A biaxial column is a column that is subjected to compressive axial force and bending moment in the two planes. They are usually found at the corners of a building or at locations where the beam spans and/or loading are not equal. In the design of biaxial reinforced concrete columns, a non-linear analysis method is required, which should take into account second-order, imperfection, and biaxial bending effects.
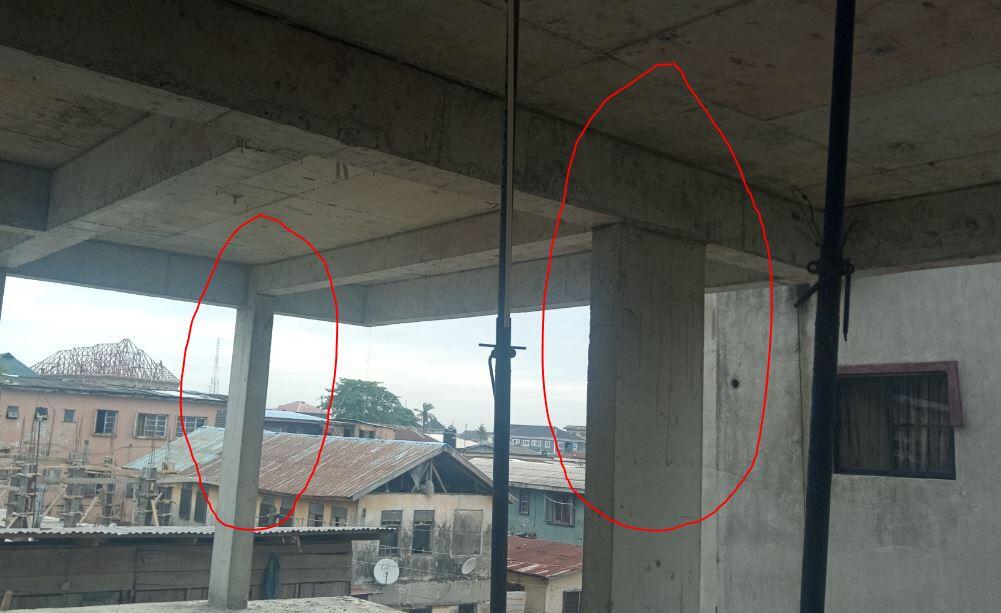
EN 1992-1-:2004 (Eurocode 2) did not give an express method of designing biaxial columns other than working from the first principles. This may not be very easy to achieve without the use of charts or computer programs. To develop such a program, one can divide the compression zone into strips that are parallel with the neutral axis of the section, and calculate the stress in each strip using the parabolic-rectangular diagram. The force and moment at each strip in the x and y-axis can be summed up in the ultimate limit state to find the moment and axial force developed by the concrete in compression.
There are however simplified methods of dealing with biaxial bending in reinforced concrete structures. An example is the approach given in clause 5.8.9(4) of EN 1992-1-1 for the design of biaxially bent sections in slender columns. This is based on the observation that the form of the Mx – My interaction diagram can conveniently be represented by a super-ellipse. A super-ellipse has an equation of the form;
xa + ya = k —— (1)
If a = 2, this equation becomes a circle, while if a = 1 it describes a straight line. At loads approaching the squash load, the Mx – My interaction diagram approaches a circle, while in the region of the balance point it is close to a straight line. Clause 5.8.9(4) adopts the equation below as a means of describing the complete interaction surface;
(ME,dz/MR,dz )a + (MEd,y/MRd,y )a ≤ 1.0 —— (2)
The proximity to the squash load can be defined using the N/Nuz ratio parameter, and EN 1992-1-1 assumes the relationship between this parameter and the exponent ‘a‘ given in the Table below. Intermediate values may be interpolated.
NEd/NRd | 0.1 | 0.7 | 1.0 |
a | 1.0 | 1.5 | 2.0 |
In the Table above, NRd is the squash load of the column, and may be calculated from
NRd = Acfcd + Asfyd —— (3)
The difficulty with the approach from the practical point of view is that it cannot be used as a direct design method since NRd can only be established once the reinforcement area has been found. It, therefore, has to be used iteratively. An initial estimate is made of N/Nuz, the section is designed, a corrected value of N/Nuz can then be estimated, and the process repeated until a correct solution is obtained.
