Filigran slab (also called filigree slab) is a universal system of composite reinforced concrete slab, that is used all over the world. This is due to their excellent structural solutions in the prefabricated construction method adapted to industrial, residential, and other special structures, such as bridges. Filigran slabs are prefabricated in the factory and are made up of thin reinforced concrete slabs, which are part of the complete reinforced concrete floor, and have a thickness between 40 and 75 mm.
The precast concrete panel in a filigree slab usually has a steel lattice girder system embedded within it. This lattice, typically formed from welded steel wire mesh or prefabricated trusses, acts as both a structural reinforcement and a void former. The voids can be filled with various lightweight materials like polystyrene blocks, clay pots, or even air, depending on the desired weight, thermal, and acoustic properties of the final slab.
The precast base incorporates bottom reinforcement, typically in the form of welded mesh or rebar cages. Once delivered to the construction site, the filigree slabs are erected on temporary supports. Additional top reinforcement is then placed on the slabs, followed by a concrete topping pour. This final layer creates a composite action with the precast element, resulting in a robust and efficient floor system.
See a picture of a filigree slab panel below;
Technical Specifications of Filigree Slabs
Due to transportation (the maximum permissible width of a moving vehicle during transportation), the recommended width is between 0.60m to 2.50m. The maximum recommended width of each precast panel is 2.70m, and the length may be as high as 12.00m.
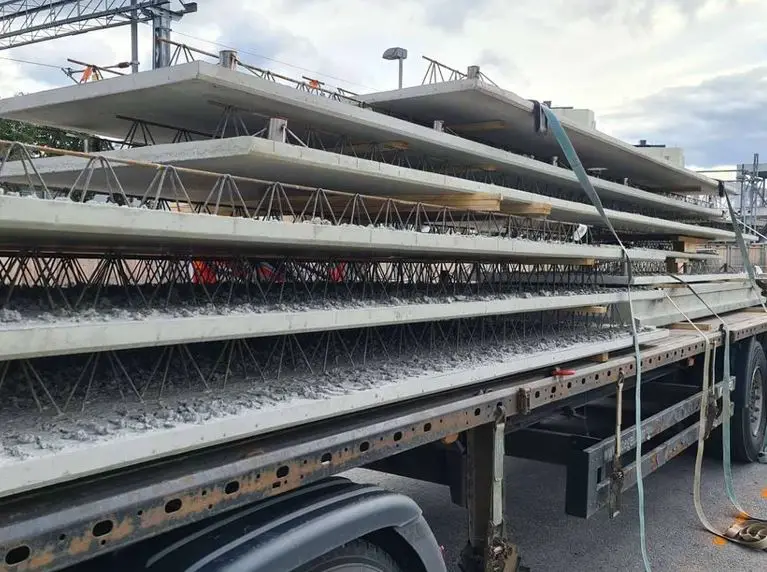
Each filigran slab has main reinforcements in the transverse and longitudinal directions (based on applied loading and design), and lattice girder trusses spaced at not more than 750mm and placed parallel to the longer side. After they are cast and installed, the final in-situ concrete topping (not less than 120mm) is used to finish the slab to the required final design thickness.
During the industrial fabrication of precast filigran slabs, all recesses, ceiling apertures, electrical sockets etc are taken into account. The prefabricated slab acts as a shuttering (soffit formwork) during the building phase, and after the addition and hardening of the in-situ concrete, the whole system effectively becomes a single slab.
A typical complete arrangement of a filigran slab is shown in the picture below;
Where;
(1) In-situ concrete topping/overlay
(2) Prefabricated plate
(3) Panel joint reinforcement
(4) Lattice girder trusses
See typical arrangement of reinforcements and lattice girder trusses for filigree slabs below.
In-situ Concrete Topping/Overlay
The fusion of the two layers of the concrete, (precast and monolithic cast in-situ) is done after the precast filigree slabs are installed in place. The surface of the prefabricated panels should be made rough so as to facilitate adequate bonding with the cast in-situ slab.
The steel trusses included in the panels are suitable motherboard for rigidity during lifting, transportation, and performance of the floor. The diagonals of the lattice truss girder serve to accept the thrust in the joint between the precast panel and the in-situ concrete, while the upper booms and diagonals serve to provide the stiffness necessary during assembly.
