 |
Mortar 1:6 (Cement:Sand mix) | 0.136 |
Steel (average recycled content) | 1.46 |
Steel (virgin) | 2.89 |
Steel (recycled) | 0.44 |
Concrete C16/20 | 0.1 |
Concrete C20/25 | 0.107 |
Concrete C25/30 | 0.113 |
Concrete C28/35 | 0.120 |
Concrete C32/40 | 0.132 |
Concrete C40/45 | 0.151 |
Reinforced concrete 25/30 (with 110 kg/m3 of steel) | 0.198 |
Rammed soil | 0.024 |
Expanded polystyrene | 3.29 |
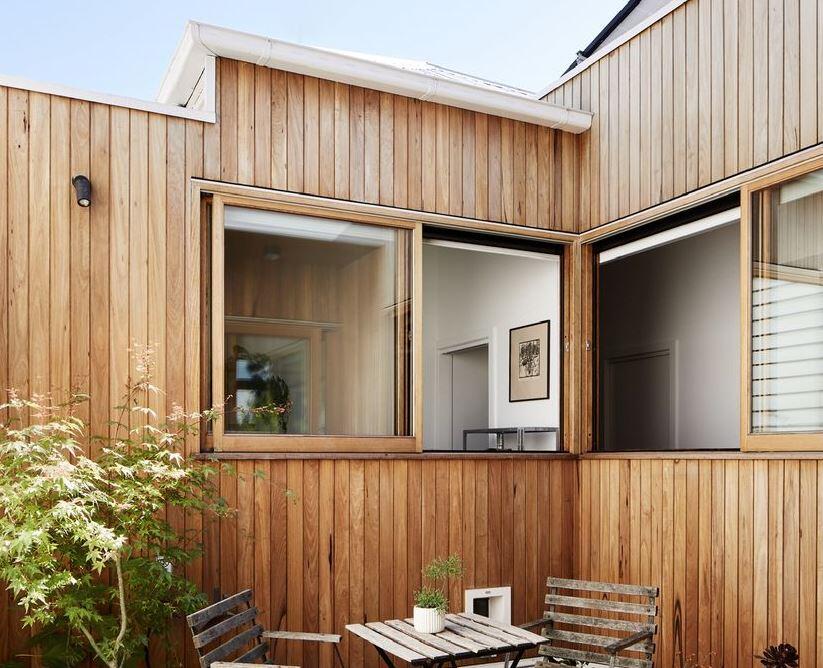
Carbon Footprint of Reinforced Concrete
The relationship between the production of the raw materials from which structural elements such as slabs, beams, columns, etc. are formed influences the embodied carbon (EC) of those structural elements and the finished structures they eventually produce (Hacker et al., 2008; Harrison et al., 2010).
As a result, there has been a lot of interest lately in the embodied carbon of structural materials (Purnell, 2013). In both scientific and quasi-technical literature, comparisons of the EC of concrete, steel, and timber (or structures made primarily of these materials) have become more common, purporting to show one or more of these materials as “the greenest.”
It can be difficult and complex to evaluate embodied carbon. The quantity of CO2 emitted per unit of production by the three main structural materials — steel, wood, and concrete — is difficult to quantify (Purnell, 2013). In general, such generalizations ought to be avoided, and any structural design or analysis ought to go through a thorough life-cycle analysis (LCA, as defined by ISO 14040, 2006), taking into account CO2 emissions generated during all production, processing, installation, maintenance, demolition, and disposal stages for the particular components of the structure under study (Purnell, 2013).
According to studies on CO2 emissions over the course of a building’s life cycle, the stages of construction, operation, and demolition are responsible for roughly 13%, 85%, and 2% of CO2 emissions, respectively (Li and Chen, 2017).
The optimization of reinforced concrete structural designs can help reduce the embedded carbon or CO2 footprint in reinforced concrete structures in addition to using novel construction materials like low-carbon cement and clinker substitutes (WBCSD-IEA 2009).
