Raft foundation is a type of shallow foundation that is provided in areas where the soils have a low bearing capacity, or where high superstructure load is anticipated such that individual pad foundations will overlap. A typical raft foundation is more expensive to construct than an equivalent pad foundation for a given area in a building. The aim of this article is to show the typical cost of constructing a raft foundation in Nigeria.
In the first place, there are different types of raft foundations such as flat raft foundation, beam and slab raft foundation, cellular raft foundation, etc. Each of these types of raft can be employed depending on the circumstances and design specifications, but the most common type of raft foundation employed for duplexes (most residential buildings) in Nigeria is the beam and slab raft foundation because of the favourable economic advantages it presents to the homeowner and the client.
The cost of constructing a raft foundation is influenced by;
- the cost of setting out
- environmental considerations
- the member sizes (depth and width of beams and slabs)
- the quantity of reinforcements required
- formwork requirements and the complexity of the construction
- the volume of excavation required
- backfilling the substructure
- Other substructure requirements such as compacting, hardcore (if required), damp proof membrane, etc
- availability and cost of labour, and
- the cost of construction materials in the area
The thickness of the raft slab and the depth and width of the ground beams will determine the volume of concrete required for executing the raft foundation. This is is actually a function of the design specifications, and will significantly affect the overall cost of the construction. Standard design drawings that will be economical and also satisfy all requirements can be provided by Structville Integrated Services Limited (info@structville.com). The cost of executing concrete works in Nigeria varies and is usually influenced by the price of cement, and aggregates.
