To reduce soil heave under a foundation or subgrade, expansive soils can be overexcavated and replaced with nonexpansive or treated soils. In this approach, the expansive soil is excavated to an adequate depth to reduce heave, and then replaced with properly treated and compacted fill up to grade.
The required depth of removal, as well as the volume, location, and cost of the fill, must all be considered. The depth of soil that must be removed is determined by the overall soil profile, the nature of the fill material, and the amount of heave that may be tolerated. A stiff layer of compacted low to nonexpansive fill has the added benefit of tending to even out variations in the heave of the underlying native soil, thereby eliminating differential heave.
In the absence of suitable nonexpansive fill around the area, moisture-conditioning and compaction control can be used to change the swell properties of the expansive soils on-site. Compacting the material to a lower density at the wet side of the optimum moisture content will minimize the expansion potential, but care must be taken to ensure that the recompacted soil is densified well enough to avoid settlement. Chemical additives can be utilized in conjunction with moisture-conditioning in some cases.
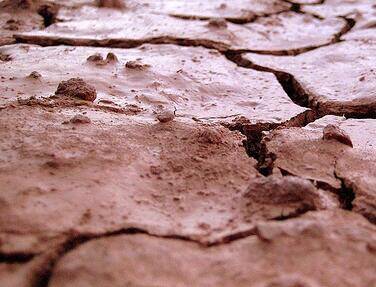
However, if the expansive soil layer extends to a depth that makes total removal and replacement prohibitively expensive, appropriate soil tests and studies should be carried out to design the overexcavation and assess the projected potential heave after the overexcavation and recompaction procedure. The expected heave must be factored into the depth of overexcavation design.
Chen (1988) suggested a maximum overexcavation depth of 3 to 4 feet (1 to 1.3 meters), but these depths have been oberved to be ineffective for sites with highly expansive soils. Thompson (1992a and 1992b) studied some insurance claims and found that if there was 10 feet (3 meters) or more of nonexpansive soil beneath the footings, the frequency of claims was lower than at shallower depths. Overexcavation depths of 10 ft (3 m) or more have been specified regularly in Thompson’s works. In certain situations, the top 20 feet (6 meters) of soil have been excavated, moisture-conditioned, and recompacted in place.
Water content changes in the underlying expansive soil layers can be controlled by overexcavation and replacement. The majority of the seasonal water content variation will occur in the top few feet of soil. However, if the underlying soil has a high potential for expansion, the overexcavated zone may not be enough to prevent surface heave or shrinkage. If the underlying expansive soil gets wet, it might cause uncontrollable movement. Some of the potential water sources are impossible to forecast or control. As a result, the design engineer must consider that such events might occur during the structure’s lifetime and make appropriate design decisions.
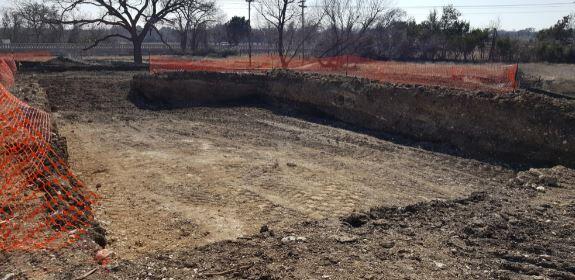
Furthermore, water collection in the overexcavation zone must be avoided at all costs. The use of permeable granular fill as a replacement fill is not suggested. Highly permeable fill will allow water to flow freely and create a reservoir for it to collect in. The ‘bathtub effect‘ is a term used to describe this phenomenon. Seepage into expansive subgrades or foundation soils will occur as a result of this situation. Any fill material that is impermeable and nonexpansive is therefore more preferable. If granular material is required, permanent, positive drainage and moisture barriers, such as geomembranes, should be installed to prevent moisture from infiltrating this zone.
The removed and recompacted material is expected to have a higher hydraulic conductivity than the underlying in situ soils and bedrock, even without granular soil. Groundwater can be intercepted using an underdrain system installed at the bottom of the overexcavation zone. Care must be taken to ensure that the drain has positive drainage and that it does not just concentrate water in an area where it would cause increased soil wetting and heave.
Advantages of Overexcavation and Replacement
The following are some of the benefits of overexcavation and replacement treatment:
• Because soil replacement does not require special construction equipment, it might be less expensive than other treatment options.
• Soil treatment additives can be mixed in a more equal manner, resulting in some soil improvement.
• Overexcavation and replacement may cause construction to be delayed less than other processes that need a curing period.
Disadvatantages of Overexcavation and Replacement
The following are some of the disadvantages of overexcavation and replacement methods:
• The expense of nonexpansive fill with low permeability can be high if the fill must be imported.
• If the recompacted on-site soils demonstrate intolerable expansion potential, removing and recompacting the on-site expansive soils may not be enough to limit the danger of foundation movement.
• The recompacted backfill material’s needed thickness may be too considerable to be practicable or cost-effective.
• If the backfill material is overly permeable, the overexcavation zone could act as a reservoir, storing water for the foundation soils and bedrock over time.
If overexcavation and replacement are ineffective on their own, they can be combined with other foundation options. It may be conceivable to employ a rigid mat foundation instead of a more expensive deep foundation if the potential heave can be suitably mitigated. The needed length of the piers may also be lowered when used in conjunction with a deep foundation.
References
[1] Chen, F. H. 1988. Foundations on Expansive Soils. New York: Elsevier Science.
[2] Thompson, R. W. 1992a. “Swell Testing as a Predictor of Structural Performance.” Proceedings of the 7th International Conference on Expansive Soils, Dallas, TX, 1, 84–88.
[3] Thompson, R. W. 1992b. “Performance of Foundations on Steeply Dipping Claystone.” Proceedings of the 7th International Conference on Expansive Soils, Dallas, TX, 1, 438–442
Very good article. Thank you for sharing.