Beams that are curved in plan are often found in buildings, circular reservoirs, bridges, and other structures with curves. Curved beams always develop torsion (twisting) in addition to bending moment and shear forces because the center of gravity of loads acting normal to the plane of the structure lies outside the lines joining its supports. Therefore to maintain equilibrium in the structure, the supports of a curved beam must be fixed or continuous.
In this post, we are going to show in the most simplified manner, how to analyse continuous circular (ring) beams.
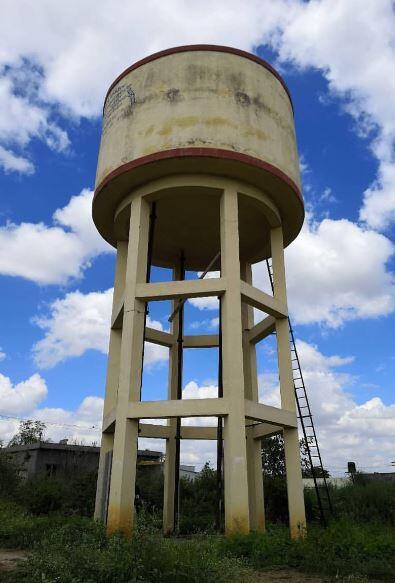
For ring beams;
Maximum Negative Moment at any support = K1wr2
Maximum Positive Moment at any span = K2wr2
Maximum Torsional Moment = K3wr2
Total load on each column (support reaction) R = wr(2θ)
Shear force at any support = R/2 = wrθ
The coefficients are given in the table below;
Solved Example
A cylindrical reservoir with a diameter of 6m is supported by a ring beam, which is supported on 8 equidistant columns. It is desired to analyse and design the ring beam to support the load from the superstructure.
The plan view of the structural disposition of the reservoir is shown below;
Load Analysis
(a) Geometry of sections
Dimension of beams = 450mm x 300mm
Dimension of column = ϕ300mm circular columns
Thickness of reservoir walls = 250mm
Thickness of reservoir slab = 250mm
(b) Density of materials
Density of stored material = 10 kN/m3
Density of concrete = 25 kN/m3
(c) Dead Loads
Weight of the walls = (25 kN/m3 × 0.25m × 4.75m × 18.849m) = 559.579 kN
Weight of bottom slab = (25 kN/m3 × 0.25m × 28.274m2) = 176.7125 kN
Weight of water stored = (10 kN/m3 × 4.5m × 23.758m2) = 1069.11 KN
Total = 1805.4015 kN
Let us transfer this load to the the ring beam based on the perimeter.
Perimeter of ring beam = πd = π × 6 = 18.849m
w = 1805.4015 kN / Perimeter of ring beam = 1805.4015 kN / 18.849m = 95.782 kN/m
Self weight of the beam = 25 kN/m3 × 0.3m × 0.45m = 3.375 kN/m
Total dead load on beam = 95.782 kN/m + 3.375 kN/m = 99.157 kN/m
Factoring the load on the beams at ultimate limit state = 1.35 × 99.157 kN/m = 133.862 kN/m
From the table above;
Number of supports (n) = 8
θ = π/n = 45°
K1 = 0.052
K2 = 0.026
K3 = 0.0040
Radius (r) = 3m
Maximum Negative Moment at the supports = K1wr2 = -0.052 × 133.862 × 32 = -62.647 KN.m
Maximum Positive Moment at the spans = K2wr2 = 0.026 × 133.862 × 32 = 31.323 KN.m
Maximum Torsional Moment = K3wr2 = 0.0040 × 133.862 × 32 = 4.819 KN.m
Shear force at the supports = R/2 = wrθ = 133.862 × 3 × (π/8) = 157.7 KN
Structural Design
Design strength of concrete fck = 35 N/mm2
Yield strength of reinforcement fyk = 500 N/mm2
Nominal cover to reinforcement = 30 mm
Span
MEd = 31.323 kN.m
Effective depth (d) = h – Cnom – ϕ/2 – ϕlinks
Assuming ϕ12 mm bars will be employed for the main bars, and ϕ8mm bars for the stirrups (links)
d = 450 – 30 – 6 – 8 = 406 mm
k = MEd/(fckbd2) = (31.323 × 106)/(35 × 300 × 4062) = 0.0181
Since k < 0.167, no compression reinforcement required
z = d[0.5+ √(0.25 – 0.882K) ] = z = d[0.5+ √(0.25 – 0.882(0.0181))] = 0.95d
As1 = MEd/(0.87yk z) = (31.323 × 106)/(0.87 × 500 × 0.95 × 406) = 186.69 mm2
Provide 3H12 mm BOT (ASprov = 339 mm2)
Supports
MEd = 62.647 KN.m
Effective depth (d) = h – Cnom – ϕ/2 – ϕlinks
Assuming ϕ16 mm bars will be employed for the main bars, and ϕ8mm bars for the stirrups (links)
d = 450 – 30 – 8 – 8 = 404 mm
k = MEd/(fckbd2) = (62.647 × 106)/(35 × 300 × 4042) = 0.0365
Since k < 0.167, no compression reinforcement required
z = d[0.5+ √(0.25 – 0.882K) ] = z = d[0.5+ √(0.25 – 0.882(0.0365))] = 0.95d
As1 = MEd/(0.87fyk z) = (62.647 × 106)/(0.87 × 500 × 0.95 × 404) = 375.23 mm2
Provide 2H16 mm TOP (ASprov = 402 mm2)
Interaction of shear and torsion
According to clause 6.3.2(2) of Eurocode 2, the effects of torsion and shear for both hollow and solid members may be superimposed, assuming the same value for the strut inclination θ. The limits for θ given in 6.2.3 (2) of EC2 are also fully applicable for the case of combined shear and torsion.
