Floors in buildings have a primary function of carrying loads and supporting the activities of the occupants. In addition to carrying loads, floors in buildings also provide the needed rigid diaphragm action for transmitting horizontal loads to the stabilising vertical components. Furthermore, floors also support additional superimposed loads such as ceilings, building services, and finishes such as screeds and tiles.
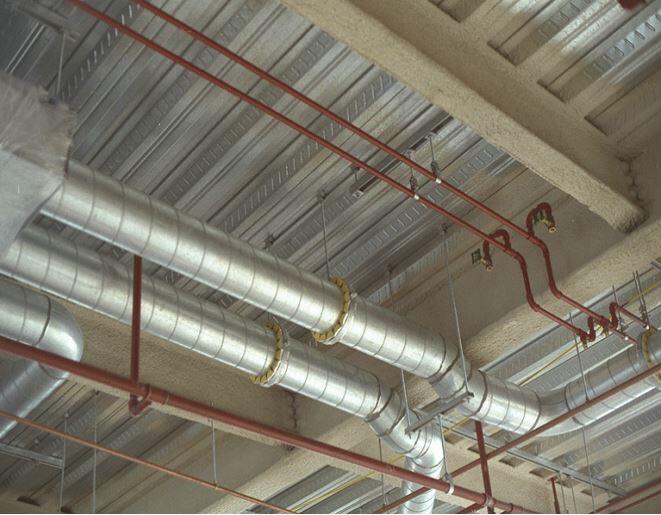
The types of floor systems that used in steel-framed buildings are;
- Short-span composite beams and composite slabs with metal decking.
- Slimdek®.
- Cellular composite beams with composite slabs and steel decking.
- Slimflor® beams with precast concrete units.
- Long-span composite beams and composite slabs with metal decking.
- Composite beams with precast concrete units.
- Non-composite beams with precast concrete units.
Short span composite beam and composite slab with metal decking
In this floor system, shear connectors are welded through the metal decking to the top flange of downstand beams to enable it act compositely with an in-situ composite slab. For short span floor systems, the secondary beams are typically spaced between 3 – 4m and are supported by the primary beams. The primary and secondary beams act compositely with the composite slab, but the edge beams are usually non-composite. At 3-4m spacing, secondary beams will span about 6 – 7.5m when positioned orthogonally to the slab, while the primary beams will span about 6-9m (positioned parallel to the slab).
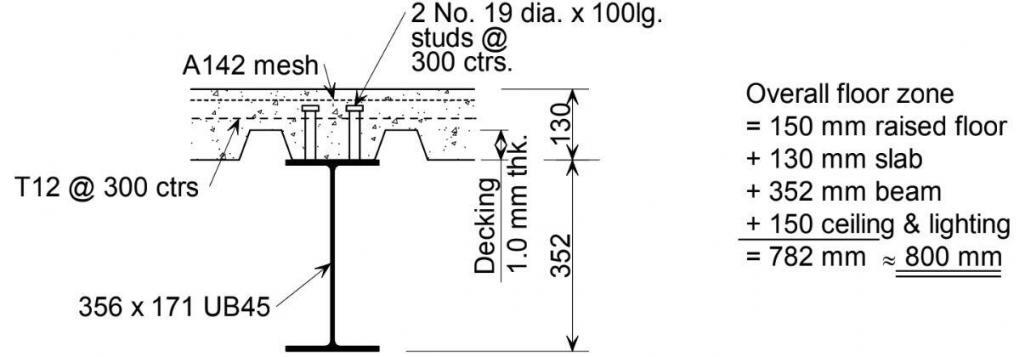
The floor slab consists of composite profiled metal decking with a typical depth of about 130 mm thick with in-situ concrete topping. The profiles may be re-entrant decking or trapezoidal. Re-entrant decking uses more concrete than trapezoidal decking, but has increased fire resistance for a given slab depth. Trapezoidal decking generally spans further than re-entrant decking, but the shear stud resistance is less with trapezoidal decking than with re-entrant decking. The profiles are usually between 0.5 to 1.2mm thick.
