Non-linear analysis can be used when all of the members, elements and support springs are linear except for cables and/or preloaded truss members. This analysis is based on applying the load in steps with equilibrium iterations to converge at each step. In Staad Pro software, the iteration continues at each step until the change in deformations is small before proceeding to the next step. If not converged, then the solution is stopped. The user can then select more steps or modify the structure and rerun.
This method assumes small displacement theory for all members/trusses/elements other than cables and preloaded trusses. The cables and preloaded trusses can have large displacement and moderate/large strain. Pretension is the force necessary to stretch the cable/truss from its unstressed length to enable it to fit between the two end joints. Alternatively, you may enter the unstressed length for cables.
The analysis sequence is as follows:
(1) Compute the unstressed length of the nonlinear members based on joint coordinates, pretension, and temperature.
(2) Member/Element/Cable stiffness is formed. Cable stiffness is from EA/L and the sag formula plus a geometric stiffness based on current tension.
(3) Assemble and solve the global matrix with the percentage of the total applied load used for this load step.
(4) Perform equilibrium iterations to adjust the change in directions of the forces in the nonlinear cables, so that the structure is in static equilibrium in the deformed position. If force changes are too large or convergence criteria not met within 15 iterations then stop the analysis.
(5) Go to step 2 and repeat with a greater percentage of the applied load. The nonlinear members will have an updated orientation with new tension and sag effects.
(6) After 100% of the applied load has converged then proceed to compute member forces, reactions, and static check.
Note that the static check is not exactly in balance due to the displacements of the applied static equivalent joint loads.
Non-linear Cable Analysis Parameters
If you open the cable analysis command on Staad Pro, you will see cable analysis parameters which can be confusing at first sight. Staad Pro advanced training manual offers some insight on the definition of the parameters and the values to use.
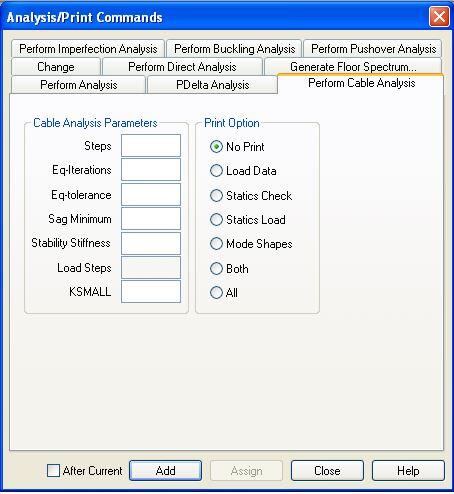
Steps: The number of steps if entered should be in the range 5 to 145.
Eq-iterations: This is the maximum number of iterations permitted in each load step. The default value is 15 and should be in the range of 10 to 30.
Eq-tolerance: This is he convergence tolerance for the above iterations. Default value is 0.0005.
Sag minimum: Cables may sag when tension is low. This is accounted for by reducing the E value. Sag minimum may be between 1.0 (no sag E reduction) and 0.0 (full sag E reduction). Default is 1.0. If sag minimum is entered, it should be in the range 0.7 to 1.0 for a relatively simple process. As soon as SAGMIN becomes less than 0.95 the possibility exists that a converged solution will not be achieved without increasing the steps or the pretension loads. The Eq iterations may need to be 30 or more. The Eq tolerance may need to be greater or smaller.
Stability stiffness: A stiffness matrix value that is added to the global matrix at each translational direction for joints connected to cables and nonlinear trusses for the first Load Steps. The amount added linearly decreases with each of the Load Steps (Load Step is 1.0 if omitted). If stability stiffness is entered, use 0.0 to 2.0 but the default value is 0. For Load Steps use a maximum value of 145.
K small stiffness: This is a stiffness matrix value, that is added to the global matrix at each translational direction for joints connected to cables and nonlinear trusses for every load step. If entered, use values between 0.0 to 1.0 but the default value is 0.0. This parameter alters the stiffness of the structure.
