In road construction, a sub-base layer is an aggregate layer that lies directly on the subgrade, the native or improved material underneath a constructed road. Likewise, the base course lies directly on the sub-base layer. The sub-base course is vital for roads built to receive vehicular traffic because it is the main load-bearing layer of flexible pavement. However, it may be omitted when a road is constructed only to receive foot traffic.
Furthermore, typical materials for sub-base courses include granular fill, recycled concrete, manufactured aggregate, lean concrete, and crushed rock or concrete. However, this article will introduce you to an alternative sub-base material in reclaimed asphalt.
Reclaimed Asphalt Material

Reclaimed asphalt material consists of removed asphalt concretes from existing road infrastructures. Perhaps you may ask why reclaimed asphalt material. Because of its intended use, reclaimed asphalt material can ensure the sustainability of asphalt materials and associated technologies in the construction and rehabilitation of flexible road pavements. In addition, reclaiming asphalt materials for reuse contributes to construction waste reduction and the provision of a cost-effective material for constructing roads and highways.
Furthermore, with the ever-increasing amount of waste generated on road construction projects and disposal costs, it becomes imperative to recover and reuse these materials. Thus, road construction companies and highway agencies have doubled their efforts in ensuring that existing asphalt concrete materials are reused on road projects. One significant way to reuse removed asphalt concrete is as a sub-base material.
Full-depth Reclamation (FDR) Technique
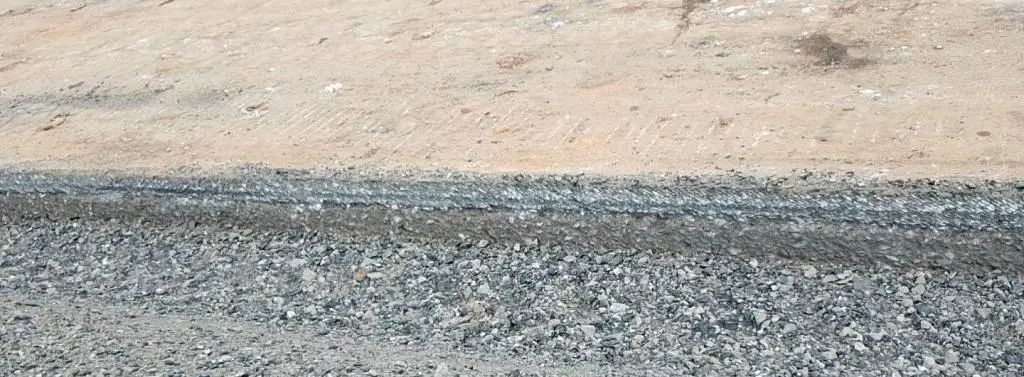
There are four techniques for removing asphalt concrete for reuse:
- cold in-place recycling,
- hot in-place recycling,
- hot in-plant recycling, and
- full-depth reclamation.
The full-depth reclamation technique is usually used for recycling asphalt cement for reuse as a sub-base material. This FDR technique has grown in popularity over the past decade. Its benefits are environmental friendliness, reduced traffic disturbance, use of virgin material, and consumption of fuel and natural resources.
The FDR technique is an on-site recycling method for reclaiming asphalt from an existing road pavement, which is to be used as the sub-base material for new roadway pavement. It involves pulverizing and blending all layers of flexible pavement and part or all of the underlying base materials to provide a homogenous material upon which to place the new base and surface courses.
