To create hardened solid materials (also known as enhanced geomaterials), which have increased strength and stiffness, chemical agents (also known as binders) can be introduced into the ground and mixed with already-existing geomaterials such as soils and rocks. Lime, cement, silicate-based gel, and chemical solutions are examples of conventional binders.
Mixing and grouting are the two common techniques for introducing and mixing binders with soils. While the grouting method uses pipelines with high-pressure grouts, the mixing approach uses mechanical mixers or augers. Mixing can take place at depths (to form columns or walls) or at the surface (mostly for improving subgrade and base course). Deep soil mixing is the term used to describe the process of mixing binders (hardening agents) with soils at depths.
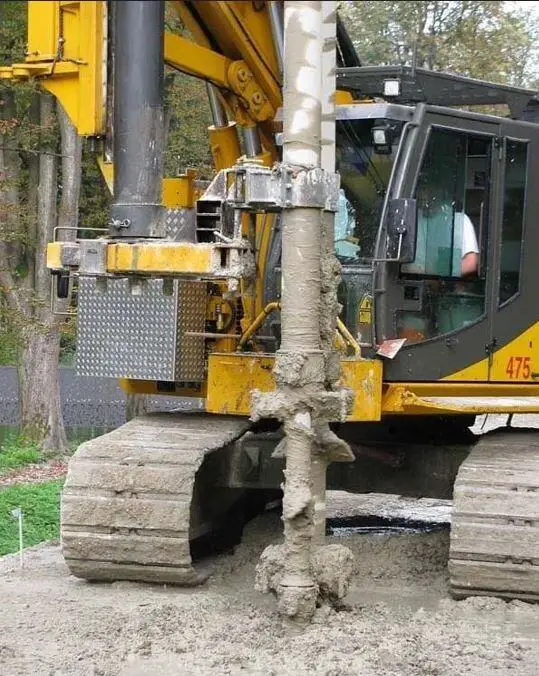
Basic Concepts of Deep Soil Mixing
The deep soil mixing (DSM) technique uses augers to mix in situ soil at depths with a binder (cement, lime, slag, or other binders). Either a wet method or a dry method can be used for deep soil mixing. Figure (a) below shows a wet method that utilises the binder as a slurry, whereas Figure (b) depicts a dry method that uses the binder as a powder.
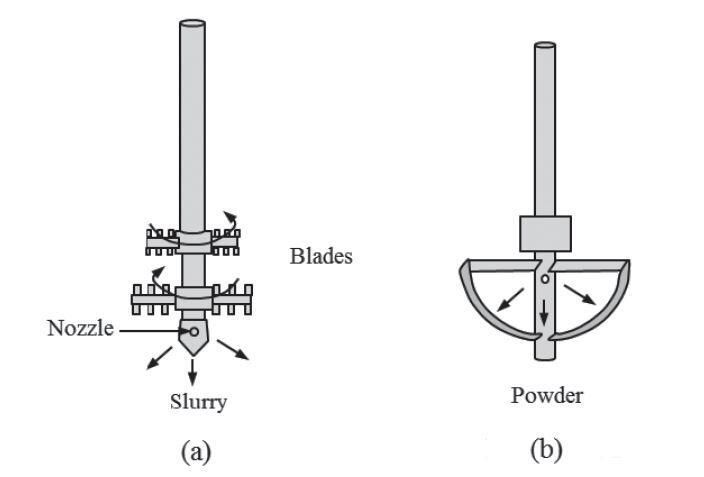
One to eight rotary hollow shafts with cutting and mixing blades above the tip may be present in the equipment for the wet method. Each hollow shaft allows the introduction of the binder slurry into the ground, which flows from the nozzle as the shaft either sinks into the soil or is removed. To increase the consistency of the soil-binder combination, some equipment features mixing blades that rotate in opposite directions.
Single or dual rotary shafts with cutting and mixing blades above the tip may be used in the dry method equipment. By using air pressure, the nozzle and each hollow shaft, the binder powder is delivered into the soil.