Analysis Example
Let us analyse the cable stayed canopy loaded as shown below. The structure comprises of UB 254 x 102 x 22 stanchions supporting cantilevered trusses of UA 50 x 50 x 5 sections. Purlins on the trusses are made of channel sections CH 100 x 150 x 10. Cables are made of 30 mm diameter steel wires and UB 127 x 76 x 13 are used to brace the stanchions in the lateral directions. The loading applied on the structure is the self weight and UDL of 1.5 kN/m on the purlins.
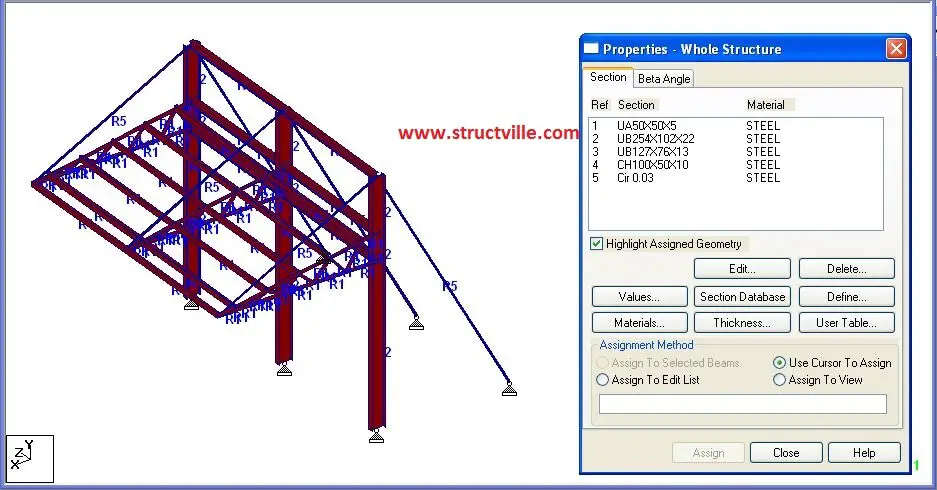
In the analysis, an initial tension of 0.1 kN was applied in the cable members using the default parameters (leaving the cable analysis parameters blank). However, the load case refused to converge after iterations. The parameters that gave acceptable convergence are shown below.
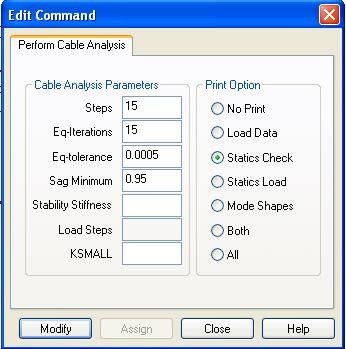
Analysis Results
The displacement of the cable stayed canopy is shown below;
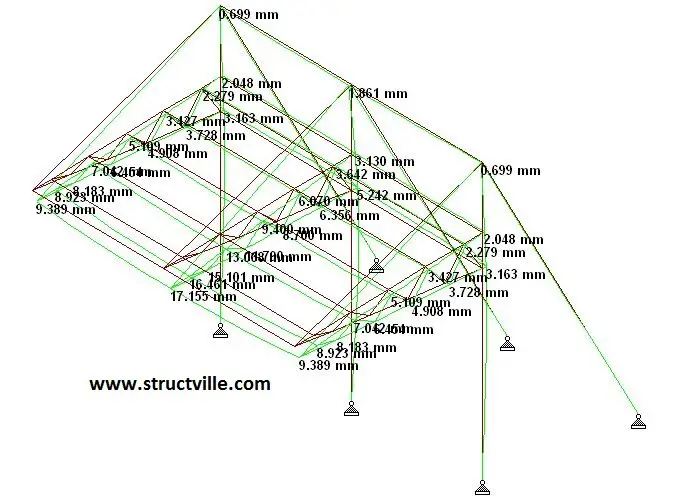
The maximum displacement in the truss was observed to be 17.155 mm.