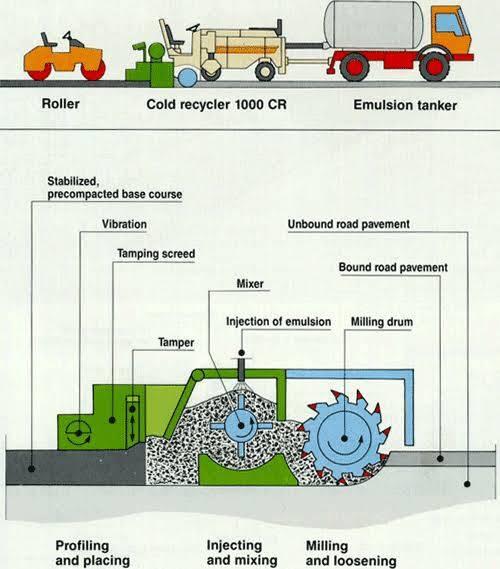
Furthermore, in cases where increased bearing capacity is required, or sub-base failure has occurred, the FDR can be employed to treat or stabilize the sub-base layer by adding chemicals such as portland limestone cement, fly ash and lime. Thus, the treatment or stabilization increases the strength capacity of the sub-base course to cater to present and future traffic.
Process of Reclamation with the FDR Technique
The process of FDR includes the milling and pulverizing of asphalt concrete material with a cold reclaimer or recycling machine in one or multiple passes. The reclaimer consists of a milling drum with teeth, mixer, tamper, fluid injector and vibrator. The fluid used is water, which is usually applied from a separate water truck. However, the liquid may also be applied through the reclaimer’s onboard fluid additive system.
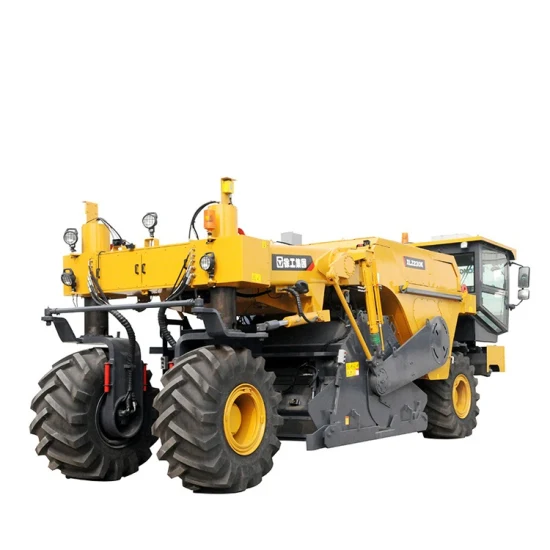
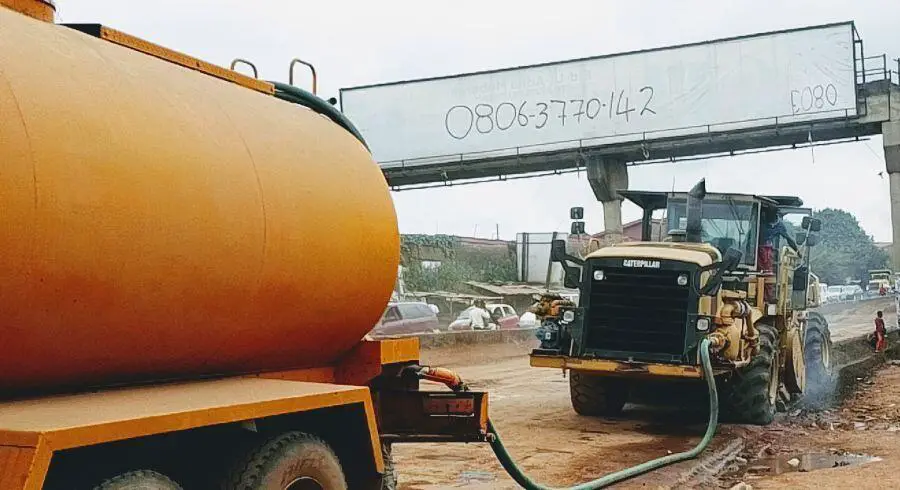
Let’s look at the reclamation process in detail below.
