Light gauge steel framing is typically based on the use of standard C or Z-shaped steel sections produced by cold rolling from strip steel. In general, hot-rolled steel sections used in fabricated steelwork, such as Universal Beams, are different from cold-formed steel sections. Galvanized steel with a typical thickness of 0.9 to 3.2 mm is used in cold-formed sections to prevent corrosion.
Cold-formed steel sections are widely utilised in many construction industries, including mezzanine floors, commercial, industrial, and hotel buildings. They are also becoming more popular in the residential market. In North America, Australia, and Japan, light steel frame is already well-established in the residential home construction industry. This article provides information on the various types of light gauge steel frame construction methods for residential buildings.
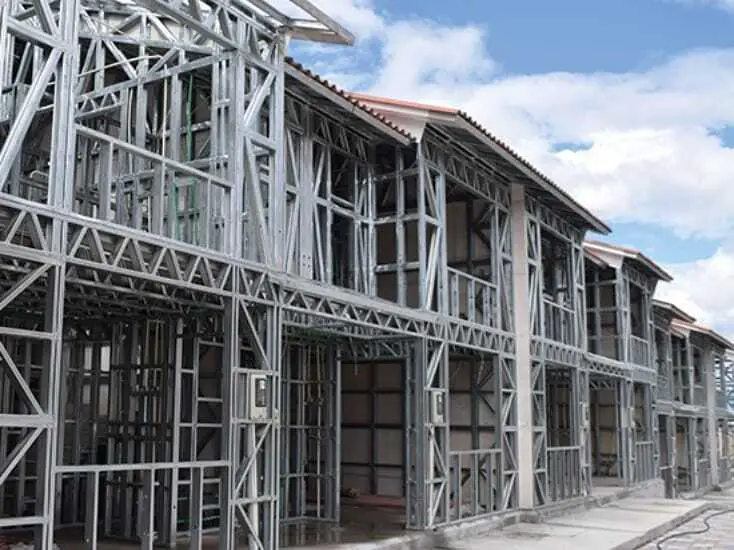
Methods of Construction using Light Gauge Steel
Cold-formed sections, which can be prefabricated into panels or modules or constructed on-site using a variety of connecting techniques, are the fundamental building blocks of the light steel gauge frame. The various types of construction are discussed in the sections that follow.
‘Stick-build’ construction
In this construction approach (shown in Figure 2), discrete members are put together on-site to create columns, walls, rafters, beams, and bracing, which are then covered with cladding, internal lining, and other components. Although the elements are typically shipped pre-punched and cut to length, connections are done on-site using bolts, screws, or other suitable site procedures.
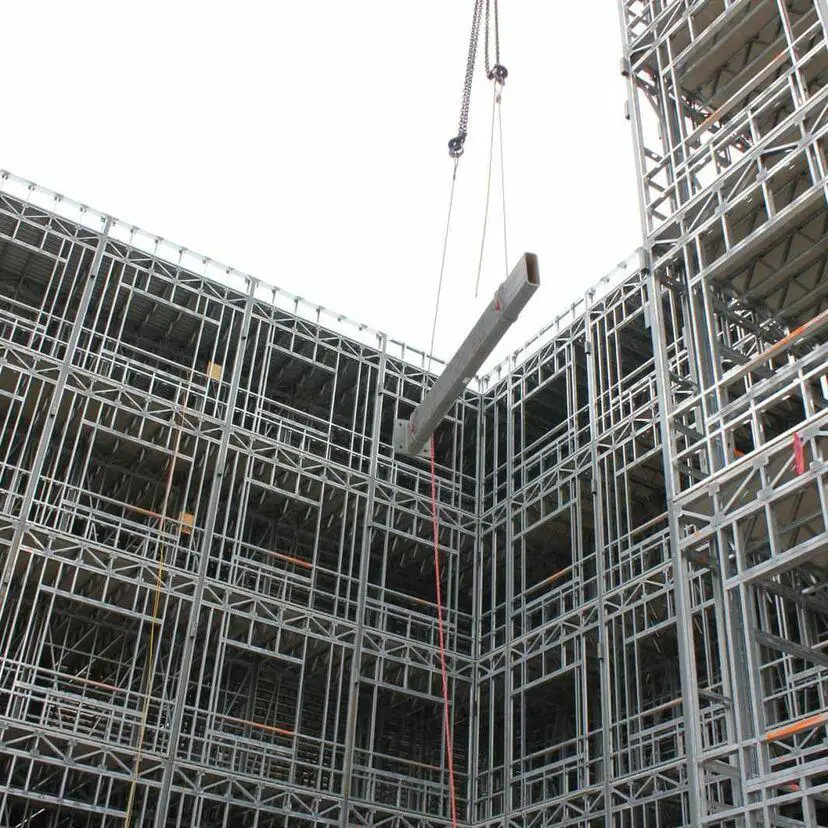
The main advantages of ‘stick-build’ construction are:
- construction tolerances and modifications can be accommodated on site
- connection techniques are relatively simple
- manufacturers do not require the workshop facilities associated with the panel or modular construction
- large quantities of light steel members can be densely packed and transported in single loads
- components can be easily handled on-site.
