Jacketing of reinforced concrete columns is normally done to reduce the lateral deformation of columns, and ultimately increase the strength and load-carrying capacity of the column. This activity is usually carried out on columns that are failing as a result of overload, material deterioration, poor maintenance, inadequate construction practices, etc. Furthermore, when the load-carrying capacity of a column is to be increased as a result of construction modification or change of usage of the building, jacketing of the column can also be done.
Materials such as concrete, steel, or laminates made of a fibre-reinforced polymer may be used for column jacketing, and as the stiffness of the jacket in the transverse direction increases, the resistance to lateral deformation of the column increases.
A column member is in a state of uniaxial deformation if the lateral expansion is totally restrained, i.e., if no lateral deformation is permitted to occur. Columns subjected to uniaxial compression fail as a result of lateral tensile strains caused by the Poisson effect, which causes lateral expansion (Abdelrahman, 2023).
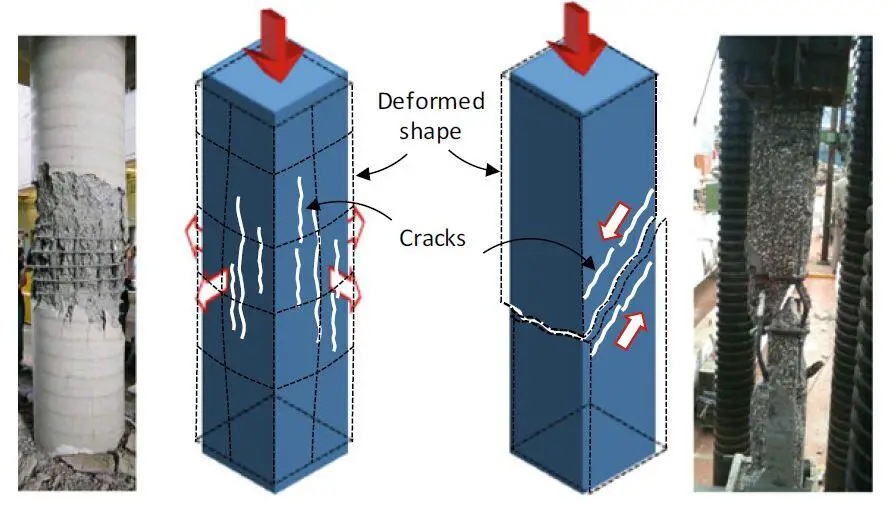
The Poisson effect is the term used to describe a material’s expansion or contraction in directions perpendicular to the direction of loading. If lateral expansion occurs freely, the member is under uniaxial stress, and tensile-splitting cracks parallel to the direction of loadings are the resultant cracks. Typically, uniaxially loaded columns with low or normal compressive strengths exhibit this form of failure.
However, since the stiffness of jackets can never be infinite, it is impractical to achieve a uniaxial stress state in jacketed columns. As a result, the triaxial stress state and deformation are always present in jacketed columns.
High tensile stresses are induced in the jacket as its stiffness increases, and vice versa, the original column section experiences high confining pressure and hence experiences less lateral displacement. It should be noted that as the cracking of concrete increases, the concrete Poisson ratio increases as well, allowing for greater confinement before failure.
The Behaviour of Jacketed Square Columns
When a square column is jacketed, the jacket is subjected to high internal pressure, causing tensile stresses in the transverse direction of the column jacket. Different deformations are seen along the jacket wall, as illustrated in Figure 2b, indicating that the distribution of confining stresses is not uniform (Abdelrahman, 2023).
The tensile stress causes elongation of the jacket at the corners; however, extra flexural deformation is also seen at the mid-wall width (δsquare in Fig. 2b); as a result, the confining effect is diminished in the mid-wall zones. As the dimensions of the square column increase, less confinement is developed at the mid-wall width and the overall confinement of the column decreases.