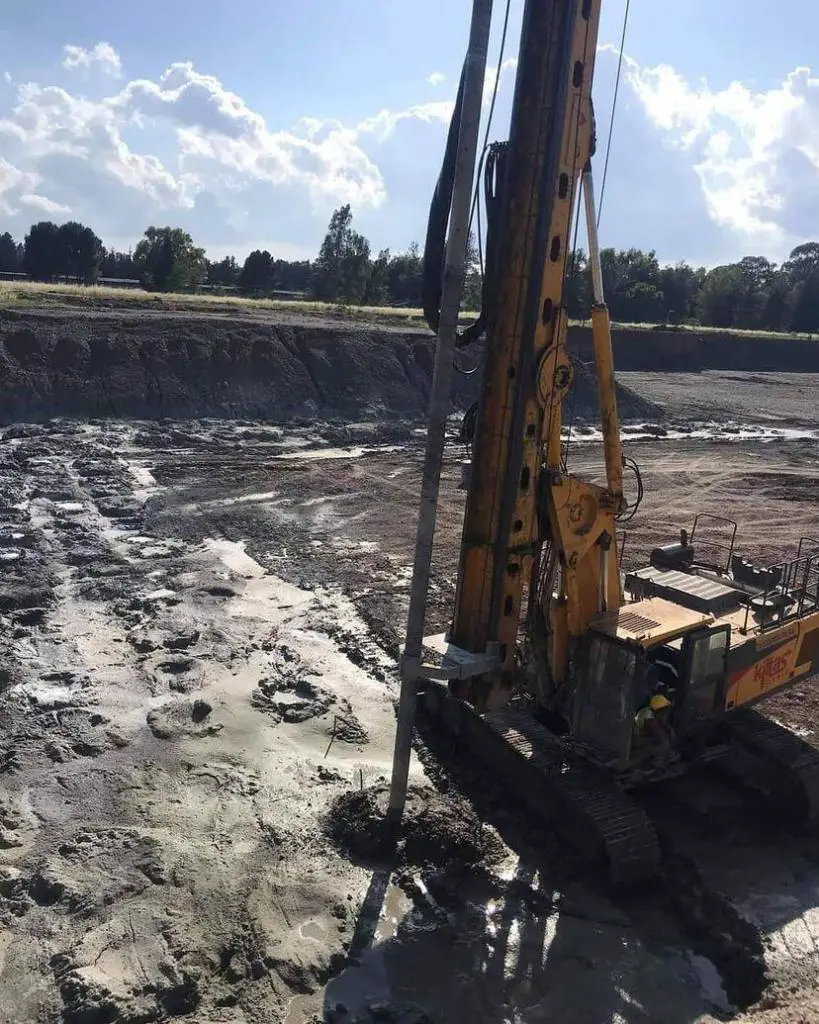
Rigid inclusions (such as concrete piles or spun piles) can be used to stiffen deep mixed columns in order to increase their stiffness and vertical and horizontal load capabilities. A composite column is another name for this kind of column. Some reseachers have demonstrated that after the installation of the column, the strength of the nearby sensitive clay generally recovered or even surpassed its pre-column strength. This has been attributed the long-term property changes to thixotropic hardening, consolidation, and diffusion of ions from the hardening agent (binder), and the short-term changes to soil disturbance and fracture.
Suitability of soils for Deep Mixing
Deep soil mixing has typically been utilized to strengthen soft cohesive soils, while it has also occasionally been used to reduce permeability and prevent the liquefaction of cohesionless soils. The ideal soil characteristics for deep mixing are shown in the Table below.
Property | Favorable Soil Chemistry |
pH | Should be greater than 5 |
Natural water content | Should be less than 200% (dry method) and less than 60% (wet method) |
Organic content | Should be less than 6% (wet method) |
Loss on ignition | Should be less than 10% |
Humus content | Should be less than 1.0% |
Electrical conductivity | Should be greater than 0.04 mS/mm |
If the soil is very hard, very dense, and has rocks or other obstructions, deep soil mixing becomes challenging. Due to the massive machinery utilised in most projects, deep mixing typically requires open site access and overhead clearance. In maritime operations, deep mixing can go as deep as 70 metres, while on land it can go as deep as 30 metres.
