Self-compacting concrete (SCC) is a special type of concrete that has the ability to consolidate under gravity, fill up all required spaces, and produce dense and smoothly finished concrete when placed in formwork without the need for any external vibration. This special property of self-compacting concrete is due to the excellent workability it possesses in its fresh state, and the ability of the concrete to remain cohesive without segregation and bleeding when placed.
Self-compacting concrete was developed in Japan in the 1980s, and has found wide applications in the construction industry due to its numerous advantages. As a result of its highly flowable nature, SCC can settle into formworks and fill up heavily reinforced, congested, narrow, and deep sections by means of its own weight. Unlike conventional concrete, SCC does not require compaction using external force from mechanical equipment such as immersion vibrators.
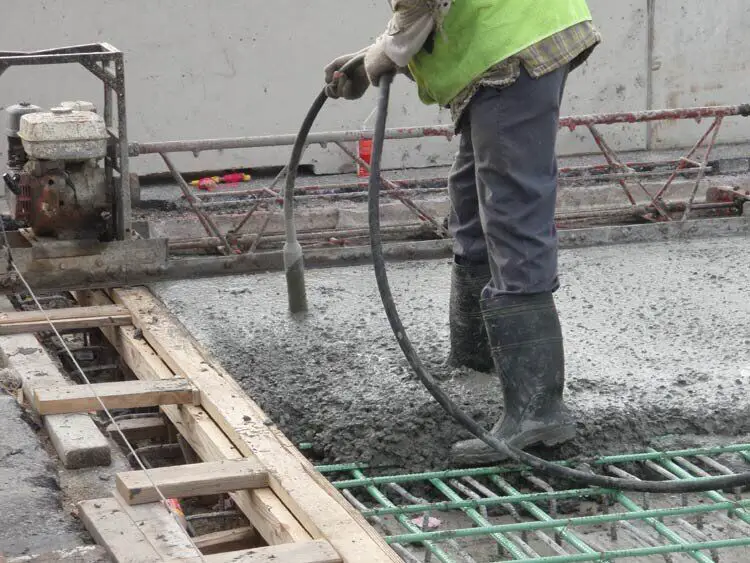
The common advantages of self-compacting concrete (SCC) are as follows;
- Less labour is required for the vibration and compaction of concrete on site
- Formwork congested with reinforcement can be cast with more ease
- Narrow and/or deep forms can be cast without the formation of honeycombs
- There is no risk of formwork damage due to vibration as commonly encountered in conventional concrete placement
- There are reduced health and safety concerns on site
- The working environment is improved due to little or no noise from concrete vibrating equipment
In many cases, self-compacting concrete is usually associated with high-strength concrete, hence the term ‘high-performance self-compacting concrete’ (HPSCC). High-performance self-compacting concrete can have compressive strength between 60 – 100 MPa. Ultra high-performance concrete can have compressive strength up to 150 MPa. High-performance concrete is expected to possess the following qualities;
- High strength
- High durability
- Low shrinkage and creep
- Easy to place and consolidate
- Cost-effective
When compared with ordinary concrete, SCC is usually produced using a large amount of cement/fillers, superplasticizer, and/or other viscosity modifying admixtures. The supplemented binder content is associated with other cement replacement materials (CRMs) such as fly ash (FA), ground granulated blast furnace slag (GGBFS), silica fume (SF), rice husk ash (RHA), etc. The incorporation of CRMs is usually to improve the workability of the concrete, and the properties of the hardened concrete. There are limits to the size of aggregates also, with a recommended maximum aggregate size of 25 mm.
Therefore, for SCC, the following properties are required;
- At the fresh state: Good workability without segregation
- At the early state: No initial defects or honeycombs
- At the hardened state: Good strength and resistance to external attacks
Tests for Self-Compacting Concrete
According to the European guidelines for self-compacting concrete, none of the test methods in the current EN 12350 series ‘Testing fresh concrete’ are suitable for the assessment of the key properties of fresh SCC. The filling ability and stability of self-compacting concrete in the fresh state can be defined by four key characteristics. Each characteristic can be addressed by one or more test methods as shown in the table below;
Characteristics | Preferred test |
Flowability | Slump-flow test |
Viscosity (assessed by rate of flow) | T500 Slump-flow test or V-funnel test |
Passing ability | L-box test |
Segregation | Segregation resistance (sieve) test |
There are other appropriate tests that can be done on fresh SCC. Tests such as Orimet and O-funnel test can be used to assess the viscosity of SCC. U-box and J-ring tests can also be used to determine the passing ability of fresh SCC, while penetration and settlement column tests can also be used to determine the segregation resistance.