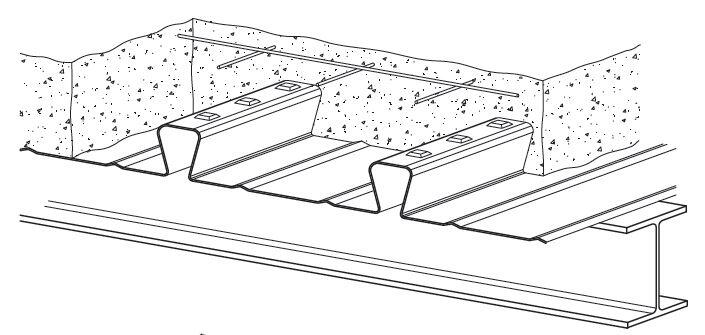
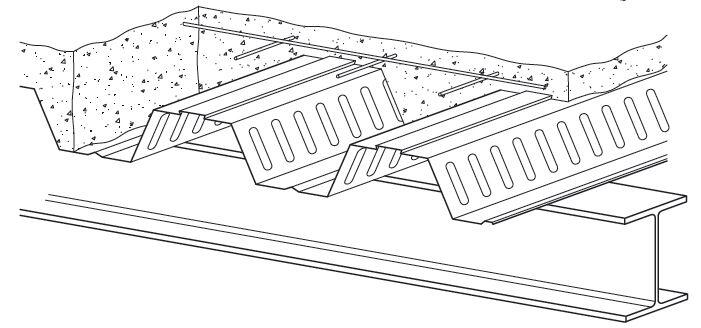
Mesh reinforcement is provided at the top of the slab to help reduce cracking, spread localised loads, enhance fire resistance, and act as shear reinforcement around the shear connectors. The decking is normally designed to support the wet weight of the concrete and construction loading as a continuous member over at least two spans, but the composite slab is normally designed as simply supported between beams (but some continuity reinforcement is required). The design of the decking is usually picked from the manufacturer’s technical data sheet.
Advantages
(1) Shallower beams than non-composite floors
(2) More economical
(3) Light weight
Disadvantages
(1) More columns needed than with long-span systems.
(2) Deeper overall floor zone than shallow floor systems.
(3) Generally, beams require fire protection.
Slimdek
Slimdek is a shallow floor system comprising asymmetric floor beams (ASBs) supporting heavily ribbed composite slabs with 225 mm deep decking. ASBs are proprietary beams with a wider bottom flange than top. The section has embossments rolled into the top flange and acts compositely with the floor slab without the need for additional shear connectors.
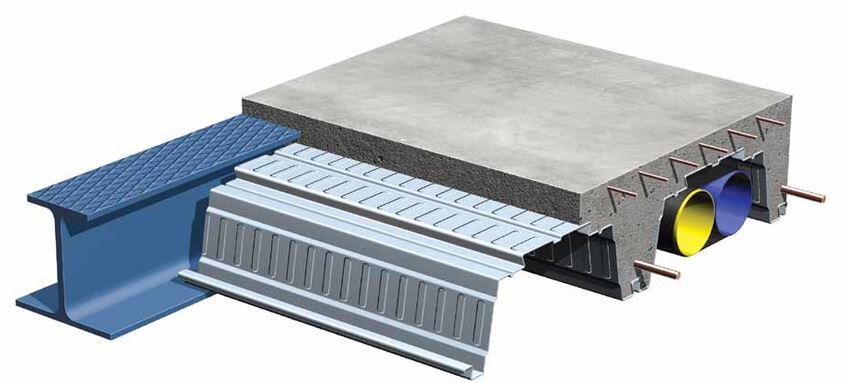
The decking spans between the bottom flanges of the beams and acts as permanent formwork to support the slab and other loads during construction. The in-situ concrete acts compositely with the decking and encases the beams so that they lie within the slab depth – apart from the exposed bottom flange. The floor normally spans between 6 – 9m grid with floor depth of about 280 – 350 mm. Reinforcements of 16mm to 25mm bars are placed in the ribs of the slab to improve strength in the fire condition, while mesh reinforcement is paced above ASB.
Advantages
(1) Shallow floor zone – reduction in overall building height and cladding.
(2) Virtually flat soffit allows easy service installation and offers flexibility of internal wall positions.
Disadvantages
(1) Steel weight is often greater than other floor systems.
(2) Connections require careful detailing due to the width of the bottom flange.
Cellular composite beams with composite slabs and steel decking
Cellular beams are beams with openings at short regular intervals along their length. The beams are either fabricated from 3 plates or made from rolled sections. Openings, or ‘cells’, are normally circular, which are ideally suited to circular ducts, but can be elongated, rectangular or hexagonal. Cells may have to be filled in to create a solid web at positions of high shear, such as at supports or either side of point loads along the beam.
