Some substances in aggregates can react with alkali hydroxides in concrete. It is only when this reactivity causes large expansion in the concrete it is deemed dangerous. There are two types of alkali-aggregate reactivity (AAR):
- Alkali-silica reaction (ASR), and
- Alkali-carbonate reaction (ACR).
Because aggregates containing reactive silica minerals are more common in concrete, alkali-silica reaction is of greater concern than alkali-carbonate reaction. Alkali-reactive carbonate aggregates have a unique composition that is not found in many other materials. Since the late 1930s, alkali-silica reactivity has been identified as a potential source of concrete distress. Alkali-silica distress in structural concrete is uncommon, despite the presence of potentially reactive aggregates across North America. This is due to a variety of factors:
- Aggregates with good performance are plentiful in many places, and most aggregates are chemically stable in hydraulic cement concrete.
- The majority of in-service concrete is dry enough to prevent ASR.
- Certain pozzolans or slags can be used to control ASR.
- The alkali concentration of certain concrete combinations is low enough to prevent damaging ASR
- Some types of alkali-silica reaction do not cause considerable detrimental expansion.
Understanding the ASR mechanism, effectively performing tests to detect potentially reactive aggregates, and, if necessary, taking efforts to decrease the possibility for expansion and subsequent cracking are all required to reduce ASR potential.
Alkali-Silica Reaction (ASR)
A network of cracks, blocked or spalled joints, relative displacements of different components of a building, or pieces breaking out of the concrete surface (popouts) are all common symptoms of alkali-silica reaction in concrete. The risk of catastrophic failure is however low because ASR deterioration is slow. Alkali-silica reaction, on the other hand, might produce serviceability issues and increase other deterioration mechanisms, such as those caused by frost, deicer, or sulphate exposure.
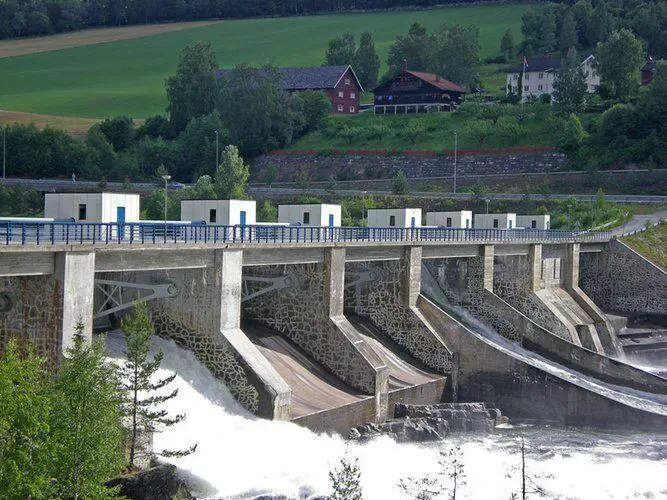
Mechanism of Alkali-Silica Reaction
The alkali-silica reaction produces a gel that expands as it absorbs water from the cement paste around it. ASR’s reaction products have a strong affinity for moisture. These gels can cause pressure, expansion, and breaking of the aggregate and surrounding paste by absorbing water. The reaction can be broken down into two steps:
- Alkali hydroxide + reactive silica gel → reaction product (alkali-silica gel)
- Gel reaction product + moisture → expansion
The amount of gel created in concrete is determined by the amount and kind of silica used, as well as the concentration of alkali hydroxide. The presence of gel does not always imply distress in concrete, and hence the presence of gel does not always imply damaging ASR.
Factors Affecting Alkali-Silica Reaction
The following three conditions must be present for the alkali-silica reaction to occur:
- reactive forms of silica in the aggregate,
- high-alkali (pH) pore solution, and
- sufficient moisture.
ASR cannot occur if one of these conditions is not met.
Identification Test Methods for Distress due to ASR
It is important to distinguish between the damage caused by the reaction, and the reaction itself. A gel product will almost certainly be discovered in the diagnosis of concrete deterioration. However, considerable volumes of gel can accumulate without causing concrete damage in some circumstances. The existence of harmful ASR gel must be confirmed in order to designate ASR as the cause of damage.
An aggregate particle that is recognisably reactive or potentially reactive that is at least partially replaced by gel is described as a site of expansive reaction. Gel can be found in cracks and voids, as well as in a ring that surrounds an aggregate particle’s edges. Cracking caused by ASR is nearly often shown by a network of interior fissures linking reacted aggregate particles. The most reliable approach for detecting ASR gel in concrete is a petrographic study. Petrography can confirm the existence of reaction products and confirm ASR as the underlying cause of degradation when used to investigate a known reacted concrete.