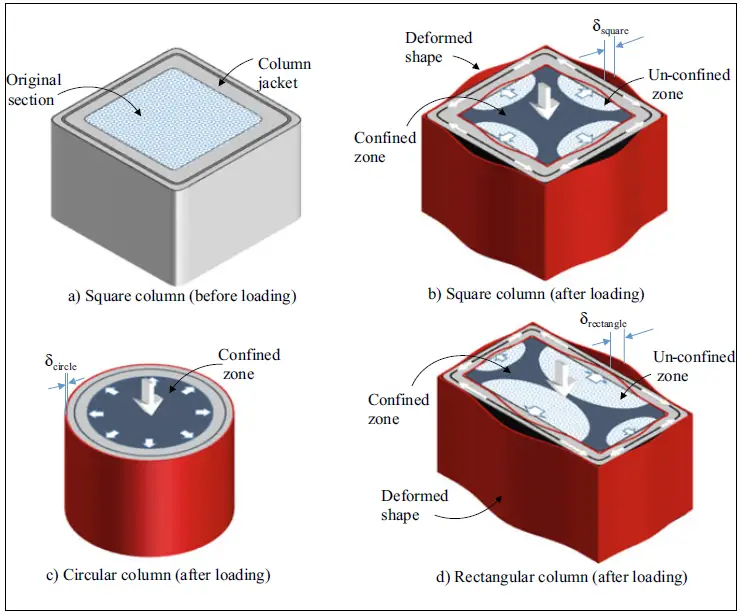
However, as seen in Figure 2d, jacketing does not properly confine rectangular columns, especially those with a large aspect ratio. This is mostly caused by the initial column section expanding, which causes a significant outward distortion of the long side of the column (the δrectangle in Figure 2d).
The behaviour of Jacketed Circular Columns
When jacketing is applied to circular columns, uniform internal pressure develops in the jacket, producing uniform tension and equal lateral displacement in the jacket wall. In this instance, the original concrete section is confined as shown in Figure 2c, and the maximum benefit of the jacket is achieved since it undergoes minimal deformation (see the δcircle in Figure 2c).
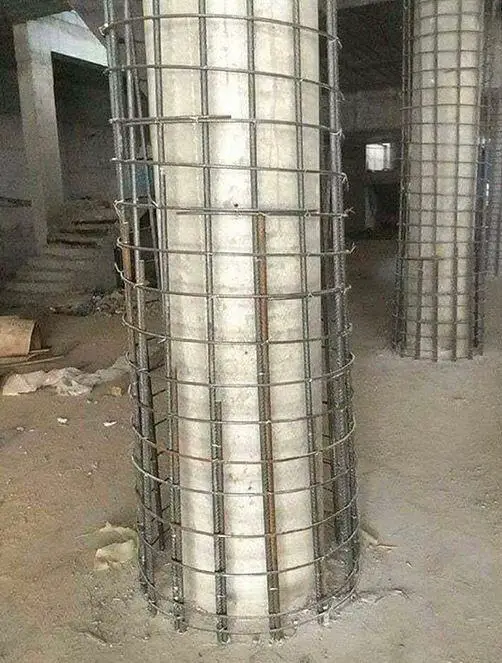
Jacketing with Reinforced Concrete
Reinforced conncrete jacketing can be applied to columns by increasing the size of the column and adding more longitudinal and transverse steel reinforcement. The essential factor in determining whether the concrete strengthening operation is successful is the composite action between the old and new concrete.
Concrete jackets are used to increase the axial-moment capacity, shear capacity, or stiffness of columns. The lateral deformation of a building can be improved by making the columns stiffer, but this will also result in higher straining actions because of the increased lateral load demand. Concrete jackets can also be used to fix the buckling issues of slender columns.
The use of concrete jacketing in the strengthening of RC columns has its drawbacks, despite being a very popular alternative. For instance, it is adverse to architects and building owners since the size of the finished concrete section after restoration increases and the amount of open space in the building decreases.
Care should be used when applying the jacket because it necessitates extensive drilling into the original column section, which may already be weak, as well as in the slabs/beams and footings. The procedure of applying concrete jackets takes time, and accuracy is necessary when casting the concrete monolithically, especially for the upper portions of the jackets.
The strength of the repaired column member following the addition of the concrete jacket mostly depends on the strength of the jacket as well as the increased strength of the original member following the jacket’s confinement (Abdelrahman, 2023). As a result, it is ideal to have the jacket on all four sides of the column; however, this is not always possible, especially for the columns that are located at the edge or corners of structures.
Procedure for the Construction of Concrete Jacket
The following steps can be adopted in the construction of column jacketing;
(1) Since the column capacity is greatly reduced during the application of the jacket, propping of the slabs surrounding the column and the slabs at other floors must be provided to establish an alternative load path to the foundations.