Slump-flow value describes the flowability of a fresh mix in unconfined conditions. It is a sensitive test that will normally be specified for all SCC, as the primary check that the consistence of the fresh concrete meets the specification. The slump flow value is usually obtained from the slup test.
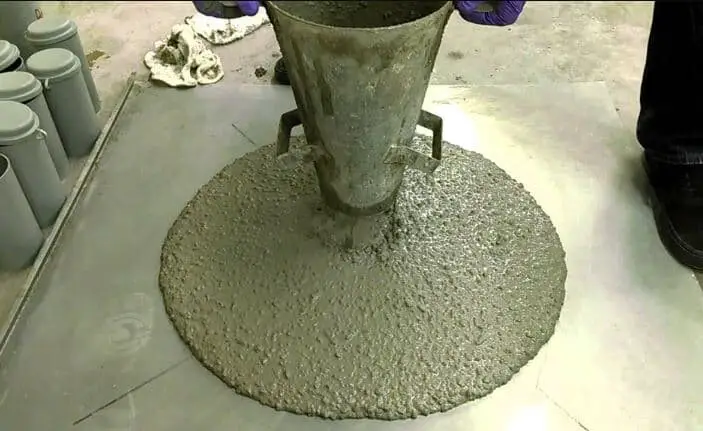
The viscosity of SCC can be assessed by the T500 time during the slump-flow test or assessed by the V-funnel flow time. The time value obtained does not measure the viscosity of SCC but is related to it by describing the rate of flow. Concrete with low viscosity will have a very quick initial flow and then stop. Concrete with high viscosity may continue to creep forward over an extended time.
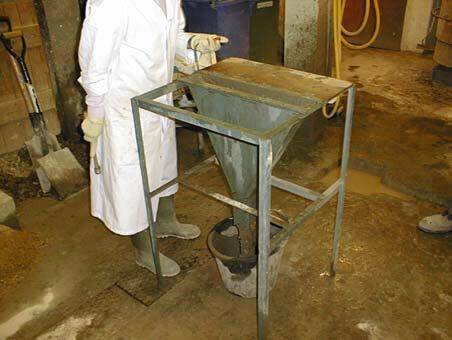
Passing ability describes the capacity of the fresh mix to flow through confined spaces and narrow openings such as areas of congested reinforcement without segregation, loss of uniformity, or causing blocking. In defining the passing ability, it is necessary to consider the geometry and density of the reinforcement, the flowability/filling ability, and the maximum aggregate size. This can be evaluated using the L-box test.
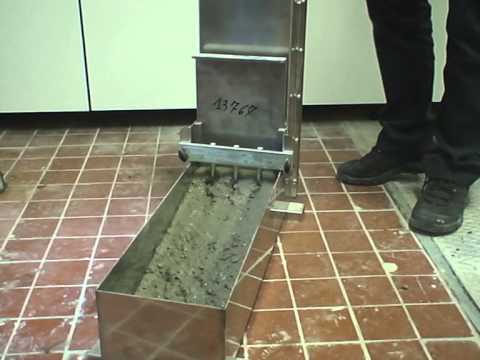
Segregation resistance is fundamental for SCC in-situ homogeneity and quality. SCC can suffer from segregation during placing and also after placing but before stiffening. Segregation which occurs after placing will be most detrimental in tall elements but even in thin slabs, it can lead to surface defects such as cracking or a weak surface.
Segregation resistance becomes an important parameter with higher slump-flow classes and/or the lower viscosity class, or if placing conditions promote segregation. If none of these apply, it is usually not necessary to specify a segregation resistance class.
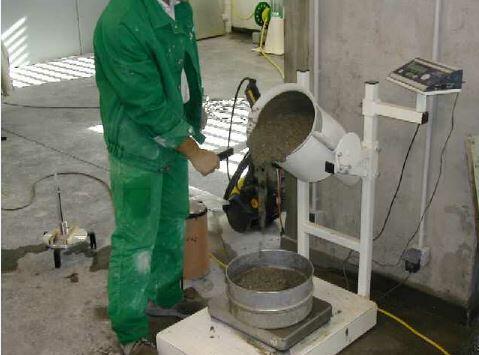
Consistency Requirements of Self-Compacting Concrete
Slump Flow
The European Guidelines for Self Compacting Concrete classifies the slump flow of SCC into;
- SF1 (550 – 650 mm)
- SF2 (660 – 750 mm), and
- SF3 (760 – 850 mm).
SF1 (550 – 650 mm) is appropriate for unreinforced or slightly reinforced concrete structures that are cast from the top with free displacement from the delivery point (e.g. housing slabs), casting by a pump injection system (e.g. tunnel linings), and sections that are small enough to prevent long horizontal flow (e.g. piles and some deep foundations).