Milling and Pulverizing
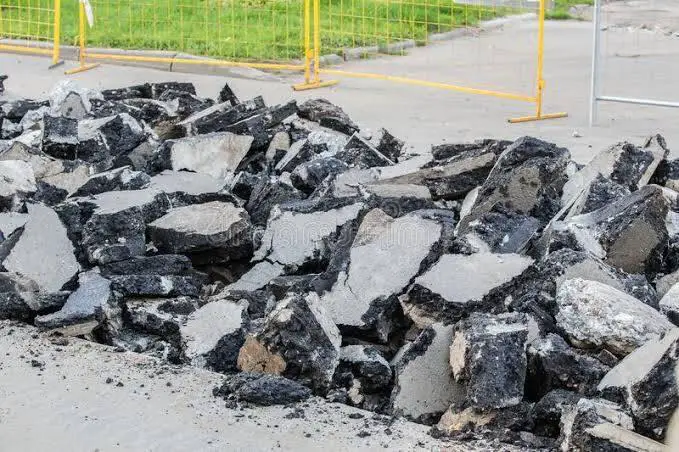
Milling involves breaking the top asphalt layers of a flexible pavement without disturbing the underlying layers; conversely, pulverising consists of grinding and blending the already pulled-up and broken asphalt concrete during milling. In a single pass, the reclaimer often does milling and pulverising of exiting asphalt concrete simultaneously.
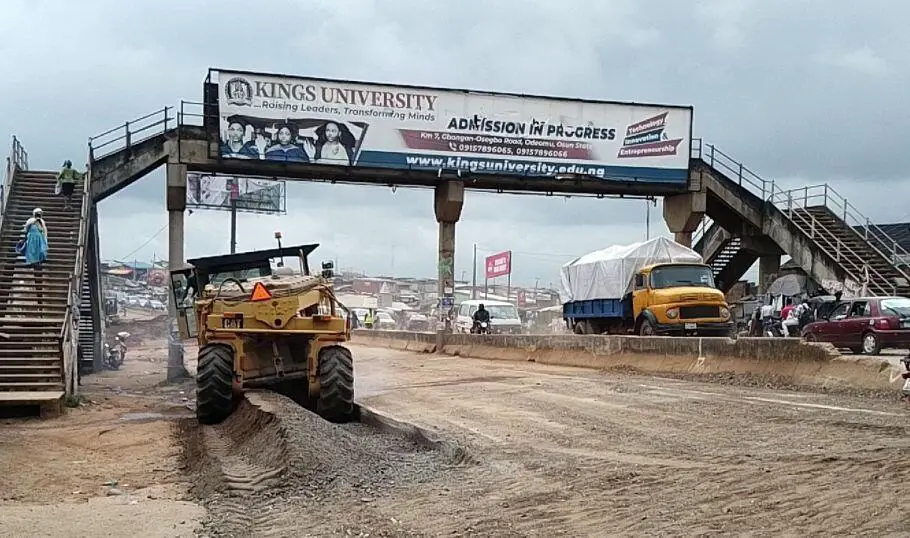
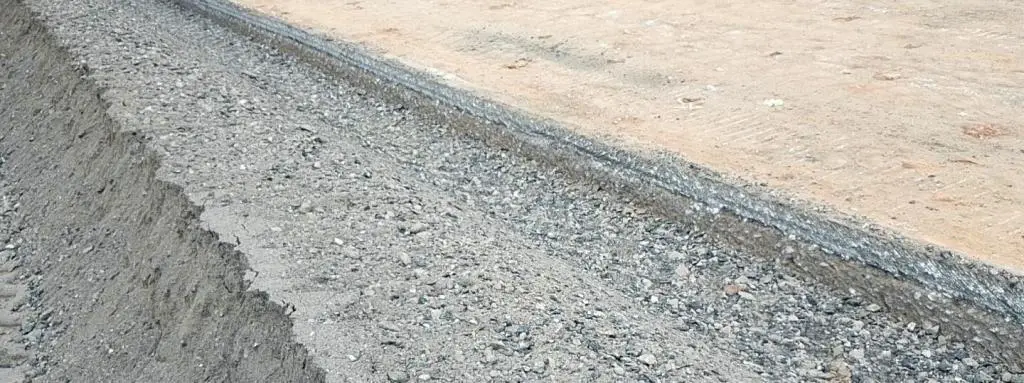
Pulverising is essential because it helps sustain ground conditions and stabilize the new asphalt layer. Thus, milling and grinding in the FDR technique reaches the underlying materials of asphalt pavement as a road reclaimer can go up to about 250 to 300mm in depth.
