When a column section is subjected to bending moment in the two axes in addition to a compressive axial force, the column is said to be biaxially loaded. The design of steel columns for biaxial bending involves the verification of the steel section’s capacity in bending, shear, compression, flexural buckling, and interaction of all these forces. Interaction formulas are available in EN 1993-1-1:2005 (Eurocode 3) for the design of members that are biaxially loaded.
Clause 6.2.9 of EN 1993-1-1:2005 describes the design of cross-sections subjected to combined bending and axial force (such as steel columns). Bending can occur along one or both major axes, with tensile or compressive axial forces (with no difference in treatment). Eurocode 3 provides several approaches for designing Class 1 and 2, Class 3, and Class 4 cross-sections in order to deal with the combined effects.
A basic linear interaction presented below and in equation (1) can be applied to all cross-sections (clause 6.2.1(7)). Although Class 4 cross-section resistances must be based on effective section properties. Furthermore, any additional moments arising from the resulting shift in neutral axis should be allowed for in class 4 sections. These extra moments necessitate the use of the expanded linear interaction expression.
NEd/NRd + My;Ed/My;Rd + Mz;Ed/Mz;Rd ≤ 1.0 ———— (1)
where NRd, My,Rd, and Mz,Rd are the design cross-sectional resistances, and any required reduction due to shear effects should be included (clause 6.2.8). The goal of equation (1) is to allow a designer to obtain a quick, approximate, and safe solution, possibly for initial member sizing, with the option to refine the calculations for final design.
Bi-axial bending with or without axial force (Class 1 and 2 sections)
EN 1993-1-1, like BS 5950: Part 1, treats bi-axial bending as a subset of the combined bending and axial force regulations. Clause 6.2.9.1 specifies the checks for Class 1 and 2 cross-sections subjected to bi-axial bending with or without axial forces (6). Although equation (1) shows a simple linear interaction expression, equation (2) represents a more sophisticated convex interaction expression that can result in large efficiency gains:
(My;Ed/MN;y;Rd)α + (Mz;Ed /MN;z;Rd)β ≤ 1.0 ———- (2)
in which α and β are constants, as defined below. Clause 6.2.9(6) allows α and β to be taken as unity, thus reverting to a conservative linear interaction.
For I- and H-sections:
α = 2 and β = 5n but β ≤ 1.0
For circular hollow sections:
α = 2 and β = 1
Rectangular hollow sections
α = β = 1.66/(1 – 1.13n2) but α = β ≤ 6.0
n = NEd / Nc,Rd
Worked Example
Verify the capacity of a 3500 mm tall column of UKC 254x254x89 in a commercial complex to withstand the following ultimate limit state actions;
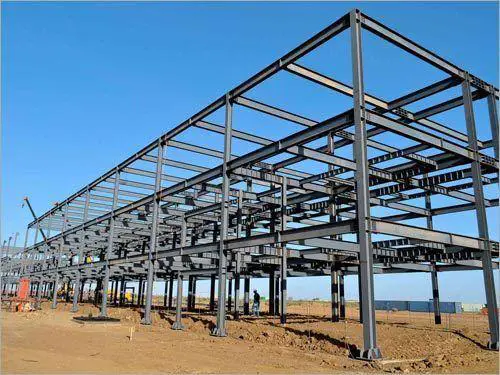
Axial load; NEd = 1500 kN; (Compression)
Major axis moment at end 1 – Bottom; My,Ed1 = 89.0 kNm
Major axis moment at end 2 – Top; My,Ed2 = 77.0 kNm
Minor axis moment at end 1 – Bottom; Mz,Ed1 = 7.9 kNm
Minor axis moment at end 2 – Top; Mz,Ed2 = 2.4 kNm
Major axis shear force; Vy,Ed = 56 kN
Minor axis shear force;Vz,Ed = 14 kN
Solution
Partial factors
Resistance of cross-sections; γM0 = 1
Resistance of members to instability; γM1 = 1