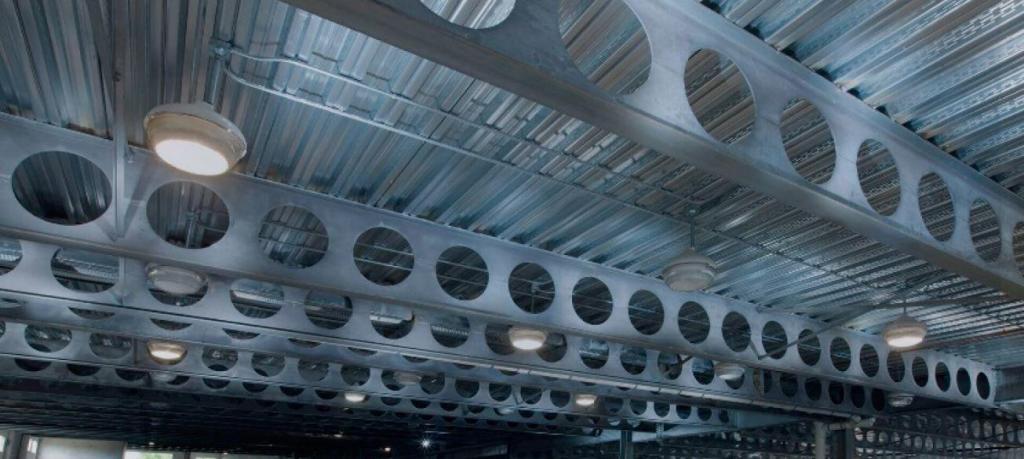
Cellular beams can be arranged as long-span secondary beams, supporting the floor slab directly, or as long-span primary beams which are aligned parallel to the span of the slab supporting other cellular beams or conventional rolled section secondary beams. The secondary beams are typically placed at 3 – 4 m spacing, supported by primary beams on a 6 m, 7.5 m or 9 m column grid. The decking and slab can be designed using decking manufacturer’s design tables or software.
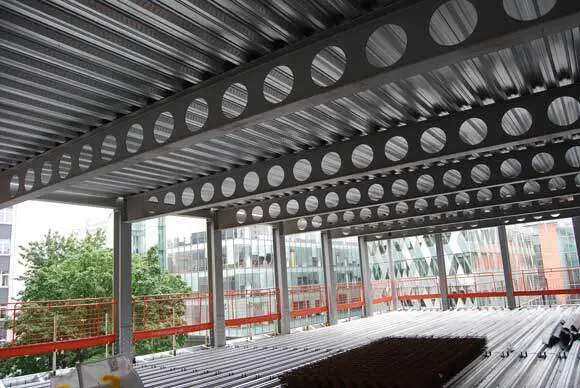
Advantages
Long, column-free floor spans.
Relatively lightweight beams compared with other long-span systems.
Economic long-span solution.
Precamber can be accommodated during the fabrication of the members.
Regular openings in the web allow ducts and other services to pass through the beams.
Disadvantages
Increased fabrication costs compared with plain sections.
Slimflor® beams with precast concrete units
In slim floor system where the beams are contained within the structural floor depth. A steel plate (typically 15 mm thick) is welded to the underside of a UC section to make the Slimflor beam. This plate extends beyond the bottom flange by 100 mm either side, and supports the precast floor units. A structural concrete topping with reinforcement is recommended to tie the units together and the topping thickness should cover the units by at least 30 mm.
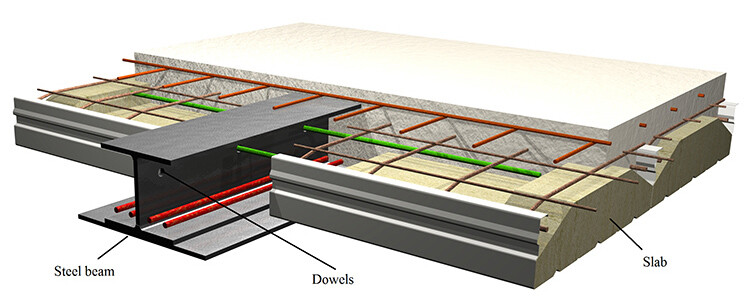
A composite Slimflor beam can be achieved by welding shear connectors (normally 19 mm diameter by 70 mm long) to the top flange of the UC. Reinforcement is then placed across the flange into slots prepared in the precast units, or on top of shallow precast units. If the steel beams are to be designed compositely, the topping should cover the shear connectors by at least 15 mm, and the precast units by 50 mm.