According to clause 6.3.2(4) of EC2, the maximum resistance of a member subjected to torsion and shear is limited by the capacity of the concrete struts. In order not to exceed this resistance the following condition should be satisfied:
TEd /TRd,max + VEd /VRd,max ≤ 1 ———- Equation (6.29 of EC2)
VEd = 157.7 KN
TEd = 4.819 kN.m
TRd,max = design torsional resistance moment
VRd,max = maximum shear resistance of the cross-section
Geometrical Properties for analysis of torsion
Area (A) = 300mm × 450mm = 135000 mm2
Perimeter (U) = 2(300) + 2(450) = 1500mm
Equivalent thickness = tef,i = A/U = 135000/1500 = 90mm
The equivalent thin wall section for the rectangular section is given below;
Ak = the area enclosed by the centre-lines of the connecting walls, including inner hollow areas = (450 – 90) × (300 – 90) = 75600 mm2
Uk = is the perimeter of the area Ak = 2(450 – 90) + 2(300 – 90) = 1140 mm
TRd,max = 2 v αcwfcdAktef,i sinθ cosθ
Assuming θ = 21.8° (cot θ = 2.5)
v = 0.6(1 – fck/250) = 0.6(1 – 35/250) = 0.516
fcd = (αcc × fck)/γc = (1 × 35)/1.5 = 23.33 N/mm2
TRd,max = 2 × 0.516 × 1.0 × 23.33 × 75600 × 90 × cos 21.8° × sin 21.8° × 10-6 = 56.485 KNm
VRd,c = [CRd,c.k.(100ρ1 fck)(1/3) + k1.σcp]bw.d
Where;
CRd,c = 0.18/γc = 0.18/1.5 = 0.12
k = 1 + √(200/d) = 1 + √(200/404) = 1.704 > 2.0, therefore, k = 1.702
ρ1 = As/bd = 402/(300 × 404) = 0.003317 < 0.02; K1 = 0.15
VRd,c = [0.12 × 1.704(100 × 0.003317 × 35 )(1/3)] 300 × 404 = 65469.358 N = 65.469 KN
Since VRd,c (65.469 KN) < VEd (157.7 KN), shear reinforcement is required.
The compression capacity of the compression strut (VRd,max) assuming θ = 21.8° (cot θ = 2.5)
VRd,max = (bw.z.v1.fcd)/(cotθ + tanθ)
V1 = 0.6(1 – fck/250) = 0.6(1 – 35/250) = 0.516
fcd = (αcc ) fck)/γc = (1 × 35)/1.5 = 23.33 N/mm2
Let z = 0.9d
VRd,max = [(300 × 0.9 × 404 × 0.516 × 23.333)/(2.5 + 0.4)] × 10-3 = 452.863 KN
Since VRd,c < VEd < VRd,max
Hence, Asw/S = VEd/(0.87Fykzcot θ) = 157700/(0.87 × 500 × 0.9 × 404 × 2.5 ) = 0.3988
Minimum shear reinforcement;
Asw/S = ρw,min × bw × sinα (α = 90° for vertical links)
ρw,min = (0.08 × √(fck))/fyk = (0.08 × √35)/500 = 0.0009465
Asw/S (min) = 0.0009465 × 300 × 1 = 0.2839
Since 0.2839 < 0.3988, adopt 0.3988
Maximum spacing of shear links = 0.75d = 0.75 × 404 = 303mm
Provide H8mm @ 250mm c/c (Asw/S = 0.402) Ok
Note that this link must be properly closed with adequate anchorage length, because it will assist in resisting torsion.
Design Considerations for Torsion
TEd /TRd,max + VEd /VRd,max ≤ 1
(4.891/56.485) + (157.7/453.863) = 0.434 < 1.0 Hence it is ok
However, note that the actual shear force at the point where torsion is maximum is actually less than the shear force at the support. The relationship above is an error but on the safe side.