Resistance of cross-sections in tension to fracture; γM2 = 1.1
Column details
Column section; UKC 254x254x89
Steel grade; S275
Yield strength; fy = 265 N/mm2
Ultimate strength; fu = 410 N/mm2
Modulus of elasticity; E = 210 kN/mm2
Poisson’s ratio; υ = 0.3
Shear modulus; G = E / [2 × (1 + υ)] = 80.8 kN/mm2
Column geometry
System length for buckling – Major axis; Ly = 3500 mm
System length for buckling – Minor axis; Lz = 3500 mm
The column is part of a sway frame in the direction of the minor axis
The column is part of a sway frame in the direction of the major axis
Column loading
Axial load; NEd = 1500 kN; (Compression)
Major axis moment at end 1 – Bottom; My,Ed1 = 89.0 kNm
Major axis moment at end 2 – Top; My,Ed2 = 77.0 kNm
Minor axis moment at end 1 – Bottom; Mz,Ed1 = 7.9 kNm
Minor axis moment at end 2 – Top; Mz,Ed2 = 2.4 kNm
Major axis shear force; Vy,Ed = 56 kN
Minor axis shear force;Vz,Ed = 14 kN
Buckling length for flexural buckling – Major axis
End restraint factor; Ky = 1.000
Buckling length; Lcr_y = Ly × Ky = 3500 mm
Buckling length for flexural buckling – Minor axis
End restraint factor; Kz = 1.000
Buckling length; Lcr_z = Lz × Kz = 3500 mm
Web section classification (Table 5.2)
fy = 265 N/mm2
Coefficient depending on fy; ε = √(235/ fy) = 0.942
Depth between fillets; cw = h – 2 × (tf + r) = 200.3 mm
Ratio of c/t; ratiow = cw / tw = 19.45
Length of web taken by axial load; lw = min(NEd / (fy × tw), cw) = 200.3 mm
For class 1 & 2 proportion in compression; α = (cw/2 + lw/2) / cw = 1.000
Limit for class 1 web;
Limit1w = (396 × e) / (13 × a – 1) = 31.08
The web is class 1
Flange section classification (Table 5.2)
Outstand length; cf = (b – tw) / 2 – r = 110.3; mm
Ratio of c/t; ratiof = cf / tf = 6.38
Conservatively assume uniform compression in flange
Limit for class 1 flange; Limit1f = 9 × e = 8.48
Limit for class 2 flange; Limit2f = 10 × e = 9.42
Limit for class 3 flange; Limit3f = 14 × e = 13.18
The section is class 1
Resistance of cross section (cl. 6.2)
Shear – Major axis (cl. 6.2.6)
Design shear force; Vy,Ed = 56.0 kN
Shear area; Avy = max((h – 2tf) × tw, A – 2 × b × tf + (tw + 2 × r) × tf) = 3081 mm2
fy = 265 N/mm2
Plastic shear resistance; Vpl,y,Rd = Avy × (fy/√3)/ γM0 = 471.4 kN
Vy,Ed / Vpl,y,Rd = 0.119
PASS – Shear resistance exceeds the design shear force
Vy,Ed ≤ 0.5×Vpl,y,Rd – No reduction in fy required for bending/axial force
Shear – Minor axis (cl. 6.2.6)
Design shear force; Vz,Ed = 13.5 kN
Shear area; Avz = 2 × b × tf – (tw + 2 × r) × tf = 8250 mm2
Plastic shear resistance; Vpl,z,Rd = Avz × (fy /√3) / γM0 = 1262.3 kN
Vz,Ed / Vpl,z,Rd = 0.011
PASS – Shear resistance exceeds the design shear force
Vz,Ed ≤ 0.5×Vpl,z,Rd – No reduction in fy required for bending/axial force
Compression (cl. 6.2.4)
Design force; NEd = 1500 kN
Design resistance; Nc,Rd = Npl,Rd = A × fy / γM0 = 3003 kN
NEd / Nc,Rd = 0.5
PASS – The compression design resistance exceeds the design force
Bending – Major axis (cl. 6.2.5)
Design bending moment; My,Ed = max(abs(My,Ed1), abs(My,Ed2)) = 89.0 kNm
Section modulus; Wy = Wpl.y = 1223.9; cm3
Design resistance; Mc,y,Rd = Wy × fy / γM0 = 324.3 kNm
My,Ed / Mc,y,Rd = 0.274
PASS – The bending design resistance exceeds the design moment
Bending – Major axis(cl. 6.2.5)
