Potentially harmful materials in aggregates for concrete are substances that react chemically with Portland cement concrete to produce one or more of the following:
(1) Significant volume change in the cement paste, aggregate, or both;
(2) interfering with cement’s regular hydration; and
(3) producing additional potentially hazardous byproducts
Organic impurities, silt, clay, shale, iron oxide, coal, lignite, and some lightweight and soft particles are all harmful materials in aggregates, that can affect the performance of the concrete in the fresh and/or hardened state (see Table 1). Alkali-reactive rocks and minerals include certain cherts, strained quartz, and some dolomitic limestones. Furthermore, sulfate attacks on concrete can be caused by gypsum and anhydrite. Popouts can be caused by swelling (absorption of water) or freezing of absorbed water in some aggregates, such as certain shales.
Table 1: Some harmful materials in aggregates for concrete
Substances | Effect on Concrete |
Organic impurities | Affects setting and hardening, may cause deterioration |
Materials finer than the 75-μm (No. 200) sieve | Affects bond, ASTM C 117 (AASHTO T 11) increases water requirement |
Coal, lignite, or other lightweight materials | Affects durability, and may cause stains and popouts |
Soft particles | Affects durability |
Clay lumps and friable particles | Affects workability and durability, and may cause popouts |
Cherts of less than 2.40 relative density | Affects durability, and may cause popouts |
Alkali-reactive aggregates | Causes abnormal expansion, map cracking, and popouts |
Most standards usually provide the maximum allowed levels of these harmful materials in aggregates. When defining limitations for dangerous compounds, the performance history of an aggregate should be a deciding factor.
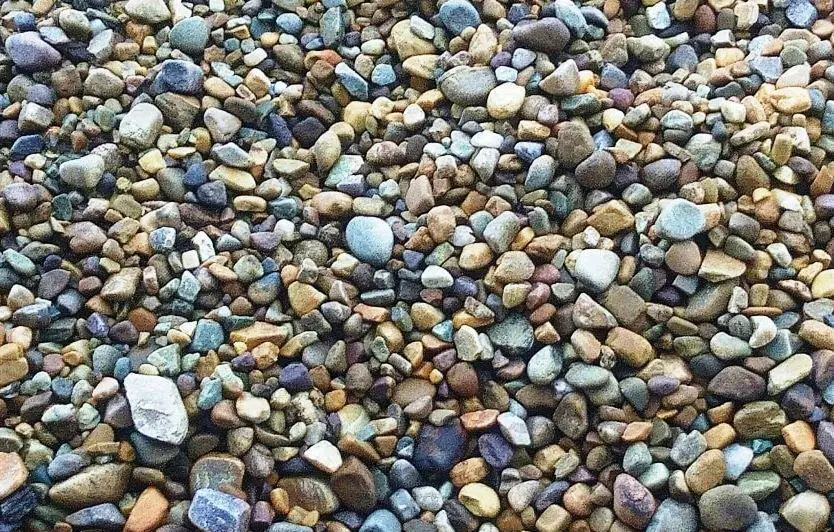
Organic Impurities
Organic impurities can cause concrete to take longer to set and harden, diminish strength increase, and, in rare situations, cause degradation. Organic impurities like peat, humus, and organic loam are less harmful, but they should still be avoided.
Fine Materials (Clay and Silt)
Very fine materials, such as silt and clay, may be present as loose dust and form a coating on aggregate particles finer than the 75μm (No. 200) sieve. Even tiny silt or clay coatings on gravel particles might be hazardous because they can damage the cement paste-aggregate bond. Water requirements may be greatly increased if certain types of silt or clay are present in excessive levels.
The grinding motion in a concrete mixer causes some fine aggregates to degrade; this effect, which is assessed using ASTM C 1137, can affect mixing water, entrained air, and slump requirements.
Low-density Materials (coal, lignite, wood, or fibrous materials)
Excessive volumes of coal or lignite, as well as other low-density components like wood or fibrous materials in concrete, will compromise the durability of concrete. These contaminants may dissolve, pop out, or generate stains if they exist near the surface. The ASTM C 123 standard can be used to identify potentially dangerous chert in coarse aggregate (AASHTO T 113).