In current practice, structural designs are usually optimized for total cost or total weight. Yet, optimal designs for embodied energy or CO2 footprint are also preferred from a sustainability perspective (Yeo and Potra, 2015). It is important to remember that the CO2 footprint embodied in the reinforced concrete used in a building is only a small portion of the total CO2 footprint included in that building, even if the CO2 footprint decrease addressed in the research only relates to the RC structure. Yet, the RC’s reduced carbon footprint adds significantly to the overall reduction in carbon emissions.
Optimisation of Reinforced Concrete Structures for Environmental Impacts
Interest in optimizing RC structures by taking environmental factors into account has been seen in a lot of research efforts by scholars.
Two objective functions were minimized by Paya-Zaforteza et al. (2009) using a simulated annealing-based approximate optimization method:
(1) total CO2 emissions embodied in the structure and
(2) total structural cost.
The dimensions of the cross sections of the columns and beams, the type of concrete and steel reinforcement used, and the details of the longitudinal and shear reinforcement in the columns and beams were all design considerations. The methodology was tested using six standard building frames with up to four bays and eight stories. From the study, it was observed that the optimal structure for reducing emissions is just slightly more expensive (2.8%) than the optimum structure for minimizing cost.
Similar research was done by Villalba et al. (2010) for cantilever earth-retaining walls that ranged in height from 4 to 6 m, and they also observed that the optimum design for reducing embedded CO2 emissions is just slightly (1.4%) more expensive than the optimum for minimizing cost. Interestingly, the authors observed that, despite the latter requiring around 2% more steel, walls designed for the lowest embedded CO2 emissions needed about 5% more concrete than those optimized for least cost. Moreover, the concrete grade is greater in the case of walls with reduced emissions.
Yeo and Gabbai (2011) investigated the cost implications of optimizing a simple RC structural element (a rectangular beam with fixed moment and shear strengths) in order to reduce embodied energy. The results show that, as compared to a cost-optimized design, optimizing structural member designs for the least embodied energy led to a 10% reduction in embodied energy at the expense of a 5% increase in cost.
The actual reduction in embodied energy is determined by the cost ratio of steel reinforcement to concrete, which must account for both the material costs of the steel and concrete as well as construction costs like those associated with placing the concrete and installing the reinforcement.
Moreover, the concrete sections optimised for embodied energy contain more reinforcements than concrete compared to the members that were optimised for minimum cost. This supported the conclusions reached by Villalba et al (2010). To ensure that ductility is adequate for design purposes despite the increase in the amount of steel, the optimization technique’s constraints included a restriction on the strain in the reinforcing bars.
Yeo and Potra (2015) conducted exploratory research to evaluate the feasibility of optimising RC design for CO2 emissions. The CO2 footprint optimization increased the proportion of steel in the member cross sections, but the requisite ductility was guaranteed by constraints set during the optimization process.
Depending on the parameter values taken into account, the CO2 footprint reduction achieved by optimizing the design to achieve minimum carbon emissions as opposed to optimizing the design to achieve minimum cost, ranges from 5% to 15%.
The study took into account an RC frame that was subjected to lateral and gravitational loads. It was shown that the design optimized for CO2 footprint achieved a smaller CO2 footprint (by 5 to 10%) than the one optimized for cost, depending on the parameter values used in the computations.
Smaller reductions may be observed in low-rise structures and other buildings with predominantly tension-controlled members. The reduction, however, might be greater for structures like high-rise buildings whose members often withstand extremely high compressive stresses. This category may also include certain concrete members that have been prestressed or post-tensioned.
In a case study involving a commercial-residential complex in South Korea, Paik and Na (2019) examined and contrasted the carbon dioxide emissions of a normal reinforced concrete slab against a voided slab system. A process-based life-cycle assessment (LCA) was employed to determine the carbon dioxide emissions during the construction phase, which includes all operations from the manufacture of materials through completion.
The results show that the normal reinforced concrete slab and the voided slab system have total CO2 emissions of 257,230 and 218,800 kg respectively. The main source of CO2 reduction comes from the embedded carbon dioxide emissions of building materials, which has a total of 34,966 kg of CO2. The transportation of building materials ranks as the second biggest source with 3417 kg of CO2. The study mentioned above shows that decreasing the amount of concrete used can aid in reducing embodied carbon.