A much simpler, but considerably more approximate method to the design of biaxial columns has been adopted in BS 8110. The design is carried out for an increased uniaxial moment, which takes account of the biaxial effects. The required uniaxial moment is obtained from whichever is appropriate of the two relationships set out below:
if Mx/h’ > My/b’ then M’x = Mx + βh’My/b’ —— (4)
if Mx/h’ < My/b’ then M’y = My + βb’Mx /h’ —— (5)
In the above relationships, Mx and My are the design moments about the x and y axes, respectively, while M’x and M’y are the effective uniaxial moments for which the section is actually designed. b’ and h’ are the effective depths of the column section (see image below). The factor β is defined in BS 8110 as a function of N/bhfcu. In terms of fck, it can be obtained from the relationship;
β = 1 – N/bhfck (0.3 < β < 1.0) —— (6)
This approach has the great advantage of being very simple. It is, however, an approximate approach.
Example on the Design of Biaxial Reinforced Concrete Columns to BS 8110 and Eurocode 2
A reinforced concrete column fixed at both ends is subjected to the loading condition shown below. We are required to obtain the appropriate longitudinal reinforcement for the column using BS 8110-1:1997 and Eurocode 2.
The column is carrying longitudinal and transverse beams of depth 600mm and width 300mm. It is also supported by beams of the same dimension. The centre to centre height of the column is 3500mm. The plan view of the arrangement of the beams and column is as shown below.
DESIGN ACCORDING TO BS 8110-1:1997
N = 716.88 kN;
TOP: Mx-x = 175.87 kNm; My-y = 35.52 kNm
BOTTOM: Mx-x = -85.832 kNm; My-y = -25.269 kNm
Concrete grade fcu = 30 N/mm2
Yield Strength of reinforcement fy = 460 N/mm2
Concrete cover = 40mm
Lo = 3.5m, Effective length Le = 0.75 × (3500 – 600) = 2175 mm;
Size of column = 400 x 300mm;
Slenderness = 2175/300 = 7.25 < 15. Thus column is short.
Effective depth about x-x axis
h’ = (400 – 40 – 12.5 – 10) = 337.5 mm
Effective depth about y-y axis
b’ = (300 – 40 – 12.5 – 10) = 237.5 mm
Mx/h’ = 521.109 kN; My/ b’ = 149.558 kN
Axial-load ratio
Nratio = (N × 1000) / (Fcu × b × h) = (716.88 × 1000) / (30 × 400 × 300) = 0.1991
From Table 3.22 of BS 8110-1:1997, for Nratio = 0.1991
Therefore, β = 1 – 1.1644(0.1991) = 0.7681
As Mx/h’ exceeds My/b’
Mx‘ = Mx + βh’/b’My
Mx‘ = 175.87 + [0.7681 × (0.3375)/(0.2375 ) × 35.52] = 214.64 kNm
Minimum Eccentricity in Columns
According to clause 3.8.2.4 of BS 8110-1:1997, at no section in a column should the design moment be taken as less than that produced by considering the design ultimate axial load as acting at a minimum eccentricity, emin equal to 0.05 times the overall dimension of the column in the plane of bending considered but not more than 20 mm.
Where biaxial bending is considered, it is only necessary to ensure that the eccentricity exceeds the minimum about one axis at a time.
In the x-x direction = emin = 0.05 × 400 = 20mm, therefore adopt 20mm, Mx = 716.88 × 0.02 = 14.3376 kNm < 214.64 kNm
In the y-y direction = emin = 0.05 × 300 = 15mm, therefore adopt 15mm, My = 716.88 × 0.015 = 10.7532 kNm < 214.64 kNm
Section design ratios for chart entry
Axial load ratio Nratio = (N × 1000)/(Fcu × b × h) = (716.88 × 1000)/(30 × 400 × 300) = 0.1991
Mratio = M/(Fcu × b × h2) = (214.64 × 106) / (30 × 300 × 4002) = 0.149
With d’/h = 337.5/400 = 0.84375
From chart, (ρ × Fy)/(Fcu) = 0.286 Therefore, ρ = (0.286 × 30) / 460 = 0.01865
ASCreq = 0.01865 × 400 × 300 = 2238.26 mm2
Provide 6Y25mm (Asprov = 2946 mm2)
Maximum area of reinforcement = 0.06bh = 0.06 × 400 × 300 = 7200 mm2
DESIGN ACCORDING TO EUROCODE 2
Clause 5.8.9(2) of EN 1992-1-1:2004 permits us to perform separate designs in each principal direction, disregarding biaxial bending as a first step. Imperfections need to be taken into account only in the direction where they will have the most unfavourable effect. However, in this example, we have carried out imperfection analysis in both directions.
