Structural steel is a major material in modern construction that offers exceptional strength, versatility, and cost-effectiveness. However, its susceptibility to corrosion can present a significant challenge to structural engineers and asset managers. Corrosion in steel structures is not only an aesthetic issue, but can impact the structures’ stability, longevity, and safety. The deterioration of steel, often termed corrosion, can be primarily understood as an electrochemical process that occurs sequentially in the presence of water and oxygen.
The initial phase involves the targeted degradation of specific surface regions, known as anodes. At these anodic sites, ferrous ions dissolve and are released into the surrounding environment. Simultaneously, electrons depart from the anode and travel through the metallic structure to adjoining cathodic locations on the surface. At these cathodic sites, the electrons interact with oxygen and water, forming hydroxyl ions.
Subsequently, these hydroxyl ions react with the ferrous ions originating from the anode to produce ferrous hydroxide. Finally, this ferrous hydroxide undergoes further oxidation in the presence of air, ultimately transforming into hydrated ferric oxide, commonly recognized as red rust.
The following equation describes the sum of these reactions:
4Fe + 3O2 + 2H2O = 2Fe2O3H2O
(iron/steel) + (oxygen) + (water) = rust
Two critical observations can therefore be drawn regarding steel corrosion:
- The deterioration of iron or steel, known as corrosion, necessitates the concurrent presence of both water and oxygen. In the absence of either element, corrosion ceases to occur.
- The entirety of the corrosion process transpires at the anode; the cathode experiences no corrosion.
However, with time, polarization effects come into play. These effects, such as the accumulation of corrosion products on the surface, hinder the continuation of the corrosion process. Subsequently, new and reactive anodic sites may form, permitting further corrosion to take place. Over extended periods, the loss of metal becomes relatively uniform across the surface, leading to a phenomenon typically described as general corrosion.
Different Forms of Steel Corrosion
Steel corrosion manifests itself in various forms, each posing unique challenges:
- Uniform Corrosion: This most common form involves the gradual, near-uniform deterioration of the entire exposed steel surface. While seemingly less damaging initially, it can significantly reduce the load-bearing capacity of a structure over time.
- Pitting Corrosion: This localized attack creates deep, often invisible pits that compromise structural integrity disproportionately to the overall material loss. It is particularly problematic due to its rapid progression and difficulty in detection.
- Galvanic Corrosion: This occurs when two dissimilar metals, like steel and copper, are in electrical contact in a corrosive environment. The more “noble” metal (copper) acts as the cathode, accelerating the corrosion of the less noble metal (steel).
- Crevice Corrosion: This localized attack occurs in confined spaces between the steel surface and another material, such as a gasket or sealant. The stagnant electrolyte within this crevice promotes a highly corrosive environment.
- Stress Corrosion Cracking (SCC): This form combines the effects of tensile stress and a corrosive environment, leading to the rapid propagation of cracks within the steel.
Rate of Steel Corrosion
The primary factors influencing the rate of steel corrosion in atmospheric environments can be categorized as follows:
(1) Wetness Duration: This metric refers to the proportional time during which the steel surface remains wet due to factors such as precipitation or condensation. Consequently, unprotected steel in arid environments, exemplified by heated buildings, experiences minimal corrosion owing to the limited availability of water.
(2) Atmospheric Contaminants: The type and concentration of airborne pollutants and contaminants, including sulfur dioxide, chlorides, and dust particles, significantly impact corrosion rates.
(3) Sulfates: These originate from sulfur dioxide gas, a byproduct of fossil fuel combustion (e.g., sulfur-laden coal and oil). Sulfur dioxide reacts with atmospheric moisture to form sulfuric and sulfurous acids. Industrial environments are particularly susceptible to high sulfur dioxide concentrations.
(4) Chlorides: Primarily found in marine environments, chlorides reach peak concentrations in coastal regions, exhibiting a rapid decline further inland. However, the presence of de-icing salts used on roadways can introduce chlorides into non-coastal environments.