Reinforcement requirements for a raft foundation are also determined by the design engineer, and the quantity provided will have a significant impact on the cost of the project too. The major cost impact will come from the cost of purchasing, cutting, bending, and installing the reinforcements according to the design drawing. The cost of executing reinforcement works will depend on the type of reinforcement, the quantity required, and the cost of labour.
The carpenters will also charge for the cost of fixing the formwork of the ground beams, and the edge formwork for receiving the raft slab. The cost of the marine boards, planks, 2″ x 3″ wood, props, nails, etc will also be borne by the client.
In areas of high water table, the cost of controlling groundwater so that construction can be carried out in the dry will also affect the cost of the raft foundation. This will also influence the cost of excavation of the trenches to receive the ground beams.
Let us show with an example, the typical cost of constructing the raft foundation of a duplex building in Nigeria. The design drawings are shown below;
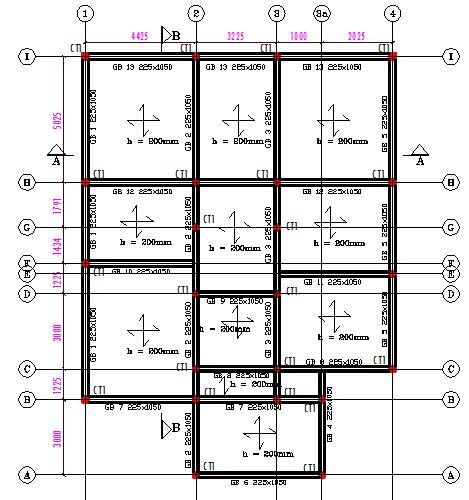
The properties of the raft foundation are as follows;
Thickness of the raft slab = 200 mm
Dimensions of the ground beams = 1050 x 230 mm
Dimensions of the columns = 230 x 230 mm
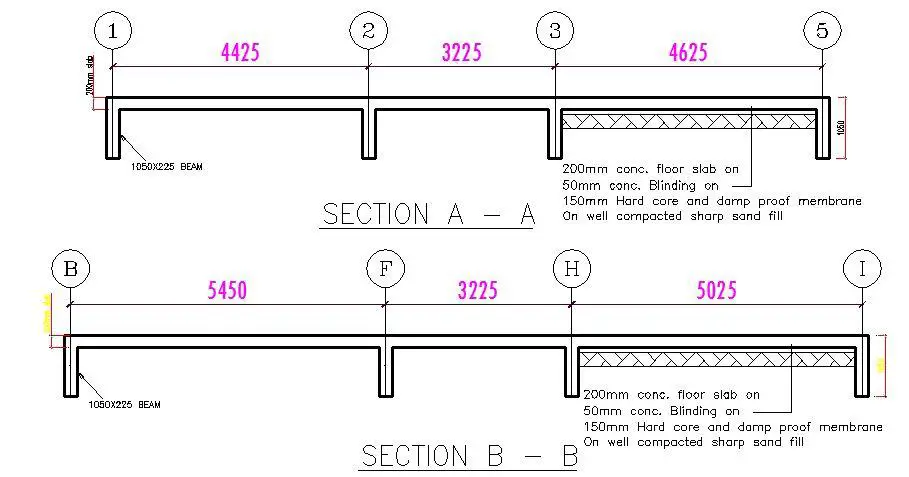
The typical ground beam reinforcement details are shown below;
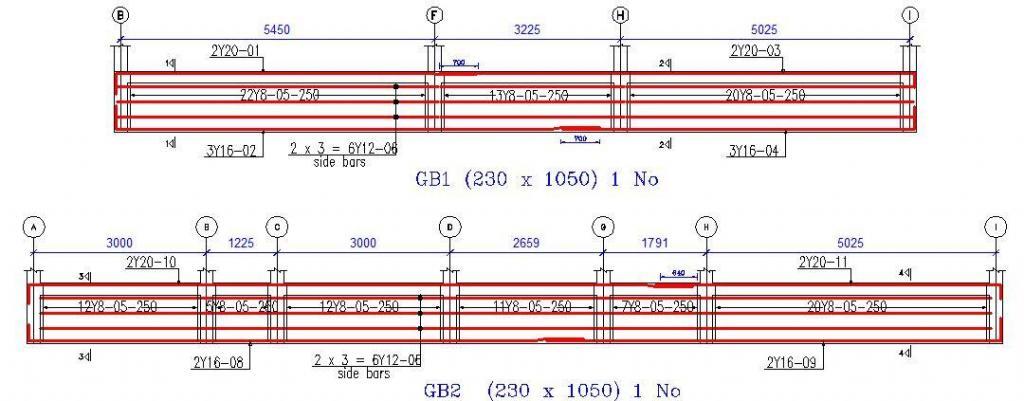
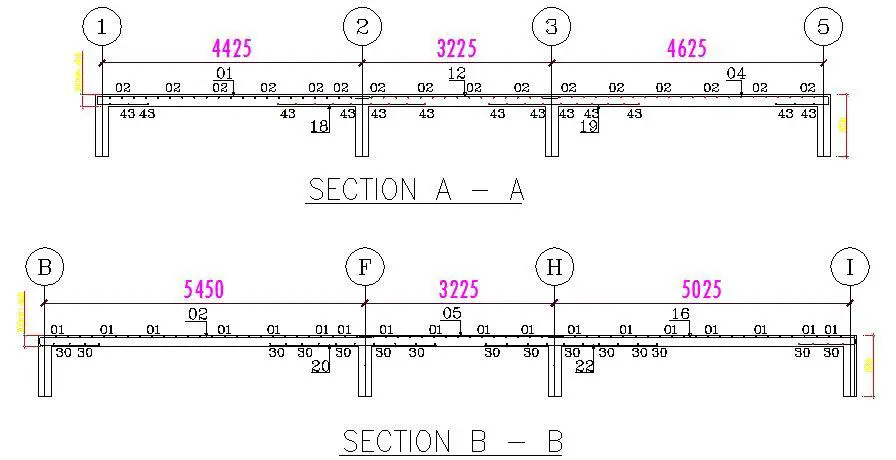
Typical Costing and Processes for Raft Foundation Construction
(1) Setting Out Works
Allow a lump sum of ₦150,000 (Note that this may vary depending on how challenging the setting out process is. The services of a surveyor may be required, and materials like pegs, 2 inches nails, 3 inches nails, 2″ x 3″ hardwood, lines, etc will be required. The professional fee of the carpenters, foreman, supervisors, resident engineers, consulting architects etc may also be required depending on the nature of the contract).
In this case, we are assuming that the contractor is accepting to do the setting out for the price stated above with his team. All professionals in the job have been paid by the client. The contractor is to provide all the materials needed for the setting out.