Applications of Deep Soil Mixing
Columns from deep soil mixing have been used for many applications in soft soils:
- support of superstructures, including buildings, walls, embankments, and the likes
- waterfront and marine applications including quay walls, wharf structures, and breakwaters
- stabilization of slopes
- lateral support
- containment of water and pollutant,
- liquefaction mitigation, and,
- vibration reduction.
Generally, deep soil mixing columns are utilised in various applications to reduce vibration, contain water and pollutant flow, improve slope stability, reduce settlement, increase bearing capacity, and provide lateral support.
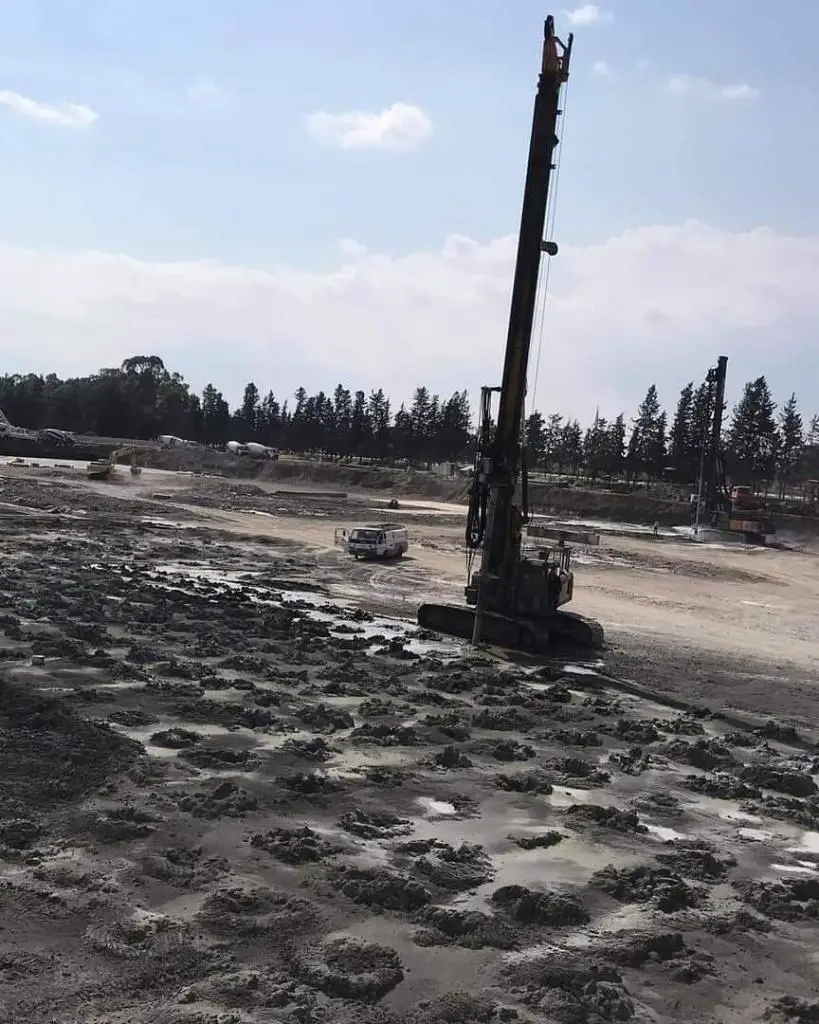
As seen in the Figure below, there are commonly four distinct arrangements for DM columns. When an area replacement ratio is relatively low, such as less than 50%, individual columns are used. The main uses of individual columns have been to improve bearing capacity and reduce settlement. When a high area replacement ratio, such as more than 50%, is required, block patterns are employed to bear substantial vertical and/or horizontal loads. Large marine structures have mostly benefited from the usage of block patterns to increase stability. This design pattern has also been applied to waste containment to stop dangerous substances from leaching.