Furthermore, there is a tendency to have big chunks of materials even after pulverising. In this case, the speed of the reclaimer can be closely monitored and reduced. The reclaimer operator can also check for worn-out teeth on the milling drum, replace them, and remove any visibly oversized materials before grading and compaction. The resulting textured material can either be used as a driving surface or as a sub-base layer to receive base and asphaltic layers.
Grading and Compaction
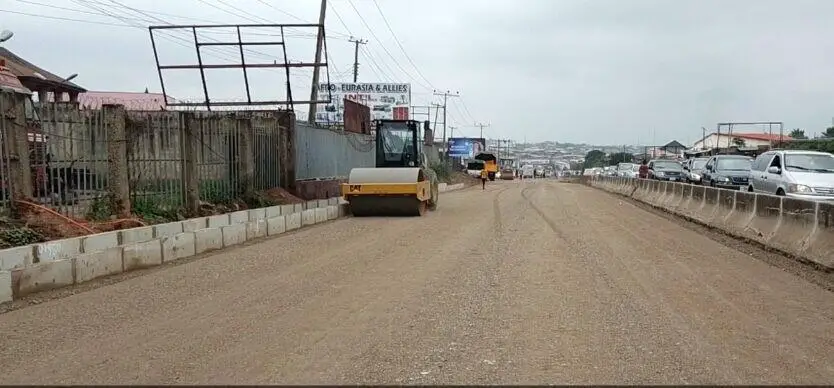
After milling and pulverising, the blended material must be graded with a grader to restore the driving surface and drainage attributes to roads. Likewise, after grading, the layer must be compacted with a vibratory drum roller. However, final compaction is preferred to be done with a pneumatic tyre roller because it brings the fines and moisture of the material to the top. Thus, creating a sealing effect. After compaction and before laying the base course material, in-situ density and moisture content tests must be performed to ascertain proper compaction at a specific dry density and moisture content.
You can watch the processes highlighted above through this link.
Conclusion
Over the past decades, the practice was to remove and replace asphalt concrete layers. However, this practice has become impractical because of cost implications and environmental impact. Therefore, an alternative sub-base material used in flexible pavement construction today is reclaimed asphalt recycled through the full-depth reclamation (FDR) technique.
The FDR technique is preferred because it can correct all types of failures, even to the highest severity. It also eliminates ruts, rough areas, potholes, and all kinds of surface cracking and restores grade contours to allow for better surface drainage. The FDR technique is ideal for replacing the traditional remove and replace flexible pavement reconstruction.
Furthermore, three requirements must be satisfied for recycled or recovered asphalt concrete to be reused as sub-base material, according to the Federal Highway Administration (FHWA). These requirements are that a reclaimed asphalt material must perform well and be cost-effective and environmentally friendly.
Lastly, reclaimed asphalt materials should be reused as sub-base materials such that a road structure’s expected performance is not compromised. Furthermore, engineers, contractors and researchers must be aware of the properties of reclaimed asphalt materials, how best they can be used, the site conditions they are suited for, and the limitations associated with their use.
Therefore, engineering investigation and material tests such as compaction, in-situ density, deformation and resilient modulus must be carried out on reclaimed asphalt materials before use as a sub-base material.
Thanks for the reminder that proper milling is also essential when recycling asphalt. I’d like to have my driveway repaved so I want to know if I could get recycled asphalt for a project like that. I think that will be a lot better for the environment in the long run.
I appreciate that the blog also touched on the importance of quality control and the need for proper processing to ensure the effectiveness of this alternative material. It’s essential to strike a balance between sustainability and performance, and it seems like the road construction industry is moving in the right direction.
Technical specifics and examples of application add credibility to the discussion. The author’s command of the material is evident; as such, the post is an excellent resource for architects, builders, and environmentalists concerned with green infrastructure. All in all, a well-researched and imaginative piece that adds to the ongoing dialogue on greener building practices.