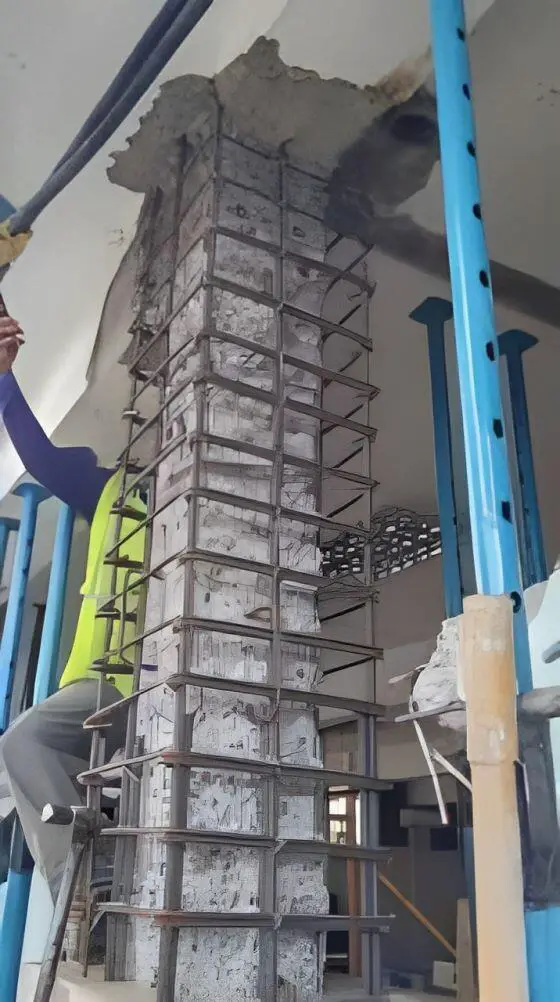
(2) If there is no steel corrosion, the concrete cover is removed until sound concrete is reached in the original section. Since pneumatic hammering may cause the substrate to micro-crack, sandblasting is advised to roughen the concrete surface. If the original section’s reinforcement has corroded, the concrete cover should be completely removed so that the longitudinal steel bars are visible. If the level of corrosion is severe, the steel bars are cleaned, painted with anticorrosion paint, or replaced with new steel bars.
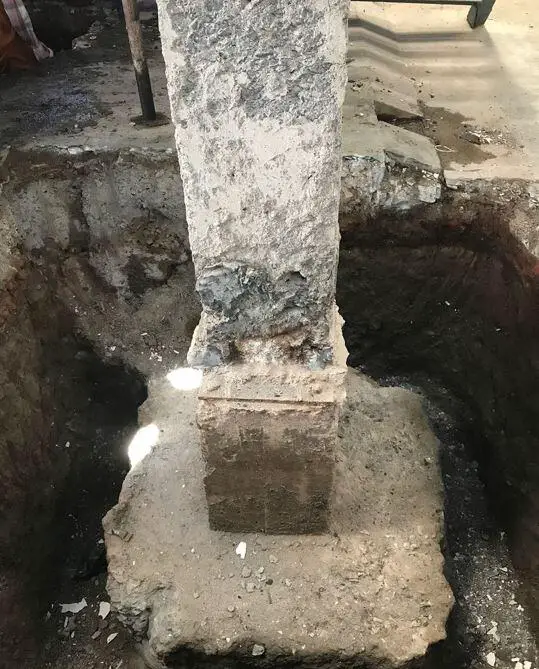
(3) To mechanically join the new concrete portion to the old concrete section, steel dowels are placed along the column all around the cross-section. The foundation must receive the longitudinal steel bars of the jacket, and holes in the slabs must be constructed to allow the longitudinal bars to pass the floor slabs.
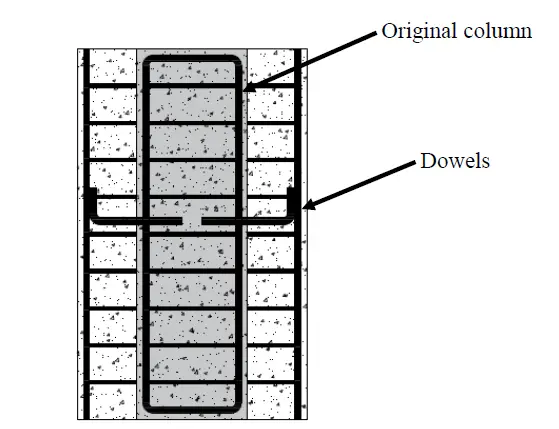
(4) The specified longitudinal and transverse steel reinforcement for the jacket is set in place, and it is advised that the steel dowels that were planted be fastened to the longitudinal bars. The hooks will stop the longitudinal steel bars from early buckling and improve the confinement level of the column cross-section.