Design bending moment; Mz,Ed = max(abs(Mz,Ed1), abs(Mz,Ed2)) = 7.9 kNm
Section modulus; Wz = Wpl.z = 575.3; cm3
Design resistance; Mc,z,Rd = Wz × fy / γM0 = 152.5 kNm
Mz,Ed / Mc,z,Rd = 0.052
PASS – The bending design resistance exceeds the design moment
Combined bending and axial force (cl. 6.2.9)
fy = 265 N/mm2;
Npl,Rd = A × fy / γM0 = 3003 kN
Ratio design axial to design plastic resistance; n = abs(NEd) / Npl,Rd = 0.500
Ratio web area to gross area; a = min(0.5, (A – 2 × b × tf) / A) = 0.217
Bending – Major axis (cl. 6.2.9.1)
Design bending moment; My,Ed = max(abs(My,Ed1), abs(My,Ed2)) = 89.0 kNm
Plastic design resistance; Mpl,y,Rd = Wpl.y × fy / γM0 = 324.3 kNm
Modified design resistance; MN,y,Rd = Mpl,y,Rd × min(1, (1 – n) / (1 – 0.5 × a)) = 182.1 kNm
My,Ed / MN,y,Rd = 0.489
PASS – Bending resistance in presence of axial load exceeds the design moment
Bending – Minor axis (cl. 6.2.9.1)
Design bending moment;Mz,Ed = max(abs(Mz,Ed1), abs(Mz,Ed2)) = 7.9 kNm
Plastic design resistance; Mpl,z,Rd = Wpl.z × fy / γM0 = 152.5 kNm
Modified design resistance;MN,z,Rd = Mpl,z,Rd × [1 – ((n – a) / (1 – a))2] = 132.6; kNm
Mz,Ed / MN,z,Rd = 0.059
PASS – Bending resistance in presence of axial load exceeds the design moment
Biaxial bending
Exponent α; α = 2.00
Exponent β; β = max(1, 5 × n) = 2.50
Section utilisation at end 1; URCS_1 = [abs(My,Ed1) / MN,y,Rd] α + [abs(Mz,Ed1) / MN,z,Rd] β = 0.240
Section utilisation at end 2; URCS_2 = [abs(My,Ed2) / MN,y,Rd] α + [abs(Mz,Ed2) / MN,z,Rd] β = 0.179
PASS – The cross-section resistance is adequate
Buckling resistance (cl. 6.3)
Yield strength for buckling resistance; fy = 265 N/mm2
Flexural buckling – Major axis
Elastic critical buckling force; Ncr,y = π2 × E × Iy / Lcr_y2 = 24140 kN
Non-dimensional slenderness; λy = √(A × fy / Ncr,y) = 0.353
Buckling curve (Table 6.2); b
Imperfection factor (Table 6.1); αy = 0.34
Parameter Φ; Φy = 0.5 × [1 + αy × (λy – 0.2) + λy2] = 0.588
Reduction factor; χy = min(1.0, 1 / [Φy + √(Φy 2 – λy2)]) = 0.944
Design buckling resistance; Nb,y,Rd = χy × A × fy / γM1 = 2835.9 kN
NEd / Nb,y,Rd = 0.529
PASS – The flexural buckling resistance exceeds the design axial load
Flexural buckling – Minor axis
Elastic critical buckling force; Ncr,z = π2 × E × Iz / Lcr_z2 = 8219 kN
Non-dimensional slenderness; λz = √(A × fy / Ncr,z) = 0.604
Buckling curve (Table 6.2); c
Imperfection factor (Table 6.1); αz = 0.49
Parameter Φ; Φz = 0.5 × [1 + αz × (λz – 0.2) + λz2] = 0.782
Reduction factor; χz = min(1.0, 1 / [Φz + √(Φz2 – λz2)]) = 0.783
Design buckling resistance; Nb,z,Rd = χz × A × fy / γM1 = 2350.4 kN
NEd / Nb,z,Rd = 0.638
PASS – The flexural buckling resistance exceeds the design axial load
Torsional and torsional-flexural buckling (cl. 6.3.1.4)
Torsional buckling length factor; KT = 1.00
Effective buckling length; Lcr_T = KT × max(Ly, Lz) = 3500 mm
Distance from shear ctr to centroid along major axis; y0 = 0.0 mm
z0 = 0 mm
Distance from shear ctr to centroid along minor axis; z0 = 0.0 mm
i0 = √(iy2 + iz2 + y02 + z02) = 129.9 mm
bT = 1 – (y0 / i0)2 = 1.000
Elastic critical torsional buckling force; Ncr,T = 1 / i02 × (G × It + π2 × E × Iw / Lcr_T2) = 12085 kN
Elastic critical torsional-flexural buckling force; Ncr,TF = Ncr,y/(2 × bT) × [1 + Ncr,T/Ncr,y – √[(1 – Ncr,T/Ncr,y)2 + 4 × (y0/i0)2 × Ncr,T/Ncr,y]]