NEd = 716.88 KN
Elastic Moments
Y – direction: M01 = 175.87 kNm; M02 = -85.832 kNm
Z – direction: M01 = 35.52 kNm; M02 = -25.269 kNm
Clear column height (L) = 3500 – 600 = 2900 mm
Calculation of the effective height of the column (Lo)
Let us first of all calculate the relative stiffnesses of the members in the planes of bending.
In the y-direction;
Second moment of area of beam 1 (I1) = bh3/12 = 0.3 × 0.63/12 = 0.0054 m4
Stiffness of beam 1 (since E is constant) = 4I1/L = (4 × 0.0054) / 6 = 0.0036
Second moment of area of beam (I2) = bh3/12 = 0.3 × 0.63/12 = 0.0054 m4
Stiffness of beam 2 (since E is constant) = 4I2/L = (4 × 0.0054) / 3.5 = 0.00617
Second moment of area of column (Ic) = bh3/12 = 0.0016 m4
Stiffness of column = 4Ic/L = (4 × 0.0016) / 3.5 = 0.001828
For compression members in regular braced frames, the slenderness criterion should be checked with an effective length l0 determined in the following way:
Lo = 0.5L √[(1 + k1)/(0.45 + k1)) × (1 + k2)/(0.45 + k2))]
Where;
k1, k2 are the relative flexibilities of rotational restraints at ends 1 and 2 respectively
L is the clear height of the column between the end restraints
k = 0 is the theoretical limit for rigid rotational restraint, and k = ∞ represents the limit for no restraint at all. Since fully rigid restraint is rare in practise, a minimum value of 0.1 is recommended for k1 and k2.
In the above equations, k1 and k2 are the relative flexibilities of rotational restraint at nodes 1 and 2 respectively. If the stiffness of adjacent columns does not vary significantly (say, the difference not exceeding 15% of the higher value), the relative flexibility may be taken as the stiffness of the column under consideration divided by the sum of the stiffness of the beams (or, for an end column, the stiffness of the beam) attached to the column in the appropriate plane of bending.
Remember that we will have to reduce the stiffness of the beams by half to account for cracking;
k1 = k2 = 0.001828 / (0.0018 + 0.003085) = 0.3743
Lo = 0.5 × 2900√[((1 + 0.3743)/(0.45 + 0.3743)) × (1 + 0.3743)/(0.45 + 0.3743)] = 2647.77 mm
Compare with BS 8110’s 0.75L = 0.75 × 2900 = 2175 mm
In the z-direction;
Second moment of area of beam 3 (I3) = bh3/12 = 0.3 × 0.63/12 = 0.0054 m4
Stiffness of beam 3 (since E is constant) = 4I1/L = (4 × 0.0054) / 3.5 = 0.00617
Second moment of area of column (Ic) = bh3/12 = 0.0009 m4
Stiffness of column = 4Ic/L = (4 × 0.0009) / 3.5 = 0.00102857
k1 = k2 = 0.00102857/(0.003085) = 0.3334
lo = 0.5 × 2900 √[(1 + 0.3334) / (0.45 + 0.3334) × (1 + 0.3334) / (0.45 + 0.3334)] = 2675.293 mm
Radius of gyration
ix = h/√12 = 400/√12 = 115.47
iz = b/√12 = 300/√12 = 86.602
Slenderness in the x-direction (λx) = 2647.77/115.47 = 22.930
Slenderness in the z-direction (λz) = 2675.293/86.602 = 30.892
Critical Slenderness for the y-direction
λlim = (20.A.B.C)/√n
A = 0.7
B = 1.1
C = 1.7 – M01/M02 = 1.7 – [(-85.832)/175.87] = 2.188
n = NEd / (Ac fcd)
NEd = 716.88 × 103 N
Ac = 400 × 300 = 120000 mm2
fcd = (αcc fck)/1.5 = (0.85 × 30)/1.5 = 17 N/mm2
