Generically, cement is an inorganic fine powder that when mixed with water undergoes hydration reaction, and forms a paste which becomes the binder that holds aggregates together in concrete. The raw materials from which cement is made are lime, silica, alumina, and iron oxide.
These constituents are crushed and blended in the correct proportions and burnt in a rotary kiln. The resulting product is called clinker. The cooled clinker can be mixed with gypsum and various additional constituents and ground to a fine powder in order to produce different types of cement. The main chemical compounds in cement are calcium silicates and aluminates.
Hydraulic cements set and harden by reacting chemically with water in a process known as hydration reaction. During this reaction, cement combines with water to form a stonelike mass, called paste. When the paste (cement and water) is added to aggregates (sand and gravel, crushed stone, or other granular material) it acts as an adhesive and binds the aggregates together to form concrete, the world’s most versatile and most widely used construction material.
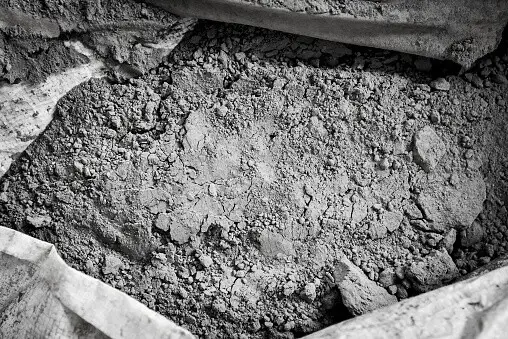
The European standard for cements is BS EN 197-1:2011 Cement –Part 1: Composition, specifications, and conformity criteria for common cements. The Standard defines and gives the specifications of 27 distinct common cements, 7 sulfate resisting common cements, as well as 3 distinct low early strength blast furnace cements and 2 sulfate resisting low early strength blast furnace cements and their constituents.
Standard Designation of Cements
CEM cement designation includes the following information:
i. Cement type (CEM I – CEM V)
ii. Strength class (32.5-52.5)
iii. Indication of early strength
iv. Additional designation SR for sulfate resisting cement
v. Additional designation LH for low heat cement
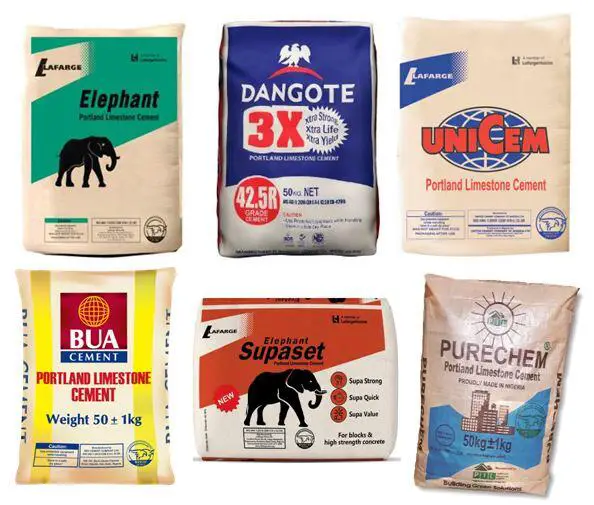
Types of Cements
All types of cement are grouped into five major groups, all of which are mixtures of different proportions of clinker and another major constituent. The five groups are:
- CEM I – Portland cement: This comprises mainly ground clinker and up to 5% of minor additional constituents.
- CEM II – Portland composite cement: This comprises of seven types which contain clinker and up to 35% of another single constituent.
i. Portland slag cement (CEM II/A-S and CEM II/B-S): This comprises of clinker and blast furnace slag which originates from the rapid cooling of slag obtained by smelting iron ore in a blast furnace. The percentage of the slag varies between 6 and 35%.
ii. Portland silica fume cement (CEM II/A-D): This comprises of clinker and silica fume which originates from the reduction of high purity quartz with coal in an electric arc furnace in the production of silicon and ferrosilicon alloys.
iii. Portland-Pozzolana cement (CEM II/A-P, CEM II/B-P, CEM II/A-Q, CEM II/B-Q): This comprises clinker and natural pozzolana such as volcanic ashes or sedimentary rocks with suitable chemical and mineralogical composition or Natural calcined pozzolana such as materials of volcanic origin, clays, shales or sedimentary rocks activated by thermal treatment.
iv. Portland-fly ash cement (CEM II/A-V, CEM II/B-V, CEM II/A-W, CEM II/B-W): This mixture of clinker and fly ash dust-like particles precipitated from the flue gases from furnaces fired with pulverised coal.
v. Portland burnt shale cement (CEM II/A-T, CEM II/B-T): This consists of clinker and burnt shale, specifically oil shale burnt in a special kiln at 800 °C.
vi. Portland-limestone cement (CEM II/A-L, CEM II/B-L, CEM II/A-LL, CEM II/B-LL).
vii. Portland-composite cement (CEM II/A-M, CEM II/B-M). - CEM III – blast furnace cement (CEM III/A, CEM III/B, CEM III/C): This comprises clinker and a higher percentage (36-95%) of blast furnace slag than that in CEM II/A-S and CEM II/B-S.
