Prestressed concrete is a special type of reinforced concrete. Concrete is weak in tension, and tends to crack when subjected to tensile stresses. Prestressing entails applying an initial compressive load to the structure, in order to reduce or eliminate the internal tensile stresses and, consequently, control or eliminate cracking. By acting on the concrete, highly tensioned steel reinforcement (tendons) apply and maintain the initial compressive load.
A prestressed concrete section is significantly stiffer than an equivalent (often cracked) reinforced concrete section because cracking is minimized or eliminated. Additionally, prestressing may impose internal forces that have the opposite sign from the external loads, which may greatly reduce or even completely eliminate deflection.
The development of prestressing technologies utilized in the production of prestressed concrete has evolved throughout time, mostly as a result of research and development by specialized firms involved in the planning and construction of prestressed concrete structures. These companies regularly operate on related projects including lifting huge structures, cable-stayed bridges, suspension bridges, and soil and rock anchors that call for specialized knowledge and unique equipment, materials, and designs. Each company’s website or direct contact with that company will typically provide information on its items.
The fundamental types of prestressing and the prestressing components are discussed in this article with examples. These include the wire, strand, and bar steel tendons, that are utilized to prestress the concrete.
Types of Prestressing Steel
High-strength steel is typically utilized as tendons in prestressed concrete construction and comes in three basic types which are;
- Cold-drawn stress-relieved round wire;
- Stress-relieved strand; and
- High-strength alloy steel bars.
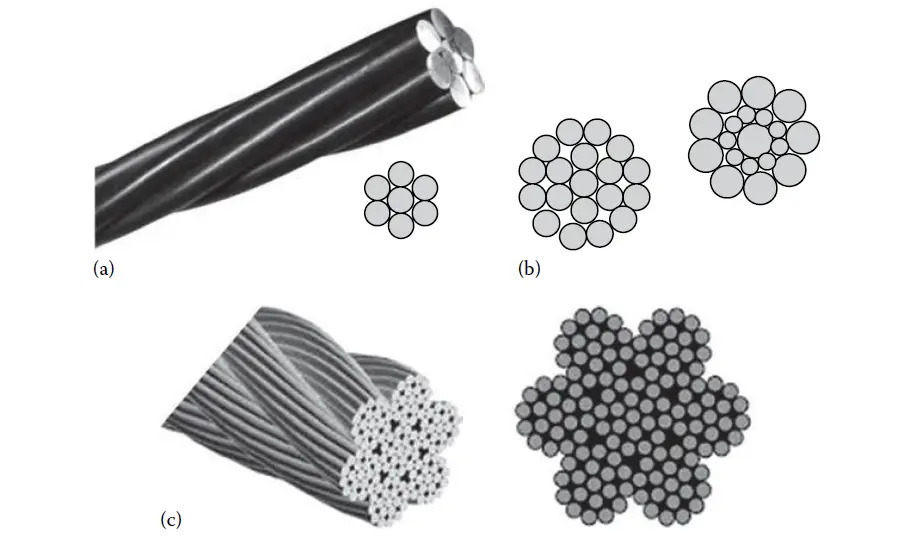
Cold-drawn stress-relieved round wire
Generally speaking, a wire, strand, or bar (or any distinct set of wires, strands, or bars) that is meant to be pre- or post-tensioned is referred to as a tendon. Wires are round, cold-drawn, solid steel parts having a diameter typically between 2.5 and 12.5 mm. Hot-rolled medium to high-carbon steel rods are pulled through dies to create wires of the desired diameter to create cold-drawn wires. Steel is cold-worked throughout the drawing process, changing its mechanical characteristics and improving its strength.
The wires are then continuously heated and straightened to relieve stress, increase ductility, and create the desired material qualities (such as low-relaxation). For wires, the normal characteristic tensile strength fpk ranges from 1570 to 1860 MPa. To enhance the bonding properties of wires, these techniques may be used.
