Waste rubber tyre is a serious environmental issue that is becoming increasingly important. Currently, huge amounts of waste rubber tyres are being stockpiled (whole tyres) or landfilled (shredded tyres), with 3 billion in the EU and 1 billion in the US (Sofi, 2018). By the year 2030, the number of tyres used in automobiles is expected to exceed 1.2 billion, equating to about 5 billion waste tyres thrown away on a yearly basis.
Landfilling of tyres poses a severe environmental risk. Waste tyre disposal regions, in particular, contribute to biodiversity loss, as tyres contain hazardous and soluble components (Thomas et al, 2015). Recycling is one of the most significant waste reduction methods; nevertheless, recycling discarded tyres is especially difficult due to their high creation rates and non-biodegradability. Incorporating waste tyres as a partial substitute for coarse aggregate in the most extensively used building material, concrete, is one strategy to reduce the volume of waste tyres in the environment (Muyen et al, 2019).
In the majority of studies and research works, three general categories of waste tyre rubber are usually investigated, namely chipped, crumb, and ground rubber:
(1) Chipped Rubber:
Chipped rubber is waste tyre rubber that has been shredded or chopped to replace the gravel (coarse aggregate in concrete). Two phases of tyre shredding are required to generate this rubber. The rubber should be 300 – 430 mm long and 100–230 mm wide by the end of stage one. Cutting reduces the size to 100–150 mm in the second stage. If the shredding process is prolonged, shredded particles with a size of 13–76 mm are formed, which are referred to as “shredded particles.”
(2) Crumb Rubber:
Crumb rubber, which is used to substitute sand (fine aggregate), is made in special mills where large rubbers are broken down into smaller ripped pieces. Depending on the type of mills used and the temperature generated, different sizes of rubber particles may be produced. Particles with a high irregularity in the range of 0.425–4.75 mm are created using a simple approach.
(3) Ground Rubber:
Ground rubber that could be used to replace cement is dependent on the equipment used for the size reduction. Magnetic separation and screening are commonly performed in two steps on waste rubber tyres. In increasingly complicated techniques, different size percentages of rubber are obtained. The particles produced in the micro-milling process range in size from 0.075 to 0.475 mm.
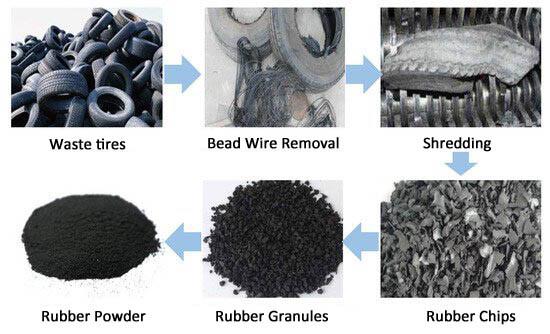
Generically, rubber aggregates are made from waste tyres using one of two methods: mechanical grinding at room temperature or cryogenic grinding below the glass transition temperature. To substitute coarse aggregates, the first process yields chipped rubber. The second process, on the other hand, frequently results in crumb rubber being used to substitute fine aggregates (Kotresh and Belachew, 2014).
Effect of Waste Rubber Tyre on the Mechanical Properties of Concrete
The inclusion of tyre rubber particles in concrete has been proven to affect the performance of concrete in both positive and negative ways, according to research. According to some research works cited by Sofi (2018), waste rubber tyre in concrete is especially recommended for concrete constructions located in locations with a high risk of earthquakes, as well as applications subjected to high dynamic forces, such as railway sleepers. One of the most significant disadvantages of employing tyre rubber in concrete is that it has a significantly lower mechanical performance than normal concrete.
According to Muyen et al. (2019), a 5% replacement of conventional aggregates with waste tyre chips leads to a 5% loss in compressive strength, a 10% replacement results in a 26% drop, and a 15% replacement results in a 47% reduction in compressive strength. As a result, when waste tyre rubber aggregates are utilized in concrete production, a reduction in compressive strength is predicted. This is consistent with the findings of Ganjian et al (2009) and Su et al (2014).
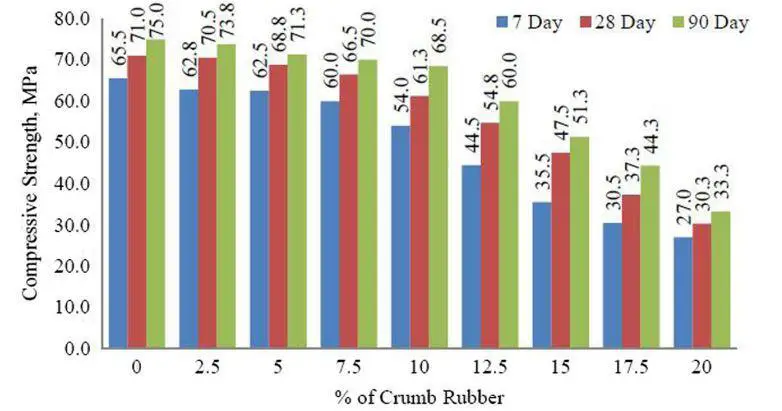
On the other hand, when 20% fine aggregate was replaced with rubber aggregate, Su et al. (2015) observed a 12.8%drop in the flexural strength. When the rubber particles were smaller, there was less loss of strength. The tensile strength of concrete reduces with increase in the percentage of rubber replacement in concrete. The tensile strength of concrete containing chipped rubber (replacement for aggregates) is lower than that of concrete containing powdered rubber (for cement replacement) (Sofi, 2018).