The maximum torsion occurs at an angle of 9.5° from the support (see Table above). Therefore, the actual shear force at that section ( VEd) = Shear force at support – wrα
VEd = 157.7 – (133.862 × 3 × (9.5/180) × π) = 91.114 KN
Therefore for educational purposes, this is the shear force that should be used to check the shear-torsion interaction. A little consideration will show that VRd,max is constant all through the section, but VRd,c might vary depending on the longitudinal reinforcement provided at the section.
Rechecking the interaction above;
(4.891/56.485) + (91.114/453.863) = 0.287< 1.0 Hence it is ok
Area of transverse reinforcement to resist torsion
Asw/s = TEd/2Ak fyw,d cotθ
Asw/s = (4.819 × 106) / (2 × 135000 × 0.87 × 500 × 2.5) = 0.0164 < Asw/S (min)
Therefore, links provided for shear will be adequate for resisting torsion.
Area of longitudinal reinforcement to resist torsion
As1 = TEdUk cot θ / 2Ak fyd
As1 = (4.819 × 106 × 1140 × 2.5) / (2 × 75600 × 0.87 × 500) = 208 mm2
According to clause 6.3.2(4), in compressive chords, the longitudinal reinforcement may be reduced in proportion to the available compressive force. In tensile chords the longitudinal reinforcement for torsion should be added to the other reinforcement. The longitudinal reinforcement should generally be distributed over the length of side, but for smaller sections it may be concentrated at the ends of this length.
However, for the avoidance of doubt since no definition was given for what could be regarded as a ‘smaller section’, Provide 1H12mm bar at the middle of the section at both faces. The tensile and longitudinal reinforcement provided at the top and bottom of the section should be able to take care of the rest.
Further information
Nominal shear reinforcement is required in rectangular sections when;
TEd /TRd,c + VEd /VRd,c ≤ 1 ————– Equation (6.31 of EC2)
Where;
TRd,c is the value of the torsion cracking moment:
VRd,c is as defined above.
TRd,c = fctd⋅t⋅2Ak
τ = fctd = fctk /γc = 2.2/1.5 = 1.466 MPa (fctk deducted from Table [3.1 – EC2]).
It results therefore:
TRd,c = fctd⋅t⋅2Ak = 1.466 × 90 × 2 × 75600 × 10-6 = 19.949 kNm
From above calculations;
VRd,c = [0.12 × 1.704(100 × 0.003317 × 35 )(1/3)] 300 × 404 = 65469.358 N = 65.469 KN
(4.819/19.949) + 91.114/65.469) = 1.633 > 1.0 (Shear force at point of maximum torsion was used)
Therefore obviously this showed that shear reinforcement calculations were required.
References
Hassoun M.N., Al-Manaseer A. (2008): Structural Concrete Theory and Design (4th Edition). John Wile and Son Inc., New Jersey
You are doing a great job Ubani. #thumbs up
Thanks for the effort
Sir
Thank you Engr. Apele
Thank you so much
Dear Ubani, i just throughly look to your post. The design of curved beam with moment coefficients O.K. But it is not good to assume the storage tank weight as uniform load. If the circular beam and the tank is casted together, the 5m depth tank shell will support the circular beam. Even concrete tank is seperate and freely supported , the tank wt will be supported by columns mostly. Another comment, the liquid content is LL. U may check ur assumtions with FEM analysis..Good Luck…….
I totally agree with you on both counts. Except the tank will be permanently filled with water. It is safe to consider the water as a live load.
Thank you for your intelligent contributions. As for the real load transfer pattern, I need more expert opinion.
On the second issue, I initially wanted to treat water as live load because the volume of water in the tank will fluctuate. But on the other hand, I do not need any statistical analysis to predict the maximum load the tank can ever experience due to water storage, so why should I use a higher factor of safety?
Dear Ubani, i just saw ur last comment… First of all ur tank ht 5 m and water ht 4,5m. What is dictating this level? say ..overflow pipe.. that means prone to blocking or valve closing and water content will reach to max level and then spills.. Another issue, unit wt of content. If u are sure for the content will be only water and if u assume the max level can be reached , u can use indeed γQ = 1.2 . Good luck…
Theta = 2π÷n not π÷n
dear Ubani, how do you calculated and get the coefficient in the table for -/+ moment and torsional moment ?
Kindly furnish reference material from which this procedure is taken
• This is the first time I am visiting your website. I would like to tell you that I am genuinely engaged by reading your blogs. Keep up the good work!Fabrication Drawings preparation in USA
Shop Drawings Preparation in USA
Structural Analysis in USA
Thank you
Hello Mr Udozammi,
I think you are doing a great job, and I believe I will continue to follow you and share our experiences in structural design practice as needed.
Again, good job and thank you for your spirit of
sharing
Patrick Saint-Louis,
Canada
GREAT JOB
I am also a staunch follower because of how try to simplify solutions to difficult problems in this field of engineering
I want circular beam subjected to concentrated load at the midspan example
Many thanks for sharing
R sir, I would like to ask that how to decide thickness of circular beam? sir you mentioned directly.