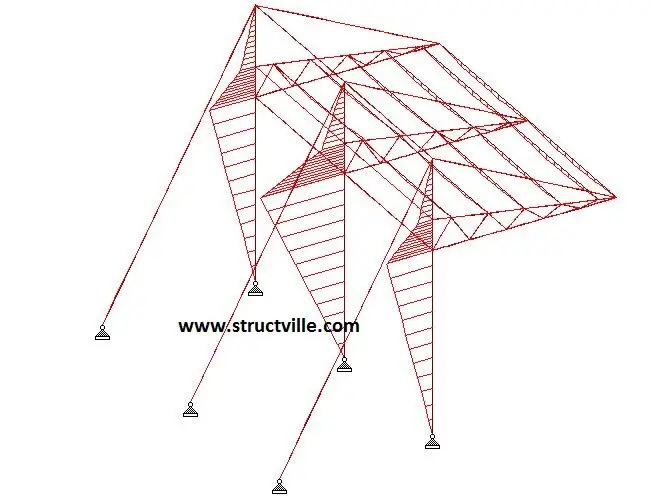
The bending moment in the intermediate column was observed to be 27.2 kNm. The shear force in the same column was observed to be 9.08 kN with an axial force of 45.5 kN.
The axial forces in the cables and trusses of the intermediate members are shown below;
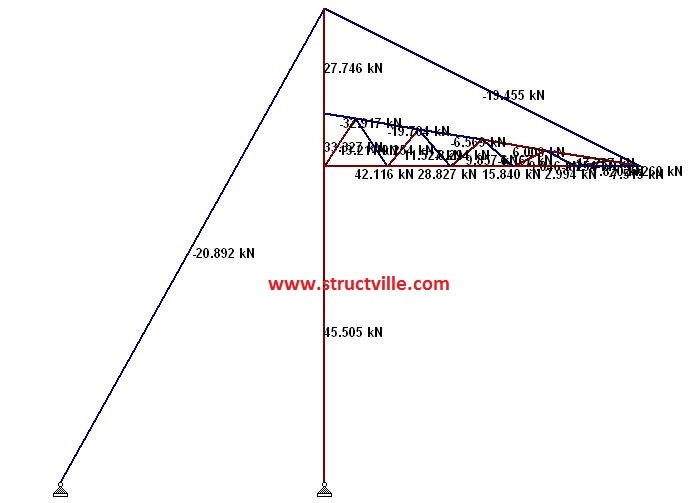
The axial forces in the cables and trusses of the end members are shown below;
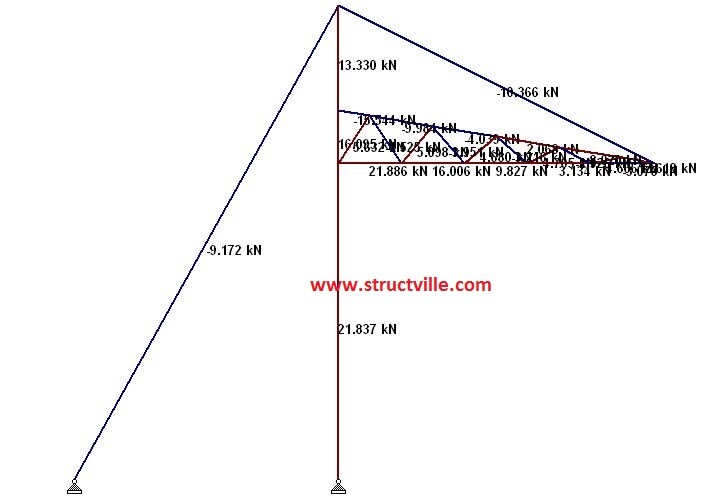
Thank you for visiting Structville today. God bless you.