Rubberized concrete’s strength and elastic modulus were found to be significantly reduced, according to researchers (Zheng et al, 2008; Elchalakani, 2015). The decreased stiffness (5 MPa) of the rubber, the uneven distribution of the rubber aggregate due to its lightweight, and the poor bonding between the rubber aggregate and the cement paste have all been blamed for the reduced mechanical performance (Panda et al, 2012).
Chipped rubber causes larger strength losses than crumb rubber, according to several researchers (Khatib and Bayomy, 1999; Topçu and Avcular, 1997). The lowering of stress and strain concentrations in the concrete, according to Huang et al. (2013), is what causes the strength improvement when smaller sizes are employed.
Li et al. (2011) investigated the effects of tyre rubber content and rubber particle size on the mechanical performance of concrete. High rubber content and smaller tyre rubber aggregate size were shown to reduce rubberised concrete’s compressive strength and static young’s modulus. The final strain of the rubberised concrete, on the other hand, increased as the rubber content and particle size reduced.
The explanations for the rubberized concrete’s decreased compressive and flexural strength (Ganjian et al, 2009);
(a) The aggregate in the concrete mix would be surrounded by the cement paste containing rubber particles. This leads to a cement paste that will be softer compared to cement paste without rubber particles. When loaded, there will be rapid development of cracks around the rubber particles and this leads to quick failure of specimens.
(b) There will be no proper bonding between rubber particles and cement paste, as compared to cement paste and natural aggregate. This can lead to cracks due to non-uniform distribution of applied stresses.
(c) The compressive strength depends on the physical and mechanical properties of the constituent materials. If part of the materials is replaced by rubber, a reduction in strength will occur.
(d) Due to the low specific gravity of rubber and lack of bonding of rubber with other concrete ingredients, there is a tendency for rubber to move upwards during vibration leading to higher rubber concentration at the top layer. Such a non-homogeneous concrete sample leads to reduced strengths.
Summarily, when tyre rubber aggregate content and rubber aggregate size increased, the mechanical properties of concrete reduced. Different studies by several researchers corroborated these findings. As a result, most studies recommend a maximum rubber content of no more than 20% total aggregate volume and a size no larger than crumb rubber size in terms of rubber content and size. The soft rubber was thought to act as air gaps inside the concrete matrix, providing minimal resistance to loads and causing the particles to become weak spots within the concrete matrix.
References
[1] Elchalakani M. (2015): High strength rubberized concrete containing silica fume for the construction of sustainable road side barriers, Structures (1):20–38
[2] Ganjian E, Morteza K, Ali AM. (2009): Scrap-tire-rubber replacement for aggregate and filler in concrete. Constr Build Mater 2009(23):1828–36.
[3] Khatib Z. K., Bayomy F. M. (1999): Rubberized Portland Cement Concrete, J. Mater. Civ. Eng., 11(3):206–213
[4] Kotresh K.M., and Mesfin G. B. (2014): Study on Waste Tyre Rubber as Concrete Aggregates. International Journal of Scientific Engineering and Technology 3(4): 433-436
[5] Li L. J., Xie W. F., Liu F., Guo Y. C., Deng J. (2011): Fire performance of high-strength concrete reinforced with recycled rubber particles, Mag. Concr. Res., 63(3):187–195
[6] Muyen Z., Mahmud F., and Hoque M. N. (2019): Application of waste tyre rubber chips as coarse aggregate in concrete. Progressive Agriculture 30 (3): 328-334
[7] Panda K. C., Parhi P. S., Jena T. (2012): Scrap-Tyre Rubber Replacement for Aggregate in Cement Concrete: Experimental Study, Int. J. Earth Sci. Eng., 5(6):1692–1701
[8] Sofi A. (2018): Effect of waste tyre rubber on mechanical and durability properties of concrete – A review. Shams Engineering Journal 9 (2018):2691–2700 https://doi.org/10.1016/j.asej.2017.08.007
[9] Su H, Yang J, Ling TC, Ghataora GS, Dirar S. (2015): Properties of concrete prepared with waste tyre rubber particles of uniform and varying sizes. J. Clean. Prod. 2015(91):288–96.
[10] Thomas BS, Gupta RC, Mehra P, Kumar S. (2015): Performance of high strength rubberized concrete in aggressive environment. Constr. Build. Mater. 2015(83):320–6.
[11] Topçu I. B., Avcular N. (1997): Analysis of rubberized concrete as a composite material, Cem. Concr. Res., 27(8):1135–1139
[12] Zheng L., Huo X. S., Yuan Y. (2008): Strength, Modulus of Elasticity, and Brittleness Index of Rubberised Concrete, J. Mater. Civ. Eng., 20, 11 (2008)
In this type of concrete (rapper chips)
The disadvantage of concrete low resistance of fire ?
Hi there, I simply couldn’t leave your website without saying that I appreciate the information you supply to your visitors. .