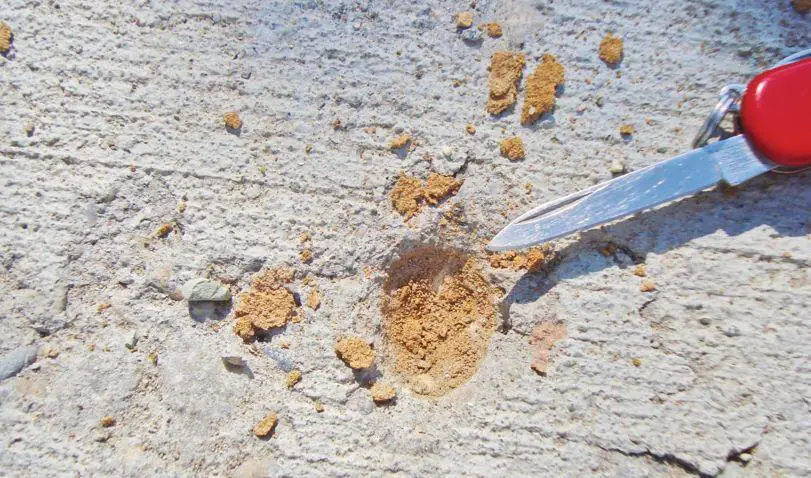
Soft, friable particles
Soft particles in coarse aggregates are particularly problematic because they produce popouts and can compromise concrete’s durability and wear resistance. If they are friable, they may break up when mixing, increasing the amount of water requirement. Testing may show that more inquiry or a different aggregate source is required where abrasion resistance is crucial, such as in heavy-duty industrial floors.
Clay Lumps
Clay lumps in concrete can absorb some of the mixing water, causing popouts in hardened concrete and reducing the durability and wear resistance of the concrete. They can also break up while mixing, increasing the amount of mixing water required.
Iron oxide and iron sulfide particles
Iron oxide and iron sulfide particles can occasionally be found in aggregates, causing unattractive stains on exposed concrete surfaces (see image below). When tested according to ASTM C 641, the aggregate should meet the staining standards of ASTM C 330 (AASHTO M 195); the quarry face and aggregate stockpiles should not exhibit evidence of staining.
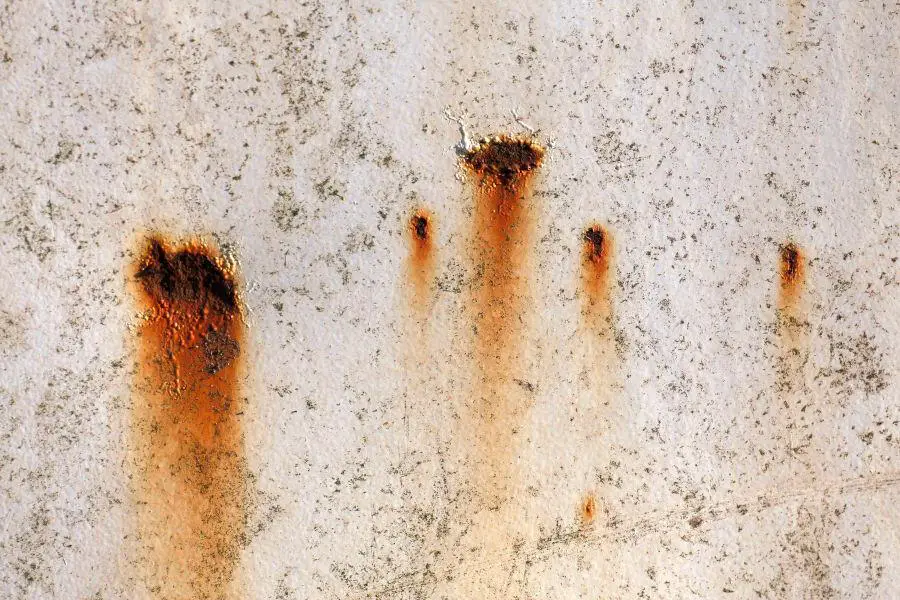
The aggregate can also be submerged in a lime slurry to help detect stained particles. If staining particles are present, a blue-green gelatinous precipitate will form within 5 to 10 minutes; when exposed to air and light, it will quickly turn brown. Within 30 minutes, the reaction should be completed. When a suspicious aggregate is placed in lime slurry and no brown gelatinous precipitate forms, there is little chance of a reaction occurring in concrete. When aggregates with no prior successful use in architectural concrete are utilized, certain tests should be required.
It’s great that you discussed that the mixing water can be absorbed with clay lumps in concrete. My friend wants aggregate concrete for their project. I should advise him to turn to a supplier that specializes in concrete solutions.