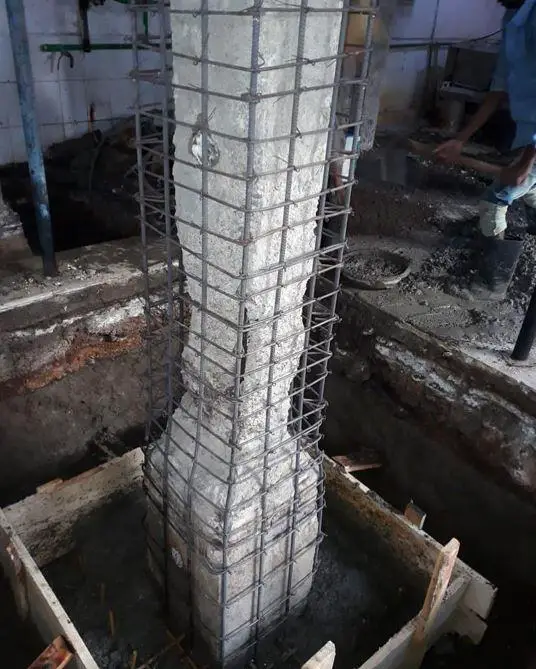
(5) The jacket should be cast using a material that is compatible with the original concrete section’s properties. In order to reduce the strain on the steel dowels and the likelihood of fresh concrete cracking, the shrinkage of the jacket material should be kept to a minimum. If the original column has been provided with both dowels and surface roughening, monolithic behaviour—where there is no separation at the joint between the old and new concrete—can be anticipated.
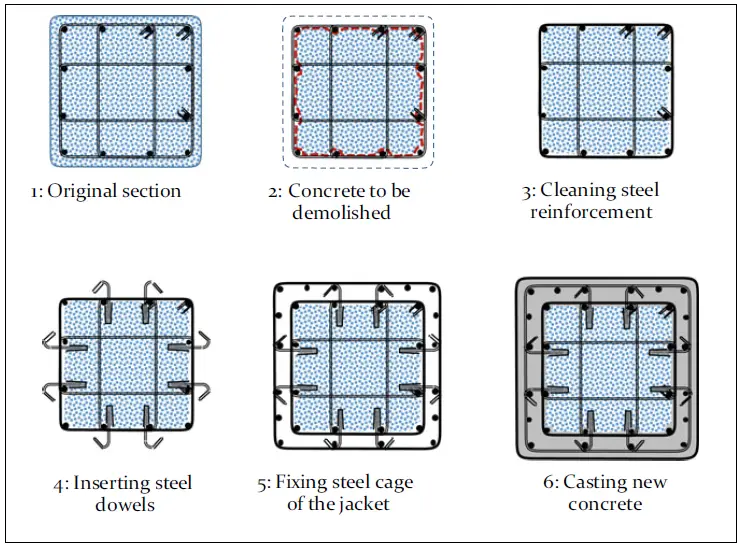
Material Specifications for Concrete Jacketing
The design mix used to cast the concrete jacket should have physical properties that are comparable to or compatible with those of the concrete used in the original section. Compressive strength, elastic modulus, coefficient of thermal expansion, and creep are some of these properties. Unless it can be demonstrated through testing that similar physical properties are attainable, the type of aggregate used in the mix should be comparable to that of the original concrete.
If the properties of the two materials differ, a vertical separation between the original section and the jacket can be anticipated over time. In this regard, grout or mortar used in the jacket shouldn’t have long-term behaviour that differs from that of concrete. The tensile properties of the jacket may be improved by adding fibres or shrinkage-compensating material to the mixture.
Prior to casting, a bonding agent may be applied to the old concrete as long as the manufacturer’s material specifications are rigorously followed. In order to prevent honeycombs or voids from appearing in the jacket, it is recommended to utilize the form-and-pump approach during concreting.
Reference
Abdelrahman A. (2023): Strengthening of Concrete Structures, Springer https://doi.org/10.1007/978-981-19-8076-3_1
Dear Sir/Madam,
I do have a question to ask. The Column Jacking process goes all the way to the Column Matting in the ground?
I have a few of those to repair on my property any advise and help would be greatly appreciated.