It is noteworthy that within a specific geographic location, corrosion rates can exhibit significant variability due to the sheltering effects of structures and prevailing wind patterns. Therefore, for practical purposes, the immediate “microclimate” surrounding the steel structure dictates its corrosion rate.
This section explores the corrosion rates of steel in a range of United Kingdom environments, expressed in micrometres per year (μm/year). Note: 1 μm (micrometre) is equivalent to 0.001 mm (millimetre).
- Rural Atmospheric: Unobstructed, inland environments with minimal pollution generally exhibit low steel corrosion rates, typically below 50 μm/year.
- Industrial Atmospheric: Inland environments characterized by air pollution experience moderate corrosion rates, typically ranging from 40 to 80 μm/year, with variations influenced by sulfur dioxide (SO2) levels.
- Marine Atmospheric: Within the UK, a broad 2-kilometre coastal strip is considered a marine environment. Steel corrosion rates in this zone typically fall between 50 and 100 μm/year, heavily influenced by proximity to the seawater.
- Marine Industrial Atmospheric: Coastal environments with significant pollution exposure exhibit the highest corrosion rates, ranging from 50 to 150 μm/year.
- Seawater Immersion: Four distinct vertical zones are typically encountered in tidal waters, each with varying corrosion rates:
- Splash Zone (Above High Tide): This zone experiences the most severe corrosion, with an average rate of approximately 75 μm/year.
- Tidal Zone (High Tide to Low Tide): Often covered by marine organisms, this zone exhibits lower corrosion rates, averaging around 35 μm/year.
- Low-Water Zone (Just Below Low Tide): Corrosion rates in this narrow band are comparable to the splash zone.
- Permanent Immersion Zone (Low-Water Level to Seabed): This zone exhibits the lowest corrosion rates, averaging around 35 μm/year.
- Freshwater Immersion: Steel corrosion rates in freshwater environments are generally lower than those observed in saltwater, typically ranging from 30 to 50 μm/year.
Impact of Steel Corrosion
The effects of steel corrosion are far-reaching and pose significant economic and safety concerns in structural steel works:
- Structural Failure: Severe corrosion can compromise the structural integrity of steel beams, columns, and connections, potentially leading to catastrophic failure.
- Aesthetics and Property Value: Visible corrosion not only detracts from the visual appeal of a structure but can also decrease its market value.
- Maintenance Costs: The continuous battle against corrosion necessitates ongoing inspection, repair, and replacement of affected steel components, leading to substantial financial burdens.
Corrosion Protection of Steel Structures
For most common applications, specifying cost-effective protective treatments for structural steelwork becomes a straightforward process when the factors influencing durability are understood. The primary consideration lies in recognizing and defining the corrosivity of the environment where the structure will reside. This understanding is very important for selecting an appropriate protective system.
Many structures are situated in relatively low-risk environments, necessitating minimal protective treatment. Conversely, exposure to an aggressive environment necessitates a more durable protective system, potentially requiring maintenance to ensure extended service life. Striking the optimal balance involves combining proper surface preparation with suitable coating materials to achieve the desired durability at the lowest possible cost.
Modern practices, applied in accordance with relevant industry standards, offer the opportunity to attain the specific protection requirements for various structures. Numerous standards exist to aid in drafting protection specifications. One of the most significant is ISO 12944, titled “Paints and Varnishes – Corrosion Protection of Steel Structures by Protective Paint Systems.” This comprehensive standard, published in eight parts, serves as a valuable resource when crafting protection specifications for structural steelwork.
Strategies for Mitigating Corrosion
A multi-pronged approach is required in mitigating steel corrosion and ensuring the long-term serviceability of steel structures:
- Material Selection: Selecting steel alloys with enhanced corrosion resistance, such as weathering steels or those with higher chromium content, can be very beneficial.
- Protective Coatings: Applying paints, galvanizing (zinc coating), or using cathodic protection systems (electrical current application to suppress corrosion) act as barriers against the corrosive environment.