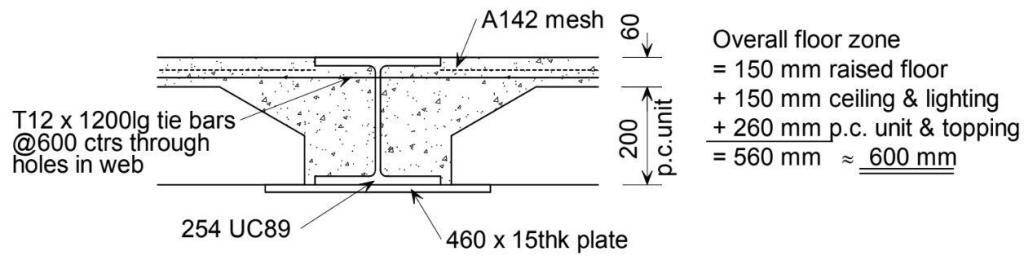
Only 152 UCs and 203 UCs are normally suitable as composite beams because the overall depth of the floor slab becomes impractical for larger serial sizes. Precast units are usually cambered to cancel out dead load deflections between beams, and the floor spans are typically between 4.5m to 7.5m even though spans of 10m can be achieved.
Advantages
(1) Beams normally require no fire protection for up to 60 minutes fire protection.
(2) Shallow floor zone – reduction in overall building height and cladding. Virtually flat soffit allows easy service installation and offers flexibility of internal wall positions.
(3) Shear connectors can be welded off-site, enabling larger stud diameters to be used and reducing site operations.
Disadvantages
(1) The steelwork is relatively heavy.
(2) Extra fabrication is involved in welding the plate to the UC. Connections require more detailing as the plate is wider than the column.
(3) Precast units involve more individual lifting operations than decking, which is delivered and erected in bundles. The erection sequence requires access for installation of the concrete units.
Long-span composite beams and composite slabs with metal decking
This system consists of composite beams using rolled steel sections supporting a composite slab in a long-span arrangement of, typically, 10 to 15 m. Grids are either arranged with long-span secondary beams at 3 m to 4 m spacing supporting the slab, supported by short-span primary beams, or with short- span secondary beams (6-9 m span) supported by long-span primary beams.
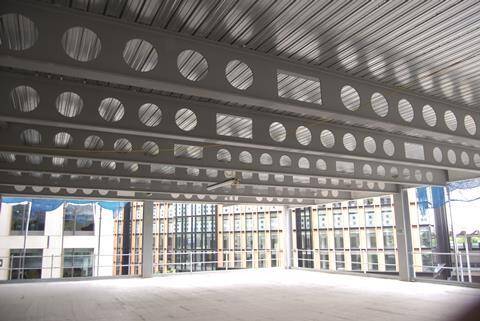
The depth of the long-span beams means that service openings, if required, are provided within the web of the beam. Openings can be circular, elongated or rectangular in shape, and can be up to 70% of the beam depth. They can have a length/depth ratio of up to 2.5. Web stiffeners may be required around holes. Shear studs are normally positioned in pairs, with reinforcing bars placed transversely across the beams to act as longitudinal shear reinforcement.
Advantages
(1) Large column-free areas.
(2) Service ducts pass through openings in the web of the beams
Disadvantages
(1) Deeper floor zones.
(2) Heavier steelwork than some short-span solutions.
(3) Fire protection required for 60 minutes fire resistance and above.
Composite beams with precast units
This system consists of rolled steel beams with shear studs welded to the top flange. The beams support precast concrete units with a structural concrete infill over the beam between the ends of the units, and often with an additional topping covering the units. The precast units are either hollow core, normally 150 – 260 mm deep, or they are solid planks of 75 mm to 100 mm depth.
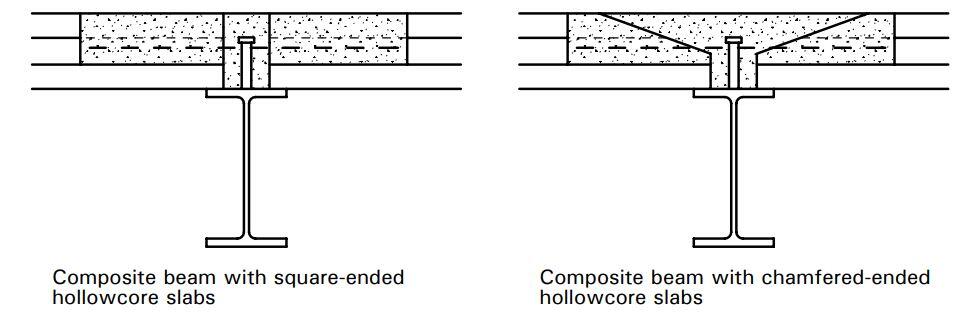
The shear studs and transverse reinforcement allow the transfer of the longitudinal shear force from the steel section into the precast units and the concrete topping, so that they can act together compositely. Composite design is not permitted unless the shear connectors are situated in an end gap (between the concrete units) of at least 50 mm. Minimum flange widths are crucial for providing a safe bearing for the precast units and room for the shear studs.