In comparison to the other methods, “stick-build” construction is typically labour-intensive on-site, but it can be effective in a complex building when prefabrication is difficult. In North America and Australia, where there is a strong infrastructure of trained contractors, this type of building is common. This is a result of the widespread use of power tools in the craft of timber frame construction. Traditional timber contractors have easily transitioned to light gauge steel frames in these nations.
Panel Construction
As shown in Figure 3, wall panels, floor cassettes, and roof trusses can be manufactured in a factory and then erected on-site. Panels are fabricated in specialised jigs for precision. To speed up building on-site, some finishing materials may be used in the factory. Steel pieces alone or with facing materials and insulation placed at the factory can make up panels. The panels are connected on-site utilising customary methods (bolts or self-drilling screws).
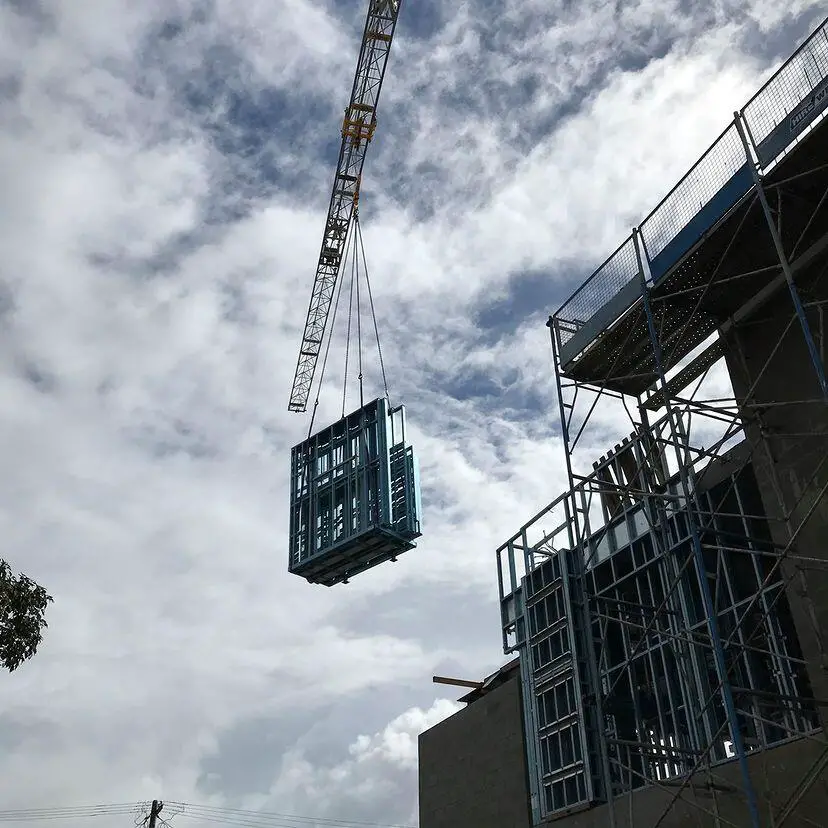
The main advantages of panel or sub-frame construction are:
- speed of erection of the panels or sub-frames
- quality control in production
- reduced site labour costs
- scope for automation in factory production.
The fact that the panels are prefabricated in a manufacturing environment improves their geometrical precision and dependability compared to stick-build construction. To achieve quick panel assembly and to reach the highest level of building efficiency, precise foundation planning and installation are essential.
Modular Construction
In modular construction, units can be brought to the site with all interior finishes, fixtures, and fittings already installed because they are totally constructed in the factory, as shown in Figure 4. To create a stable final construction, units may be piled one above the other or side by side.