- CEM IV – pozzolanic cement (CEM IV/A, CEM IV/B): This comprises of clinker and a mixture of silica fume, pozzolanas and fly ash.
- CEM V – composite cement (CEM V/A, CEM V/B): This comprises clinker and a higher percentage of blast furnace slag and pozzolana or fly ash.
The clinker contents in different types of cements are given in Table 1. The letters A, B and C designate respectively higher, medium and lower proportion of clinker in the final mixture. However, the percentage of clinker with the designations A, B, C can be different in different types of cement as shown in Table 1.
Cement Type | Clinker Content – A | Clinker Content – B | Clinker Content – C |
CEM II | 80-94% | 65-79% | – |
CEM III | 35-64% | 20-34% | 5-19% |
CEM IV | 65-89% | 45-64% | – |
CEM V | 40-64% | 20-38% | – |
The second constituent in cement in addition to clinker is designated by the second letter as follows:
S = blast furnace slag
D = silica fume
P = natural pozzolana
Q = natural calcined pozzolana
V = siliceous fly ash
W = calcareous fly ash (e.g., high lime content fly ash)
L or LL = limestone
T = burnt shale
M = combination of two or more of the above components
Strength Class of Cement
The standard strength of a cement is the compressive strength determined in accordance with EN 196-1 at 28 days and shall conform to the requirements in Table 3 of EN197-1. The three standard classes of cement strength are;
- class 32.5
- class 42.5, and
- class 52.5
Strength Class | 28 days Compressive strength (MPa) | Initial setting time (mins) |
32.5 N | ≥ 32.5, ≤ 52.5 | ≥ 75 |
32.5 R | ≥ 32.5, ≤ 52.5 | ≥ 75 |
42.5 N | ≥ 42.5, ≤ 62.5 | ≥ 60 |
42.5 R | ≥ 42.5, ≤ 62.5 | ≥ 60 |
52.5 N | ≥ 52.5 | ≥ 45 |
52.5 R | ≥ 52.5 | ≥ 45 |
Sulfate-Resisting Cement
Sulfate resisting cements are used particularly in foundations where the presence of sulfates in the soil which can attack ordinary cements. The sulfate resisting cements have the designation SR and they are produced by controlling the amount of tricalcium aluminate (C3A) in the clinker. The available types are:
- i. Sulfate resisting Portland cements CEM I-SR0, CEM I-SR3, CEM I-SR5 which have the percentage of tricalcium aluminate in the clinker less than or equal to 0, 3 and 5% respectively
- ii. Sulfate resisting blast furnace cements CEM III/B-SR, CEM III/C-SR (no need for control of C3A content in the clinker).
- iii. Sulphate resisting pozzolanic cements CEM IV/A-SR, CEM IV/B-SR (C3A content in the clinker should be less than 9%).
Low Early Strength Cement
These are CEM III blast furnace cements. Three classes of early strength are available with the designations N, R and L respectively signifying normal, ordinary, high and low early strength.
Examples of Cement Designation
- CEM II/A-S 42.5 N
This indicates Portland composite cement (indicated by CEM II), with high proportion of clinker (indicated by letter A) and the second constituent is slag (indicated by letter S) and the strength class is 42.5 MPa (indicating that the characteristic strength at 28 days is a minimum of 42.5 MPa) and it gains normal early strength (indicated by letter N). - CEM III/B 32.5 N
This indicates blast furnace cement (indicated by CEM III); with medium proportion of clinker (indicated by letter B) and the strength class is 32.5 MPa (indicating that the characteristic strength at 28 days is a minimum of 32.5 MPa) and it gains normal early strength (indicated by letter N).
- CEM I 42.5 R-SR3
This indicates Portland cement (indicated by CEM I), the strength class is 42.5 MPa (indicating that the characteristic strength at 28 days is a minimum of 42.5 MPa) and it gains high early strength (indicated by letter R) and is sulfate resisting with C3A content in the clinker less than 3%. - CEM III-C 32.5 L – LH/SR
This indicates blast furnace cement (indicated by CEM III), the strength class is 32.5 MPa (indicating that the characteristic strength at 28 days is a minimum of 32.5 MPa) and it gains low early strength (indicated by letter L) and is sulfate resisting (indicated by letters SR) and is of low heat of hydration (indicated by LH).
Common Types of Cements
Of different types of cement, the most common ones are mainly six:
i. CEM I
ii. CEM II/B-S (containing 65-79% of clinker and 21-35% of blast furnace slag)
iii. CEM II/B-V (containing 65-79% of clinker and 21-35% of siliceous fly ash)
iv. CEM II/A-LL (containing 80-94% of clinker and 6-20% of limestone)
v. CEM III/A (containing 35-64% of clinker and 36-65% of other constituents)
vi. CEM III/B (containing 20-34% of clinker and 66-80% of other constituents)