In the construction industry, reinforced concrete typically employs the use of deformed reinforcement steel bars or, alternatively, welded steel mesh fabric to enhance its structural integrity. Concrete is weak in tension, and as a result, steel reinforcement is used to take up the tensile stresses that develop in the structure. This approach hinges entirely upon the inherent alkalinity of the concrete cover to protect the reinforcement against corrosion.
Special situations may necessitate the utilization of galvanized, epoxy-coated, or even stainless steel for improved protection. Recent advancements have paved the way for the development of fibre-reinforced polymer materials, yet their application in the construction industry typically predominantly focuses on external strengthening and remediation of existing damage.
Reinforcement Bars
Within the United Kingdom, the specification, procurement, and delivery of reinforcing bars are primarily governed by the BS 4449 standard. This standard encompasses steel bars possessing a yield strength of 500 MPa, categorized into three distinct ductility levels: B500A, B500B, and B500C. Hot-rolled bars intended for conventional applications, manufactured within the UK, exhibit a characteristic strength of 500 MPa and conform to either Class B or C ductility criteria. The notations for steel reinforcement bars are shown in Table 1.
Type of steel reinforcement | Notation |
Grade B500A, B500B or B500C to BS 4449 | H |
Grade B500A to BS 4449 | A |
Grade B500B or B500C to BS 4449 | B |
Grade B500C to BS 4449 | C |
A specified grade and type of ribbed stainless steel to BS 6744 | S |
Reinforcement of a type not included above but with material properties defined in the design or contract specification. | X |
These bars feature a circular cross-section, characterized by sets of parallel transverse ribs interspersed with longitudinal ribs. The nominal size denotes the diameter of a circle whose area corresponds to the bar’s effective cross-sectional area. Notably, the maximum overall size surpasses the nominal size by approximately 15%.
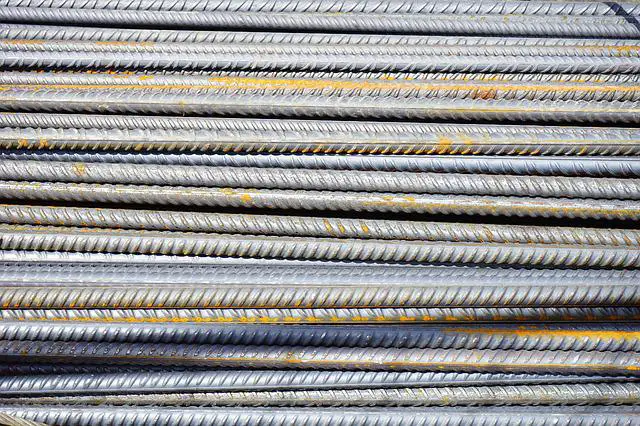
Manufacture of reinforcement bars
The production of all reinforcing bars relies upon a hot-rolling process. Under this method, a cast steel billet undergoes reheating to a temperature range of 1100°C to 1200°C, followed by subsequent rolling within a dedicated mill. This rolling sequence serves to both reduce the billet’s cross-section and imprint the desired rib pattern upon its surface. Two primary techniques exist for achieving the requisite mechanical properties within hot-rolled bars: in-line heat treatment and micro-alloying.
The in-line heat treatment approach, sometimes referred to as the quench-and-self-temper (QST) process, utilizes high-pressure water sprays to rapidly cool the bar’s surface as it exits the rolling mill. This quenching action generates a bar with a tempered outer layer offering enhanced rigidity, while preserving a softer, more ductile core. The majority of reinforcing bars employed within the United Kingdom are manufactured through this method, typically achieving either Class B or Class C ductility classifications.
Conversely, the micro-alloying technique relies upon the addition of minute quantities of alloying elements during the steel-making process itself to achieve the desired strength properties. Steel bars manufactured through this method generally attain Class C ductility. A historical approach, albeit now obsolete within the UK, involved cold-twisting the bars to achieve high-yield strength. These bars are identifiable by their characteristic spiralling longitudinal ribs and may still be seen in certain older structures.
Properties of Reinforcement Bars
The essential properties of bars to BS 4449 and wires to BS 4482, both of which are in general conformity with BS EN 10080, are given in Table 2 for a characteristic yield strength of 500 MPa.
Ductility Class | A | B | C |
Grade designation | B500A | B500B | B500C |
Characteristic tensile/yield strength ratio | 1.05 | 1.08 | 1.15 |
Characteristic total elongation at maximum force (%) | 2.5 | 5.0 | 7.5 |
It is important to note that in construction works, the preferred bar sizes are 8 mm, 10 mm, 12 mm, 16 mm, 20 mm, 25 mm, 32 mm and 40 mm. For sizes below 8 mm, the values are 1.02 for the strength ratio, and 1% for the total elongation. For bar sizes smaller than 8 mm or larger than 40 mm, the recommended sizes are 6mm and 50mm respectively. The absolute maximum permissible value for yield strength is 650 MPa and 1.35 for tensile/yield strength ratio.
Area of reinforcement based on number and spacing of steel bars
Table 3 provides the cross-sectional area of the number of reinforcement bars (mm2) for different sizes of bars (mm). This is typically used in the design of beams and columns.