Although wire diameters differ from country to country, they are typically between 4 and 8 mm. In prestressed concrete construction, the use of wires has decreased recently, with 7-wire strand being favoured in most situations.
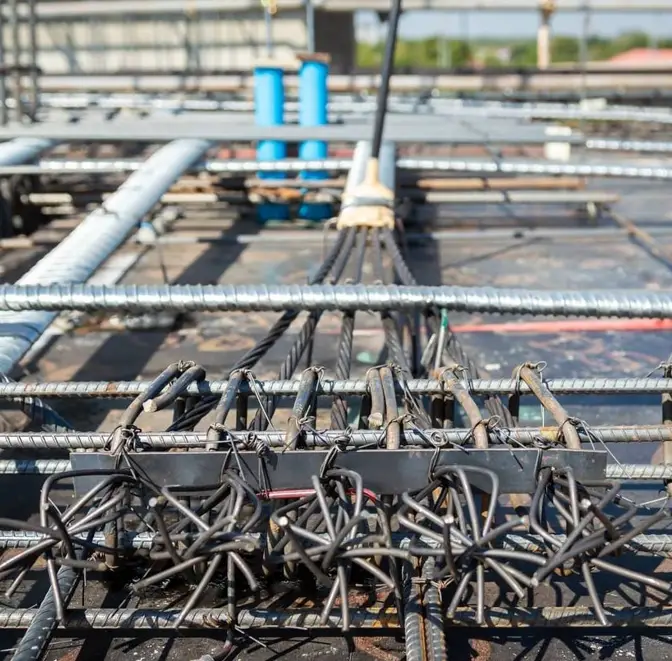
Stress-relieved strand
The most popular kind of prestressing steel is stress-relieved strand. There are options for both 7-wire and 19-wire strands. According to Figure 1a, a seven-wire strand is made up of six tightly coiled wires that are centred around a central core wire with a seventh, somewhat larger diameter wire.
The six spirally wound wires have a pitch that ranges from 12 to 18 times the normal strand diameter. The seven-wire strands’ nominal diameters range from 7 to 15.2 mm, and their typical characteristic tensile strengths fall between 1760 and 2060 MPa.
Pretensioned and post-tensioned applications both frequently use seven-wire strands. Two layers of 9 wires, or alternately two layers of 6 and 12 wires, are spirally coiled around a core wire to make a 19-wire strand. The spirally wound wires have a pitch that is 12–22 times the nominal strand diameter.
The usual cross-sections are depicted in Figure 1b, and the nominal diameters of 19-wire strands in common usage range from 17 to 22 mm. While 19-wire strand is used in post-tensioned applications, pretensioned applications, where the transfer of prestress depends on the surface area of the strand available for binding to the concrete, are not advised due to 19-wire strand’s comparatively low surface area to volume ratio.
By drawing the strand through a compacting die, the diameter of the strand can be reduced while keeping the steel’s cross-sectional area constant. Strand compression also makes it easier to grasp the strand at its anchorage. The strand’s mechanical characteristics differ slightly from those of the wire from which it is produced. This is due to the fact that when under tension, stranded wires have a tendency to somewhat straighten, which lowers the apparent elastic modulus. For design reasons, the elastic modulus is Ep = 195 × 103 MPa, and the yield stress of the stress-relieved strand is approximately 0.86fpk.
As seen in Figure 1c, cables are made up of a collection of strands that are frequently braided together from multiple wires. Typically, stay cables are produced straight from strands and are utilized extensively in cable-stayed and suspension bridges.
High-strength alloy steel bars
Hot-rolled high-strength alloy steel bars have alloying components added during the steelmaking process. To strengthen the relationship, some bars have ribs. Bars are single, straight lengths of solid steel that are larger in diameter than wire. They normally have diameters between 20 and 50 mm and typically have a minimum breaking stresses between 1030 and 1230 MPa.