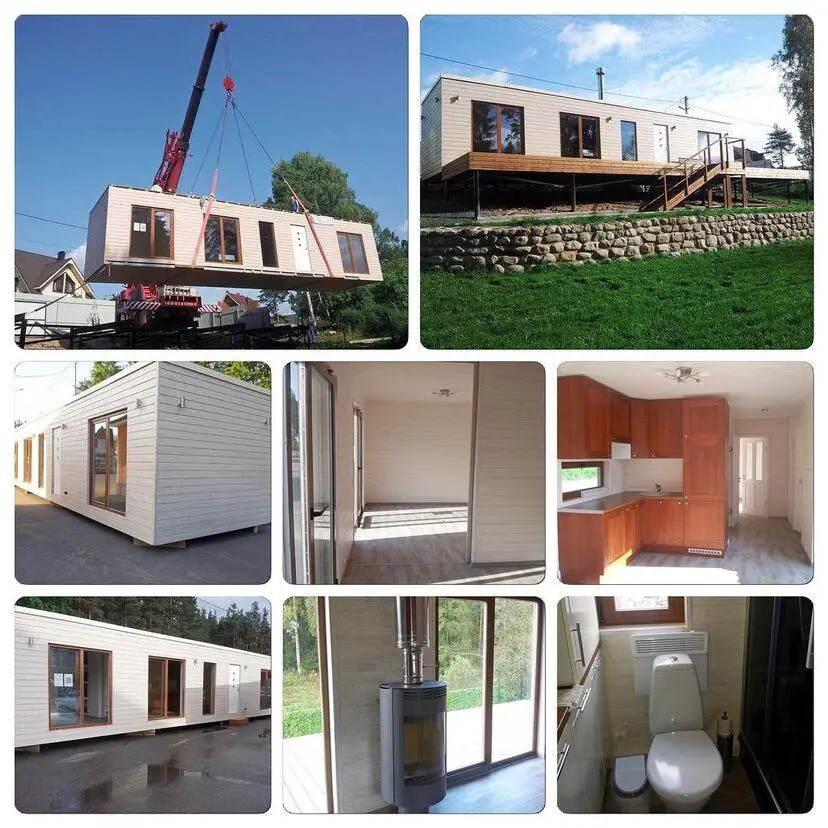
Where massive production runs for the same basic configuration of modular unit are feasible, modular building is most cost-effective. This is possible because the costs of prototype and setup, which are largely scale-independent, may be distributed over numerous units.
Platform and ‘balloon’ construction
“Stick-build” or panel components can be put together in either “platform” or “balloon” construction. The walls are not physically continuous in platform construction since the floors and walls are created one level at a time. In some types of construction, loads are carried from the walls above to the walls below through the floor joists.
The wall panels used in “balloon” construction are frequently significantly larger and extend over multiple stories. These panels require temporary bracing while the floors are being placed since they are more challenging to assemble than single-storey height panels. The fundamental benefit of this strategy is that loads are carried directly from the walls above to those below. The external cladding or finishes are often installed and affixed to the frames on-site in both types of construction.
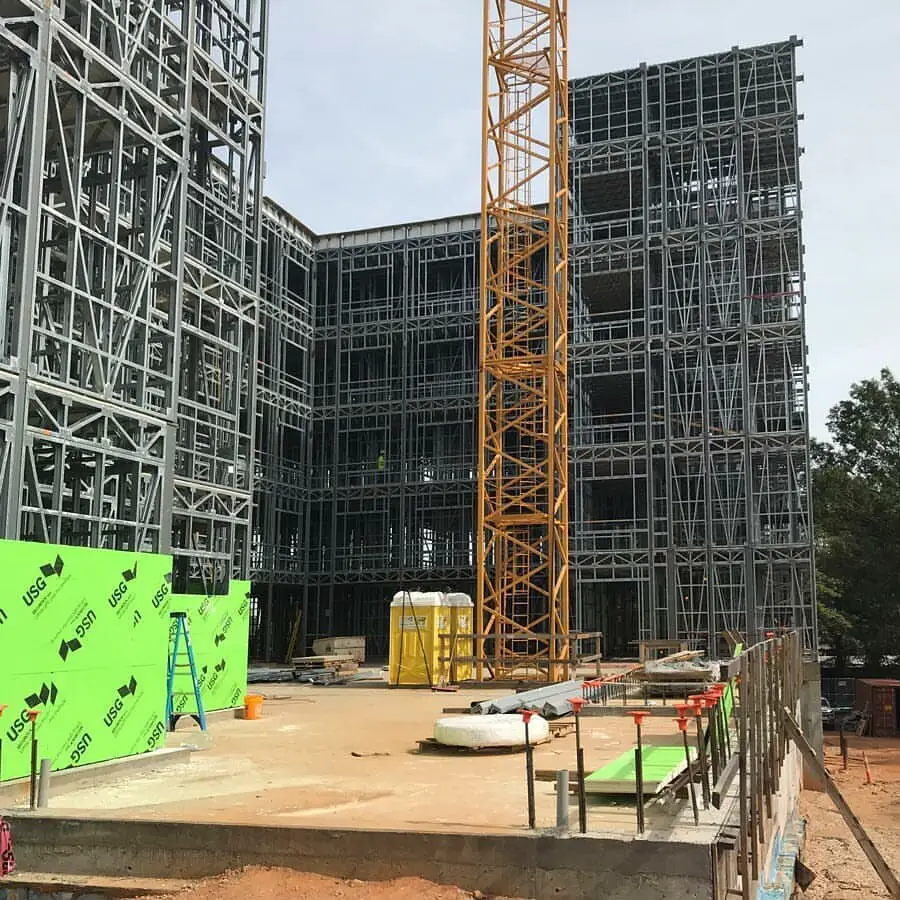
plz revert