Control of Alkali-Silica Reaction in New Concrete
The easiest approach to prevent ASR is to take proper precautions before pouring concrete. To address ASR, standard concrete specifications may need to be modified. To prevent limiting the concrete producer’s possibilities, these alterations should be carefully customised. This allows for a thorough examination of cementitious materials and aggregates, as well as the selection of a control plan that balances effectiveness and cost. There are no extra criteria if the aggregate is not reactive based on past identification or testing.
Identification of Potentially Reactive Aggregates
The easiest way to assess an aggregate’s susceptibility to alkali-silica reaction is to look at its field performance history. The concrete should have been in use for at least 15 years for the most accurate assessment. Comparisons should be performed between the mix proportions, constituents, and service settings of existing and projected concrete. This procedure should reveal whether unique requirements are required, whether they are not required, and whether aggregate or work concrete testing is required.
For preliminary screening, newer, faster test methods can be used. Longer testing can be performed to confirm results where there are uncertainties. Some of the different test procedures for evaluating possible alkali-silica reactivity are;
- ASTM C 227: Potential alkali reactivity of cement-aggregate combinations (mortar-bar method)
- ASTM C 289: Potential alkali-silica reactivity of aggregates (chemical method)
- ASTM C 295: Petrographic examination of aggregates for concrete, etc
These tests should not be used to rule out the use of potentially reactive aggregates; reactive aggregates can be used safely with appropriate cementitious material selection, as explained below.
Materials and Methods to Control Alkali-Silica Reaction
Designing combinations particularly to limit ASR, ideally utilising locally available materials, is the most effective approach of controlling expansion owing to ASR. The following options are not in any particular sequence of importance, and they can be used in conjunction with one another.
In North America, current procedures include controlling the alkali content of the concrete or using a supplemental cementitious ingredient or blended cement shown by testing to control ASR. Fly ash, powdered granulated blast-furnace slag, silica fume, and natural pozzolans are examples of supplementary cementitious materials. Slag, fly ash, silica fume, and natural pozzolans are used in blended cements to control ASR.
The use of low-alkali portland cement (ASTM C 150) with an alkali concentration of less than 0.60 percent (equivalent sodium oxide) has been successful in the control of ASR in aggregates that are marginally reactive to moderately reactive. Low-alkali cements, however, are not accessible everywhere. For controlling ASR, it is preferable to use locally accessible cements in combination with pozzolans, slags, or mixed cements. When pozzolans, slags, or mixed cements are used to control ASR, tests like ASTM C 1260 (modified) or C 1293 must be employed to determine their effectiveness.
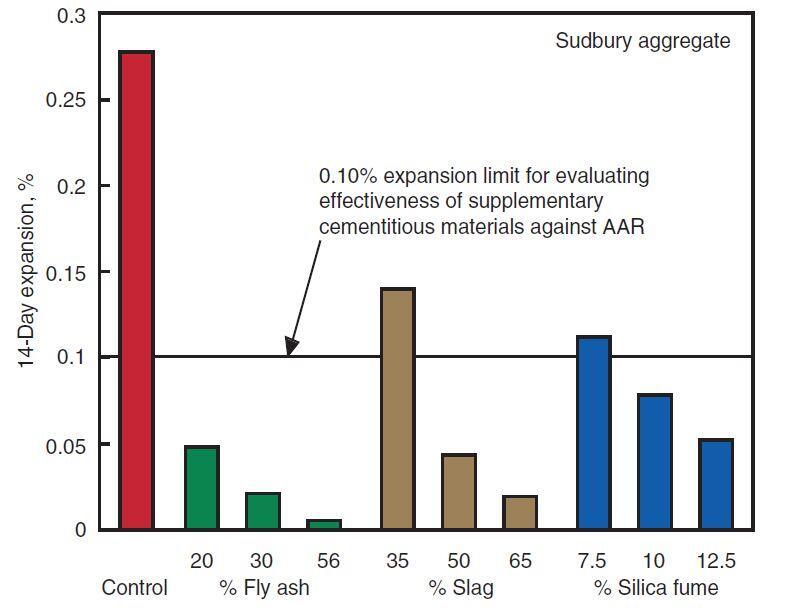
Different amounts of pozzolan or slag should be tested to establish the best dosage, if applicable. As the dosage of pozzolan or slag is increased, expansion normally decreases (see Figure 2). ASR can also be controlled with lithium-based admixtures. Limestone sweetening (changing around 30% of the reactive sand-gravel aggregate with crushed limestone) is useful in preventing concrete deterioration in various sand-gravel aggregate concretes.