SF2 (660 – 750 mm) is suitable for many normal applications (e.g. walls, columns)
SF3 (760 – 850 mm) is typically produced with a small maximum size of aggregates (less than 16 mm) and is used for vertical applications in very congested structures, structures with complex shapes, or for filling under formwork. SF3 will often give a better surface finish than SF2 for normal vertical applications but segregation resistance is more difficult to control.
Viscosity
The viscosity of SCC is classified into:
- VS1 (V-funnel time ≤ 8 seconds), and
- VS2 (V-funnel time between 9 -25 seconds)
VS1/VF1 has good filling ability even with congested reinforcement. It is capable of self-levelling and generally has the best surface finish. However, it is more likely to suffer from bleeding and segregation.
VS2/VF2 has no upper class limit but with increasing flow time it is more likely to exhibit thixotropic effects, which may be helpful in limiting the formwork pressure or improving segregation resistance. Negative effects may be experienced regarding surface finish (blow holes) and sensitivity to stoppages or delays between successive lifts.
Passing Ability
It is important to define the confinement gap when specifying SCC. The defining dimension is the smallest gap (confinement gap) through which SCC has to continuously flow to fill the formwork. This gap is usually but not always related to the reinforcement spacing. Unless the reinforcement is very congested, the space between reinforcement and formwork cover is not normally taken into account as SCC can surround the bars and does not need to continuously flow through these spaces.
Examples of passing ability specifications are given below:
- PA 1 structures with a gap of 80 mm to 100 mm, (e.g. housing, vertical structures)
- PA 2 structures with a gap of 60 mm to 80 mm, (e.g. civil engineering structures)
With L-box test;
PA1 (≥ 0.80 with 2 rebars)
PA2 (≥ 0.80 with 3 rebars)
For thin slabs where the gap is greater than 80 mm and other structures where the gap is greater than 100 mm no specified passing ability is required. For complex structures with a gap less than 60 mm, specific mock-up trials may be necessary.
Segregation Resistance
Segregation resistance of SCC is classified into;
- SR1 (segregation resistance ≤ 20%), and
- SR2 (segregation resistance ≤ 15%).
SR1 is generally applicable for thin slabs and for vertical applications with a flow distance of less than 5 metres and a confinement gap greater than 80 mm.
SR2 is preferred in vertical applications if the flow distance is more than 5 metres with a confinement gap greater than 80 mm in order to take care of segregation during flow. SR2 may also be used for tall vertical applications with a confinement gap of less than 80 mm if the flow distance is less than 5 metres but if the flow is more than 5 metres a target SR value of less than 10% is recommended.
Mix Design Approach for Self-Compacting Concrete
Laboratory trials should be used to verify the properties of the initial mix composition with respect to the specified characteristics and classes. If necessary, adjustments to the mix composition should then be made. Once all requirements are fulfilled, the mix should be tested at full scale in the concrete plant and if necessary at the site to verify both the fresh and hardened properties.
Mix design principles
To achieve the required combination of properties in fresh SCC mixes:
- The fluidity and viscosity of the paste is adjusted and balanced by careful selection and proportioning of the cement and additions, by limiting the water/powder ratio and then by adding a superplasticiser and (optionally) a viscosity modifying admixture. Correctly controlling these components of SCC, their compatibility and interaction is the key to achieving good filling ability, passing ability and resistance to segregation.
- In order to control temperature rise and thermal shrinkage cracking as well as strength, the fine powder content may contain a significant proportion of type l or ll additions to keep the cement content at an acceptable level.
- The paste is the vehicle for the transport of the aggregate; therefore the volume of the paste must be greater than the void volume in the aggregate so that all individual aggregate particles are fully coated and lubricated by a layer of paste. This increases fluidity and reduces aggregate friction.
- The coarse to fine aggregate ratio in the mix is reduced so that individual coarse aggregate particles are fully surrounded by a layer of mortar. This reduces aggregate interlock and bridging when the concrete passes through narrow openings or gaps between reinforcement and increases the passing ability of the SCC.
The mix design is generally based on the approach outlined below:
- Evaluate the water demand and optimise the flow and stability of the paste
- Determine the proportion of sand and the dose of admixture to give the required robustness
- Test the sensitivity for small variations in quantities (the robustness)
- Add an appropriate amount of coarse aggregate
- Produce the fresh SCC in the laboratory mixer, perform the required tests
- Test the properties of the SCC in the hardened state
- Produce trial mixes in the plant mixer.
Primary Source of Information:
SCC European Project Group (2005): The European Guidelines for Self-Compacting Concrete (Specification, Production and Use). https://www.theconcreteinitiative.eu/images/ECP_Documents/EuropeanGuidelinesSelfCompactingConcrete.pdf