Gan et al. (2017) looked into the effects of material selection, recycled content, building heights, and structural forms on the embodied carbon in high-rise buildings. The findings showed that while steel buildings release 25% to 30% more embodied carbon than composite and RC buildings, they are 50%–60% lighter overall.
This is due to the fact that the lateral load-resisting system of a steel building typically calls for sizable quantities of steel sections that are particularly carbon-demanding. If more than 80% of the steel is recycled, the steel building’s embodied carbon can be reduced to the lowest level of the three structures.
When compared to a steel building composed completely of recycled steel, the RC structure has the lowest embodied carbon, even when employing cement substitutes like fly ash and powdered granulated blast furnace slag (Gan et al, 2017). The unitary embodied carbon (kg CO2-e/m2 GFA) vs. building height graph displays an upward concavity, showing that there is a recommended height range for each structural type where embodied carbon is at its lowest level.
Conclusion
The results from the literature surveyed showed that the embodied carbon in buildings and structures varies considerably depending on the building materials and structural designs employed. Depending on structural performance, material cost and availability, and other factors, structural engineers may in fact have a variety of options for construction materials and structural designs, which can lead to significant variations in the embodied carbon of high-rise buildings.
These studies can help decision-makers consider sustainability concerns when making choices about structural forms and materials in particular. First off, for highrise buildings, selecting the most effective lateral load-resisting system for a particular height can result in significant embodied carbon savings because it accounts for 70% to 80% of the embodied carbon in high-rise buildings.
Engineers can, for instance, select the less carbon-embedded core-outrigger structural form to withstand lateral stress for a 60-story high-rise building. Once the structural form has been decided upon, engineers can select a low-carbon alternative by taking into account the readily available materials (concrete, rebar, and structural steel) and their recycled content.
The following recommendations can be followed to reduce the carbon footprint of reinforced concrete structures:
(1) Floor slabs account for the majority of the mass in load-bearing building structures, and improving/optimising them can result in significant cost/carbon savings. Voided slab solutions, thinner sections, and slabs with high-performance concrete can be adopted.
(2) For load-bearing building structures with columns of smaller spacing (say equal to or less than 4m), only concrete of lower strength classes (e.g., C20/25 and C25/30) should be used. The environmental implications of employing higher-strength concrete are exacerbated by increased cement use.
(3) Variants of load-bearing building structures with columns of higher spacing (say about 8 m) are best designed from a concrete of strength class C50/60, which has the lowest construction costs and environmental impact.
(4) It is advantageous to design a building with more storeys by recalculating the construction costs and environmental impacts per m2 of usable area. This is due to the foundation structure, which is the most expensive for a building with fewer storeys.
References
Acree G. A., Arpad H. (2005): Comparison of environmental effects of steel- and concrete-framed buildings, J. Infrastruct. Syst. 11 (2): 93–101.
Carre A., (2011): A Comparative Life Cycle Assessment of Alternative Constructions of a Typical Australian House Design, Final Report, Project No: PNA147-0809 Forest & Wood Products Australia, Melbourne, Victoria, 2011.
Ferdyn-Grygierek J. and Grygierek K. (2017): Multi-variable optimization of building Thermal design using genetic algorithms, Energies 10 (10) (2017) 1570.
Gan V. J. L, Chan C. M., Tse K. T., Irene M.C.L, Cheng J. C. P. (2017): A comparative analysis of embodied carbon in high-rise buildings regarding different design parameters. Journal of Cleaner Production 161 (2017) 663e675 http://dx.doi.org/10.1016/j.jclepro.2017.05.156
Haapio A. And Viitaniemi P. (2008): Environmental effect of structural solutions and building materials to a building, Environ. Impact Assess. Rev. 28(8):587–600.
Hacker J. N., De Saulles T. P., Minson A. J., Holmes M. J. (2008): Embodied and operational carbon dioxide emissions from housing: A case study on the effects of thermal mass and climate change. Energy Build. 40(3):375- 384. doi:10.1016/j.enbuild.2007.03.005.
