Springer is a leading global scientific, technical and medical portfolio, providing researchers in academia, scientific institutions and corporate R&D departments with quality content through innovative information, products and services. With more than 2,900 journals and 300,000 books, Springer offers many opportunities for authors, customers and partners. Here is a list of top civil engineering related textbooks that you can download for free on Springer during this COVID-19 period.
(1) Fatigue of Structures and Materials (2nd Edition, 2009)
Author: J. Schijve
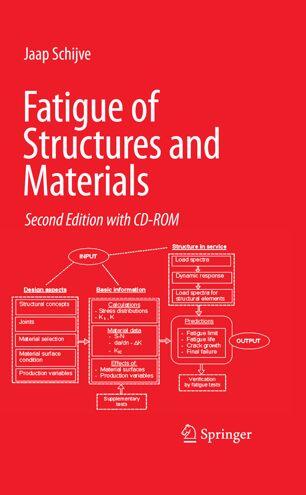
To download this textbook, click HERE
(2) Composite Materials (3rd Edition, 2012)
Author: Krishan K. Chawla
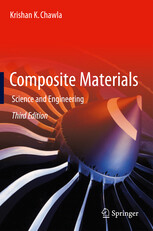
To download the text book, click HERE
(3) Introduction to Partial Differential Equations (1st Edition, 2016)
Author: David Borthwick
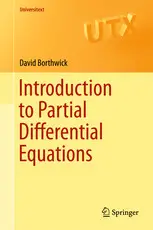
To download, click HERE
(4) Structural Analysis (2009)
Authors: O. A. Bauchau, J.I. Craig
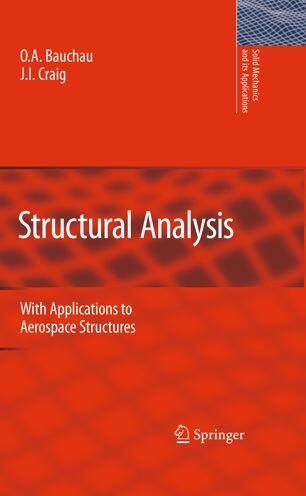
Click HERE to download
(5) Irrigation and Drainage Engineering (1st Edition, 2016)
Authors: Peter Waller, Muluneh Yitayew
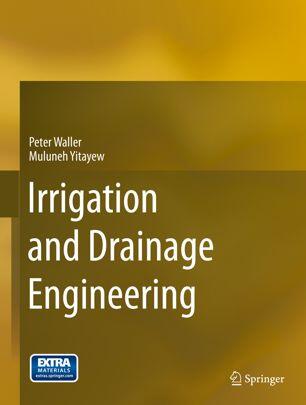
Click HERE to download
(6) Design and Analysis of Experiments (2nd Edition, 2017)
Authors: Angela Dean, Daniel Voss, Danel Draguljić
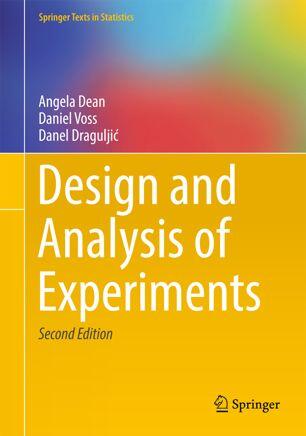
To download the textbook, click HERE
(7) Engineering Mechanics 1 (2nd Edition, 2013)
Authors: Schröder, Wolfgang A. Wall, Nimal Rajapakse
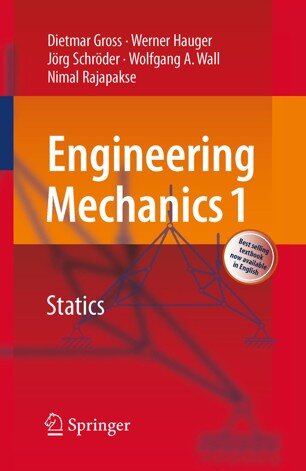
To download the textbook, click HERE
(8) Fluid Dynamics (2015)
Author: Michel Rieutord
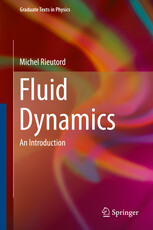
To download this textbook, click HERE
(9) Multivariate Calculus and Geometry (3rd Edition, 2014)
Author: Seán Dineen
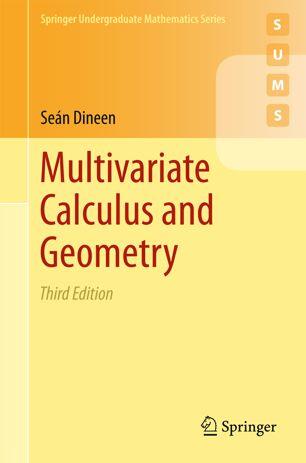
Click HERE to download
(10) Fundamentals of Structural Engineering (2nd Edition, 2016)
Authors: Jerome J. Connor, Susan Faraji
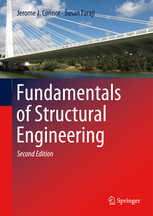
Click HERE to download
(11) The Finite Element Method and Applications in Engineering Using ANSYS (2nd Edition, 2015)
Authors: Erdogan Madenci, Ibrahim Guven