n = (716.88 × 103) / (120000 × 17) = 0.3514
λlim = (20 × 0.7 × 1.1 × 2.188 )/√0.3514 = 56.842
22.930 < 56.842, second order effects need not to be considered in the y-direction
Critical Slenderness for the z-direction
A = 0.7
B = 1.1
C = 1.7 – M01/M02 = 1.7 – [(-25.269)/35.52] = 2.411
n = NEd / (Ac fcd)
NEd = 716.88 × 103 N
Ac = 400 × 300 = 120000 mm2
fcd = (αcc fck)/1.5 = (0.85 × 30)/1.5 = 17 N/mm2
n = (716.88 × 103) / (120000 × 17) = 0.3514
λlim = (20 × 0.7 × 1.1 × 2.411 )/√0.3514 = 62.634
30.892 < 62.634, second-order effects need not be considered in the z-direction
Design Moments (y-direction)
Y – direction: M01 = 175.87 kNm; M02 = -85.832 kNm
e1 is the geometric imperfection = (θi l0/2) = (1/200) × (2647.77/2) = 6.619 mm
Minimum eccentricity e0 = h/30 = 400/30 = 13.333 mm. Since this is less than 20mm, take minimum eccentricity = 20mm (clause 6.1(4) EC2).
Minimum design moment = e0NEd = 20 × 10-3 × 716.88 = 14.3376 kNm
First order end moment M02 = MTop + eiNEd
eiNEd = 6.619 × 10-3 × 716.88 = 4.745 KNm
M02 = MTop + eiNEd = 175.87 + 4.754 = 180.624 KNm
Longitudinal Steel Area
d2 = Cnom + ϕ/2 + ϕlinks = 40 + 12.5 + 10 = 62.5 mm
d2/h = 62.5/400 = 0.156
Let us read from chart; d2/h = 0.15;
MEd/(fck bh2) = (180.624 × 106)/(30 × 300 × 4002 ) = 0.125
NEd/(fck bh) = (716.88 × 103) / (30 × 300 × 400) = 0.199
From the chart, (As Fyk)/(bhfck) = 0.23
Area of longitudinal steel required As,req = (0.23 × 30 × 400 × 300)/460 = 1800 mm2
As,min = 0.10 NEd/fyd = (0.1 × 716.88)/400 = 0.179 mm2 < 0.002 × 400 × 300 = 240 mm2
As,max = 0.04bh = 4800 mm2
Provide 4Y25mm (Asprov = 1964 mm2)
Design Moments (z-direction)z – direction: M01 = 35.52 kNm; M02 = -25.269 kNm
e1 is the geometric imperfection = (θi l0/2) = (1/200) × (2675.293/2) = 6.688 mm
Minimum eccentricity e0 = h/30 = 400/30 = 13.333 mm. Since this is less than 20mm, take minimum eccentricity = 20mm (clause 6.1(4) EC2)
Minimum design moment = e0NEd = 20 × 10-3 × 716.88 = 14.3376 kNm
First order end moment M02 = MTop + eiNEd
eiNEd = 6.688 × 10-3 × 716.88 = 4.794 KNm
M02 = MTop + eiNEd = 35.52 + 4.794 = 40.314 KNm
Longitudinal Steel Area
d2 = Cnom + ϕ/2 + ϕlinks = 40 + 12.5 + 10 = 62.5 mm
d2/h = 62.5/400 = 0.156
Reading from chart No 1; d2/h = 0.156;
MEd/(fck bh2) = (40.314 × 106)/(30 × 300 × 4002) = 0.0279
NEd/(fck bh) = (716.88 × 103) / (30 × 300 × 400) = 0.199
From the chart, (As Fyk)/(bhfck) = 0.00 (Nominal reinforcement required)
Biaxial Effects
Check if λy / λz ≤ 2.0 and λz/λy ≤ 2.0
17.203/18.159 = 0.9473 < 2.0, and 18.159/17.203 = 1.0556 < 2.0
Furthermore, let us also check;
(ey/heq) / (ez/beq) ≤ 0.2 or (ez / beq) / (ey / heq) ≤ 0.2
The definition of eccentricity is given in Figure 5.8 of EC2
ey = MEd,y/NEd = (180.624 × 106) / (716.88 × 103) = 251.958 mm
ez = MEd,z/NEd = (40.314 × 106) / (716.88 × 103) = 56.235 mm
heq = iz.√12 = 300 mm
beq = iy.√12 = 400 mm
(ey/heq) ÷ (ez/beq) = 251.958/300 ÷ 56.235/400 = 5.9739 > 0.2
Therefore we have to check for biaxial bending interaction;
(ME,dz/MR,dz )a + (MEd,y/MRd,y )a ≤ 1.0
(As Fyk)/(bhfck) = (1964 × 460) / (30 × 300 × 400) = 0.251