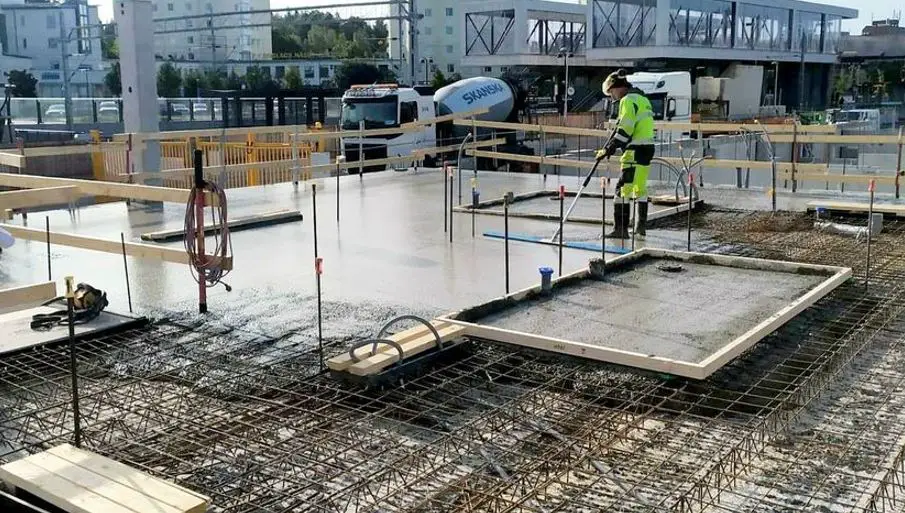
Work Placement of Filigran Slab
Filigree slab panels are transported to the building in accordance with draft assembly drawings. Project cost and transport cost are included in the total cost of the floor. Before installation, there is a need to prepare a support/mounting place, to place them in the required panel, and the designed level.
The necessary supports (props, joints) are indicated by the designer. The permissible moments and lateral forces are independent of the girder diameters and the assembly height of the lattice girders.
The thickness of the precast slab and the diagonal diameter of the lattice girders determine the bending capacity as well as the lateral load capacity. In addition to the net weight of the ceiling, assembly loads of 1.5 kN/m2 or 1.5 kN (under the most unfavourable conditions) are taken into account.
Unloading Filigree Slab
Filigree slab panels are generally unloaded from the truck by a building site crane. The slab weighs approximately 125 kg/m2 (standard thickness). The karabiners are hooked into the diagonals of the truss lattice girder, not into the upper boom. Stabilizing suspension gear should be used while lifting the filigree slab.
The stabilizing suspension gear of steel cables or chains should be used to guarantee equally distributed loading of the dead weight on the lattice girders. In either case, the spacing of the suspension gear from the end of the lattice slab should be approximately 1/5 of the total length of the slab.
Reinforcing across the joints
Joint reinforcement between the slabs is guaranteed either in the form of reinforcing steel mesh or individual reinforcing rods. The dimensions of the reinforcing rods are stated in the installation plan. The joint reinforcement must go beyond the butt of the plates by at least 500 mm in the installation plan. The reinforcement prevents dowelling or uneven deformation of the individual pieces of the ceiling.
Preparation for concreting
Before the in-situ concrete is added, the following must be checked whether:
1. The slab has been laid properly. It is imperative to note that the main reinforcements are parallel to the long span in the panel, but during placement, they are placed parallel to the short span.
2. The precast slabs are supported and should be lying horizontally.
3. The edges of the slab are completely level along the entire length of the joints on the underside.
4. The reinforcement over the joints, the additional top reinforcement bars as well as services have been laid.
Design Considerations for Filigree Slabs
While offering numerous advantages, filigree slabs require careful design considerations:
- Span Limitations: The precast elements have inherent limitations in terms of achievable spans compared to solid post-tensioned slabs.
- Load Capacity: The design needs to account for the dead load of the precast element, superimposed dead loads (partitions, finishes), live loads (occupancy), and any additional loads.
- Deflection Control: The design must ensure that the deflections of the completed floor system stay within acceptable limits to prevent serviceability issues.
- Fire Resistance Requirements: The choice of precast concrete strength, void fillers, and top concrete thickness needs to meet the building’s fire resistance rating.
- Service Integration: The layout of voids must be carefully planned to accommodate necessary building services without compromising structural integrity.
- Transportation and Handling: The weight and dimensions of precast elements need to comply with transportation regulations and on-site handling limitations.
Advantages of Filigree Slab
Filigree slabs offer a multitude of benefits compared to traditional cast-in-place concrete slabs or other precast options:
1. High accuracy and smoothness of the floor eliminate the need for plastering.
2. The strength of plates adapts to the individual changes, in accordance with the terms of use of the ceiling.
3. The production of the plate for the construction requires minimum formwork.
4. Simple and short construction period
5. Reduction in the number of workers needed for the preparation of the floor.
6. Filigran slab saves materials costs and labour charges for scaffolding and formwork.
7. Filigree slabs are lightweight and easy to handle and fix.
8. Recesses for electrical and plumbing installations are made at the pre-production stage itself.
Like our Facebook page on www.facebook.com/structville
• Hey there! Someone in my Facebook group shared this site with us so I came to look it over. I’m definitely loving the information. I’m bookmarking and will be tweeting this to my followers! Fantastic blog and outstanding design.
MEP F modelling
COBie adaptation
BIM documentation in India
BIM Consulting in India
cad services in India
BIM Solutions in India
Hey, do you have a document that can help me understand the design methods for the filigree slabs?
Like what considerations are to be made and a typical design philosophy.
Thank you