- Design Considerations: Design features that minimize water accumulation, such as proper drainage, ventilation, and avoiding crevices, can significantly retard corrosion progression.
- Regular Inspection and Maintenance: Proactive inspection programs that identify and address corrosion early are essential to prevent catastrophic failures.
Metallic Coating
Four primary methods are employed for applying metallic coatings to steel surfaces, each offering distinct advantages:
- Hot-Dip Galvanizing: This process involves immersing the steel in molten zinc, resulting in the formation of a zinc-iron alloy layer that provides excellent corrosion resistance.
- Thermal (Metal) Spraying: This technique utilizes a high-temperature source to melt a metallic wire, which is then sprayed onto the prepared steel surface. Thermal spraying offers the flexibility to apply a variety of coating materials but may exhibit lower consistency in coating thickness compared to other methods.
- Electroplating: While not typically used for structural steelwork due to limitations in achievable coating thickness, electroplating is a suitable method for coating fittings, fasteners, and other smaller steel components. This process involves depositing a thin layer of metal onto the steel surface using an electrical current.
- Sherardizing: Similar to electroplating, sherardizing is not commonly employed for structural steelwork. This process involves diffusing a zinc powder coating onto the steel surface at elevated temperatures. It finds application in protecting smaller steel items.
It is important to note that the effectiveness of metallic coatings in protecting against corrosion is primarily influenced by the type of coating metal chosen and its applied thickness. The specific method of application, with the exception of thermal metal spraying due to potential thickness variations, has a lesser impact on overall corrosion resistance. In this article, we will focus on hot-dip galvanising as a method of metallic coating.
Hot-dip Galvanizing
Hot-dip galvanizing is the most prevalent method for applying a metallic coating to structural steel. This process adheres to the specifications outlined in ISO 1461, which mandates a minimum zinc coating weight of 610 g/m² (equivalent to a minimum average thickness of 85 micrometres) for sections no less than 6 millimetres thick.
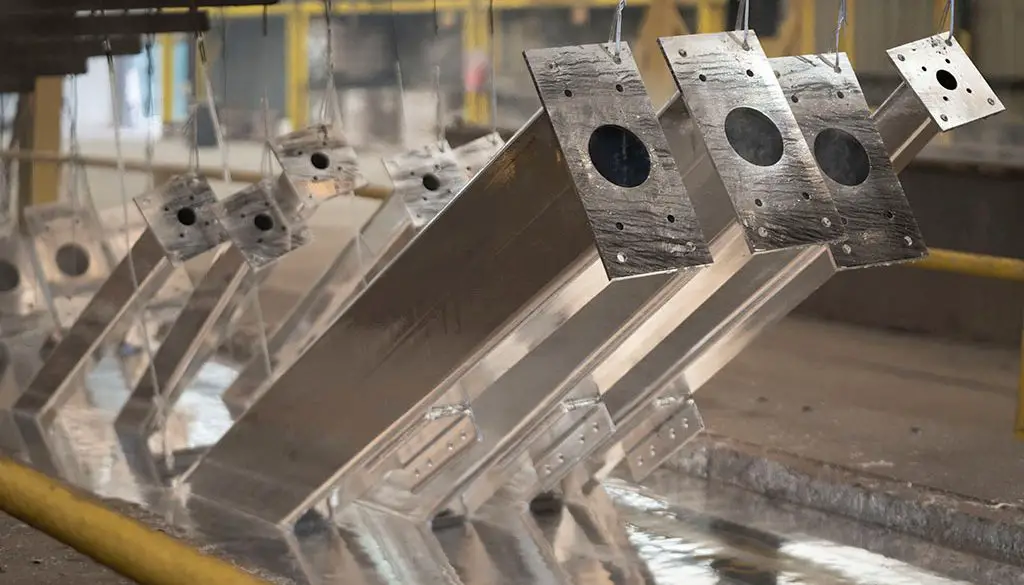
The process of hot-dip galvanizing is as follows:
- Degreasing: Any surface contaminants like oil or grease are removed using appropriate degreasing agents.