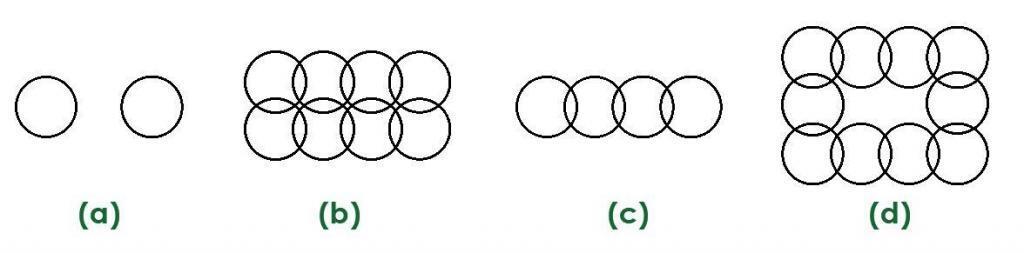
For retaining walls to provide lateral support, seepage walls to stop seepage, curtain walls to hold waste, and walls perpendicular to the centerline of embankments to promote stability, panel or wall patterns have been widely utilised. Between the wall pattern and the block pattern is the grid pattern. It can be utilised in applications that call for block and wall layouts. The grid layout has a special use in preventing sandy soil liquefaction. The cells of grids are where the liquefiable soils are contained.
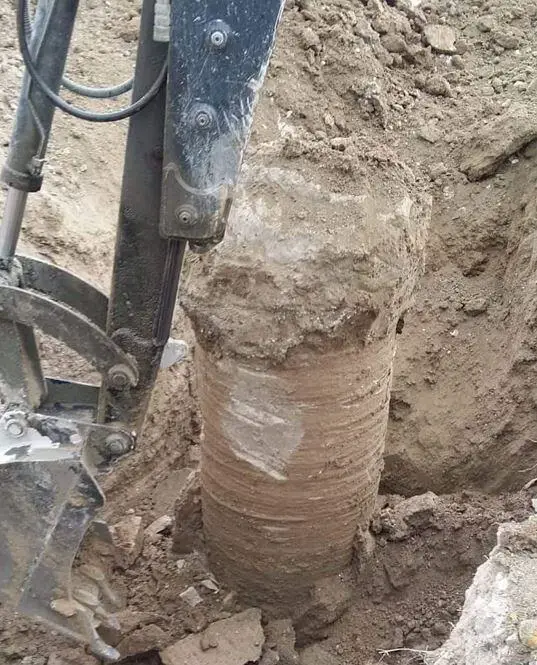
In recent years, embankments over weak foundations have primarily been supported by columns. One of the most significant applications of column technologies is thought to be this one. Deep mixed columns have also been progressively combined with other technologies, including rigid piles, PVDs, and geosynthetic reinforcement.
The geosynthetic reinforcement placed on top of the columns serves as a bridge layer to distribute the embankment load to the columns and lessen the variance in column settlement. Geosynthetic-reinforced column-supported embankments are frequently used for the following purposes:
(1) bridge approach
(2) roadway widening
(3) subgrade improvement, and
(4) support of storage tanks
Advantages and Limitations of deep soil mixing
The deep mixing method has the following advantages:
- Applicable for most soil types
- Installed at great depths
- Relatively fast installation
- Low noise and vibration level
- Formation of a DSM wall for earth retaining and water barrier at the same location and time
- Less spoil soil, especially for the dry method
However, the deep soil mixing method may have the following limitations:
- Relatively high mobilization cost
- High variability in column quality
- Lack of standardized quality control methods
Thank you for the in-depth look at DSM! I appreciate the insight, and this is a very thorough introduction, for the layman!
I am interested in some of the hillside stabilization applications; how does DSM specifically work for that? Does it reduce lateral earth pressure, or bind the soil together? The grout method I understand is a high-pressure method, but does the mechanical “mixing” implementation begin stressing the soils surrounding it? What sort of QC exists, even if it is not standardized at this point?