It very important that the architect and design engineer verify the setting out before excavation can commence. All setbacks and airspace should be confirmed, including the squareness of the building. The deviation of dimensions on the profile board should not exceed 5 mm.
(2) Excavation
From the design drawings and quantity take-off, the following quantities have been verified;
Total length of excavation = 121 m
Depth of excavation = 500 mm
Width of excavation = 700 mm
Volume of excavation = 42.218 m3
Allow for excavation using direct manual labour @ ₦300 per linear metre.
Cost of excavation = 300 x 121 = ₦36,300
Allow 30% to cover for contractors profit and overhead = 1.3 x 36,300 = ₦47,190
(3) Blinding of excavation
The thickness of blinding = 50 mm
The volume of concrete required for blinding = 4.3 m3 (Using M15 concrete)
For mixing, placing, and consolidating grade 15 concrete (cement price at ₦3,500) = ₦30,800/m3
Cost of blinding = 30800 x 4.3 = ₦132,440
Allow 20% to cover for contractor’s profit and overhead = 1.2 x 132,440 = ₦158,928
(4) Reinforcement works – Ground beam
Y20 required = 596.772 kg
Y16 required = 573.177 kg
Y12 required (side bars) = 644.688 kg
Y8 required (links) = 462.655 kg
Y16 required (column starter bars)= 297.8 kg
Y8 required (as links for column starter bars)
Total quantity of reinforcement required for ground beams = 2277.292 kg = 2.278 tonnes
Allow 5% for waste and laps = 1.05 x 2.278 = 2.391 tonnes
Total cost of reinforcements and binding wire = ₦825,120
Cost of labour = ₦60,000
Cost of materials and labour for reinforcement works (ground beam) = ₦885,120
Allow 25% to cover for contractor’s profit and overhead = 1.25 x 885,120 = ₦1,106,400
(5) Formwork – Ground beam
The marine board to be purchased will be reused for the decking of the first-floor slab. Therefore, we will utilise full boards for the ground beam formwork. Marine board can be reused about 5 times before the quality deteriorates. Let us assume that the quantity to be purchased at this stage should be able to do half of the ground beams.
The total area of formwork = 288 m2
Quantity of marine board required for half of the formwork = 55 pieces @ ₦9000/board = ₦495,000
2″ x 3″ softwood required = 380 pieces @ ₦400/length = ₦152,000
3″ Nails reuired = 100 kg @ ₦300/kg = ₦30,000
Labour @ ₦500/m2 = ₦144,000
Cost of ground beam formwork (materials and labour) = ₦821,000
Allow 20% to cover for contractor’s profit and overhead = 1.2 x 821,000 = ₦985,200
(6) Concrete Works – Ground Beam
Volume of concrete required = 23.46 m3
For mixing, placing, and consolidating grade 25 concrete (cement price at ₦3,500) = ₦44,100/m3
Cost of concrete for ground beams = 44,100 x 23.46 = ₦1,034,586
Allow 20% to cover for contractor’s profit and overhead = 1.2 x 1,034,586 = ₦1,241,503
(7) Backfilling and compaction
The volume of filling sand required = 86.775 m3 = 145 tonnes of filling sand
Cost of filling sand = ₦181,250
Cost of labour for filling and compacting (direct manual labour) = @ ₦800/m3 = ₦69,420
Total cost for filling = ₦250,670