- Surface Preparation: All rust and scale are eliminated from the steel through acid pickling. In some cases, this stage may be preceded by blast-cleaning to enhance surface roughness and remove scale. However, blast-cleaned surfaces invariably undergo subsequent pickling with inhibited hydrochloric acid.
- Flux Application: Following cleaning, the steel is immersed in a fluxing agent. This step ensures optimal contact between the molten zinc and the steel during the dipping process.
- Galvanizing: The cleaned and fluxed steel is submerged in a molten zinc bath maintained at approximately 450°C. At this elevated temperature, the steel undergoes a reactive process with the molten zinc, resulting in the formation of a series of zinc-iron alloy layers on its surface.
- Zinc Layer Formation: Upon extraction from the bath, a layer of virtually pure zinc deposits on top of the pre-formed alloy layers.
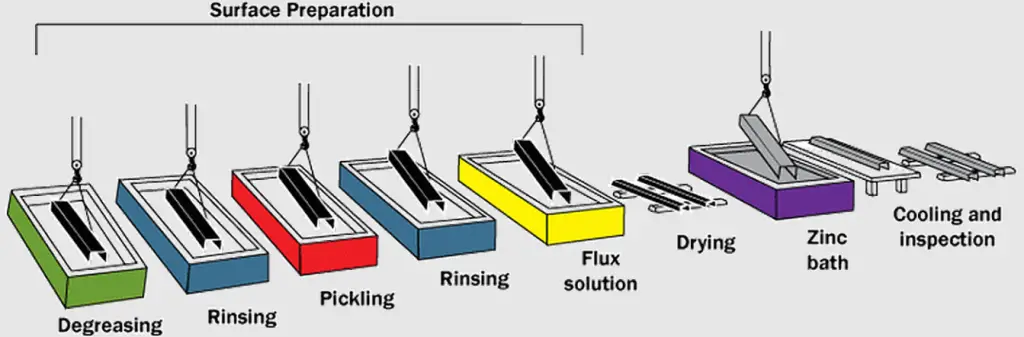
As the zinc solidifies, it adopts a characteristic crystalline metallic sheen, commonly referred to as spangling. The final thickness of the galvanized coating is influenced by several factors, including:
- Size and thickness of the steel workpiece
- Surface preparation technique employed (abrasive blast cleaning typically yields thicker coatings)
- Steel composition
The inherent nature of hot-dip galvanizing, being a dipping process, imposes limitations on the size of components that can be treated. For workpieces exceeding the dimensions of the galvanizing bath, a technique called double dipping can be employed. This involves sequentially dipping one end of the item before the other.
In many applications, hot-dip galvanized steel offers sufficient protection without further treatment. However, for enhanced durability, particularly in specific atmospheric environments, or for aesthetic purposes, paint coatings can be applied over the galvanized surface.
Thermal (metal) Spraying
Thermal (metal) spraying presents an alternative approach for applying a metallic coating to structural steelwork. This method offers the flexibility of utilizing either zinc or aluminium as the coating material, typically supplied in powder or wire form.
The core process involves feeding the metal through a specialized spray gun equipped with a heat source, which can be either an oxy-fuel flame or an electric arc. The heat source melts the metal, transforming it into molten globules that are then propelled onto the previously blast-cleaned steel surface using compressed air.
It is important to note that, unlike hot-dip galvanizing, no alloying occurs between the coating and the steel substrate. The resulting coating consists of overlapping metallic platelets with a porous structure. This necessitates subsequent sealing of the pores
The adhesion of thermally sprayed metal coatings to steel is primarily attributed to mechanical interlocking. Consequently, achieving an optimal bond necessitates applying the coating to a thoroughly cleaned and roughened steel surface. Blast-cleaning with a coarse abrasive grit is the standard practice for surface preparation.