Harrison G. P., Maclean E. J., Karamanlis S., Ochoa L. F. (2010): Life cycle assessment of the transmission network in Great Britain. Energy Policy 38(7):3622-3631. doi:10.1016/j.enpol.2010.02.039.
Hoxha E., Habert G., Lasvaux S., Chevalier J. and Le Roy R. (2017): Influence of construction material uncertainties on residential building LCA reliability, J. Clean. Prod. 144 (2017):33–47.
Kofoworola O.F. and Gheewala S.H. (2008): Environmental life cycle assessment of a commercial office building in Thailand, Int. J. Life Cycle Assess. 13 (6) (2008):498–511.
Kurda R., Silvestre J.D., de Brito J., and Ahmed H. A. (2018): Optimizing recycled concrete containing high volume of fly ash in terms of the embodied energy and chloride ion resistance. Journal of Cleaner Production 194:735–750 DOI: 10.1016/j.jclepro.2018.05.177
Li, L. and Chen, K. (2017): Quantitative assessment of carbon dioxide emissions in construction projects: A case study in Shenzhen. J. Clean. Prod. 2017(141):394–408.
Marinković S., Radonjanin V., Malesev M., and Lukic I., Life cycle environmental impact assessment of concrete. ed. by L.; Koukkari Em: Bragança, H.; Blok, R.; Gervásio, H.; Veljkovic, M.; Plewako, Z.; Landolfo, R.; Ungureanu, V.; Silva, L.S.; Haller, P. (eds.), Sustainability of constructions – Integrated approach to life-time structural engineering. COST Action C25 (Proceedings of seminar: Dresden, 2008. Addprint AG, Possendorf, Herstellung: 2008).
Paik I. and Na S. (2019): Comparison of Carbon Dioxide Emissions of the Ordinary Reinforced Concrete Slab and the Voided Slab System During the Construction Phase: A Case Study of a Residential Building in South Korea. Sustainability 2019, 11, 3571; doi:10.3390/su11133571
Paris J. M., Roessler J. G, Ferraro C. C., DeFord H. D., and Townsend T. G. (2016): A review of waste products utilized as supplements to Portland cement in concrete’, Journal of Cleaner Production, 121 (2016):1-18
Paya-Zaforteza, I., Yepes, V., Hospitaler, A., and González-Vidosa, F. (2009): CO2-optimization of reinforced concrete frames by simulated annealing. Eng. Struct., 31(7):1501–1508.
Purnell P. (2013): The carbon footprint of reinforced concrete. Advances in Cement Research 25(6):362-368 DOI: 10.1680/adcr.13.00013
Rossi B., Marique A.-F., Reiter S. (2012): Life-cycle assessment of residential buildings in three different European locations, case study, Build. Environ. 51 (2012):402–407.
Skullestad J.L., Bohne R.A., Lohne J. (2016):High-rise timber buildings as a climate change Mitigation measure – a comparative LCA of structural system alternatives, Energy Procedia 96 (2016):112–123.
Stephan A., Jensen C.A. and Crawford R.H, (2017): Improving the life cycle energy performance of apartment units through façade design, Procedia Eng. 196 (2017):1003–1010.
Thiel C., Campion N., Landis A., Jones A., Schaefer L., Bilec M., (2013): A materials life cycle assessment of a net-zero energy building, Energies 6 (2) :1125–1141.
Villalba, P., Alcala, J., Yepes, V., and González-Vidosa, F. (2010): CO2 optimization of reinforced concrete cantilever retaining walls. 2nd Intl. Conf. Eng. Optim., Technical Univ. of Lisbon, Lisbon, Portugal.
World Business Council for Sustainable Development—International Energy Agency (WBCSD-IEA). (2009): Cement Technology Roadmap 2009: Carbon emissions reductions up to 2050, Geneva, Switzerland.
Yeo D. and Gabbai R. D. (2011): Sustainable design of reinforced concrete structures through embodied energy optimization, Energy Build. 43(8):2028–2033.
Yeo D. and Potra F. A. (2015): Sustainable Design of Reinforced Concrete Structures through CO2 Emission Optimization. J. Struct. Eng., 2015, 141(3): B4014002