Ncr,TF = 12085 kN
Non-dimensional slenderness; λT = √(A × fy / min(Ncr,T, Ncr,TF)) = 0.498
Buckling curve (Table 6.2); c
Imperfection factor (Table 6.1); αT = 0.49
Parameter Φ; ΦT = 0.5 × [1 + αT × (λT – 0.2) + λT2] = 0.697
Reduction factor; χT = min(1.0, 1 / [ΦT + √(ΦT 2 – λT2)]) = 0.844
Design buckling resistance; Nb,T,Rd = χT × A × fy / γM1 = 2533.9 kN
NEd / Nb,T,Rd = 0.592
PASS – The torsional/torsional-flexural buckling resistance exceeds the design axial load
Minimum buckling resistance
Minimum buckling resistance; Nb,Rd = min(Nb,y,Rd, Nb,z,Rd, Nb,T,Rd) = 2350.4 kN
NEd / Nb,Rd = 0.638
PASS – The axial load buckling resistance exceeds the design axial load
Buckling resistance moment (cl.6.3.2.1)
Lateral torsional buckling length factor; KLT = 1.00
Effective buckling length; Lcr_LT = KLT × Lz = 3500 mm
End moment factor; y = My,Ed2 / My,Ed1 = 0.865
Moment distribution correction factor (Table 6.6); kc = 1 / (1.33 – 0.33 × y) = 0.957
C1 = 1 / kc2 = 1.091
Curvature factor; g = √[1 – (Iz / Iy)] = 0.812
Poissons ratio; υ = 0.3
Shear modulus; G = E / [2 × (1 + υ)] = 80769 N/mm2
Elastic critical buckling moment; Mcr = C1 × π2 × E × Iz × √[Iw / Iz + Lcr_LT2 × G × It /(π2 × E × Iz)]/(Lcr_LT2 × g)
Mcr = 1739.3 kNm
Slenderness ratio for lateral torsional buckling; λLT = √[Wy × fy / Mcr] = 0.432
Limiting slenderness ratio; λLT,0 = 0.40
Correction factor for rolled sections; βr = 0.75
Buckling curve (Table 6.5); b
Imperfection factor (Table 6.1); αLT = 0.34
Parameter ΦLT; ΦLT = 0.5 × [1 + αLT × (λLT – λLT,0) + βr × λLT2] = 0.575
Reduction factor; χLT = min(1.0, 1/λLT2, 1 / [ΦLT + √(ΦLT2 – βr × λLT2)]) = 0.988
Modification factor; f = min(1 – 0.5 × (1 – kc) × [1 – 2 × (λLT – 0.8)2], 1) = 0.984
Modified LTB reduction factor – eq 6.58; χLT,mod = min(χLT / f, 1, 1/λLT2) = 1.000
Design buckling resistance moment; Mb,Rd = χLT,mod × Wy × fy / γM1 = 324.3 kNm
Design bending moment; My,Ed = max(abs(My,Ed1), abs(My,Ed2)) = 89.0 kNm
My,Ed / Mb,Rd = 0.274
PASS – The design buckling resistance moment exceeds the maximum design moment
Combined bending and axial compression (cl. 6.3.3)
Characteristic resistance to normal force; NRk = A × fy = 3003 kN
Characteristic moment resistance – Major axis; My,Rk = Wpl.y × fy = 324.3 kNm
Characteristic moment resistance – Minor axis; Mz,Rk = Wpl.z × fy = 152.5 kNm
Moment factor – Major axis; Cmy = 0.9
Moment factor – Minor axis; Cmz = 0.9
Moment distribution factor for LTB; yLT = My,Ed2 / My,Ed1 = 0.865
Moment factor for LTB; CmLT = max(0.4, 0.6 + 0.4 × yLT) = 0.946
Interaction factor kyy; kyy = Cmy × [1 + min(0.8, λy – 0.2) × NEd / (χy × NRk / γM1)] = 0.973
Interaction factor kzy; kzy = 1 – min(0.1, 0.1 × λz) × NEd / ((CmLT – 0.25) × (χz × NRk/γM1)) = 0.945
Interaction factor kzz; kzz = Cmz × [1 + min(1.4, 2 × λz – 0.6) × NEd / (χz × NRk / γM1)] = 1.250
Interaction factor kyz; kyz = 0.6 × kzz = 0.750
Section utilisation;
URB_1 = NEd / (χy × NRk / γM1) + kyy × My,Ed / (χLT × My,Rk / γM1) + kyz × Mz,Ed / (Mz,Rk / γM1)
URB_1 = 0.838
URB_2 = NEd / (χz × NRk / γM1) + kzy × My,Ed / (χLT × My,Rk / γM1) + kzz × Mz,Ed / (Mz,Rk / γM1)
URB_2 = 0.965
PASS – The buckling resistance is adequate
Great job Engr Ubani
Professional post!