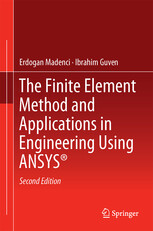
Click HERE to download
(12) An Introduction to Soil Mechanics (1st Edition, 2020)
Author: Arnold Verruijt
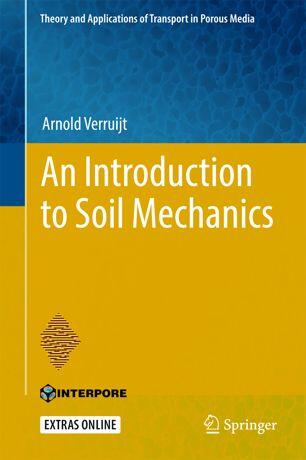
Click HERE to download
(13) The Finite Volume Method in Computational Fluid Dynamics (1st Edition, 2016)
Authors: F. Moukalled, L. Mangani, M. Darwish
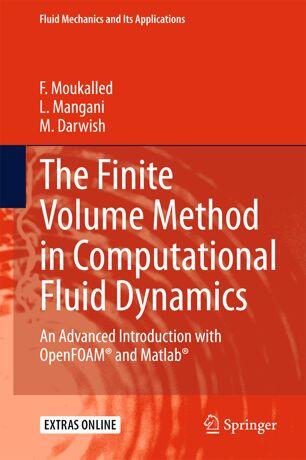
Click HERE to download
(14) Statics and Mechanics of Structures (2013)
Authors: Steen Krenk, Jan Høgsberg
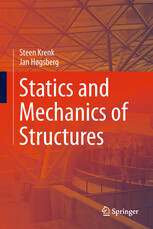
Click HERE to download
(15) Engineering Mechanics 2 (2nd Edition, 2018)
Authors: Schröder, Wolfgang A. Wall, Javier Bonet
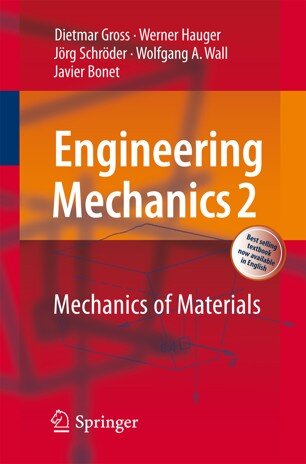
Click HERE to download
(16) Structural Dynamics (6th Edition, 2019)
Authors: Mario Paz, Young Hoon Kim
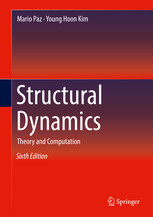
Click HERE to download
(17) Excel Data Analysis (2nd Edition, 2019)
Author: Hector Guerrero
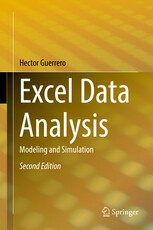
Click HERE to download
(18) Statistical Mechanics for Engineers (1st Edition, 2015)
Author: Isamu Kusaka
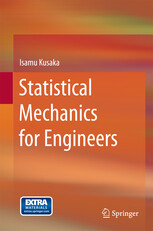
Click HERE to download
(19) An Introduction to Machine Learning (2nd Edition, 2017)
Author: Miroslav Kubat
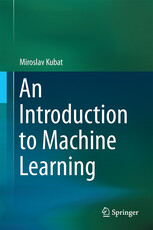
Click HERE to download
(20) Elementary Mechanics Using Matlab (2015)
Author: Anders Malthe-Sørenssen
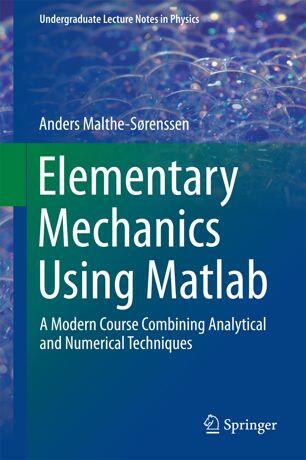
Click HERE to download
(21) Introduction to Artificial Intelligence (2nd Edition, 2017)
Author: Wolfgang Ertel
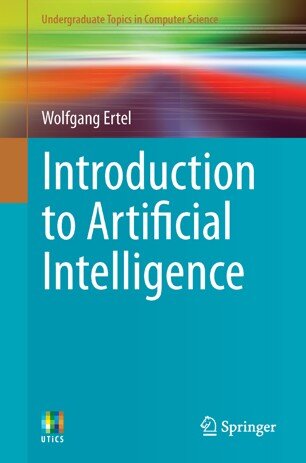
Click HERE to download
(22) Computational Geometry (3rd Edition, 2008)
Authors: Mark de Berg, Otfried Cheong, Marc van Kreveld, Mark Overmars
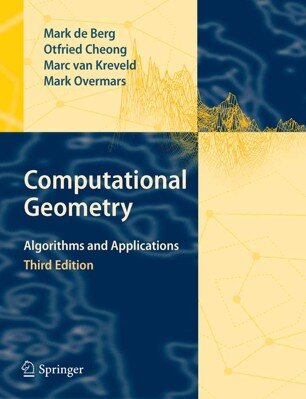
Click HERE to download
(23) Leadership Today (1st Edition, 2017)
Authors: Joan Marques, Satinder Dhiman
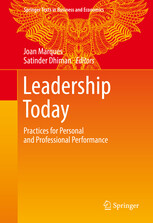
Click HERE to download
(24) Handbook of Marriage and the family (3rd Edition, 2013)
Authors: Gary W. PetersonKevin R. Bush
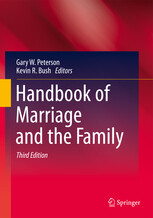
Click HERE to download
(25) Neural Networks and Deep Learning (1st Edition, 2018)
Authors: Charu C. Aggarwal
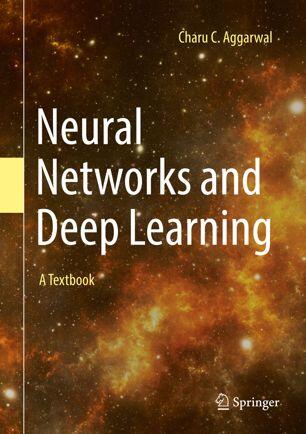
Click HERE to download