Typical coating thicknesses for thermally sprayed aluminium range from 150 to 200 micrometres, while zinc coatings typically fall between 100 and 150 micrometres.
A significant advantage of thermal metal spraying lies in its versatility. Unlike hot-dip galvanizing, which has limitations on workpiece size due to the dipping process, thermal spraying can be performed either in workshops or directly on-site, accommodating components of any size. Additionally, as the steel surface remains cool during the spraying process, concerns regarding thermal distortion are mitigated.
Design guidance for objects intended for thermal spraying can be found in BS 4479-7. However, it is important to acknowledge that thermal metal spraying is a considerably more expensive option compared to hot-dip galvanizing.
Paint Coatings
Painting remains the primary method for safeguarding structural steelwork from corrosion. Paints consist of a carefully balanced mixture of three key components: pigments, binders, and solvents. Application to steel surfaces can be achieved through various methods; however, all methods result in an initial wet film. As the solvent evaporates, a film-forming process occurs, leaving behind a dry film composed of pigments and binders adhering to the surface.
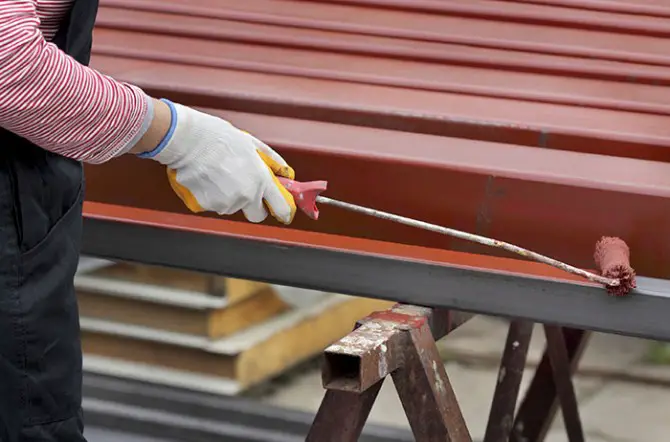
Common classification systems for paints categorize them based on either pigmentation or binder type. Primers designed for steel are usually classified according to the predominant corrosion-inhibiting pigments incorporated into their formulation. Examples include zinc phosphate and metallic zinc.
These inhibitive pigments can be formulated with various binder resins, resulting in variations like zinc phosphate alkyd primers or zinc phosphate epoxy primers. Intermediate and finishing coats are typically classified based on their binders (e.g., epoxy build coats, vinyl finishes, urethane finishes) or their pigments.
Paint application typically involves layering multiple coats, each serving a specific purpose.
The primer, applied directly to the cleaned steel surface, serves the dual function of wetting the surface and ensuring optimal adhesion for subsequent layers. Primers formulated for steel surfaces often possess additional corrosion-inhibiting properties.
Intermediate coats, also known as undercoats, contribute to building the overall film thickness of the paint system. This may necessitate the application of several coats.
Finishing coats provide the frontline defence against environmental elements while also determining the final aesthetic appearance in terms of gloss, colour, and other visual characteristics.
Compatibility between the various superimposed coats within a painting system is crucial for optimal performance. Additionally, vulnerable areas of the structure require the application of extra coats, known as stripe coats, to achieve the minimum required thickness. As a general best practice, it is recommended to source all paints within a system from the same manufacturer.
The chosen application method and prevailing environmental conditions significantly impact the quality and longevity of the applied coating. While other methods like dipping may be employed, the standard application methods for paint on structural steelwork include brush, roller, conventional air-spray, and airless spray techniques.
Conclusion
Steel remains a vital material in modern construction. However, the ever-present threat of corrosion necessitates a thorough understanding of the underlying mechanisms, the various forms of attack, and the potential consequences. By implementing a comprehensive corrosion mitigation strategy, engineers and asset managers can ensure the safety, longevity, and economic viability of steel structures.