Therefore from the chart; MRd/(fckbh2) = 0.13
MRd = (0.13 × 30 × 300 × 4002) × 10-6 = 187.2 KNm
NRd = Acfcd + Asfyd
NRd = [(300 × 400 × 17) + (1964 × 400)] × 10-3 = 2825.6 kN
NEd/NRd = 716.88 / 2825.6 = 0.2537
To evaluate the value of a, let us look at the table below as given in Clause 5.8.9(4) of EC2
By linear interpolation, a = 1.0 + [(0.2537 – 0.1 )/(0.7 – 0.1)] × (1.5 – 1.0) = 1.128
(ME,dz/MR,dz )a + (MEd,y/MRd,y )a ≤ 1.0
(40.314/187.2)1.128 + (180.624/187.2)1.128 = 0.1769 + 0.9606 = 1.1375 > 1.0.
This is not ok, and this shows that 4Y25 is inadequate for the biaxial action on the column.
Let us increase the area of steel to 6Y25mm (Asprov = 2946 mm2)
Let us check again;
(As Fyk)/(bhfck) = (2964 × 460) / (30 × 300 × 400) = 0.3787
Therefore from the chart; MRd/(fckbh2) = 0.175
MRd = (0.175 × 30 × 300 × 4002) × 10-6 = 252 kNm
NRd = Acfcd + Asfyd
NRd = [(300 × 400 × 17) + (2964 × 400)] × 10-3 = 3225.6 kN
NEd/NRd = 716.88 / 3225.6 = 0.222
By linear interpolation, a = 1.0 + [(0.222 – 0.1 )/(0.7 – 0.1)] × (1.5 – 1.0) = 1.102
(ME,dz/MR,dz )a + (MEd,y/MRd,y )a ≤ 1.0
(40.314/252)1.102 + (180.624/252)1.102 = 0.132 + 0.6928 = 0.825 > 1.0.
This shows that 6Y25mm is adequate for the column, and shows some agreement with result from BS 8110-1:1997.
Thank you for visiting Structville
Visit our facebook fan page;
www.facebook.com/structville
Dear Ubani,
I was doing a research about this topic and I came across your blog.
I'm trying to understand the right combination of design moments for biaxial check.
As you mentioned EC2 states that the imperfections need to be considered only in the direction where they will have the most unfavourable effect, Cl 5.8.9(2)
Now, since I'm dealing with high axial force and relative small bending moment(flat slab) the minimum design moment due to eccentricity Cl 6.1(4) dictates the design.
At the biaxial bending moment check which combination would you consider;
_Minimum moment due to eccentricity in both axis.
_Minimum moment due to eccentricity in the unfavourable axis and moment from analysis in the other one.
_Minimum moment due to eccentricity in the unfavourable axis and moment from imperfection in the other one.
I noticed that there is confusion about this aspect and because I've just started working with a new software which consider the third option I want to find out the right procedure.
Best Regards
Alessio
• It is appropriate time to make a few plans for the future and it is time to be happy. I have learn this publish and if I may just I desire to recommend you some attention-grabbing things or tips. Perhaps you can write next articles relating to this article. I want to read more issues about it!.
MEP F modelling
COBie adaptation
BIM documentation in India
BIM Consulting in India
cad services in India
BIM Solutions in India
BIM Project Management in India
Dear Ubani,
is there a typographic error in writing the formula for effective length (lo)?
I think, it should be 0.5*L*sqrt((1+K1/(0.45+K1))*(1+K2/(0.45+K2))) than of (1+K1)/(0.45+K1) or (1+K2)/(0.45+K2)