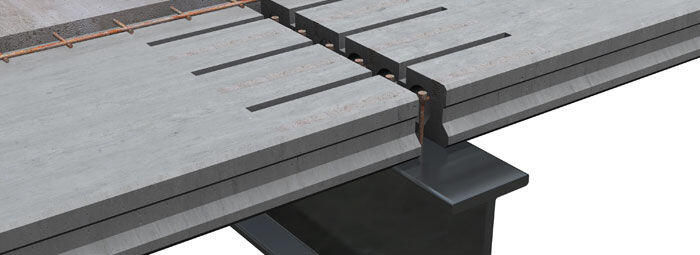
Advantages
(1) Fewer secondary beams, due to long-span precast units.
(2) Shear connectors for most beams can be welded off site, enabling larger stud diameters to be used and fewer site operations. It is usually convenient to weld studs to edge beams on site.
Disadvantages
(1) The beams are subject to torsion and may need stabilising during the construction stage.
(2) The precast units need careful detailing for adequate concrete encasement of shear connectors and installation of transverse reinforcement.
(3) More individual lifting operations compared to the erection of decking, and the erection sequence requires access for installation of the concrete units.
Non-composite beams with precast units
This system consists of rolled steel beams supporting precast concrete units. The precast units may be supported on the top flange of the steel beams, or, to reduce construction depth, supported on ‘shelf’ angles. Shelf angles are bolted or welded to the beam web, with an outstand leg long enough to provide adequate bearing of the precast units and to aid positioning of the units during erection. Precast concrete units are generally grouted in position. The units may have a screed (which may be structural), or may have a raised floor. The precast units are either hollow core, normally 150-260 mm deep, or they are solid planks of 75 mm to 100 mm depth.
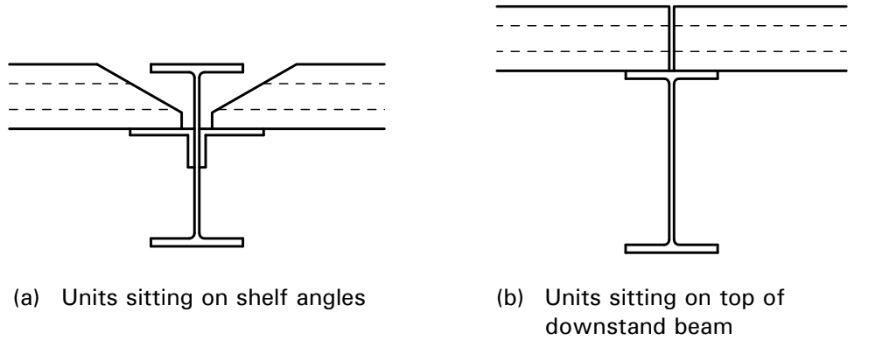
In order to meet robustness requirements, mesh and a structural topping may be required, or reinforcement concreted into hollow cores and passed through holes in the steel beam web. Tying may also be required between the concrete units and the edge beams.
Advantages
(1) Fewer secondary beams, due to long-span precast units.
(2) A simple solution involving basic member design.
Disadvantages
The beams are subject to torsion and may need stabilising during the construction stage.
More individual lifting operations compared with the erection of decking, and the erection sequence requires access for installation of the concrete units.
Source:
Brown D.G., Iles D.C., Yandzio E. (2009): Steel building design: Medium rise braced frames (In accordance with Eurocodes and the UK National Annexes). The Steel Construction Institute, UK
Hi,
Nice article, but I miss the Slimline Floor in your article. For more than 23 years Slimline is used in many high rise buildings with exelend fire and sound proofing, high building speeds, complete dry system and much more.
Regards,
Xander Vos
I think the Slimdek flooring system is a superior choice due to its strength, durability, slim profile, versatility, and construction efficiency. It combines steel and concrete to create a robust, space-efficient floor that can withstand heavy loads. With easy installation, it is both efficient and cost-effective, making it an outstanding solution for durable and visually appealing floors.
High-rise flooring is a unique blend of aesthetics, functionality, and innovation. The choices seem endless, ranging from exquisite hardwoods to sleek tiles and luxurious carpets.