Number of bars | Cross-sectional area of number of bars (mm2) for sizes of bars (mm) | ||||||||
6 | 8 | 10 | 12 | 16 | 20 | 25 | 32 | 40 | |
1 | 28 | 50 | 79 | 113 | 201 | 314 | 491 | 804 | 1257 |
2 | 57 | 101 | 157 | 226 | 402 | 628 | 982 | 1608 | 2513 |
3 | 85 | 151 | 236 | 339 | 603 | 942 | 1473 | 2413 | 3770 |
4 | 113 | 201 | 314 | 452 | 804 | 1257 | 1963 | 3217 | 5027 |
5 | 141 | 251 | 393 | 565 | 1005 | 1571 | 2454 | 4021 | 6283 |
6 | 170 | 302 | 471 | 679 | 1206 | 1885 | 2945 | 4825 | 7540 |
7 | 198 | 352 | 550 | 792 | 1407 | 2199 | 3436 | 5630 | 8796 |
8 | 226 | 402 | 628 | 905 | 1608 | 2513 | 3927 | 6434 | 10053 |
9 | 254 | 452 | 707 | 1018 | 1810 | 2827 | 4418 | 7238 | 11310 |
10 | 283 | 503 | 785 | 1131 | 2011 | 3142 | 4909 | 8042 | 12566 |
Table 4 presents precise values for the total cross-sectional area provided within a concrete section, based on the number or spacing of bars and their respective sizes. This is used in the design of slabs, walls, footings, and raft foundations.
Spacing of bars (mm) | Cross-sectional area of bars per unit width (mm2/m) for sizes of bars (mm) | ||||||||
6 | 8 | 10 | 12 | 16 | 20 | 25 | 32 | 40 | |
75 | 377 | 670 | 1047 | 1508 | 2681 | 4189 | 6545 | 10723 | 16755 |
100 | 283 | 503 | 785 | 1131 | 2011 | 3142 | 4909 | 8042 | 12566 |
125 | 226 | 402 | 628 | 905 | 1608 | 2513 | 3927 | 6434 | 10053 |
150 | 188 | 335 | 524 | 754 | 1340 | 2094 | 3272 | 5362 | 8378 |
175 | 162 | 287 | 449 | 646 | 1149 | 1795 | 2805 | 4596 | 7181 |
200 | 141 | 251 | 393 | 565 | 1005 | 1571 | 2454 | 4021 | 6283 |
225 | 223 | 349 | 503 | 894 | 1396 | 2182 | 3574 | 5585 | |
250 | 201 | 314 | 452 | 804 | 1257 | 1963 | 3217 | 5027 | |
275 | 286 | 411 | 731 | 1142 | 1785 | 2925 | 4570 | ||
300 | 262 | 377 | 670 | 1047 | 1636 | 2681 | 4189 |
Cutting and Bending Tolerances
Reinforcing bars are typically manufactured and stockpiled in standard lengths of 12 meters. Upon special request, bars of up to 18 meters in length can be procured. However, the majority of structural applications necessitate shorter bar lengths, frequently requiring bending to specific configurations.
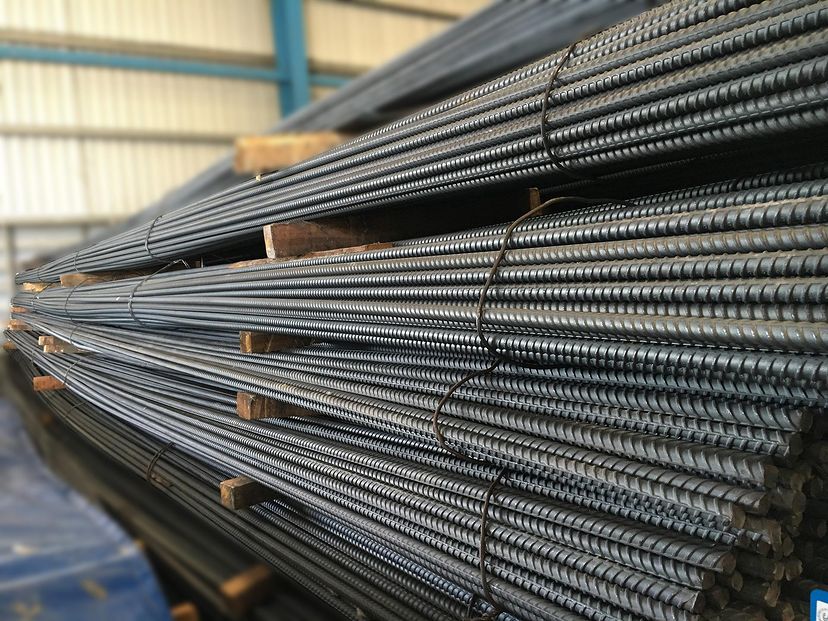
To ensure consistent and accurate fabrication, the cutting and bending of reinforcement is generally mandated to comply with the stipulations outlined in BS 8666. This standard defines the following tolerances for critical dimensions:
Cutting and Bending Process | Tolerance (mm) |
Cutting of straight lengths | ± 25 |
Bending dimension (mm) ≤ 1000 > 1000 and ≤ 2000 > 2000 | ± 5 +5, -10 +5, -25 |
Conclusion
The incorporation of steel reinforcement within a concrete matrix, an important practice in modern construction known as reinforced concrete, fosters a synergistic relationship that enhances the material’s structural performance. While concrete possesses robust compressive strength, its inherent brittleness renders it susceptible to tensile failure under applied loads.
The introduction of steel rebars, strategically positioned within the concrete, effectively mitigates this vulnerability due to their superior tensile resistance. This complementary interaction offers several key advantages to reinforced concrete structures. Notably, it significantly increases load-bearing capacity, enabling the construction of larger and more complex structures. Additionally, it enhances flexural and shear resistance, contributing to improved structural integrity and resilience.