Allow 20% to cover for contractor’s profit and overhead = 1.2 x 250,670 = ₦300,804
(8) Levelling and installation of damp proof membrane
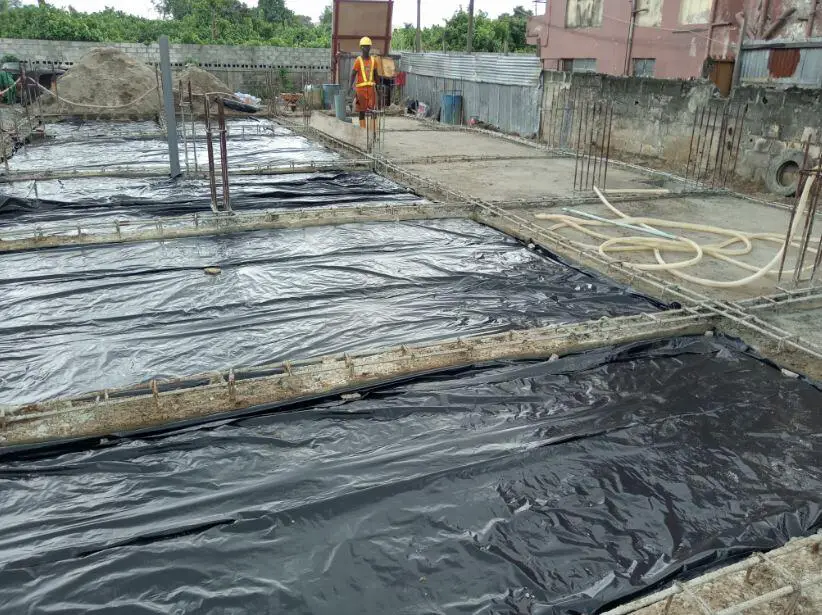
Allow a lump sum of ₦70,000
(9) Blinding to receive raft slab
Thickness of blinding = 50 mm
The volume of concrete required for blinding = 9.35 m3 (Using M15 concrete)
For mixing, placing, and consolidating grade 15 concrete (cement price at ₦3,500) = ₦30,800/m3
Cost of blinding = 30800 x 9.35 = ₦287,980
Allow 20% to cover for contractor’s profit and overhead = 1.2 x 287,980 = ₦345,576
(10) Raft slab reinforcement works
Y12 – 2922 kg
Y10 – 300 kg
Total quantity of reinforcement required = 3222 kg = 3.222 tonnes
Allow 5% for waste and laps = 1.05 x 3.222 = 3.383 tonnes
Cost of reinforcement and binding wire = ₦1,132,560
Cost of labour = ₦84,575
Cost of materials and labour for reinforcement works (raft slab) = ₦1,217,135
Allow 25% to cover for contractor’s profit and overhead = 1.25 x 1,217,135 = ₦1,521,419
(11) Edge formwork for raft slab
Allow a labour cost of = ₦30,000
(12) Concrete Works – Raft Slab
The volume of concrete required = 37.4 m3
For mixing, placing, and consolidating grade 25 concrete (cement price at ₦3,500) = ₦44,100/m3
Cost of concrete for ground beams = 44,100 x 37.4 = ₦1,649,340
Allow 20% to cover for contractor’s profit and overhead = 1.2 x 1,649,340 = ₦1,979,208
Summary
(1) Setting Out – ₦150,000
(2) Excavation – ₦47,190
(3) Blinding of excavation = ₦158,928
(4) Reinforcement works – Ground beam – ₦1,106,400
(5) Formwork – Ground beam – ₦985,200
(6) Concrete Works – Ground Beam – ₦1,241,503
(7) Backfilling and Compaction – ₦300,804
(8) Levelling and installation of damp proof membrane – ₦70,000
(9) Blinding to receive raft slab – ₦345,576
(10) Raft slab reinforcement works – ₦1,521,419
(11) Edge formwork for raft slab – ₦30,000
(12) Concrete Works – Raft Slab – ₦1,979,208
The total typical cost of constructing a raft foundation in Nigeria = ₦7,936,288
Remember to add 7.5% tax.
For the design, construction, and project management of your building projects in Nigeria, contact;
Structville Integrated Services Limited
E-mail: info@structville.com
Phone: +2348060307054
WhatAapp: +2347053638996
Hi. I work in the construction industry here in Nigeria with a major player in the geotechnical field but this is the first time I have come across something this – detailed and informative. I am impressed. Kudos and well done. Keep it up.
Heloo..your explanations are on point..very comprehensive and explicit….keep it up bro
This i s highly impressing
I am highly impressed with this kind of people that want progress for others. This are information hidden by some people thinking they can be surpassed by others, forgetting that God has a way of paying back. Engr Obinna, God bless you and gives you your earth desires for been the eye opener for the young engineers.
Nice one Ubani..
I need Comprehensive details for 3 floor using Raft Foundation
I can say this is very detailed and useful and even a young engineer or quantity surveyor in the industry will be pleased to see this.